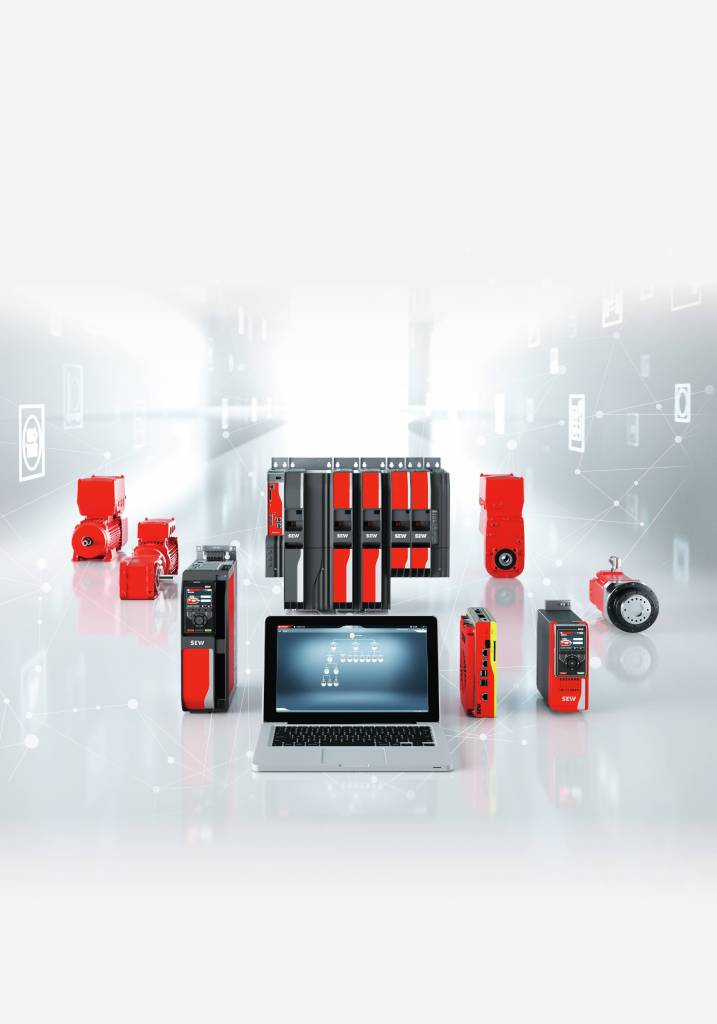
Modular, durchgängig, skalierbar: Auf diese Eigenschaften bricht Geschäftsführer Dr. Hans Krattenmacher die Eigenschaften des Automatisierungsbaukastens Movi-C herunter (zum Interview aus dem SPS-MAGAZIN 4/2024 geht es direkt über den QR-Code auf dieser Seite). SEW-Eurodrive positioniert sich damit als Anbieter kompletter Antriebs- und Automatisierungslösungen aus einer Hand – inklusive Software und Services. Mit konfigurierbaren Antrieben und durchgängiger Steuerungstechnik will SEW die Gerätevarianten reduzieren, ohne auf Funktionalität, wie bei Motion oder Safety, zu verzichten. Ein zentraler Aspekt ist es laut Krattenmacher zudem, bei steigenden Ansprüchen stets Einfachheit und Nutzerfreundlichkeit sicherzustellen.
Dieses Angebot muss SEW-Eurodrive natürlich produktionsseitig abbilden können. Maßgeblichen Anteil daran hat die Elektronikfertigung in Bruchsal. Auf 30.000m² wird dort eine Vielzahl an Geräten produziert. Dazu gehören:
- Antriebselektronik für den Schaltschrank vom Einfach-Umrichter über Standard- oder applikationsspezifische Geräte bis zum modularen Servo-Umrichter.
- Frequenzumrichter für die Wandmontage in IP54 bis IP66 für Anwendungen, bei denen die Anschaffung eines Schaltschrankes vermieden werden soll.
- Umrichter für die dezentrale Installation, die sich direkt auf oder ganz nah am Motor bzw. Getriebemotor platzieren lassen.
- Motorstarter für Einsätze, bei denen ein Motor nur ein- und ausgeschaltet oder die Drehrichtung umgeschaltet werden muss.
- Steuerungstechnik für den Schaltschrank oder für dezentrale Anwendungen sowie I/O-Module, um die Antriebe automatisierungsseitig einzubinden.
Um einen Eindruck der Dimensionen zu geben: Jeden Monat fertigt SEW-Eurodrive rund 70.000 bis 90.000 Umrichter. Mittelfristig will man für bis zu 1,2 Millionen Geräte pro Jahr gerüstet sein. Um diese Zahlen zu erreichen, hat das Unternehmen kurz vor der Pandemie in Bruchsal eine neue Elektronikfertigung in Betrieb genommen, die – genauso wie das Produktionswerk in Graben-Neudorf – als sogenannte Schaufensterfabrik, also als Musterbeispiel für die zukunftsfähige, smarte Fertigung positioniert ist. Ein erstes unübersehbares Indiz dafür ist die Flotte an autonomen Transporteinheiten, die in der Produktion unterwegs ist. Ein weiteres: Um die Fertigungsanlagen bestmöglich auf die spezifische Elektronik abzustimmen, baut SEW-Eurodrive fast alle Betriebsmittel selbst.
Was den organisatorischen Aufbau angeht, ist die gesamte Produktion in eigenständige Produktionsbereiche unterteilt, den sogenannten Small Factory Units (SFU). Der jeweilige SFU-Leiter ist eigenständig dafür verantwortlich, dass sein Bereich störungsfrei läuft und so abliefert, wie geplant. Dafür werden alle Kennzahlen und Performance-Informationen über das interaktive Cockpit in Echtzeit visualisiert. Egal ob Auslastung, Durchsatz, Soll/Ist-Vergleich oder Fehlerrate: Der SFU-Leiter kann bei Bedarf jederzeit eingreifen und entsprechende Maßnahmen einleiten.
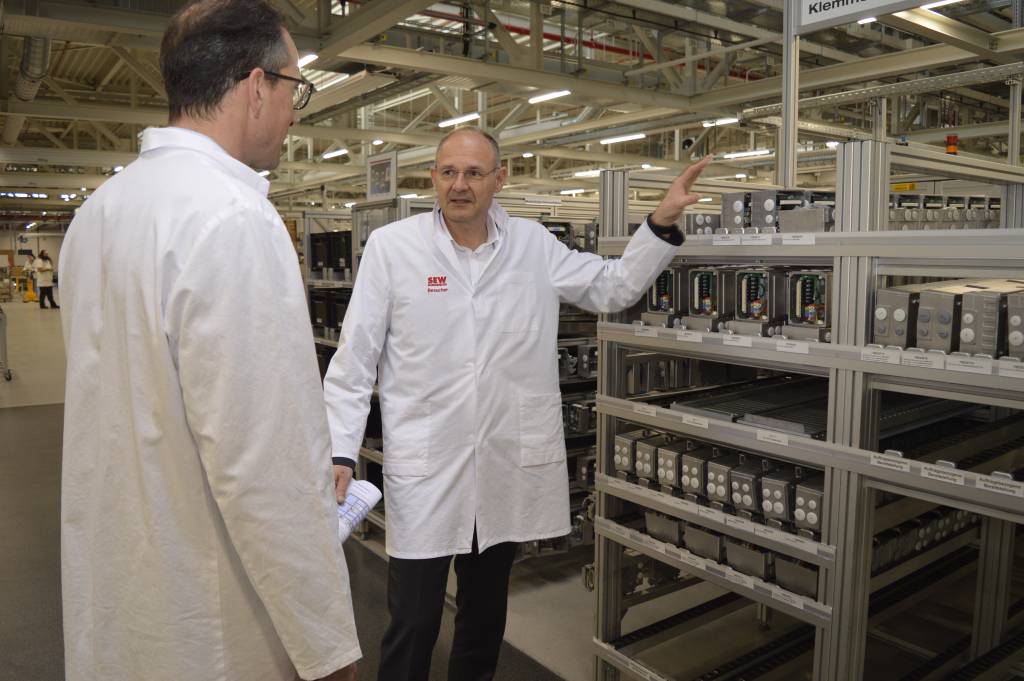
Lager als Rückgrat
„Das Rückgrat unserer Elektronikfertigung bildet das vollautomatische Behälter- und Palettenlager“, erklärt der Geschäftsführer. „Hier werden alle Lieferungen eingeliefert, egal ob große Werkstücke oder Kleinteile.“ Das Lager bietet Platz für 232.000 Behälter und fast 10.000 Stellplätze für Paletten, Vollwandbehälter oder Gitterboxen. „Natürlich basiert das Lager komplett auf SEW-eigener Antriebstechnik“, führt Krattenmacher aus. In der angeschlossenen Kommissionierung werden die Bauteile aus dem Lager dann genau so für die entsprechenden Aufträge sortiert und vorbereitet, wie es die Montagestation benötigt. Eine zentrale Rolle spielen die fahrerlosen Transportfahrzeuge, bei SEW-Eurodrive mobile Logistikassistenten genannt, kurz MLA. Sie wurden vom Unternehmen selbst entwickelt und kommen etwa auch am Standort Graben-Neudorf zum Einsatz. Das Lager umfasst 24 Stationen für automatische Übergaben an die MLA zur sequenzgesteuerten Ein- und Auslagerung. „Einen klassischen Milkrun nutzen wir eigentlich nur noch in Sonderfällen“, so Krattenmacher. Die hohe Lagertiefe und Flexibilität seien Voraussetzung für das Prinzip der auftragsneutralen Fertigung. „Wir fürchten uns nicht vor hohen Lagerbeständen. Schließlich bilden sie die Voraussetzung für kurze Lieferzeiten.“ Diesen Ansatz hätten die Erfahrungen aus der Lieferkettenkrise nochmal bestärkt.
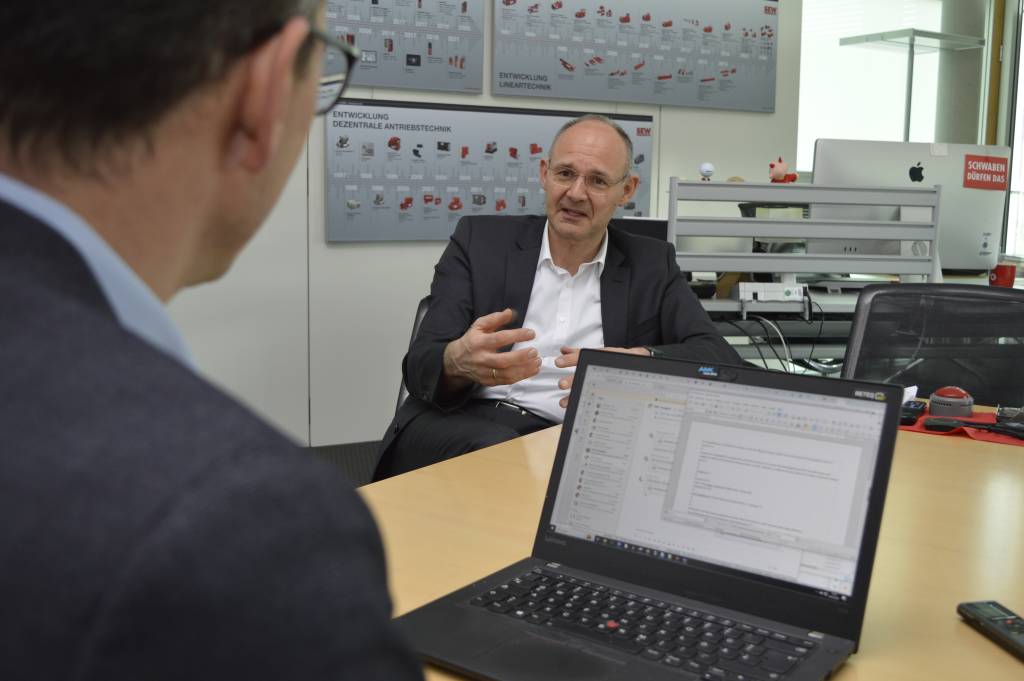
Hohe Wertschöpfung
Die SMD-Fertigung markiert als SFU den Beginn des Wertschöpfungsprozesses in der SEW-Elektronikfertigung. Dort werden Leiterplatten on demand für die zu fertigenden Geräte produziert. Dafür stehen acht SMD-Linien für die spezifisch passenden Rüstfamilien bereit. So bringt es das Unternehmen auf rund 800 bis 1.000 verschiedene Leiterplatten pro Jahr und bis zu 90 Millionen bestückte Bauteile pro Monat.
Die Montage- und Produktionsbereiche in der SEW-Fertigung sind – ebenfalls als SFUs – auf die jeweiligen Baureihen und Geräte ausgerichtet. Egal ob dezentrale oder zentrale Produkte: Der Fertigungsprozess ist standardisiert und stets nach dem gleichen Schema aufgebaut. Die richtige Leiterplatte und alle Bauteile werden angeliefert, montiert und getestet. Jede Montagezelle hat ihre eigene Prüfanlage. Die fast fertigen Umrichter werden dann in einem Puffer auftragsneutral zwischengelagert, an dessen Füllgrad sich die gesamte Montagestation orientiert. Sobald eine Untergrenze erreicht ist, läuft die Fertigung an dieser Station automatisch an. „Damit passen wir die Produktionsleistung exakt an den tatsächlichen Bedarf an“, betont der Geschäftsführer. „Es wird immer rechtzeitig produziert, bevor die Puffer leer sind.“
Spezifischer Abschluss
Das Customizing findet bei SEW möglichst spät statt. Erst beim jeweiligen Auftrag werden die Umrichter aus den Puffern abgeholt, ggf. um Optionskarten und andere Besonderheiten erweitert und zusammen mit dem passenden Zubehör zur Kommissionierung am Warenausgang gebracht. Die Grundkomponenten müssen also nicht erst in ein Lager gebracht werden, sondern stehen direkt am Ort der Entstehung zur Entnahme bereit. Alle Puffer sind dabei – vergleichbar mit den Regalen eines Supermarktes – direkt zum Logistikweg ausgerichtet. Das schafft hohe Transparenz bezüglich der Komponentenverfügbarkeit und ermöglicht den Werkern im Produktionsbereich, selbstständig, ohne externe Steuerung, die richtige Variante zur richtigen Zeit nachzubauen. Damit ist ein kontinuierlicher Materialfluss mit geringstmöglichen Beständen an Halbfertigerzeugnissen gewährleistet. „Vor der Supply-Chain-Krise-Krise hatten wir eine Liefertreue von 99,9 Prozent. Durch die Bauteilknappheit konnten wir dieses Versprechen erstmals nicht einhalten“, blickt Hans Krattenmacher zurück. „In diese Situation wollen wir natürlich nicht mehr kommen.“ Deswegen stockt SEW-Eurodrive die Vorräte im Lager weiter auf, um künftig zwölf bis 18 Monate überbrücken zu können.