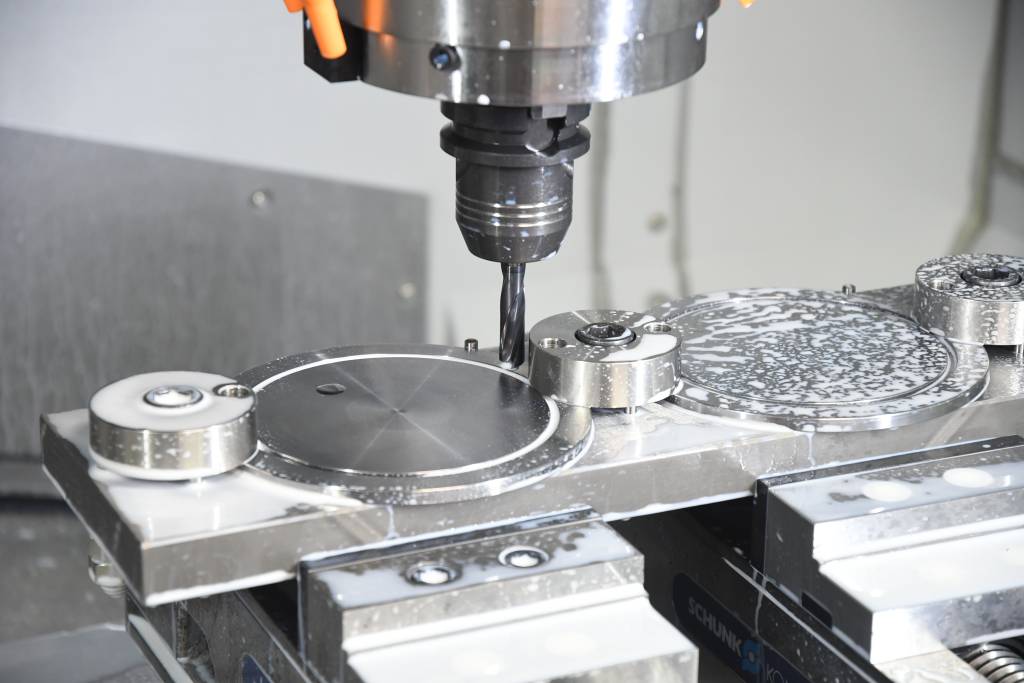
Enge Beziehungen zum Werkzeuglieferanten sind für den Fertigungsbetrieb Hähnel von entscheidender Bedeutung. „Ein Werkzeug verkaufen kann jeder, maßgeblich aber ist der Service dazu“, stellt Geschäftsführer Henry Hähnel klar. „Wendeplatten z.B. kann ich aus China, bei ebay oder sonst wo bestellen. Habe ich aber ein Problem bei der Bearbeitung, kommt niemand aus China und erzählt mir was dazu.“ Informationen und Service rund ums Werkzeug seien daher ein zentraler Punkt, der die mittlerweile über zehnjährige Zusammenarbeit präge: „OSG legt nicht nur ein Strohfeuer, um mal ein Werkzeug zu verkaufen. Vielmehr werden Kundenbindungen par excellence aufgebaut, namentlich von Jürgen Rösler. Natürlich muss das Werkzeug Leistung bringen, das ist Voraussetzung. Aber der Support stimmt eben auch.“
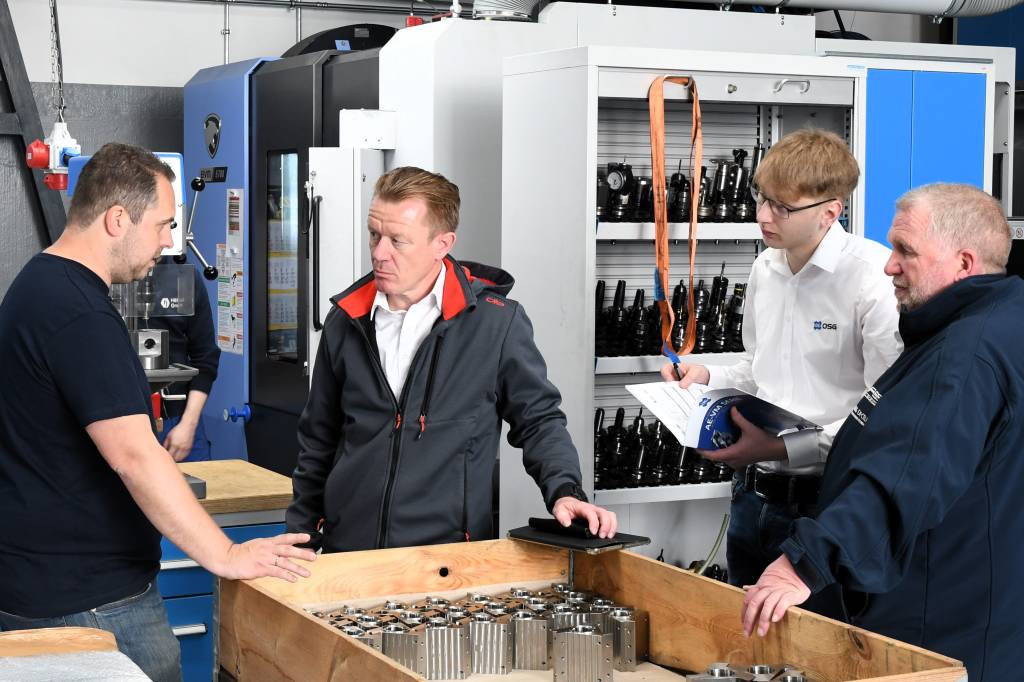
Darf´s gern etwas schwieriger sein?
Hähnel ist seit 1968 ein Familienunternehmen, das heute in dritte Generation geführt wird und acht Mitarbeiter beschäftigt. „Im Bereich Lohnfertigung positioniert, zählt die Herstellung von Prototypen, Erstmustern und daraus resultierenden Serien aus Werkstoffen jeglicher Güte zu unseren Stärken“, verortet der Geschäftsführer. „Unsere Dreh- und Frästeile etwa zerspanen wir aus Edelstählen und Sonderwerkstoffen, u.a. aus 1.3343, 1.4034, 1.4404 oder unserem Steckenpferd 1.4112. Schwerpunkt sind also Materialien, die sonst keiner gern zerspant.“ Die Größe der rotationssymmetrischen Teile reicht dabei von circa 3 bis 270mm Durchmesser; die kubischen werden mit Seitenlängen bis 1m beherrscht. Beim Herstellen solcher Teile, deren Losgrößen sich üblicherweise von 1 bis in den 1.000er Bereich erstrecken, agiert Hähnel nicht allein als verlängerte Werkbank, der Lohnfertiger unterstützt den Anwender auch bei der Entwicklung seines Werkstücks.
Für Hähnel ist OSG heute der Spezialist fürs Gewinden, und das zu 100 Prozent. Begonnen hatte alles mit dem Gewindebohren. Inzwischen ist auch das Gewindefräsen komplett auf OSG umgestellt. In jüngerer Zeit kam das Thema Flachbohren hinzu – zugegeben ein Nischenbereich – und somit zur Einführung des ADF. Ausgelegt ist das Werkzeug für eine Vielzahl von Bohranwendungen wie geneigte oder kurvenförmige Flächen, Senken, exzentrische Bohrungen oder dünne Platten. Die Schneidengeometrie ist dafür in Schärfe und Stabilität wohl ausbalanciert, ein großer Spanraum sorgt für sichere Spanabfuhr und die ‚EgiAs‘-Beschichtung für hohe Verschleißfestigkeit und Robustheit. Geometrisch ist der Spitzenwinkel des ADF so ausgelegt, dass – egal, in welcher Richtung die Toleranzen ausgelotet werden – stets ein Hohlschliff vermieden wird. Mit diesem Zentrum ist nicht nur gewährleistet, dass Folgewerkzeuge positionsgenau arbeiten, sondern auch, dass kurze Späne gebildet werden.
Nut als Problem
Bei einer ersten Anwendung in Velbert galt es eine M12-Bohrung in ein Bauteil aus 1.4301 stirnseitig einzubringen. Das Problem bestand darin, dass das Kernloch zu einer 7er Nut hin geöffnet werden musste, anschließend ein Gewinde sehr nah zum Bohrungsgrund hin zu fertigen war und die später eingeschraubte Gewindestange nicht in die Nut hereinragen durfte. Mit einem regulären VHM-Bohrer mit 140°-Spitzenwinkel ließ sich die Gewindetiefe nur mit Mühe erreichen. OSG schlug den ADF als Alternative vor und übergab die zugehörigen Schnittwerte.
„Wir haben dann direkt einen Versuch gestartet“, erinnert sich Hähnel. „Als erstes überraschten uns hierbei die Laufruhe und die Spanabfuhr. Ähnliche Werkzeuge hatten gezeigt, dass sich Späne mitunter nur unkontrolliert brechen lassen und damit einen ständigen Eingriff in den Prozess erfordern. Beim ADF war das zu keiner Zeit der Fall. Die Positionsgenauigkeit sowie die Oberflächengüte waren absolut maßhaltig und objektiv als ,sehr gut‘ zu bewerten.“ Nach 500 Bohrungen beurteilten Hähnel und OSG gemeinsam den Verschleiß des Werkzeugs, wobei bis auf einen geringen Freiflächenverschleiß nichts zu erkennen war. „Im Weiteren haben wir das Werkzeug dann nach je 300 Bohrungen geprüft. Selbst nach Erreichen der vorgesehenen 1.600 Bohrungen war der Verschleiß so gering, dass wir das Werkzeug weiterhin hätten einsetzen können“, unterstreicht Hähnel. „Besonders positiv fiel außerdem auf, dass es zu keinerlei Schneidkanten- und Eckenausbrüchen kam.“ Das Gewinde wurde schließlich mit einem AT-1 von OSG gefräst.
ADF optimiert weiteren Prozess
Mit diesen Erfahrungen ging Hähnel eine weitere Problematik bei einer anderen Bauteilfamilie an. Bei diesen Teilen aus 1.4112 bzw. 1.3343 verlaufen Bohrungen mit 8,2 und 13mm Durchmesser durch eine Nut: mal zur Hälfte, mal zu zwei Dritteln der Bohrung. „Die bisherige Lösung – kleiner vorbohren und mit einem HSS-Werkzeug aufstechen – war nicht mehr zeitgemäß“, urteilt Hähnel. „Also haben wir Jürgen darauf angesprochen, ob wir das mit dem ADF probieren. Nach einigen Tests zu den Schnittdaten konnten wir den Prozess mit dem Flachbohrer um mehr als die Hälfte verkürzen.“ Wurde früher mit zwei Werkzeugen und zwei Arbeitsschritten gearbeitet, spart sich Hähnel heute mit dem ADF zwei Werkzeugwechsel pro Teil – bei kürzerer Laufzeit, besserer Qualität und einer Standzeit, die den höheren Preis des Werkzeugs mehr als rechtfertigt.