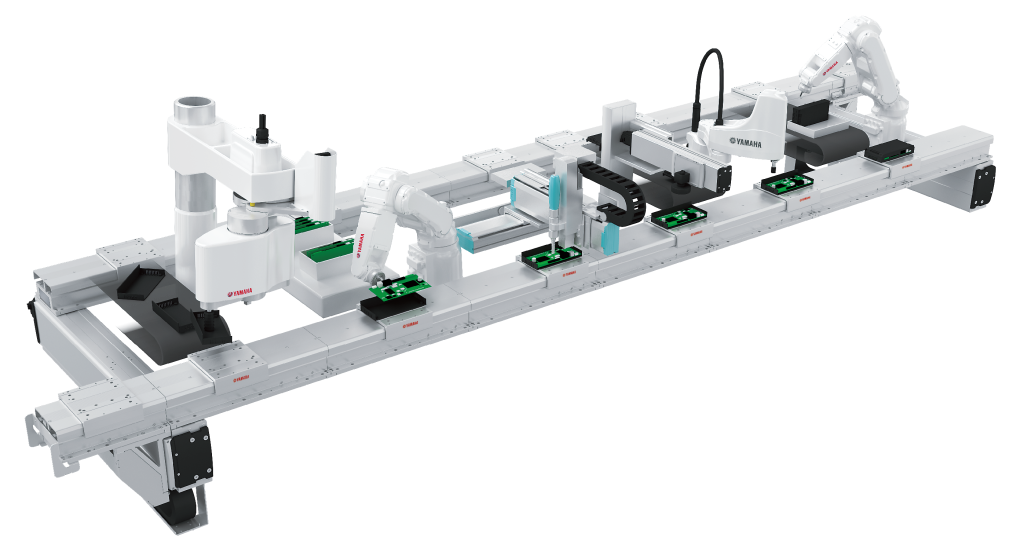
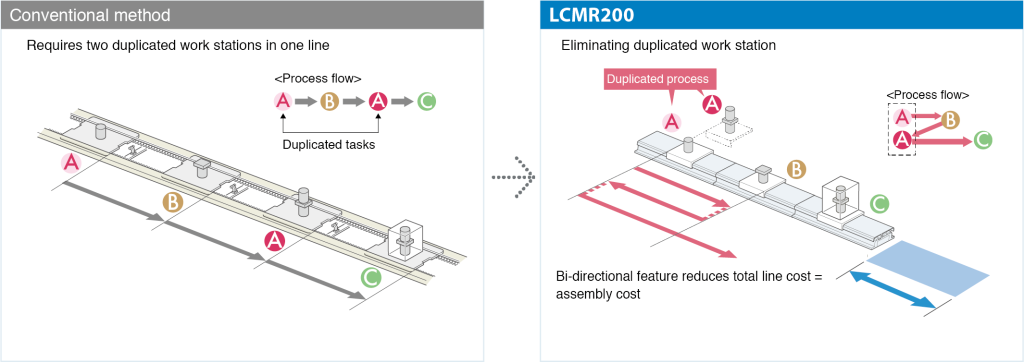
Herausforderung 1: Stückzahlerhöhung
Bei der Konstruktion und Einrichtung einer Montagesequenz, die mit Rundschalttischen durchgeführt werden soll, müssen Prozessingenieure kritische Rundschalttischparameter wie Auflösung, Wiederholbarkeit, Genauigkeit, zulässiges Spiel sowie Hysterese berücksichtigen. Wenn der Durchsatz erhöht werden muss, kann unter Umständen einfach die Rotationsgeschwindigkeit erhöht werden, während der Tisch sich zwischen Indexpositionen bewegt. Wenn eine zusätzliche Maschine in die Montagesequenz einzufügen ist, die entweder am Umfang des Tisches oder in der Mitte installiert wird, kann das eine komplexe Aufgabe sein. Vorhandene Vorrichtungen müssen in der Regel an eine neue Position verschoben werden, um die zusätzliche Maschine unterzubringen. Die Skalierbarkeit ist jedoch durch den Umfang des Rundschalttisches begrenzt. Das Hinzufügen einer zusätzlichen Maschine kann möglicherweise sogar physisch unmöglich sein. Wenn die Grenzen der Geschwindigkeit und der Größe des Rundschalttisches erreicht sind, kann die einzige Alternative darin bestehen, einen weiteren Rundschalttisch hinzuzufügen. Das würde erheblichen zusätzlichen Platz erfordern, der eventuell gar nicht zur Verfügung steht.
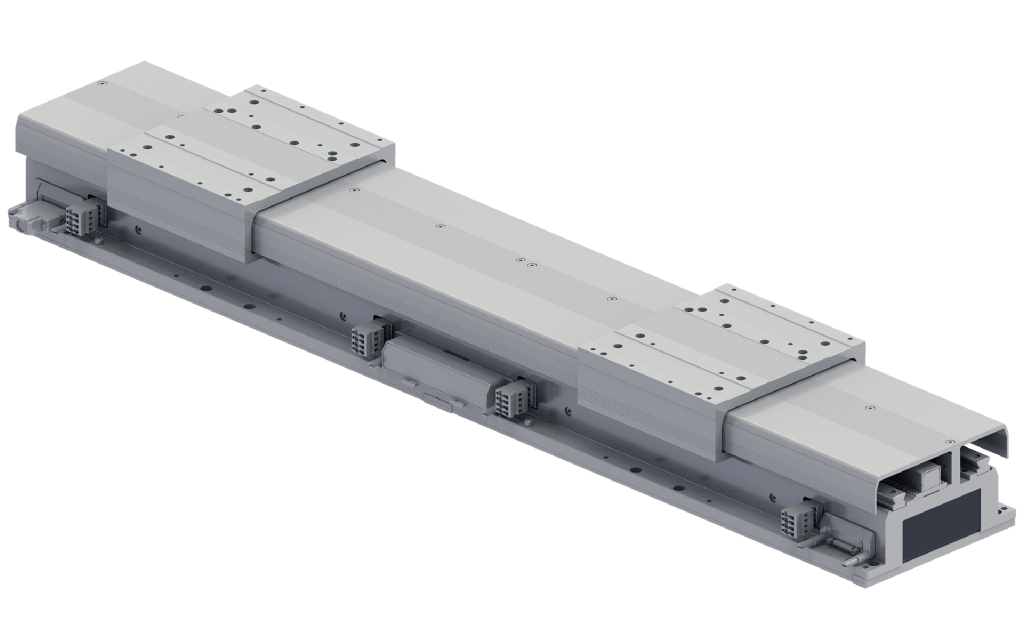
Herausforderung 2: Verkürzung der Linientaktzeit
Wenn es darum geht, Werkstücke entlang einer Produktionslinie von Prozess zu Prozess zu transportieren, sind herkömmliche Band- und Rollenförderer oft das Transportmittel der Wahl. Sie eignen sich gleichermaßen für den Transport von Werkstücken zwischen sowohl automatisierten Maschinen als auch Handmontageplätzen. Typischerweise ist die Fördergeschwindigkeit nicht veränderlich und die Transportrichtung unidirektional. Um die Zykluszeit zu verkürzen und damit den Durchsatz der Produktionslinie zu erhöhen, kann die Erhöhung der Fördergeschwindigkeit eine naheliegende Maßnahme sein. Das ist jedoch nicht immer erfolgreich und kann in manchen Situationen sogar kontraproduktiv sein. Das Problem tritt auf, wenn die sich bewegenden Werkstücke angehalten werden, was typischerweise durch einen Mechanismus, wie einem Mikroschalter oder einem Endanschlag, realisiert wird, der das Förderband zu einem abrupten Stopp bringt. Einige Unternehmen haben festgestellt, dass hierdurch Werkstücke verschoben und Werkstückträger oder Paletten beschädigt wurden. Ein Anhalten der Linie zur Behebung dieser Probleme verringert deren Produktivität.
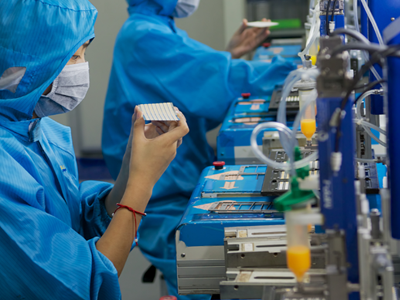
Herausforderung 3: Prozess-Sharing
Bei der Analyse des Konzepts, wie die Montage eines neuen Produkts automatisiert werden kann, wird häufig festgestellt, dass einige Prozesse – wie z.B. das Einschrauben von Schrauben, das Auftragen von Klebstoff oder das Anbringen einer mehrteiligen Blende – möglicherweise mehr als einmal an demselben Werkstück ausgeführt werden. Um die Arbeitsabläufe in einer herkömmlichen, unidirektionalen Reihenfolge zu erledigen, müsste der gleiche Maschinentyp an mehreren Stellen entlang der Montagelinie installiert werden. Sowohl Platz als auch Investitionsmittel könnten eingespart werden, wenn ein Werkstück z.B. zu einer Schraubmaschine zurückgeführt werden könnte, um unmittelbar nach einem Prozess, der eine äußere Abdeckung oder ein Gehäuse positioniert, einen zweiten Satz Schrauben zu montieren. Das Zurückbewegen von Werkstücken entlang der Produktionslinie ist jedoch mit herkömmlichen Transportsystemen nicht einfach zu bewerkstelligen.