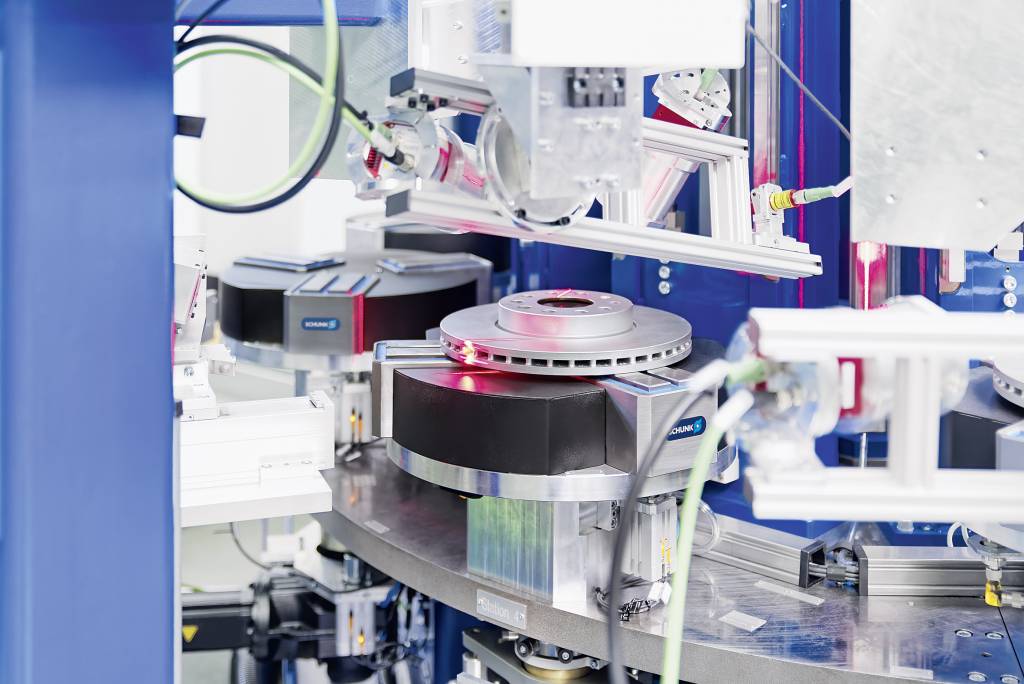
Herausfordernde Automatisierungsprojekte sind eine Stärke von Matheus. Immer wieder springt das Unternehmen in die Bresche, wenn herkömmliche Lösungen an Grenzen stoßen. So auch bei einer vollautomatisierten Prüfanlage für Bremsscheiben mit variablem Größenspektrum. Ausgangspunkt für das Projekt war eine Kundenanfrage, bei der die Schwächen einer herkömmlichen Prüfzelle eliminiert werden sollten: Bauteiltoleranzen und die Beschaffenheit der Gussteiloberfläche hatten bei Anlagen anderer Hersteller immer wieder dazu geführt, dass auch Gutteile ausgeschleust wurden. Hauptgrund war das Taumeln der über Rollen angetriebenen Teile während des Prüfvorgangs, wodurch die Messung verfälscht oder gänzlich unmöglich wurde. Nach einer eingehenden Analyse entwickelte Matheus ein alternatives Konzept, dessen zentrales Element Magnetspannlösungen von Schunk sind, auf denen die Gussteile gespannt werden. Der Vorteil: Ein prozesssicherer Prüfprozess. Zudem können Größe, Gewicht und Form der Bremsscheibentypen stark variieren, ohne dass der automatisierte Prozess langwierig für Rüstarbeiten unterbrochen werden muss. Sowohl bei der Fixierung der Bremsscheiben auf den Prüfsatelliten als auch beim anschließenden Verpacken in Transportboxen erweist sich die Schunk Magnettechnologie als effiziente und zuverlässige Lösung.
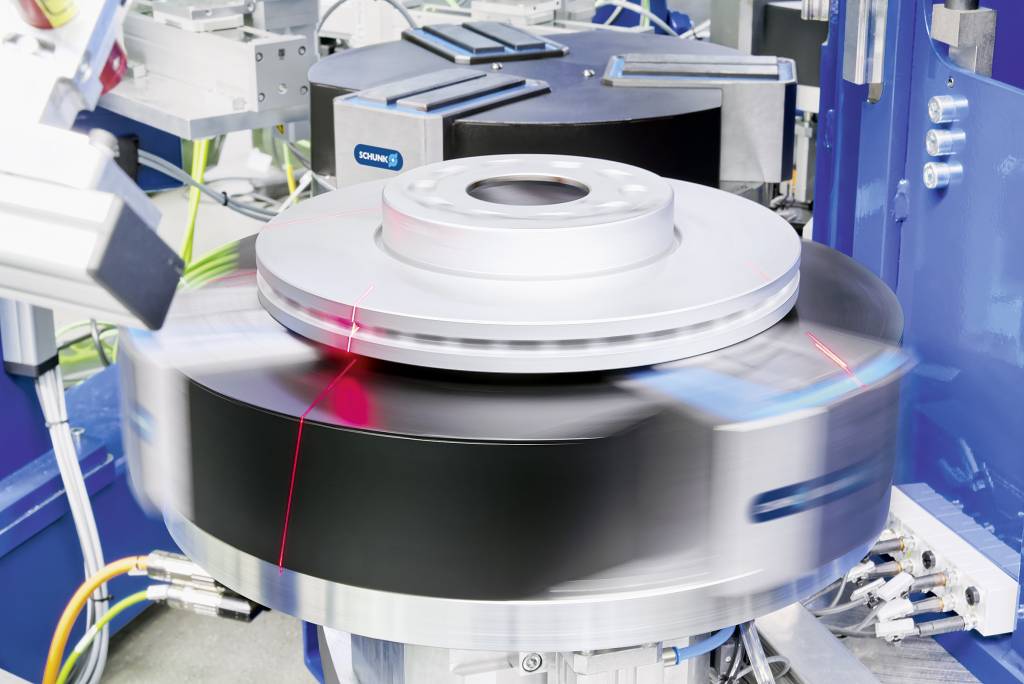
Taktzeit von 4,5 Sekunden Über ein Transportband werden die Bremsscheiben aus der Vorbearbeitung zugeführt und zunächst gereinigt. Eine von Matheus konstruierte, mechanische Greifeinheit platziert sie anschließend exakt zentrisch auf einem Satelliten-Drehteller, der mit einer Magnetlösung ausgerüstet ist. Da die Unterseite der Gussteile eine vergleichsweise ebene Fläche ohne Grat aufweist und die darunterliegenden Drehteller präzise gelagert sind, ist eine rotationssymmetrische Spannung gewährleistet – ein wesentlicher Vorteil gegenüber der herkömmlichen Rotation der Bremsscheiben über Rollen. Zur Aktivierung der Spannlösung versorgt eine verfahrbare Schnellkupplung die Spanneinheit mit einem kurzen Stromimpuls. Der eigentliche Spannvorgang ist in nur 300 ms abgeschlossen. Die Elektropermanentmagnete sorgen auch dann für einen zuverlässige Halt, wenn die Energiezufuhr unmittelbar nach der Aktivierung abgekoppelt wird. Alle neun Drehteller des Rundtakttischs sind mit den identischen Magnetspannmitteln ausgestattet: Jeder Drehteller verfügt über drei sternförmig angeordnete Spannsegmente, die eine optimale Auflage gewährleisten und deren Haltekraft selbst bei konvexen oder konkaven Oberflächen ausreicht. „Angesichts der Beschleunigung beim Prüfvorgang und der kurzen Taktzeit haben wir die bei Magnetgreifern übliche Leichtbaulösung in Segmentbauweise bevorzugt. Damit sparen wir Gewicht und können kürzeste Taktzeiten realisieren, ohne dass sich das Modul übermäßig erwärmt“, erläutert Attila Heinrich, technischer Berater für mechatronische Greifsysteme bei Schunk. „Ein Systemvergleich hatte zuvor gezeigt, dass für die Fixierung der Bauteile auf dem Drehteller grundsätzlich auch eine Spannlösung auf Basis der Quadratpol- oder Radialpoltechnologie infrage kommen würde. Angesichts der kurzen Taktzeiten und des damit verbundenen Wärmeeintrags wurde jedoch der in der Greiftechnik verbreiteten Segmentbauweise der Vorzug gegeben. Mit ihr lassen sich kurze Taktzeiten bei maximaler Prozesssicherheit gewährleisten.“ Präzise Prüfung Indem die Bremsscheiben an der Unterseite per Magnet gespannt werden, sind sowohl die Oberseite als auch der Rand der Bremsscheiben für die optische Prüfung frei zugänglich. An drei aufeinanderfolgenden Prüfstationen werden die Drehteller mit den gespannten Bauteilen definiert rotiert, so dass eine exakte Auswertung möglich ist. Anschließend wird die Magnetspannung über einen erneuten Stromimpuls gelöst, die Scheibe mechanisch von innen gegriffen und es folgen diverse Laserprüfungen der Unterseite. Insgesamt 16 Kameras erfassen an den einzelnen Stationen jeweils unterschiedliche Areale der Bremsscheiben und detektieren Gussfehler, beispielsweise Wölbungen an der Oberfläche oder fehlende Rippen. 21 Verfahrachsen stellen sicher, dass sowohl die Laser als auch die Sensoren stets optimal positioniert sind und das komplette Bauteilspektrum abgedeckt werden kann, ohne dass ein langwieriger manueller Eingriff erforderlich ist. NIO-Teile werden automatisch gekennzeichnet, ausgeschleust und händisch auf ihre Verwendbarkeit geprüft. Magnettechnik auch beim Verpacken IO-Teile wiederum gelangen nach der Kennzeichnung über ein Förderband zu einer separaten Verpackungszelle und werden dort von zwei Robotern, die mit störkonturarmen SCHUNK EGM Magnetgreifern ausgestattet sind, platzsparend nach einem vom OEM vorgegebenen Packmuster in Gitterboxen abgestapelt. Auch hier zahlt sich die hohe Flexibilität der Magnettechnik aus: Mit den Greifmodulen lassen sich sämtliche Bauteilgrößen und -varianten handhaben, ohne dass ein Wechsel des Greifers erforderlich ist. Da auch beim EGM in aktiviertem Zustand keinerlei Energiezufuhr erforderlich ist, bleiben die Teile selbst bei einem Not-Aus oder einem plötzlichen Stromausfall zuverlässig gegriffen. Die standardisierten Magnetgreifer sind wahlweise mit einem, zwei oder vier Polpaaren in den Polgrößen 30, 50 oder 70 mm erhältlich. Darüber hinaus sind anwendungsspezifische Sonderlösungen möglich. Über Gewinde und Stiftbohrungen können die Magnetpole schnell und einfach mit Polverlängerungen ausgestattet und optimal an das jeweilige Werkstück angepasst werden. Aufgrund ihrer kompakten Abmessungen bieten die Magnetgreifer gerade auch in beengten Räumen wie etwa den Transportboxen erhebliche Vorteile. Ein OPR Kollisionsschutz stellt in den Greifsystemen bei Matheus zusätzlich sicher, dass der Prozess im Falle einer Kollision, beispielsweise aufgrund einer beschädigten Transportbox, sofort gestoppt wird. Kleinere Abweichungen werden über einen Z-Ausgleich kompensiert. „Jede Bauteilvariante hat ein eigenes Packmuster, das exakt umgesetzt werden muss“, berichtet Matheus Projektmanager Björn Hammann. „Wir können also nicht einfach einen großen Magneten nehmen und fertig. Vielmehr mussten wir individuell untersuchen, wie die Teile gegriffen und abgelegt werden. Auf keinen Fall dürfen die Greifer über den Rand der Gitterbox hinausschauen. Je kompakter sie also ausfallen desto besser.“ Über einen Federbolzen lassen sich die Stichmaße der Greifer mit wenigen Handgriffen manuell verstellen. Die Ansteuerung der einzelnen Magnete erfolgt zentral über den Hauptschaltschrank, wobei zwei Controller für die Aktivierung und Deaktivierung der Module am Drehtisch und je zwei Controller für jeden Roboter verbaut wurden. Im Regelbetrieb sind die beiden Magnetgreifer jedes Roboters gekoppelt, so dass das Greifsystem als Ganzes aktiviert beziehungsweise deaktiviert wird. Bei Bedarf könnten die beiden Magnetmodule über eine Zweikanal-Steuereinheit oder ein Relais auch einzeln geschaltet werden. Um den Verschleiß der Magnetpole zu verhindern, sind diese mit einem aufgeschraubten Polschutz aus ST52 ausgestattet, der gegebenenfalls überschliffen oder bei Bedarf auch mit einer individuellen Kontur ausgeführt werden kann.
Die Zykluszeit der Prüfanlage liegt bei 4,5s. Eine so kurze Taktzeit ist nur mit einer speziellen Magnettechnik realisierbar, die Schunk auch bei seinen Magnetgreifern nutzt. Ansonsten würden die Module innerhalb kürzester Zeit überhitzen. – Bild: Schunk GmbH & Co. KG Die Greifsysteme an den beiden Robotern ermöglichen ein flexibles Handling der unterschiedlichen Prüfteile bei minimalen Störkonturen – Bild: Schunk GmbH & Co. KG Über einen Federbolzen lässt sich das Stichmaß der Greifer an die unterschiedlichen Bauteilvarianten anpassen. – Bild: Schunk GmbH & Co. KG
Hohe Varianz ohne Rüstaufwand „Unsere Magnetspannlösung ermöglicht eine große Variantenvielfalt, ohne dass die Maschine aufwändig umgerüstet werden muss. Zudem können die Kühlkanäle der Bremsscheiben von außen auf Durchgängigkeit inspiziert werden, ohne dass Teile durch die Spannmittel verdeckt werden“, betont Björn Hammann. Während große Topfscheiben einen Innendurchmesser von bis zu 260 mm haben, beträgt der Außendurchmesser bei manchen kleinen Bremsscheiben gerade einmal 240 mm. „Die kleinste Bremsscheibe passt also durch den Innendurchmesser des größten Reibrings.“ Während der Einsatz der Magnettechnik beim Handling von Bremsscheiben bereits weit verbreitet ist, geht Matheus mit den rotierenden Spannstationen einen Schritt weiter. Sorgfalt bei der Auslegung der Magnetlösung war auch hier angebracht. So hat Schunk jede einzelne Bremsscheibe individuell geprüft und kalkuliert. „Luftspalte, Toleranzen, Temperatur, Zahl der Schaltungen, Werkstoffe – all das muss individuell für jede Bremsscheibe betrachtet und berücksichtigt werden“, erläutert Attila Heinrich. Entsprechend der jeweiligen Anforderungen können beispielsweise die Anzahl der Magnetpakete, die Art der Spulen oder die mechanische Anbindung variiert werden. Um auch für künftige Bauteilvarianten gerüstet zu sein, wurde die Anlage anhand theoretischer Minimal- und Maximaldurchmesser ausgelegt. „Solange neue Teile ähnlich aufgebaut sind wie die alten, können wir sie mit der Anlage ohne größeren Aufwand abdecken“, ist Björn Hammann überzeugt.
www.schunk.de