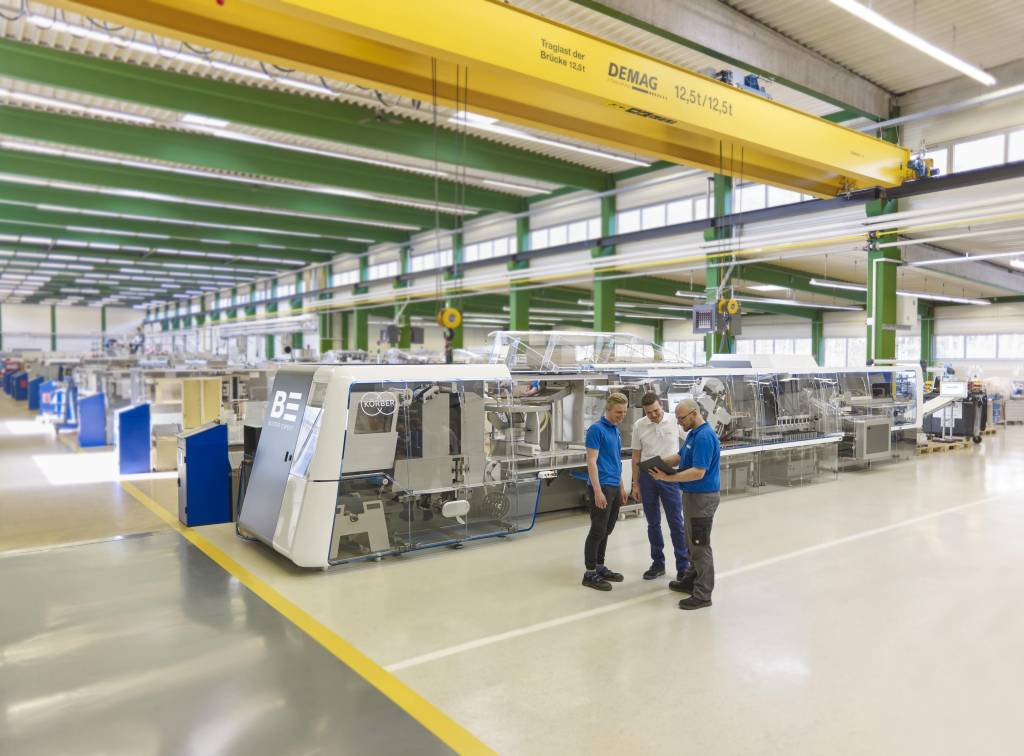
Bei der Verpackung von Medikamenten sind in der pharmazeutischen Industrie neben höchsten Qualitätsanforderungen zunehmend auch minimierte Produktionszeiten und eine flexible Nutzbarkeit der Anlagen entscheidend. Blisterverpackungen werden in der pharmazeutischen Industrie in der Regel zum Verpacken von Einzeldosen verwendet – besonders für Solida wie Tabletten und Kapseln, aber auch für Parenteralia, die etwa in Spritzen oder Ampullen abgefüllt sind. „Viele Hersteller haben für diese Aufgabe in ihrem Maschinenpark Monoblockmaschinen, die für eine spezielle Anwendung angeschafft wurden“, erklärt Ulf Leineke, Leiter der Entwicklung bei Mediseal, einem Unternehmen der Körber Gruppe mit mehr als 11.000 Mitarbeitern weltweit. „Ändern sich die Anforderungen, können diese Maschinen in der Regel nicht oder nur mit großem Aufwand verändert werden, was in vielen Fällen die Anschaffung einer neuen Blistermaschine erforderlich macht.“
Mit der modularen Blister-Expert-Plattform von Mediseal, die sowohl Blistermaschinen, als auch Kartonierlösungen umfasst, entfällt jedoch diese Notwendigkeit: „In einem modularen System können bestehende Maschinen an die Anforderungen der Zukunft angepasst werden, da sich die Funktionen der Anlage im Rahmen der vorher festgelegten räumlichen Grenzen und der definierten Schnittstellen verändern lassen“, so Leineke weiter. „Gibt es beispielsweise bei der Funktion ‚Siegeln‘ nach Inbetriebnahme der Maschine eine Innovation, kann das alte Modul gegen die neue, optimierte Variante getauscht werden, da beide kompatibel konstruiert sind.“ Auf diese Weise wird der immer kürzeren Innovationszykluszeit in der pharmazeutischen Industrie Rechnung getragen.
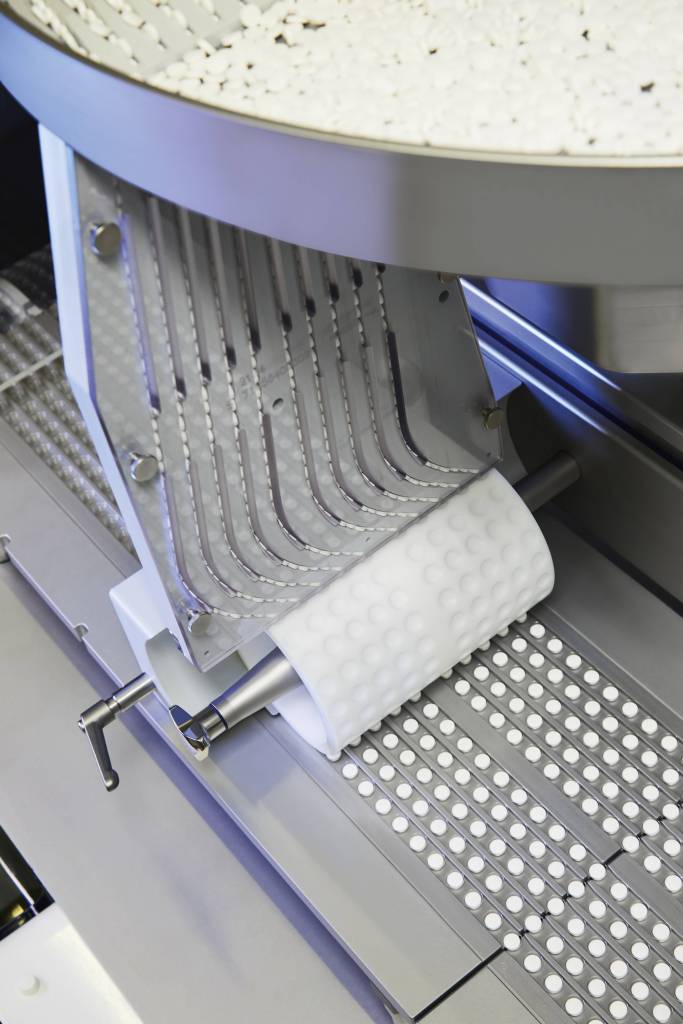
Nachrüstmöglichkeit plus Verlängerung der Maschine
Die Möglichkeit, Optionen beziehungsweise Module zu einem späteren Zeitpunkt nachzukaufen, bietet Unternehmen wie beispielsweise Lohnverpackern, die aufgrund ihrer Auftragsabhängigkeit die Anforderungen kommender Jahre kaum antizipieren können, eine besonders hohe Zukunftssicherheit. Das zeigt sich etwa am Beispiel der Verpackung von Ampullen: Diese werden im Normalfall in eine Blisterverpackung eingelegt, die oben nicht durch eine Deckelfolie versiegelt wird. Ein Unternehmen mit einem entsprechend lautenden Auftrag kann bei einem modularen System wie der Blister-Expert-Plattform eine Maschine anschaffen, die auf diesen aktuellen Auftrag zugeschnitten ist und auf die für die Versiegelung mit Deckelfolie notwendige Komponente verzichtet.
Müssen zu einem späteren Zeitpunkt Produkte mit Deckelfolie ausgestattet werden, etwa weil im Anschluss eine Sterilisation erfolgt, lässt sich die entsprechende Station nachrüsten. Dabei ermöglichen die normierten modularen Anschlussstellen sogar, die Maschine im Feld zu verlängern. „So ist es etwa auch realisierbar, Blistermaschine und Kartonierer voneinander zu trennen und ein weiteres Modul dazwischenzusetzen“, erklärt Stefan Kemner, System Integration & Portfolio Manager bei Mediseal. Bei herkömmlichen Blisterlinien ohne modularem Konzept stehen Unternehmen aufgrund der fehlenden Nachrüstbarkeit dagegen vor der Entscheidung, beim Kauf der Linie zukünftige Eventualitäten mit abzudecken und teure Funktionen mit anzuschaffen, die später möglicherweise gar nicht benötigt werden.
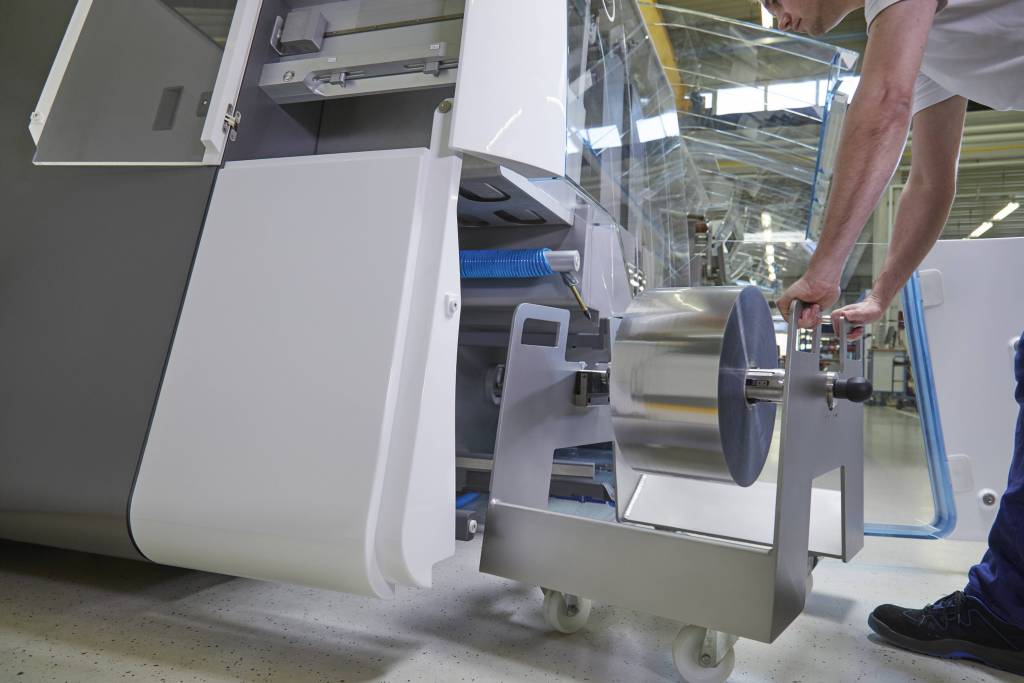
Verkürzte Lieferzeiten durch Configure-to-Order
Die Fertigung von Blisterlinien nach einem modularen Baukastenprinzip hat noch weitere Vorteile: Sie erlaubte Mediseal bei der Blister-Expert-Plattform die konsequente Umsetzung eines Configure-to-Order-Ansatzes. „Der Kunde lässt uns zunächst grundlegende Informationen zukommen, die dann in einen Konfigurator eingespeist werden – zum Beispiel, ob Solida oder Parenteralia verpackt werden und welche Leistungsklasse benötigt wird. Danach kann zwischen verschiedenen Optionspaketen ausgewählt werden, also etwa einer besonders leicht umzubauenden, ergonomischen oder produktiven Maschine“, erklärt Kemner. „Damit wird die Anlage genau auf das Zielprodukt zugeschnitten.“ Der Konfigurator identifiziert die notwendigen Module und auf Basis dieser Informationen wird der Produktionsauftrag erstellt. Mediseal beschafft dann direkt die notwendigen Bauteile beziehungsweise baut vormontierte Module zusammen. Dies unterscheidet sich vom klassischen Vorgehen, bei dem zunächst ein Konstrukteur auf Basis des Kundenauftrags Einzelteile und Baugruppen zusammenstellt und daraus den Produktionsauftrag erstellt. Dieser aufwendige und fehleranfällige Schritt entfällt beim Blister-Expert-System. Zudem lässt sich auch jeder Kartonierer hinter die Blistermaschine konfigurieren, während bei vielen anderen Serien oft nur genau ein Kartonierer zur ausgewählten Blistermaschine passt.
Zusätzlich können von Mediseal Sonderkonstruktionen vorgenommen werden. „Möchte ein Kunde beispielsweise eine UV-Desinfektionsstation oder eine andere Option, die wir noch nicht als Standardkomponente in unseren Pool von Modulen aufgenommen haben, entwickeln wir das benötigte Element“, so Leineke. „Das ist möglich, weil wir entweder an der relevanten Stelle ohnehin noch Platz in der bisher konfigurierten Maschine haben oder dann eben die Maschine etwas verlängern.“ Während das Zusatzmodul konstruiert wird, werden die Standardmodule bereits produziert, sodass die Anlage insgesamt schneller in Betrieb genommen werden kann.
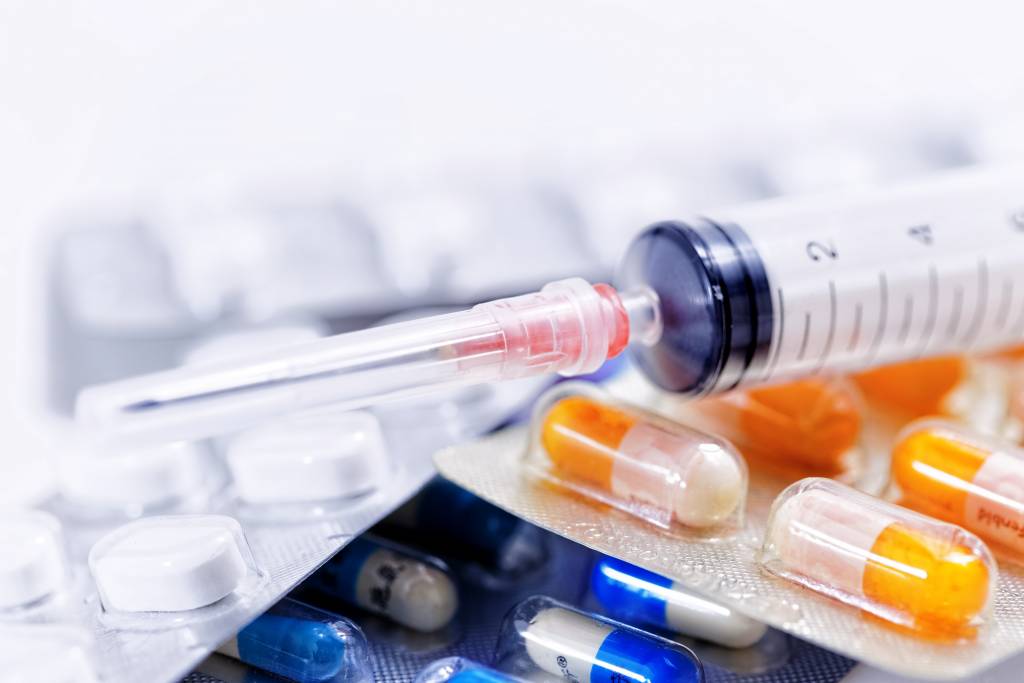
Modularität reduziert Stillstandszeiten
Gleichzeitig trägt das modulare System dazu bei, die Stillstandszeiten der Maschine zu minimieren. Werden bei Anpassungen an der Maschine alte Module durch neue ersetzt oder zusätzliche nachgerüstet, reduziert sich auch der Validierungsaufwand signifikant. „Der pharmazeutische Hersteller muss nicht die komplette Maschine noch einmal validieren, sondern nur das neue Modul“, erläutert Leineke. „Damit steht die Anlage in Upgradefällen deutlich kürzer still als Systeme, die über keine modulare Struktur verfügen.“ Hinzu kommt: Wenn eine bereits in Produktion befindliche Maschine ausfällt und eine Einzelkomponente defekt ist, kann diese Komponente bei einem modularen Baukastensystem durch ein vorher beim Maschinenhersteller komplett in Betrieb genommenes Modul ausgetauscht werden. Bei herkömmlichen Blisterlinien ist es dagegen meist notwendig, dass ein Techniker zunächst die Maschine demontiert und feststellt, welche einzelnen Teile betroffen sind. Häufig können die passenden Ersatzteile erst dann aus dem Lager entnommen werden, was im Vergleich deutlich mehr Zeit in Anspruch nimmt.