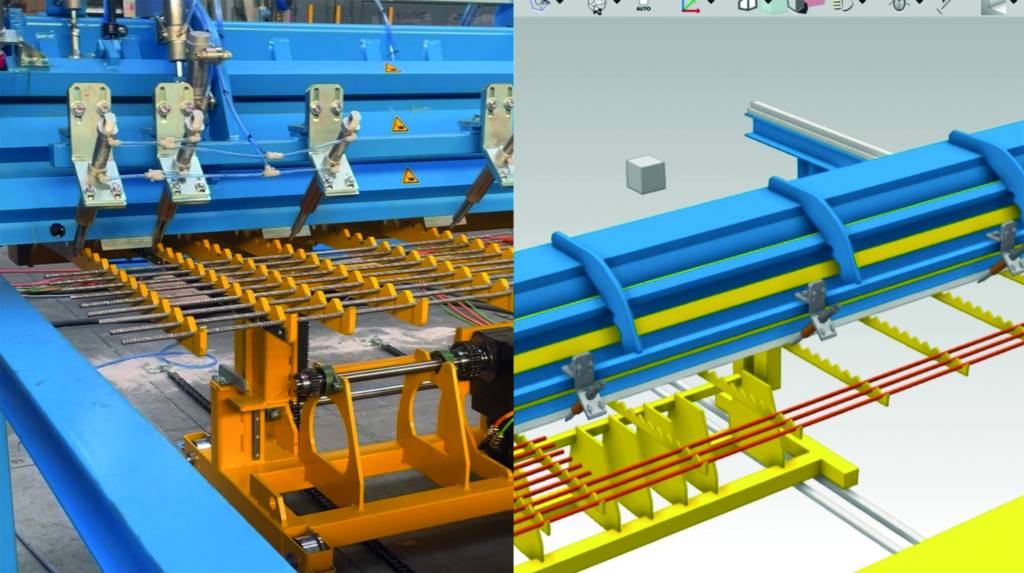
Die Progress Maschinen & Automation AG fertigt Produktionslinien nach den Anforderungen und Vorgaben der Kunden. Das Unternehmen ist ein Komplettanbieter für Betonfertigteilwerke, Biegebetriebe und Mattenhersteller. Die Kunden erwarten schon früh im Planungsprozess möglichst genaue Prognosen über die Produktivität der geplanten Maschine. „Diese Berechnung gestaltete sich oft sehr schwierig und lieferte nur für einfache Produkte verlässliche Produktivitätskennzahlen“, sagt Bernd Plaikner, zuständig für Prozesse & IT-Services. „Hier bestand noch Potenzial für Verbesserung.“
Um auch die relativ langen Inbetriebnahmezeiten zu verkürzen, entschied sich der Maschinenbauer, künftig auf den digitalen Zwilling als virtuelles Pendant zur geplanten Maschine zu setzen. „Mit einem digitalen Zwilling lassen sich Produkte simulieren und anschließend Zeiten und Kennzahlen ablesen.“
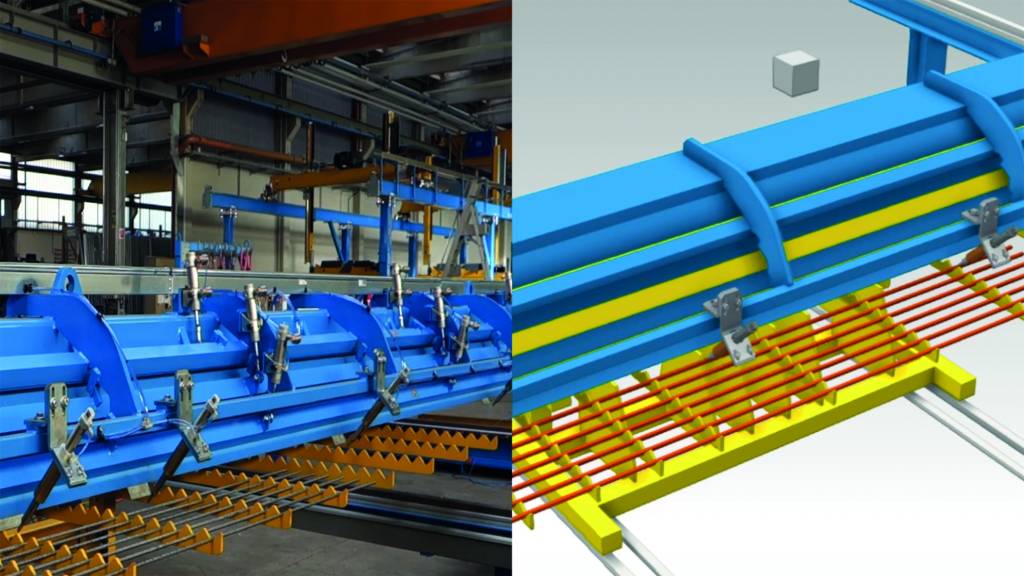
Die Entscheidung und Erwartungen
Bei einer Veranstaltung des VDMA nahm Bernd Plaikner an einem Vortrag zum Thema ‚Digitaler Zwilling‘ teil. Das Interesse war geweckt. „Wir haben uns intensiv über die Tools auf dem Markt informiert“, sagt Plaikner und das Unternehmen nahm Kontakt zu Machineering auf. Die Mitarbeiter des Münchner Herstellers von Simulationssoftware erstellten daraufhin einen ersten kleinen Prototypen, mit dem der Maschinenbauer den Einsatz des digitalen Zwillings testete. Die Ergebnisse überzeugten schließlich und Progess entschied sich für die Software iPhysics.
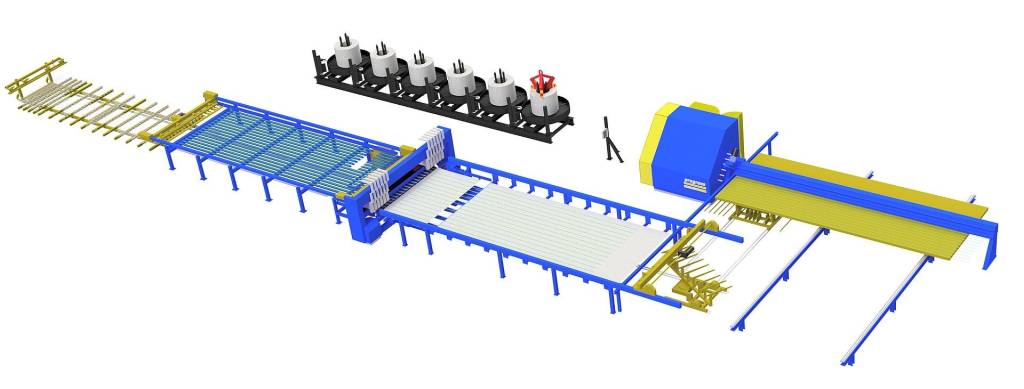
Die Implementierung
Nachdem der erste Prototyp von einem Mitarbeiter von Machineering auf Basis des Inputs der Progress-Mitarbeiter gebaut worden war, gab es zu Beginn des Projekts eine etwa vierstündige Einführung in die Software. „Bei späteren Projekten war es dann eine Kombination aus Lernen mit der Dokumentation und Unterstützung von Machineering, wenn wir nicht weiter kamen“, sagt Plaikner. „Wir konnten nach der Implementierung sehr schnell mit der eigentlichen Arbeit beginnen. Installieren und los war die Devise.“
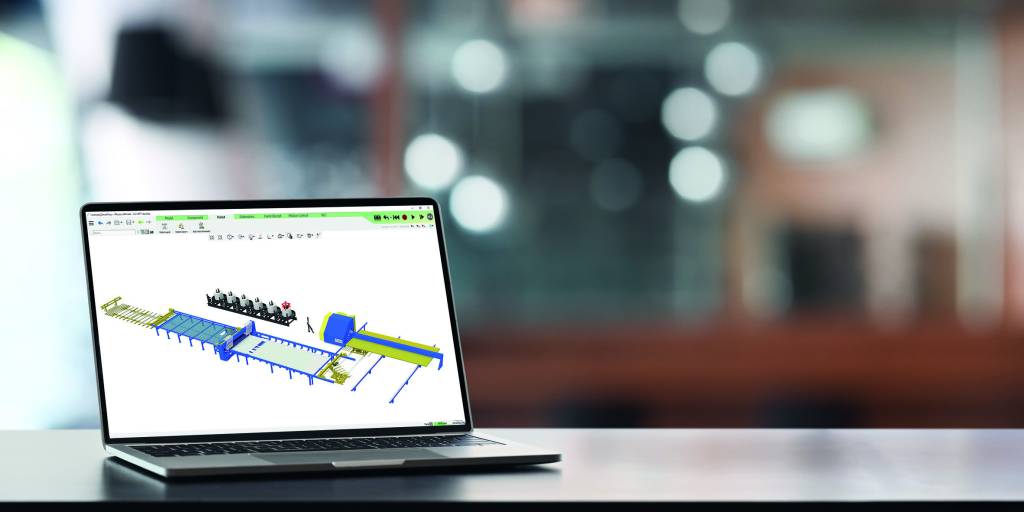
Das Ergebnis
Schon zu Beginn des Projekts war die Erstellung mehrerer digitaler Zwillinge das Ziel. „So konnten wir schon beim ersten Projekt effektiv Zeit bei der Inbetriebnahme sparen“, erklärt Plaikner. „Am Anfang war der Inbetriebnahmeprozess noch recht aufwendig, weil uns einfach noch die Erfahrung fehlte.“ Mittlerweile vergleichen die Mitarbeiterinnen und Mitarbeiter die Daten einer realen Maschine mit denen des digitalen Zwillings. „Diese Tests sollen die Verwendbarkeit des digitalen Zwillings für Leistungsberechnungen validieren. Und das tun sie“, sagt Plaikner.