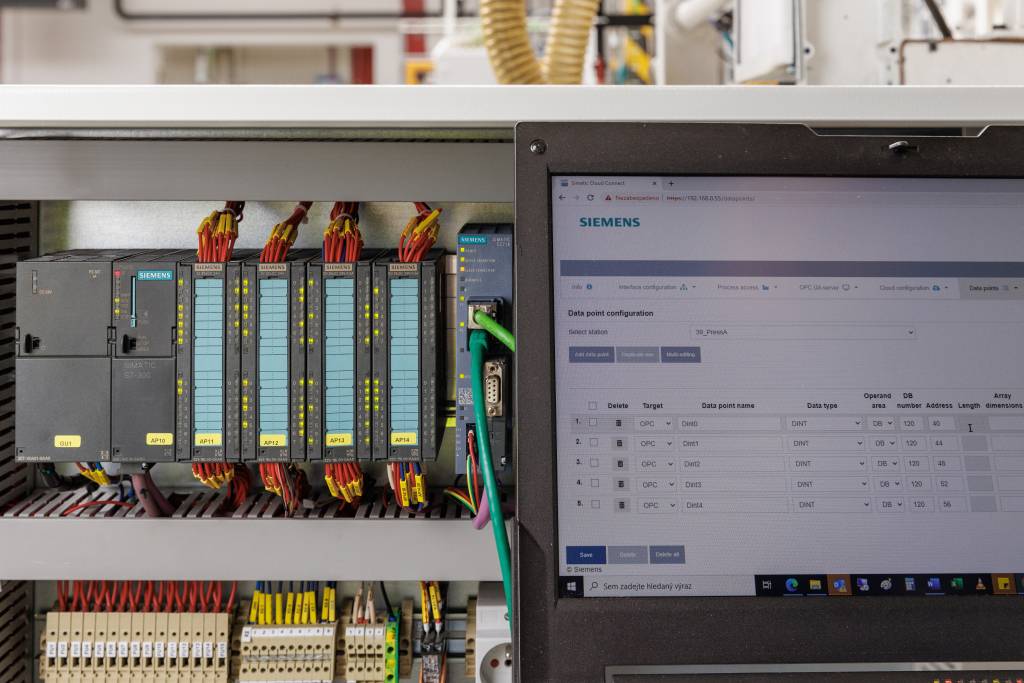
Für den Umstieg auf eine automatisierte Datenerfassung ist häufig eine umfassende Hochrüstung der Produktionslinien erforderlich. Dabei müssen Maschinen und Technologien kostspielig ausgetauscht werden. Falls nicht unbedingt erforderlich, müssen ältere Produktionsmaschinen, die noch reibungslos funktionieren, jedoch nicht vollständig ersetzt werden – es genügt die Ausstattung mit Komponenten, die für einen Bruchteil der Kosten Zusatzfunktionen bereitstellen. Dadurch kann der Modernisierungsprozess schrittweise, spontan und präzise den aktuellen Anforderungen entsprechend erfolgen. Mit dem Produktspektrum von Siemens kann sich dieser Prozess durch individuell ausgelegte Systeme erheblich vereinfachen lassen.

Ein Beispiel aus der Praxis
Zu den vielen Unternehmen auf dem Weg zur digitalen Transformation gehört auch Trivium Packaging Czech Republic s.r.o. In seiner Metallverarbeitungsanlage in Skivany in der tschechischen Region Hradec Králové hat Trivium die ersten Schritte zu einer unternehmensweiten Datenüberwachung unternommen. Ziel ist die Integration der bisher getrennt betriebenen Maschinen und Produktionslinien in ein zentrales System mit einem einzelnen Server zur Erfassung der Fertigungsdaten, um die Produktivität zu erhöhen. Die Digitalisierung sollte zunächst in der Schneidanlage, der Lackiererei und der Produktionslinie für Deckel umgesetzt werden. Diese Bereiche sind für den Betrieb des Werks von zentraler Bedeutung. Eine der größten Herausforderungen lag im unterschiedlichen Alter der Maschinen, Produktionslinien und eingesetzten Technologien. „Die Produktionslinien mussten mit dem Netzwerk verbunden werden – zwischen den einzelnen Maschinen war jedoch keine Kommunikationsinfrastruktur vorhanden. Gruppen von Produktionslinien wichen voneinander ab und enthielten Komponenten unterschiedlichen Alters“, erläutert David apek, technischer Berater bei Trivium Packaging. Einige Maschinen waren mit der Siemens-Steuerung Simatic S7-300 ausgestattet, die lediglich eine Profibus DP-Schnittstelle bietet. Andere Steuerungen wiesen nur eine MPI-Schnittstelle auf. Die zuletzt installierten Produktionslinien verfügten zwar über Ethernet, die Zuweisung eindeutiger IP-Adressen war jedoch noch nicht erfolgt. Daher konnten weder Kommunikationsprozessoren angebracht noch konnte eine Verbindung mit dem Netzwerk hergestellt werden, ohne die Adressen komplett neu zuzuweisen. Nach Prüfung der verfügbaren Optionen sah David apek in der von Siemens angebotenen Technologie das am besten geeignete System.

Digitale Metallverarbeitung
Als Lösungweg schlug der Anbieter vor, sämtliche Maschinen und Produktionslinien des Unternehmens mit den Gateways Simatic CloudConnect 7 (Simatic CC716) zu integrieren. So könnte sich künftig bei Bedarf über das OPC UA-Protokoll kommunizieren lassen. Darüber hinaus unterstützen die Gateways auch verhältnismäßig veraltete Steuerungen, die nur über eine Profibus DP- oder MPI-Schnittstelle verfügen. Das OPC UA-Protokoll (Open Platform Communications Unified Architecture) gilt als Standard bei der Digitalisierung der Produktionsautomatisierung. Es ist bei allen neuen Steuerungen vom Typ Simatic S7-1500 zu finden. Die Simatic S7-1500 PLC als OPC UA-Client liest zunächst die Daten der Gateways Simatic CC716 aus und leitet diese anschließend an das zentrale Unternehmenssystem TLM (Trivium Line Monitoring) weiter. Dort werden die Daten den Werken des Herstellers weltweit zur Verfügung gestellt. Außerdem können die bisher getrennten Maschinen und Produktionslinien zentral an jeder Stelle in der Produktionsanlage programmiert, überwacht und diagnostiziert werden. War die ursprüngliche Anfrage auf die Datenerfassung beschränkt, sind heute deutlich mehr als die benötigten Funktionen verfügbar. Erreicht wurde das über die Applikationsunterstützung von Siemens, in deren Rahmen die Geschäftsführung des Produktionsbetriebes bei der Entwicklung des Konzeptes beraten und der anschließenden Konfiguration der Komponenten unterstützt wurde. Bei der Installation und Inbetriebnahme arbeitete man mit den Automatisierungsspezialisten und Programmierern von Trivium Packaging Miroslav Frýba zusammen.

Blick unter die Motorhaube
Im Projekt mussten die Produktionsmaschinen physisch miteinander verbunden werden, um die Grundlage für das künftige Backbone-Netzwerk mit den 16-Port-Industrial Ethernet Switches Scalance XC216 zu schaffen. Maschinen mit doppelten Adressen wurden über NAT-Router Scalance S615 angebunden. Diese konvertieren anhand einer eindeutigen Adresse Daten vom internen in das externe Netzwerk. Darüber hinaus enthalten sie eine Firewall, um unberechtigten Zugriff zu verhindern und sicherzustellen, dass die Kommunikation nur zwischen vordefinierten IP-Adressen erfolgt. Um die Kommunikation ausschließlich über definierte Knoten zuzulassen, wurden Router konfiguriert. Zusätzlich konnte durch diesen Ansatz das neu aufgebaute Netzwerk spontan in Mikrosegmente unterteilt werden.