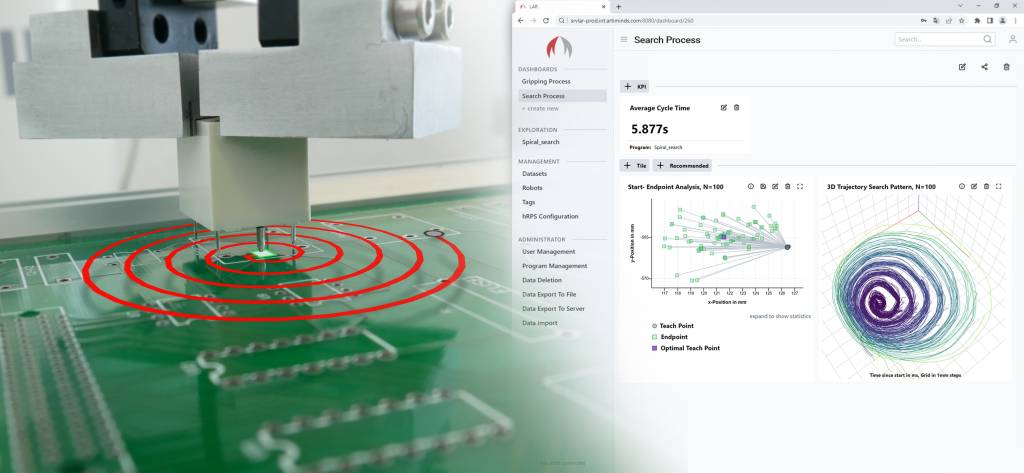
Schnelle Lieferantenwechsel, hohe Variantenvielfalt mit High-mix/Low-volume-Produktion, Produktion auf kurzfristigen Auftrag hin sowie immer kürzere Produktlebenszyklen stellen die klassische Automatisierung vor große Herausforderungen. Die klassische, starre Automatisierung wird mechanisch auf eine ganz bestimmte Aufgabe abgestimmt und oft über einen längeren Zeitraum darauf eingerichtet. Kurzfristige Veränderungen im Prozess können dadurch oft nicht abgebildet werden, sodass dies an vielen Stellen bis heute die Domäne manueller Arbeit bleibt.
Durch sensoradaptive Industrieroboter und Cobots im Zusammenspiel mit intelligenter Software können nun jedoch einige bisher manuell ausgeführte Arbeitsschritte in die Automatisierung übernommen werden. Dazu gehört, dass der Roboter mittels Kraft/Momenten-Sensoren oder Kameras Veränderungen in seiner unmittelbaren Umgebung wahrnehmen kann. Darüber hinaus muss diese Wahrnehmung in Form von Prozessdaten über viele Produktionstakte hinweg in sauber aufbereiteter Form gesammelt werden. Auf Basis dieses Erfahrungswissens zum aktuellen Prozess kann intelligente Software anschließend Programmanpassungen berechnen, die die Roboteraufgabe an aktuelle Werkstück- oder Anlageneigenschaften adaptieren.
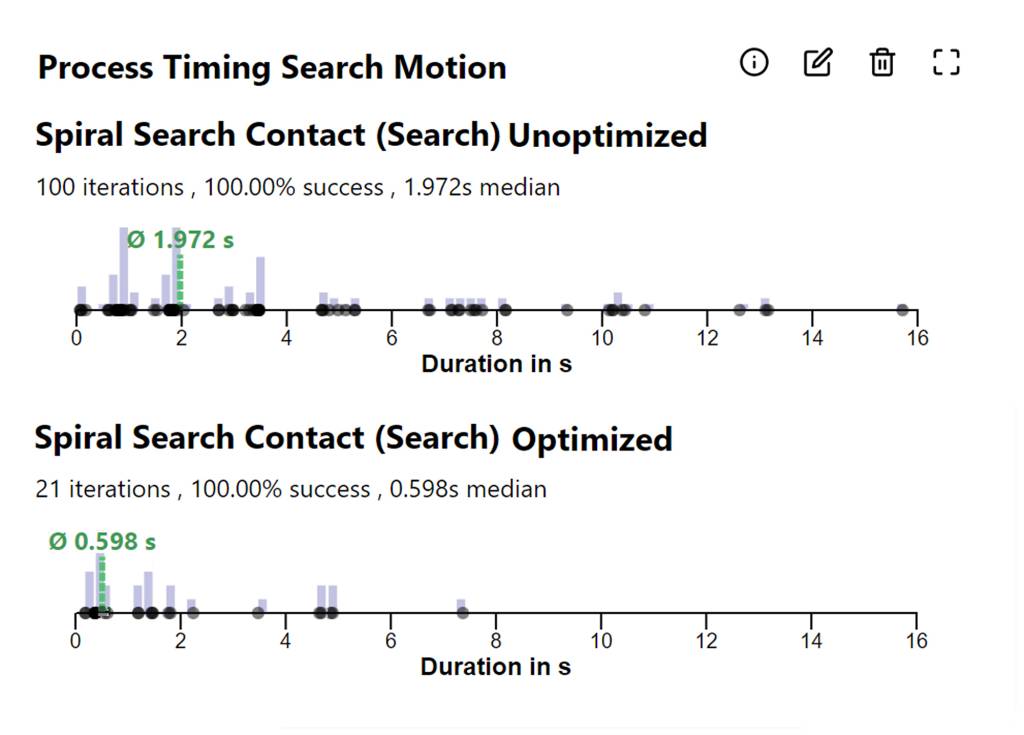
Datengetriebene Anpassung der Roboterposen
Teach-Punkte bzw. einzelne Roboterposen bilden räumliche Schlüsselelemente für Roboterprogramme mit sensorbasierten Teiloperationen. Das kann z.B. der Startpunkt für eine kraftsensitive Fügeoperation oder die Richtung einer Kontaktfahrt sein. Solche Schlüsselposen müssen bei sensoradaptiven Roboterprogrammen herkömmlich mühsam iterativ händisch angepasst werden. Bei kleinräumigen Varianzen oder stochastischen Streuungen über eine große Anzahl an Werkstücken ist eine manuelle Anpassung oft überhaupt nicht mehr möglich. Das gleiche gilt für eine kurzfristige Nachoptimierung im laufenden Betrieb.
Datengetriebene, automatische Anpassungen können diese Herausforderungen bewältigen. Während des Produktivbetriebs werden vom Roboter Bewegungsdaten in hoher Abtastrate gesammelt. Aufgrund der sensoradaptiven Bewegungen können diese Daten Aufschluss über tatsächliche geometrische Anordnungen während der Operationsaufführung liefern, die aus der Bewegungsanpassung basierend auf den Sensormessungen resultieren. Typische zeitliche Abtastraten liegen um die 250Hz bei räumlichen Auflösungen bis 50m sowie Kräften bis unter 0,1N. Mittels semantischer Gliederung eines Roboterprogramms können die Daten nach ihrer Sammlung klar definierten Bewegungselementen zugeordnet werden, die wiederum Schlüsselposen, Teach-Punkte enthalten. Auf Basis der gesammelten Laufzeitdaten aus einer Menge von Arbeitszyklen – von einigen wenigen bis hin zu einigen tausend – kann mittels statistischer Anpassungsverfahren eine Neuberechnung der Teach-Punkte durchgeführt werden.
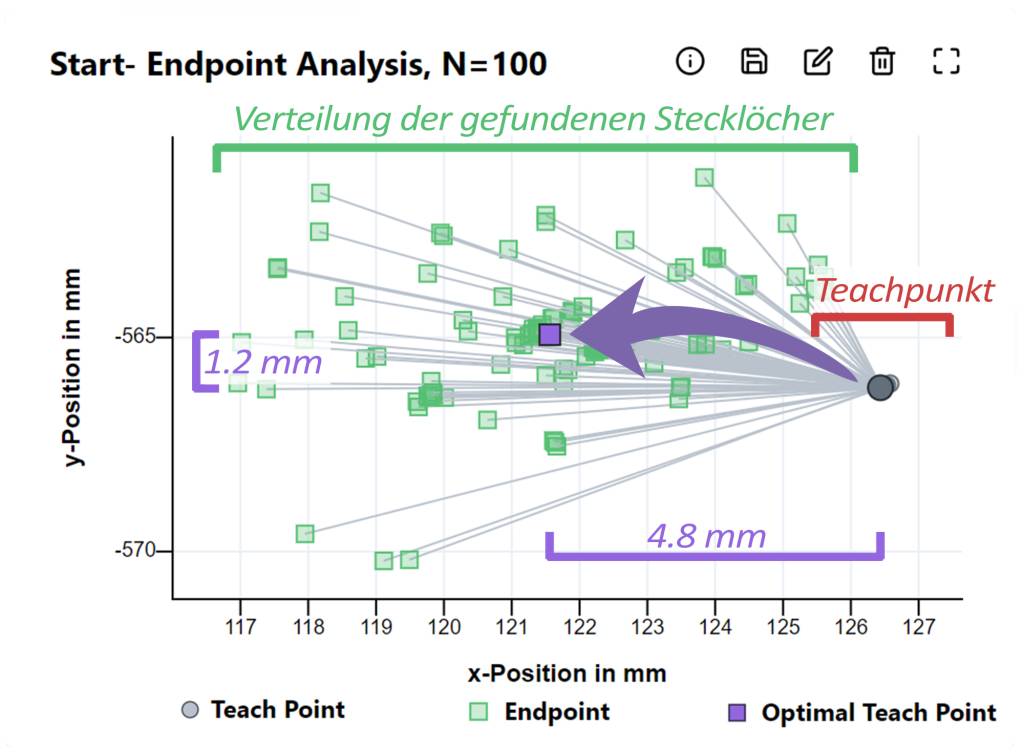
Objektive Datenanalyse und Prozessüberwachung
ArtiMinds Robotics hat mit dem Softwaretool Learning & Analytics for Robots (LAR) eine Lösung entwickelt, um relevante Punkte eines Roboterprogramms hinsichtlich Laufzeit und Robustheit gezielt anzupassen und Prozesse kontinuierlich zu überwachen. Hierfür wird eine Analyse der im laufenden Betrieb des Roboters anfallenden Prozessdaten auf einem zeitlich entkoppelten Edge-PC erstellt. Diese Daten können durch die Nutzung der Low-Code-Programmiersoftware ArtiMinds RPS ohne zusätzlichen Programmieraufwand automatisch erhoben und annotiert werden. Somit lässt sich z.B. der bestmögliche Startpunkt einer sensorbasierten Suche für einen Fügeprozess sehr effizient und transparent ermitteln. Die Ergebnisse sind dann offline in das anzupassende RPS-Programm übertragbar.
Um die Anpassung vollautomatisch ohne händische Benutzereingaben in den laufenden Roboterbetrieb, das heißt ohne Produktionsstopp, einfließen zu lassen, bietet ArtiMinds seit Neuestem den Weg über eine SPS an. Diese vermittelt als Gatekeeper zwischen dem LAR-Datenbank-Backend und dem Robotercontroller, da beide unterschiedliche Anforderungen bezüglich ihrer Kommunikationsprotokolle aufweisen. Weiterhin übernimmt die SPS die Rolle einer zusätzlichen Sicherheitsinstanz, die sicherstellt, dass automatische Anpassungen nur in einem sicheren Maße stattfinden können, und die den unterbrechungsfreien Roboterbetrieb auch gewährleistet, falls die Verfügbarkeit der Datenbank nicht gegeben sein sollte. Die SPS speichert Optimierungsergebnisse zwischen und überprüft sie mit unabhängig hinterlegten Absicherungsregeln auf unerlaubte Grenzwertüberschreitungen. Das Bewegungsprogramm fragt wiederum aktiv von der SPS angepasste Teach-Punkte an. Auf diese Weise können zeitliche Synchronisationsanomalien ebenso ausgeschlossen werden, wie unerlaubte Ausreißer, die bei komplizierteren Optimierungsverfahren in ungetesteten Sonderfällen entstehen können. Zu guter Letzt erlaubt ein HMI an der SPS nach erfolgreicher Benutzerauthentifizierung das manuelle Eingreifen in die Optimierungsparameter oder das (De-)Aktivieren der Anpassung.
„Das Roboterprogramm kann bei der SPS regelmäßig die neuen, optimierten Posen abfragen und übernehmen. Dadurch dass das Roboterprogramm die Posen abfragt, ist über das Netzwerk gewährleistet, dass der Vorgang zeitlich korrekt synchronisiert abläuft.“ So Dr. Sven Schmidt-Rohr, CEO von Artiminds Robotics. „Unser Ansatz ist das Zusammenspiel von prozesskritischem Roboter-Controller, dem Roboter-Controller, unserer Software ArtiMinds LAR und der zeitlich sicher eingekoppelten SPS.“
Sich selbst verbesserndes System
Mittels des beschriebenen Ansatzes aus Roboter, SPS und datengetriebener Anpassung sind nicht nur einzelne, generelle Verbesserungen durchführbar. Das System ist in der Lage, Optimierungen pro spezifischem Bauteil- oder Werkstückträger zu erlernen und diese zur Laufzeit und zur vorliegenden Situation passend zu nutzen. Ein sicheres, sich selbst optimierendes System aus etablierten Industriekomponenten ist damit aus einer Hand realisierbar.