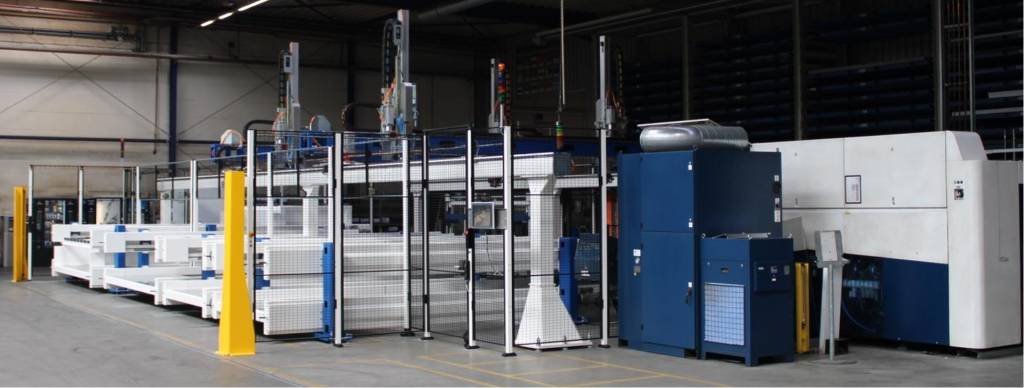
Das Schweizer Unternehmen Isochronic wurde im Jahr 2020 gegründet und ist mittlerweile auf 15 Mitarbeiter angewachsen. Die Geschäftsidee lautete von Anfang an, simultane, sogegannte isochrone Pick&Place-Robotersysteme zu entwickeln, die den Teiletransfer im Vergleich zu den seit Langem etablierten kartesischen Flächenportalen signifikant beschleunigen. Flächenportale haben z.B. gegenüber Knickarmrobotern den großen Vorteil, dass ihre Reichweite ungleich höher ist. Aber herkömmliche Systeme bewegen sich stets in einem starren, rechtwinkligen Koordinatensystem und bieten daher wenig Flexibilität und geringen Durchsatz. Das ist bei dem von Isochronic neu entwickelten System anders.
Die mehrfach patentierte, doppelt rotative Kinematik erlaubt die simultane Bewegung aller vier zur Verfügung stehenden Pick-Köpfe, während herkömmliche kartesische Systeme lediglich sequenziell arbeiten und damit deutlich langsamer agieren. Tatsächlich arbeitet das von Isochronic entwickelte System, laut COO Armin Haller, deutlich effizienter als alternative Lösungen und erreicht einen massiv höheren Durchsatz bei 30% weniger Energieverbrauch. Die beiden Basisträger (X-Achsen) stehen fest, wie bei den konventionellen Systemen auch, wohingegen die Querträger (Y-Achsen) mit einem zusätzlichen Freiheitsgrad auch in Winkeln zwischen ±20° bewegt werden können. Dadurch können die leichten Pick-Kopf-Schlitten (Z-Achse inklusive Rotation/Theta-Achse und Greifer) die Hauptbewegung übernehmen, wodurch weniger Masse bewegt wird, das System dynamischer ist und zusätzlich eine deutliche Energieeinsparung erreicht wird.
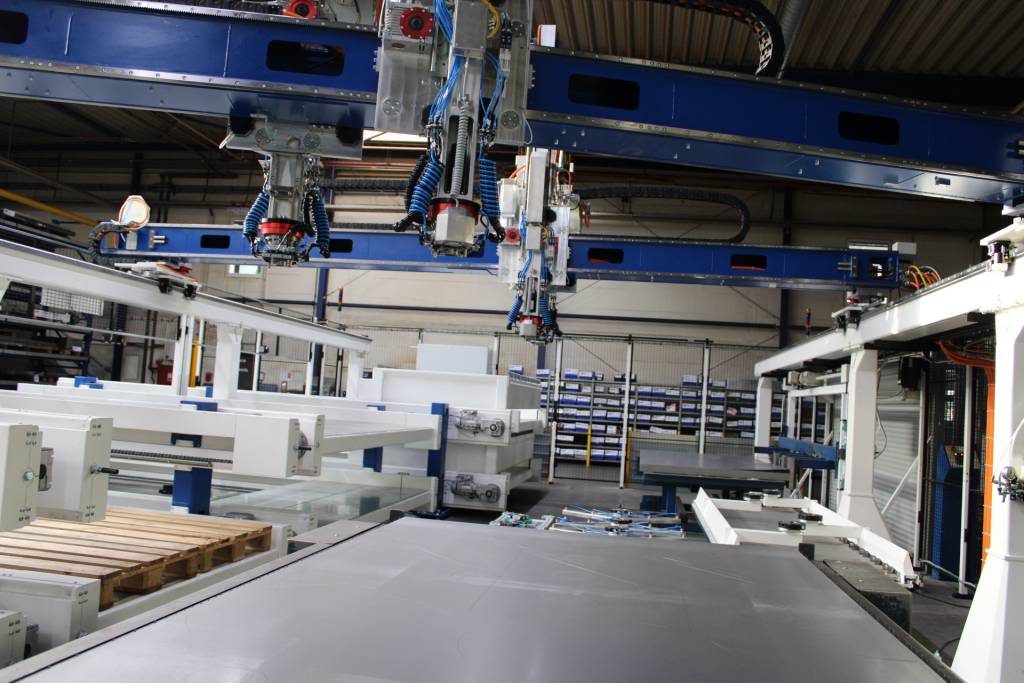
Pick&Place in der Blechbearbeitung
Zum Einsatz kommt das System erstmals bei einem Metallverarbeiter in Deutschland und automatisiert dort das Beladen von Rohblechen in der Größe bis 3×1,5m, das Absortieren der gefertigten Teile, das Stapeln auf Paletten und das Entsorgen des Restgitters. Somit automatisiert Isochronic mit dem System den vor- und nachgelagerten Arbeitsprozess einer Laserschneidanlage von Trumpf. Das Team von Isochronic hat das iSort-3015-System von der Idee bis zum ersten industriellen Einsatz in 24 Monaten entwickelt und realisiert. Der größte Anteil der Entwicklung liegt, fast unsichtbar, in der komplexen Software, die letztendlich über ein intuitiv zu verstehendes Panel (HMI) vom Anwender einfach bedient werden kann. Vor der Auslieferung an den Kunden in Deutschland wurde das System im Isochronic-Werk in der Nähe von Lausanne in der Schweiz auf Herz und Nieren geprüft. Die mechanische Installation beim Kunden konnte in nur zwei Wochen realisiert werden und verlief parallel zur laufenden Produktion.
Die ursprüngliche Idee für den Einsatz dieses Systems waren klassische Pick&Place-Aufgaben im Kleinteilbereich, aber nicht unbedingt in der Blechbearbeitung. Die Zusammenarbeit mit Kuipers Technologies hat ihren Ursprung in einem Messebesuch, bei dem ein junger Ingenieur von Kuipers auf die Lösung von Isochronic für den Kleinteilbereich aufmerksam wurde, wie Haller erzählt. Die Frage an Isochronic war: Könnt ihr das auch etwas größer und für die Blechverarbeitungsindustrie bauen?
Das Marktpotenzial ist sehr groß, wie Haller erläutert. Heute werden jährlich Tausende von Laserschneidanlagen verkauft, wobei weniger als 1% mit einer komplett automatisierten Sortierlösung ausgestattet sind. Die leistungsstarken, schnellen Laserschneidanlagen werden vom manuellen Material-Handling-Prozess ausgebremst, ein klassisches Bottleneck entsteht und die Laserschneidanlagen werden unwirtschaftlich betrieben. Dieses Bottleneck hat Isochronic nun mit dem iSort gelöst.
„Das operative Knowhow der Mitarbeitenden von Kuipers und die daraus resultierenden präzisen Anforderungen an das System hat uns sehr dabei geholfen, das Lastenheft für diese Anwendung zu schreiben.“ erläutert Haller. Der iSort ist modular aufgebaut. Ein weiterer Pluspunkt ist die Flexibilität des Systems, das eine einfache Integration in die Produktion bei Kunden ermöglicht. Diese Flexibilität ist ein wichtiger Faktor bei den sogenannten Brownfield-Projekten, bei denen bestehende Laserschneidanlagen automatisiert werden.
In der Pilotanlage werden Bleche im Format 3×1,5m und bis zu einer Stärke von 12mm verarbeitet. Es stehen aber auch iSort-Systeme zur Verfügung für das Handling von Blechen bis 8m Länge und 2,5m Breite oder bis 25mm Materialstärke bei maximal 2,4t Gewicht. Die Modularität des iSort ermöglicht es Anwendern, eine schrittweise Automatisierung ihrer Produktion umzusetzen. Beginnend mit dem Einstiegsmodell mit Rohblechbeladung auf Paletten mithilfe von Gabelstaplern, dem Absortieren auf Paletten, die auf dem Boden stehen, und zwei Sortierköpfen. Eine Erweiterung in Schritten ist möglich. So kann später einfach auf vier Sortierköpfe erweitert werden oder die Integration von Materiallager, Schubladensystem oder FTS zum Abtransport der beladenen Paletten, was einen völlig unterbruchfreien Betrieb ermöglicht, realisiert werden. Greifermagazine mit unterschiedlichen Greifern und dem klassischen Rechen für das Restgitter erweitern die Flexibilität des Systems. Auf Wunsch können z.B. auch Entgratstationen direkt eingebunden werden.
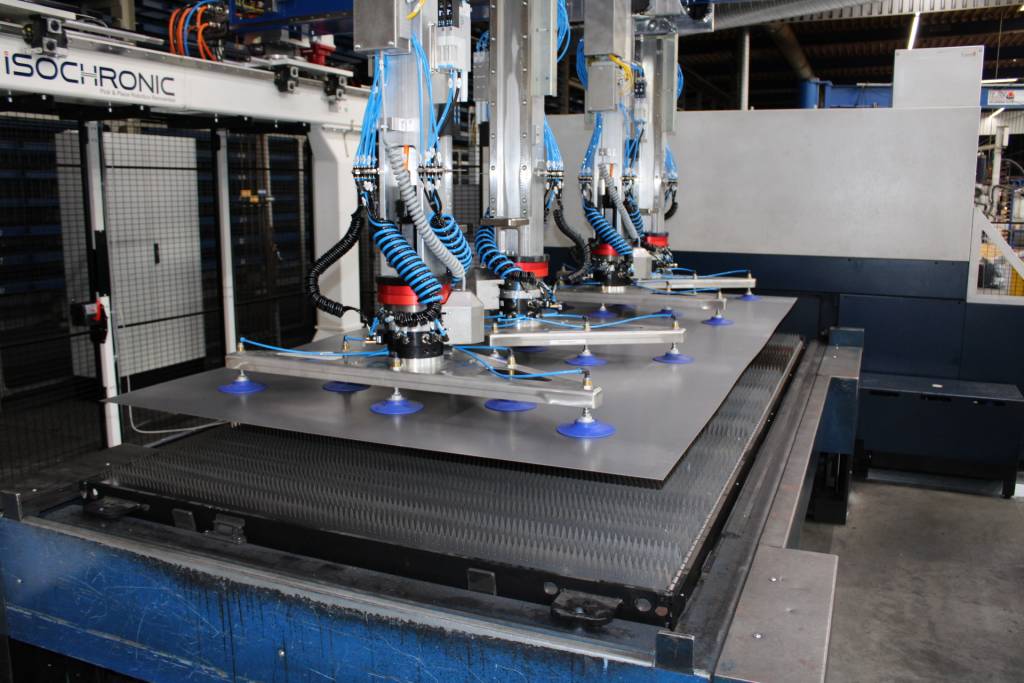
Greiftechnik mit Sensorik
Das zum Einsatz kommende, modulare Greiferkonzept ermöglicht die Anbindung an verschiedene Sensoren, die u.a. erkennen können, ob sich das zugeschnittene Blech tatsächlich vollständig aus dem Restgitter auslöst. Im Prinzip erkennt dabei der Laser, ob ein Stromschluss zwischen dem zugeschnittenen Teil und dem Restgitter besteht, sodass der Roboter das Teil wieder ablegt und versucht, es nochmals zu greifen. Ein weiterer Sensor erkennt, ob der Roboter das Teil sicher gegriffen hat, sodass der Roboter den Greifvorgang bei Bedarf erneut starten könnte. Durch das sehr präzise senkrechte Abheben durch den Roboter kommt es aber in der Regel nicht zu Verkantungen des zugeschnittenen Blechs, wie es z.B. häufiger der Fall ist, wenn die Bleche manuell aus dem Restgitter entfernt werden.
Jeder Pick-Kopf ist mit pneumatisch geschalteten Magneten unterschiedlicher Größe oder mit Vakuum Cups ausgestattet, die sich einzeln, in Gruppen oder auch alle zusammen aktivieren lassen. Für besonders große und schwere Teile lassen sich auch zwei, drei oder vier Pick-Köpfe simultan verwenden, um die Traglast zu erhöhen, wobei in vielen Fällen aufgrund der vielen Freiheitsgrade des Systems auch große Teile gedreht werden können. Jeder Pick-Kopf hat eine Traglast von 150kg und verfügt über eine integrierte Rotationsachse, die Drehbewegungen bis 180° erlaubt.
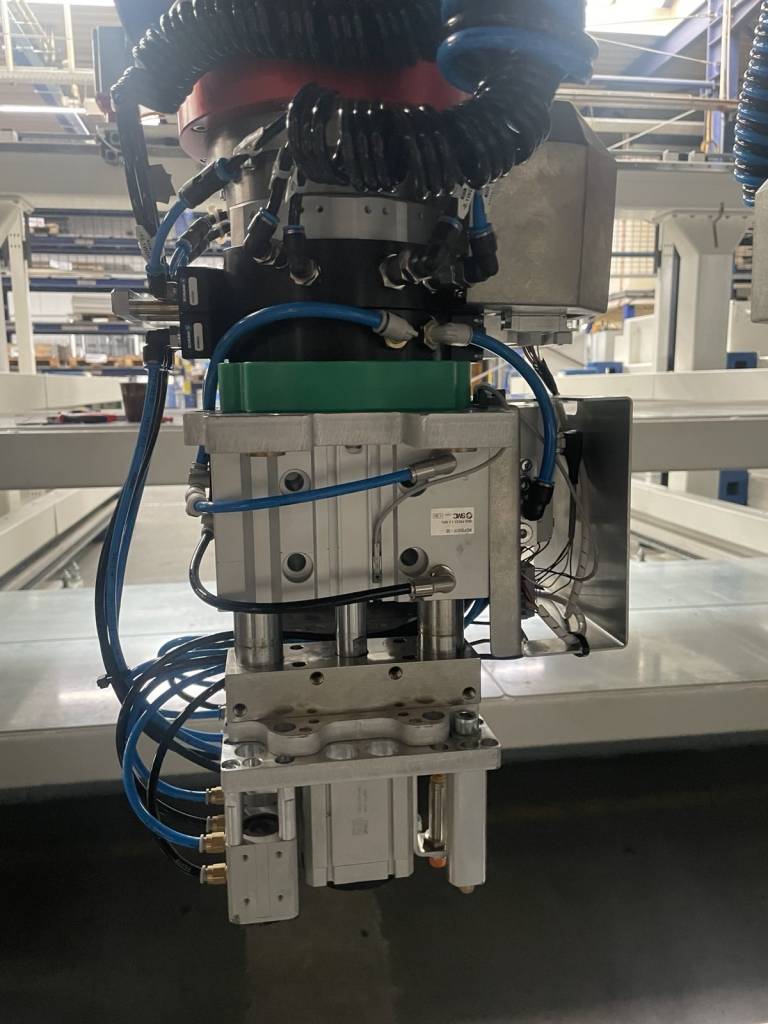
Vom Schneidtisch auf die Palette
Die flexibel zu bestückenden Paletten stehen auf einem (optional erhältlichen) Schubladensystem mit einer unteren und einer oberen Ebene bereit, sodass immer vier Paletten gleichzeitig vom Roboter beladen werden können. Genauso ist es aber möglich, auf das Schubladensystem für die Paletten zu verzichten und die Paletten einfach auf dem Boden abzustellen. Darüber hinaus plant Isochronic die Anbindung an fahrerlose Transportsysteme zu ermöglichen, um den innerbetrieblichen Materialfluss noch weitergehend zu automatisieren.