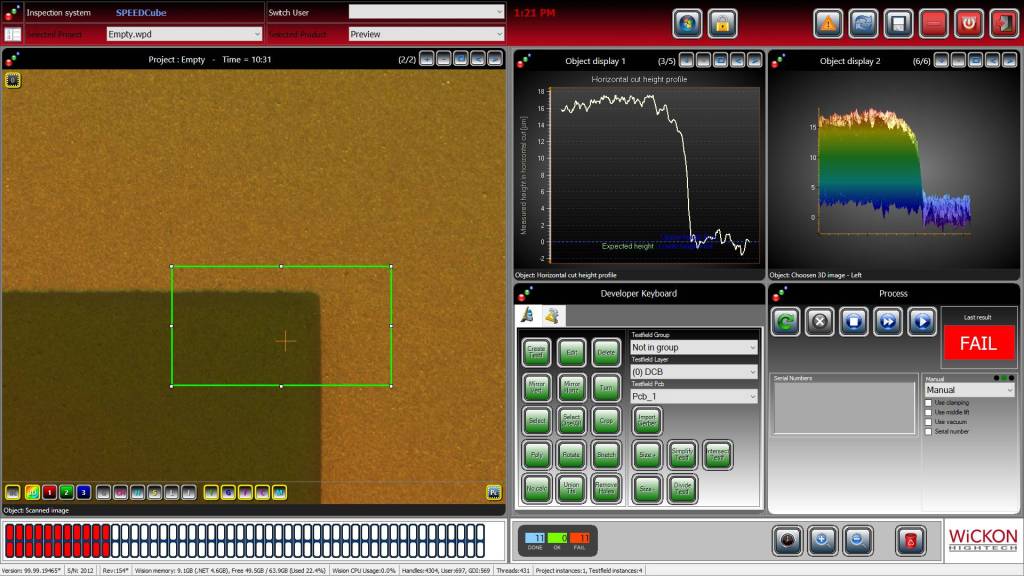
Manufacturing fuel cells requires high-temperature MEAs (Membrane Electrode Assembly) and bipolar plates, which are assembled into a stack. For this purpose, layers are applied to ceramic or metal using screen or stencil printing. The printed pastes are necessary for the electrochemical processes or seal the individual layers together by means of a glass seal. Powerful fuel cells consist of hundreds of MEAs. To meet the requirements of fuel cell manufacturers, fast and reproducible manufacturing processes are necessary – including wet inspection of the freshly printed membranes and IC plates. This is the only way to avoid serial defects and high scrap rates. Wickon Hightech has developed a fully integrated and functional solution for 3D inspection. The German-Czech provider is able to inspect all common fuel cell paste prints (screen or stencil printing) 3D – in the wet, dried or sintered state. To do so, the optical system uses illumination with a numerical aperture that allows wet and wavy surfaces to be detected in 3D. At the same time, both a 3D and a 2D image can be generated in one scan. The high-resolution colour camera unit produces images of 130x110mm in size in 0.6s. Layer thicknesses between 5 and30 µm can be achieved. The fast automation lines in the series production of fuel cell stacks currently achieve cycle rates of up to 15 substrates per minute. Roman Wieser, managing director of Wickon Hightech: „Automation manufacturers are aiming to produce at cycle rates of 60 substrates per minute in the near future. Our 3D system will be able to inspect that as well.“ Interlinked production lines are employed to manufacture MEAs and bipolar plates, which ultimately create a fuel cell consisting of several hundred individual components in one system. Wickon Hightech’s 3D inspection system can be fully integrated into this manufacturing process. Dimensioning, assembly and installation of the optical elements is handled by Wickon Hightech, including the analysis and automation software as well as the connection to the customer’s network. With a dual track machine and two inspection heads, two tracks run autonomously from each other with an inspection time of two seconds per track. Wickon Hightech is already cooperating with renowned automation companies that deploy their AOI systems.
www.wickon.com