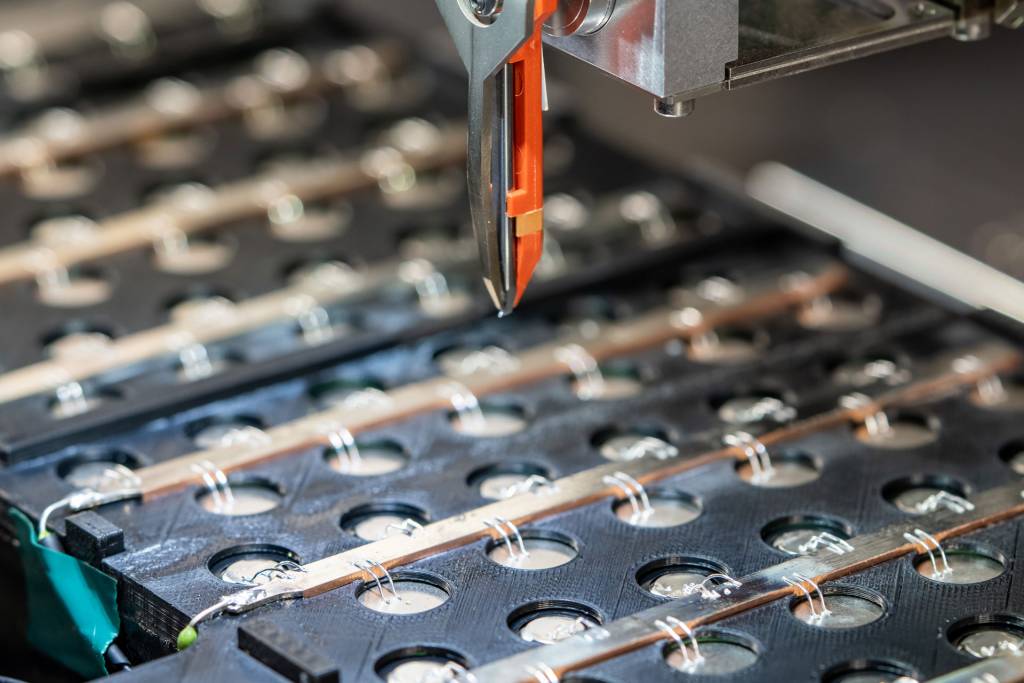
In der Chipfertigung ist das Draht-Bonden ein Verfahrensschritt, bei dem mittels dünner Drähte (Bond-Draht) die Anschlussflächen eines integrierten Schaltkreises oder eines diskreten Bauelements (z.B. Transistor, Leuchtdiode oder Batteriezelle) mit den elektrischen Anschlüssen anderer Bauteile oder des Gehäuses verbunden werden. Technisch wird dazu der Draht vom einen Anschluss zum anderen gezogen und an beiden Stellen verschweißt.
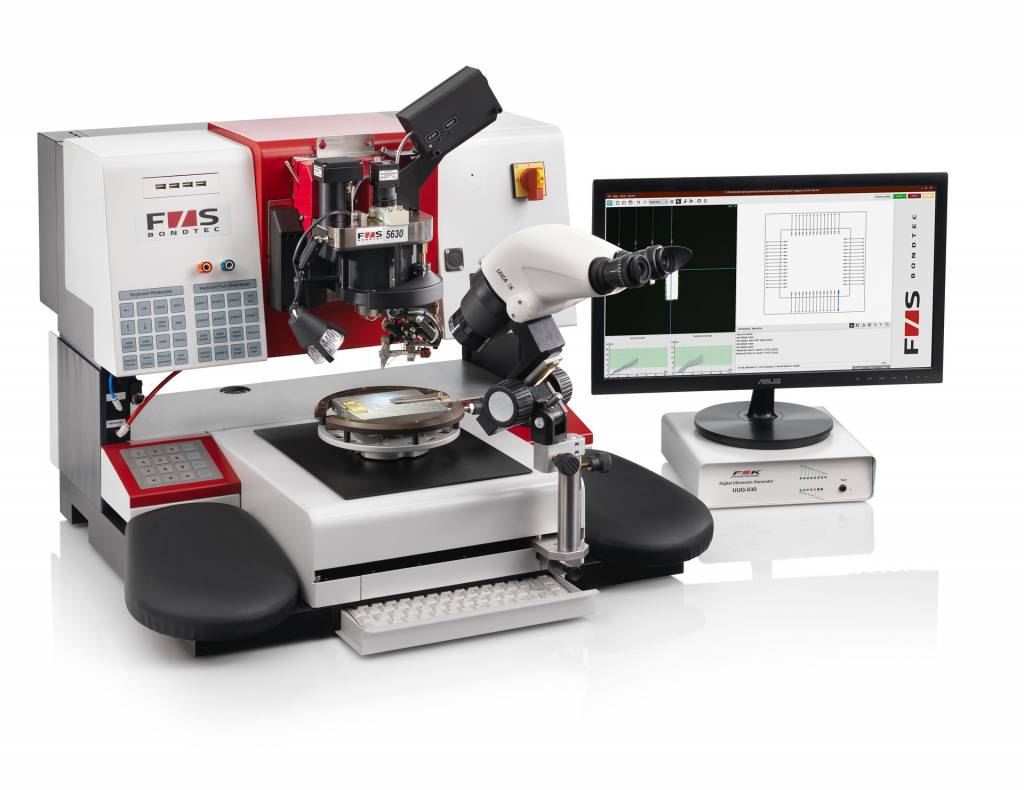
Dünner als das menschliche Haar
Der Bond-Draht selbst besteht meist aus Gold bzw. Goldlegierungen, aus Kostengründen aber auch aus Aluminiumlegierungen oder Kupfer. Übliche Durchmesser liegen zwischen 12,5 und 50µm bei Gold, bei 18µm bei Aluminium und 20µm bei Kupfer. Zum Vergleich: Ein normales Haar hat einen Durchmesser um 70µm. Dünnere Drähte erlauben engere Geometrien der Anschlussflächen (Pads) und daher höhere Packungsdichten. Bei Leistungshalbleitern mit hohen Stromlasten werden Dickdrähte mit Durchmessern zwischen 100µm und 500µm oder Dickdraht-Bändchen verwendet. Reicht deren Querschnitt für den zu erwartenden Strom nicht aus, wird pro elektrischer Verbindung mehrfach gebondet. Je nach Anwendung, Material des Drahtes, der Größe und Beschaffenheit der Kontaktflächen sowie der benötigten Drahtstärken werden unterschiedliche Bonding-Verfahren eingesetzt.
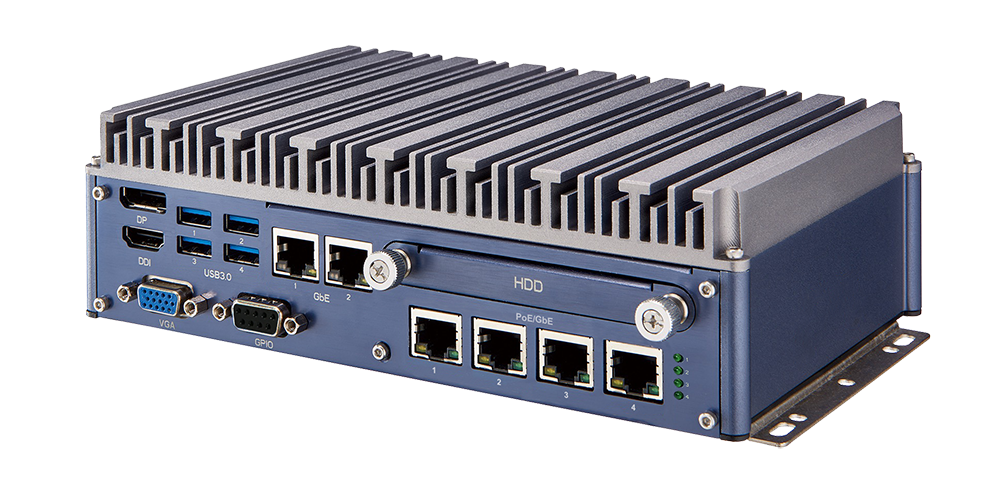
Komplexer Prozess – kompakte Maschine
Die Wahl des für die jeweilige Anwendung geeigneten Bonding-Verfahrens, der Prozess selbst, sowie die Auswahl der richtigen Parameter ist eine Wissenschaft für sich. Der Hauptmarkt für F&S-Bonder sind High-Mix/Low-Volume-Anwendungen in Forschung und Entwicklung oder kleine Serien hochpreisiger Produkte. Die spezielle Anforderung dabei: Eine Maschine soll möglichst alle Bonding-Verfahren beherrschen – und das bei Rüstzeiten von unter fünf Minuten. Heute bietet der Hersteller fünf solcher Plattformen an, die für unterschiedliche Einsatzszenarien ausgelegt sind. Allen gemeinsam ist: Einmal programmierte Abläufe laufen mit hoher Präzision vollautomatisch und reproduzierbar ab. Der kompakten Baureihe 56 von F&S, die alle Prozesse auf einer Plattform abbilden konnte und die den Grundstein des Firmenerfolgs bildet, sieht man nicht an, dass im Inneren zwei Steuerungen arbeiten: Die mikrometergenauen Bahnkurven werden von einer schnellen Echtzeitsteuerung berechnet, welche die Antriebsumrichter direkt ansteuert. Weniger zeitkritische Prozesse, etwa Bilderkennung und -verarbeitung, User-Interface, Datenbanken oder Analyse- und Programmiersoftware laufen hingegen auf dem IPC. „Die Software für beide Steuerungen entwickeln wir von Anfang an selbst,“ unterstreicht Johann Enthammer, Entwicklungsleiter bei F&S Bondtec.
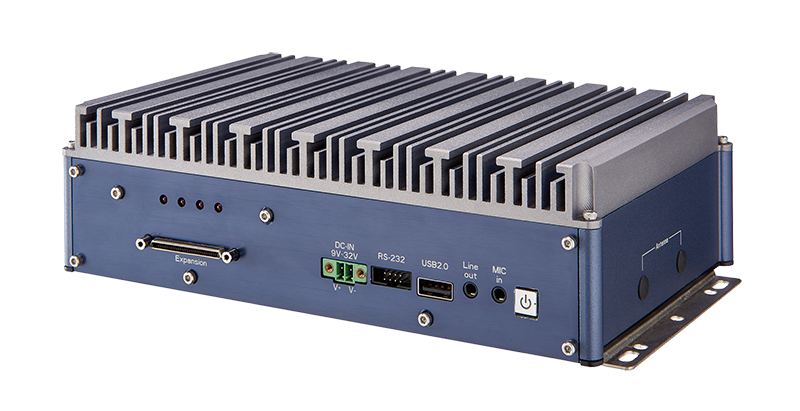
Eigenentwicklung oder Zukauf?
In der Vergangenheit hatte das Unternehmen als IPC eine selbst entwickelte Lösung auf Basis eines ETX-Moduls im Einsatz. Das Motherboard allerdings, sowie das Board für die Anbindung der Peripherie mit seinen zahlreichen Schnittstellen, waren Eigenentwicklungen. Ebenso das Rechnergehäuse. Einerseits war diese Lösung passend auf die Maschinen abgestimmt. Andererseits forderten neue und schnellere Schnittstellen, aber auch die Abkündigung von Bauelementen immer mehr Aufmerksamkeit, so dass schließlich der permanent steigende Aufwand in keinem Verhältnis mehr zu den Vorteilen der eigenen Plattform stand. Im Zuge einer Überarbeitung der Baureihe 56 wurden daher nicht nur Mechanik, Elektronik und Echtzeit-Steuerung erneuert. Es sollte auch ein kompakter IPC mit Windows 10 zum Einsatz kommen. Dabei suchte F&S nach einem Partner, der nicht nur ein Komplettsystem mit Langzeitverfügbarkeit liefern sollte, sondern sich auch der Lizenzierung annimmt und dessen Gehäuse im Idealfall ohne große konstruktive Veränderungen eingesetzt werden kann. „Ein weiterer großer Wunsch war, dass der IPC ohne drehende Teile auskommt, vor allem ohne Lüfter“, erklärt Enthammer. „Deren Vibrationen mussten wir bisher sowohl mechanisch als auch elektronisch kompensieren.“