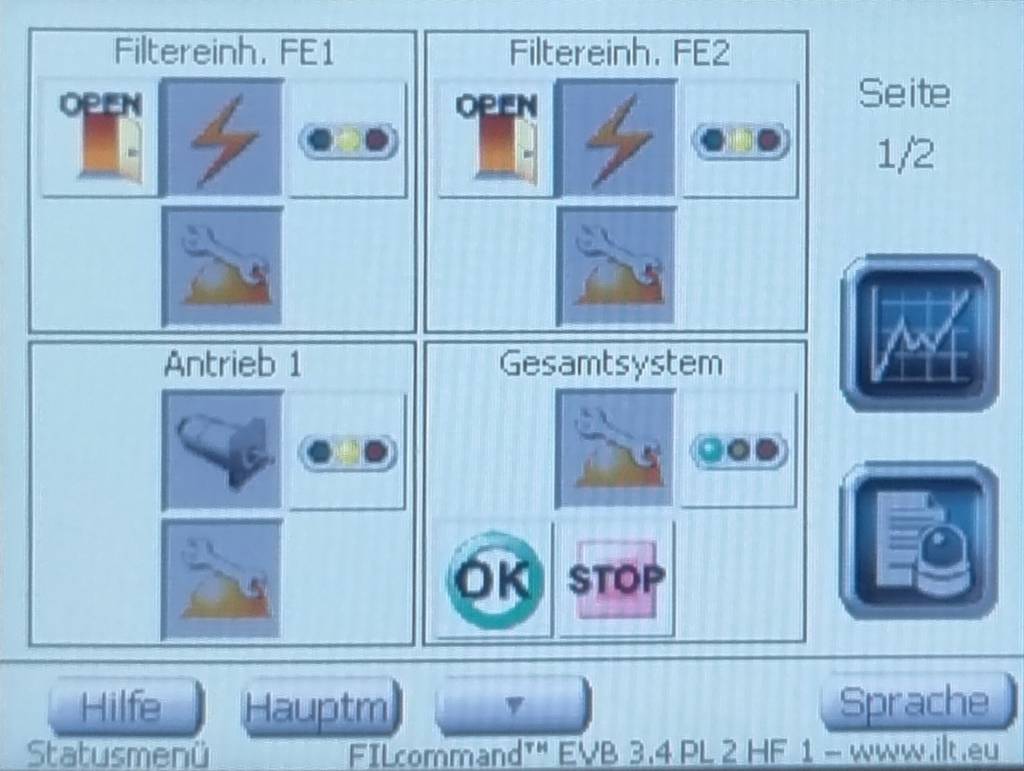
Das 1918 gegründete Unternehmen Heismann Drehtechnik fertigt Klein-, Mittel- und Großserien für die Automobil-, Elektronik-, Schloss-, Beschlag- und Armaturenindustrie sowie den Maschinenbau. Auf diversen konventionellen Fräs-, Bohr- und Drehmaschinen sowie rund 30 CNC-gesteuerten Index-Mehrspindeldrehautomaten, CNC-Drehmaschinen vom Typ Index und Traub sowie CNC- und programmgesteuerten Fräsmaschinen (Hermle) produzieren die rund 130 Beschäftigten Losgrößen zwischen 50.000 und 16 Millionen Teile je Artikel. Doch bei allen Vorteilen der CNC-Fertigung belastet die hohe Schnittgeschwindigkeit Mensch, Maschine und Umwelt: Kühl- und Schmiermittel verdampfen beim Bearbeiten und feine Partikel der benutzten Öle und Emulsionen verunreinigen die Atemluft, die Dämpfe schlagen sich in der Produktionshalle an Anlagen, Wänden und Decken nieder, in die Luft entwichene Kühl- und Schmiermittel gehen dem Fertigungsprozess verloren. „Ein untragbarer Zustand gerade für uns als Zulieferer der Automobilindustrie, in der höchste Produktqualität und Fertigungstoleranzen sowie Null-Fehler gefordert sind“, sagt Betriebsleiter Hubert Radziej. Daher entschieden sich die Verantwortlichen für die Installation von mehreren Luftfiltergeräten der ILT Industrie-Luftfiltertechnik aus Ruppichteroth: Die Fertigungslinien (mit insgesamt rund 30 CNC-Mehrspindel-Drehautomaten) wurden jeweils mit einer elektrostatischen Zentral-Absauganlage der ILT-Baureihe Elofil und die konventionellen CNC-Drehmaschinen in der zweiten Produktionshalle mit mechanischen Unifil-Zentral-Absauganlagen ausgestattet.
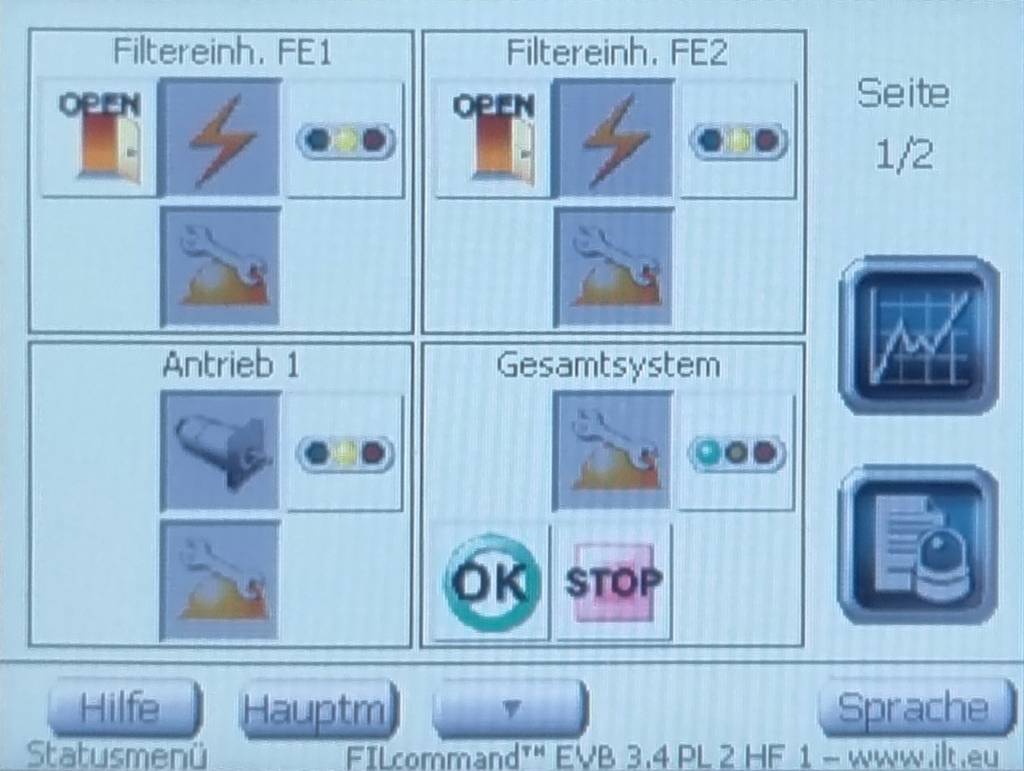
Reine Luft in beiden Hallen
So ließ sich in den beiden rund 6.000m² großen Produktionshallen die durchschnittliche Hallenbelastung von ca. 12 mg Aerosolpartikel pro m³ um rund 95 Prozent reduzieren. „Durch den Einsatz der ILT-Absauganlagen auf unseren CNC-Mehrspindel-Drehautomaten konnten wir eine Öleinsparung von etwa 400l pro Woche erreichen. Das Öl fließt über einen Sammeltank direkt in die Produktion zurück, die eingesparten Kosten für den Einkauf von Öl oder die Reinigungskosten für Halle und Betriebsmittel liegen bei über 200 Euro pro Woche“, so Hubert Radziej.
Informationen zur rechten Zeit
ILT stellt für seine Produkte auch Beratung, Service oder Wartung bereit. Darüber hinaus fließt die Expertise in der Prozesslufttechnik auch in die Weiterentwicklung der Steuerungs- und Diagnosetechnik ein. So wurden die Absauganlagen mit der digitalen Steuerungstechnik FILcommand ausgestattet. Die Bedienlogik orientiert sich dabei am 3R-Prinzip: die richtigen Informationen zur richtigen Zeit richtig integriert. Der Bediener wird darüber hinaus mit 3D-Grafiken, Touch-Display und Online-Hilfe durch die Arbeitsschritte geleitet und kann Parameter wie Filterzustand, Wartungspunkte oder Gesamtanlagenzustand abfragen. Meldungen werden in Protokollen gespeichert und Wartungen vorbeugend signalisiert. Die kontextsensitive Hilfe erklärt dem Benutzer in diesem Fall, was genau zu tun ist.
Prozesslufttechnik im Griff
In weiteren Ausbaustufen können mehrere Anlagen über Netzwerkverbindungen (auch mobil) überwacht werden. Das HMI ist baureihenübergreifend konzipiert, um in unterschiedlichen Luftfilteranlagen einsetzbar zu sein. Mit einem Steuerungssystem und einem Interface kontrolliert der Leitstand die gesamte Luftfiltertechnik. „FILcommand erfasst sämtliche Betriebsparameter zentral und unterstützt den Anwender bei der Planung der Produktion und der Maschinenzeiten – ebenso einfach wie exakt, denn ‚ungefähr‘ passt heute nicht mehr in die Produktionsumgebungen von Unternehmen“, so ILT-Geschäftsführer Falco Riemer. n Fachjournalist aus Villingen-Schwenningen.