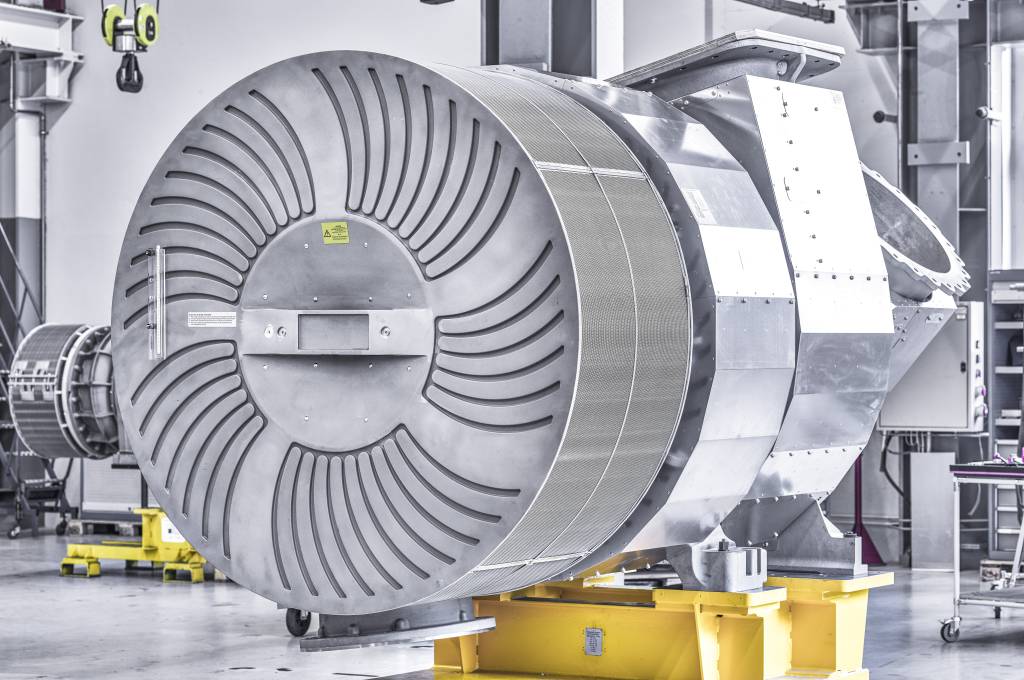
Der Startschuss bei Accelleron für die Suche nach einem geeigneten Manufacuring Execution System (MES) fiel bereits 2016, als die Firma noch eine Sparte und Marke von ABB war. Die Initiative damals fügte sich in das größere Vorhaben ein, die Digitalisierung voranzubringen, die IT-Landschaft zu harmonisieren und die Prozesse zu standardisieren. „Es gab viele Systeme, die über die Fertigung verteilt waren. Unser Ziel war es, alles möglichst kompakt unter einen Schirm zu bringen“, sagt der verantwortliche MES-Projektleiter Francesco Silani. David Andreatta, der die MES-Einführung als Mitglied des Steering Committee begleitet hat, ergänzt: „Unser bisheriges Fertigungsplanungstool war End-of-Life, der Support war abgekündigt und das System musste ersetzt werden.“ Hinzu kam die Forderung des Managements, Grundlagen für Fertigungskennzahlen wie die Overall Equipment Effectiveness (OEE) zu schaffen.
MES Hydra macht das Rennen
2018 nahm das Projekt Fahrt auf und nach einer Auswahlphase, in der etwa 30 Mitbewerber bewertet wurden, folgte die Entscheidung. MES Hydra landete auf der Shortlist und machte schließlich das Rennen: „Das MES konnte unsere Kriterien als Unternehmen in der diskreten Fertigung mit Stückzahl 1 genauso wie in einer Produktion mit Losgrößen von mehreren hundert Stück optimal abdecken“, sagt Andreatta.
30 Minuten für die Teamleiter
Auf die Entscheidung folgte eine Designphase und schließlich der etwa zweijährige Rollout. Seit Herbst 2023 läuft das MES in allen Divisionen im Produktivbetrieb. Doch erste Erfolge zeigten sich schon früher: „Die millimeterdicken Papierheftchen, die noch vor einem Jahr über die ganze Fertigung verteilt waren, sind jetzt weg. Diese Heftchen wurden am Anfang eines Auftrags vom Teamleiter gedruckt, manuell ausgefüllt, gestempelt, eingescannt und schließlich archiviert“, sagt Francesco Silani. Heute sei der Prozess digital, der Teamleiter initiiert einen Fertigungsauftrag, der Bediener sieht ihn am Terminal und am Ende gibt es eine PDF-Laufkarte. „Ein Knopfdruck und alles ist erledigt. Pro Teamleiter sparen wir so je nach Fall bis zu geschätzt einer halben Stunde am Tag.“
Weniger Fehler im Betrieb
Auch ein weiteres Beispiel verdeutlicht den Nutzen der MES-Anwendung: Seitdem sie im Einsatz ist, macht Accelleron bedeutend weniger Seriennummernfehler, die potenziell Kundenbeschwerden nach sich ziehen. Laut David Andreatta ist es bis dahin immer wieder vorgekommen, dass beim Kunden etwas falsch angeliefert wurde, was gravierende Auswirkungen haben kann. Mit dem MES merken die Verantwortlichen in der Fertigung früh, dass etwas nicht stimmt, weil der Bediener etwas nicht scannen kann. In den ersten sechs Monaten nach Einführung des Systems konnte die Firma allein in einer Abteilung zehn solcher Fehler verhindern. Auch die Werkerführung ist ein Gewinn für Accelleron: „Das System kann so begleitend gestaltet werden, dass man Mitarbeiter flexibel in den unterschiedlichen Abteilungen einsetzen kann, ohne dass sie langwierig eingelernt werden müssen“, schildert Silani. Doch der faszinierendste Aspekt ist für Francesco Silani, dass das Unternehmen einen übergreifenden MES-Standard eingeführt hat, um Verbesserungen sofort auf 17 Bereiche zu skalieren und in dem Umfang auch sofort auf Probleme reagieren kann.