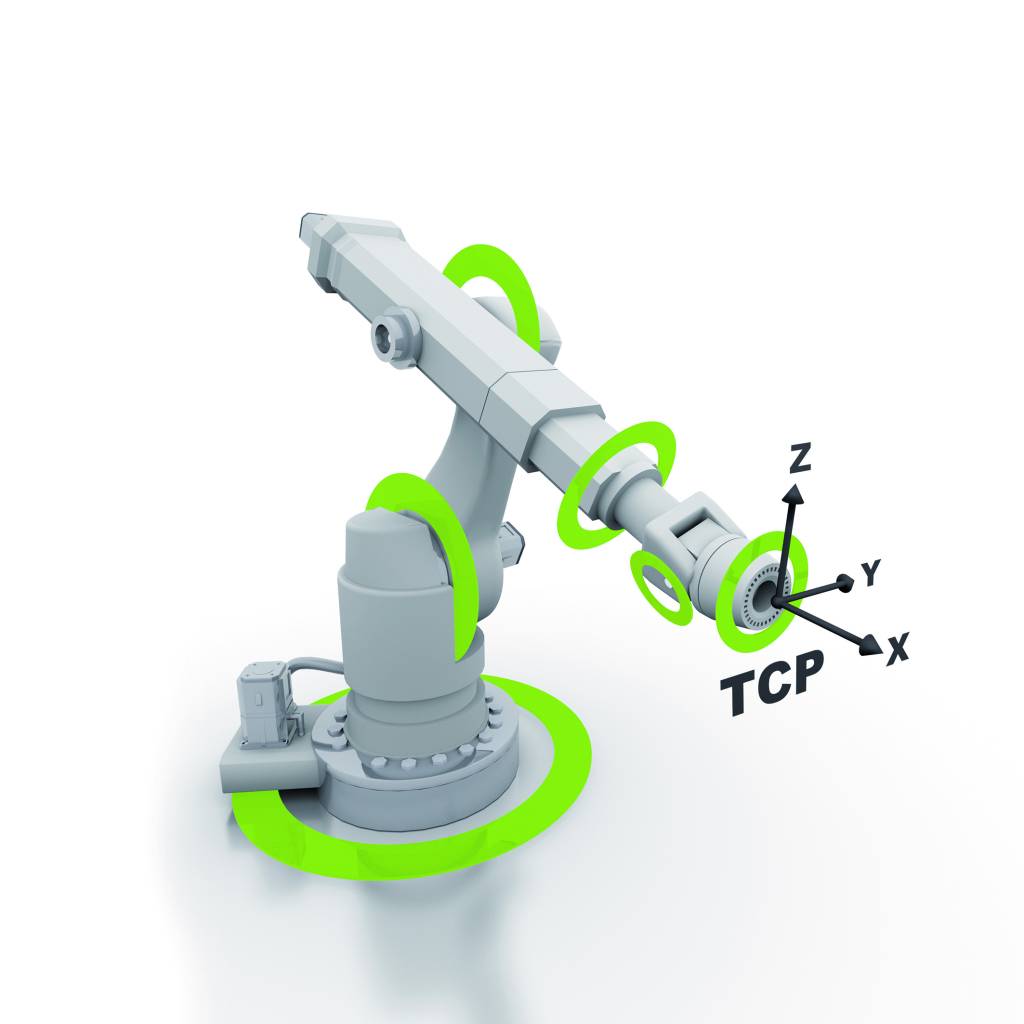
Noch vor ein paar Jahren war die absolute Positioniergenauigkeit bei Robotern kein großes Thema. Die Kinematiken arbeiteten damals noch vorwiegend in Handling-Anwendungen, in denen die Wiederholgenauigkeit wichtiger ist als die millimetergenaue Bewegung des Tool Center Point (TCP). Mittlerweile übernehmen Industrieroboter aber auch immer mehr Aufgaben in der Fertigung: Sie bohren, fräsen und schweißen Materialien oder schneiden sie per Laserstrahl. Diese Tätigkeiten erfordern eine hochpräzise Führung des TCP am Werkstück.
Materialbearbeitung mit Präzision
Die gestiegenen Anforderungen der Industrie an die Positioniergenauigkeit von Knickarmrobotern stellen deren Hersteller vor große Herausforderungen. Bisher reichte es aus, jedes Robotergelenk mit einem Drehgeber als Motorfeedback auszustatten. Der Encoder liefert dann der übergeordneten Steuerung die Informationen zur Position der jeweiligen Achse, die diese zur erfolgreichen Koordinierung des Handling-Vorgangs benötigt. Die Drehgeber erfassen die tatsächliche Position der Achsen allerdings nicht mit der erforderlichen Genauigkeit, um auch hochgenaue Bewegungen in der Materialbearbeitung präzise genug umsetzen zu können. Die Zuverlässigkeit der vom Motorfeedback-Geber ermittelten Positionsdaten variiert stark, denn die Messwertermittlung der Drehgeber wird durch diverse Faktoren negativ beeinflusst. Dazu zählen neben Nulllage-Abweichungen des Robotergelenks auch Umkehrfehler des Getriebes und die Elastizität der Roboterarme unter Last.
Einflüsse sorgen für Abweichungen
Neben dem Nulllagenfehler ist auch das Umkehrspiel in der Getriebeeinheit eine wesentlicher Einflussfaktor in Bezug auf die absolute Positioniergenauigkeit. So kann es bei der Umkehr der Antriebsrichtung durch das mechanische Spiel zwischen den Komponenten des Antriebsstrangs zu Abweichungen bei der Positioniergenauigkeit des Werkzeugs am TCP kommen. Bei Robotern mit langen Gelenken können diese Ungenauigkeiten zu einem deutlich schlechteren Bearbeitungsergebnis führen. Zu diesen inneren Einflüssen kommen noch die Krafteinwirkung sowie dynamische Effekte während des Bearbeitungsprozesses hinzu. Sie können ebenfalls auf die Steifigkeit der Robotermechanik wirken und so zu Bewegungsabweichungen führen.
Winkelmessgeräten steigern Präzision
Es gibt aber eine einfache Möglichkeit, diese Abweichungen zu kompensieren: Durch den Einsatz sogenannter Secondary Encoder. Diese Messgeräte werden zusätzlich zu den bereits installierten Drehgebern hinter dem Getriebe der Roboterachse montiert. Sie erfassen die tatsächliche Position jedes Robotergelenks im dreidimensionalen Raum, sodass der Roboter das Werkzeug mit der gewünschten Präzision führt. Darüber hinaus messen die Winkelmessgeräte an jeder Achse die Kräfte, die durch den Bearbeitungsvorgang am Werkstück auf den Roboter zurückwirken. Insgesamt lässt sich die absolute Positioniergenauigkeit am Tool Center Point so um 70 bis 80 Prozent steigern.