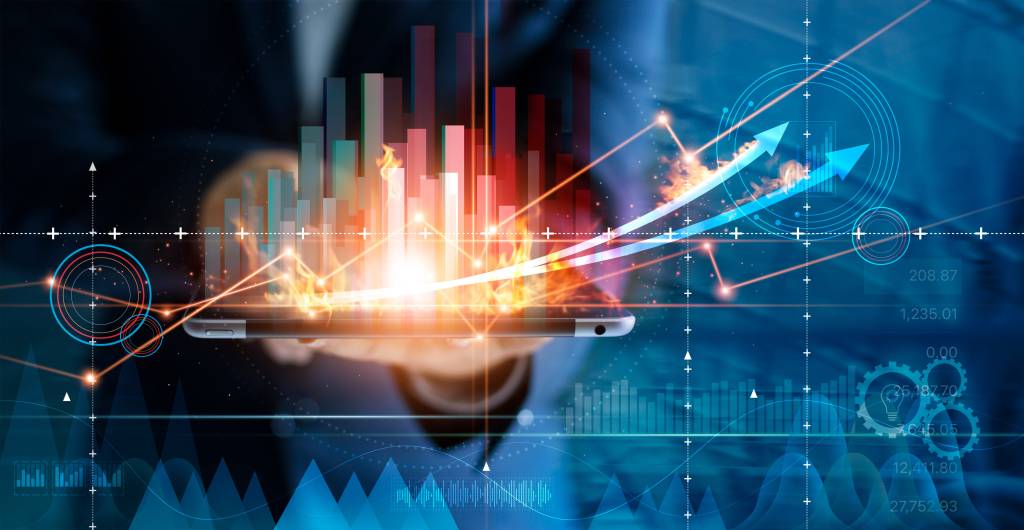
Vernetzte Produktionslandschaften bergen Chancen für viele Unternehmen. Firmen setzen auf digital vernetzte Produktions- und Wertschöpfungsprozesse, horizontale sowie vertikale Integration, Digital Twins und Predictive Maintenance. Doch was kommt eigentlich danach? Was bringt die Zukunft in der Industrie? Wissenschaftler sagen einen Paradigmenwechsel von einer smarten Produktion hin zu einem innovativen Konsumverständnis voraus. Doch was verbirgt sich genau dahinter?
Was ist die Industrie 5.0?
Forschende der Queensland University of Technology in Brisbane definieren den Begriff Industrie 5.0 als ein grundlegendes Umdenken: Es gehe künftig nicht mehr um smarte Produktionsprozesse, sondern vielmehr um smarten Konsum. Das Fundament dazu sind hochgradig individualisierte Produkte und Services. IoT-, Cloud- und App-Technologien machen das schon heute möglich und die Möglichkeiten sind noch längst nicht vollständig ausgeschöpft. Bereits im Umfeld von Industrie 4.0 entstehen Produkte, die sich vor und während der Produktion den Bedürfnissen und Wünschen der Kund:innen anpassen lassen. Ein Beispiel ist die Konfiguration eines Neuwagens: Dabei gibt es laut Internetportal meinauto.de für 22 BMW-Modelle etwa 1.295 Varianten und weitere individuell anpassbare Ausstattungsmerkmale – u.a. 30 verschiedene Lenkräder. So kann nahezu jeder noch so spezielle Kundenwunsch erfüllt werden. Doch egal wie hoch der Individualisierungsgrad bisher war, spätestens mit dem Verlassen der Produktionsstraße hat der Hersteller keine Möglichkeit mehr, das Produkt noch einmal anzupassen oder gar neue Funktionalitäten zu implementieren. Mögliche Mehrwerte bleiben den nächsten Produktionslinien vorbehalten.
Kundenzufriedenheit steigern
Rechenleistung, Software und Konnektivität ebnen smarten Produkten einen soliden Weg, um ihre Entwicklung weiter voranzutreiben. Was das in der Praxis bedeutet, präsentiert beispielsweise Tesla: Neuwagen können durch Over-the-Air-Updates über Nacht neue Fähigkeiten erlangen – nachdem sie gekauft wurden. Das Unternehmen versorgt die digitalen Komponenten seiner Fahrzeugflotte ständig mit neuen Funktionen und verbessert so beispielsweise den Autopiloten stetig. Das Ergebnis ist eine konstant steigende Zufriedenheit und ständig neue Customer Experience auch für Bestandskunden. Dies ist der erste Schritt hin zur Industrie 5.0. Da die massive Vernetzung Hersteller dazu befähigt, auch nach dem Kauf und im gesamten Produktlebenszyklus auf die Kundenbedürfnisse einzugehen, wirkt Industrie 5.0 fast wie eine Gegenbewegung zur aktuellen Industrie 4.0 – denn die Individualisierung während der Produktionsphase verliert damit an Relevanz. Digitaler Konsum führt in der Zukunft dazu, dass Hersteller überhaupt keine physischen Dinge mehr produzieren und vertreiben müssten, um neue Mehrwerte für den Markt zu generieren. Die Individualisierung und der smarte Konsum gelingen künftig ausschließlich über Software-Komponenten. Hardware-seitig wird dann eine Handvoll Varianten ausreichen und die Produktion kann wieder stärker auf Standardisierung setzen.
Digitale Produkte
Deutsche Unternehmen produzieren und vertreiben jedes Jahr Millionen von Dingen. Die Kernkompetenz liegt in der Entwicklung und Herstellung von hochwertigen Fahrzeugen, Geräten und Maschinen. Doch die immer stärker werdende Konkurrenz aus Asien, die Ressourcenknappheit und das Umdenken am Markt führen dazu, dass die Wachstumsaussichten in der reinen Produktion begrenzt sind. Die Konsumkultur wandelt sich hin zu mehr Nachhaltigkeit und Weitsicht, sodass Unternehmen neue Ansätze finden müssen, um Werte für ihre Zielgruppe zu generieren. Die zunehmende Vernetzung hilft dabei – eine Errungenschaft der Industrie 4.0 und der Industry of Things. Unternehmen statten ihre Produkte zunehmend mit digitalen Komponenten und Sensoren aus, sodass diese miteinander kommunizieren, Signale empfangen und Technologien wie 5G und LoRaWan nutzen können. IoT-Komponenten schaffen einen transparenteren Einblick in den Zustand einzelner Produkte und ganzer Prozesse und ermöglichen so ein rechtzeitiges Eingreifen bei drohenden Schwierigkeiten. Doch ein wichtiger Schritt fehlt noch: die digitale Produktisierung. Das kann in der Praxis beispielsweise bedeuten, dass Hersteller aufgrund der gelieferten Daten ihrer vernetzen Dinge Rückschlüsse ziehen, welche Optimierungen möglicherweise Sinn ergeben. Je transparenter der Blick auf die jeweilige Maschine während der Nutzung ist, umso besser kann der Produzent erkennen, wie er sie noch effizienter gestalten könnte. Aus diesem Einblick ergeben sich zahlreiche Chancen für neue Servicemodelle und Beratungsangebote, die mit flexiblen, nutzungsabhängigen Preismodellen überzeugen können.