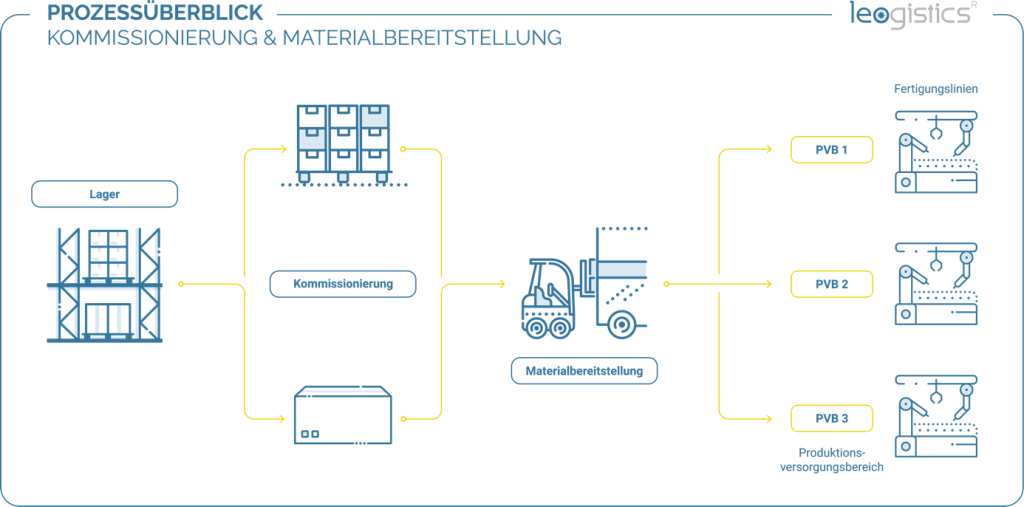
Einigen Unternehmen ist es nicht wichtig oder aufgrund verschiedener äußerer Einflüsse nicht möglich, die Produktionsversorgung effektiv zu planen. In diesem Fall bietet es sich an, die Verantwortung über die Versorgung der Produktion komplett in die Hand eines Mitarbeiters zu legen. Diese Person identifiziert im Ad-hoc-Verfahren mittels visueller Prüfung, ob physisch noch genügend Bestand im Produktionsversorgungsbereich (PVB) vor der Linie liegt.
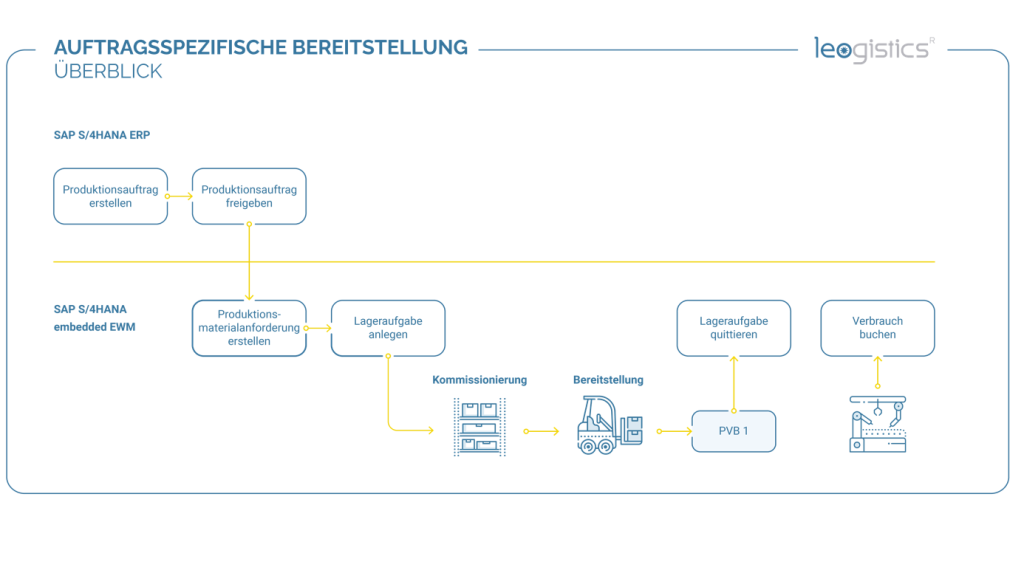
Ad-hoc-Versorgung
Ein Beispiel: Ein Regal im Produktionsversorgungsbereich beinhaltet drei Materialien. Dabei wird festgestellt, dass ein Schraubenfach leer ist. Mittels einer mobilen App kann per Scan das fehlende Material angefordert werden. Der Scan löst die Lageraufgabenerstellung mit Berücksichtigung der hinterlegten Auslagerstrategie (z.B. First-in-First-out, First-expired-First-out, Chargenmerkmale, etc.) aus und legt diese in den Arbeitsvorrat für die Kommissionierer im Lager. Bei diesem Ansatz muss das Personal in der Produktion sehr diszipliniert agieren. Ist nicht genügend Material im Versorgungsbereich, kann es zum Stillstand kommen.
Mit Minimalmengen arbeiten
Als Alternative kann die Produktionsversorgung mit Minimalmengen zum Tragen kommen. In den Stammdaten des SAP EWM (Extended Warehouse Management) wird zum Produkt und Produktionsversorgungsbereich eine Materialmenge hinterlegt, die mindestens vorgehalten werden muss bzw. bei welcher Menge eine Lageraufgabe zur Versorgung angelegt wird. Voraussetzung dafür ist, dass der Verbrauch der Komponenten entweder automatisiert per MES-Integration oder manuell über eine mobile Anwendung zeitnah zum Prozessauftrag gebucht wird. Ansonsten kommt das System schnell an seine Grenzen und die Produktion gerät ins Stocken.
Kanban-Prozesse
Wenn der Aufwand an Stammdatenpflege für die Minimalmengen in schlechter Relation zum Ergebnis steht und eine kurze Wartezeit für die Produktion kein Problem ist, kann ein Kanban-Prozess genutzt werden. Mit Leerwerden des Kanban-Behälters löst das System eine Anforderung für die Produktion aus. Im S/4Hana embedded EWM-Szenario erzeugt das System Lageraufgaben direkt. Ein weiterer Nachteil zu der oben genannten Wartezeit bei der Bereitstellung ist in dieser Prozessvariante ist, ebenso wie bei der Ad-hoc- oder der Minimalmengen-Produktionsversorgung auch, dass die Lageraktivitäten nicht effektiv geplant werden können.