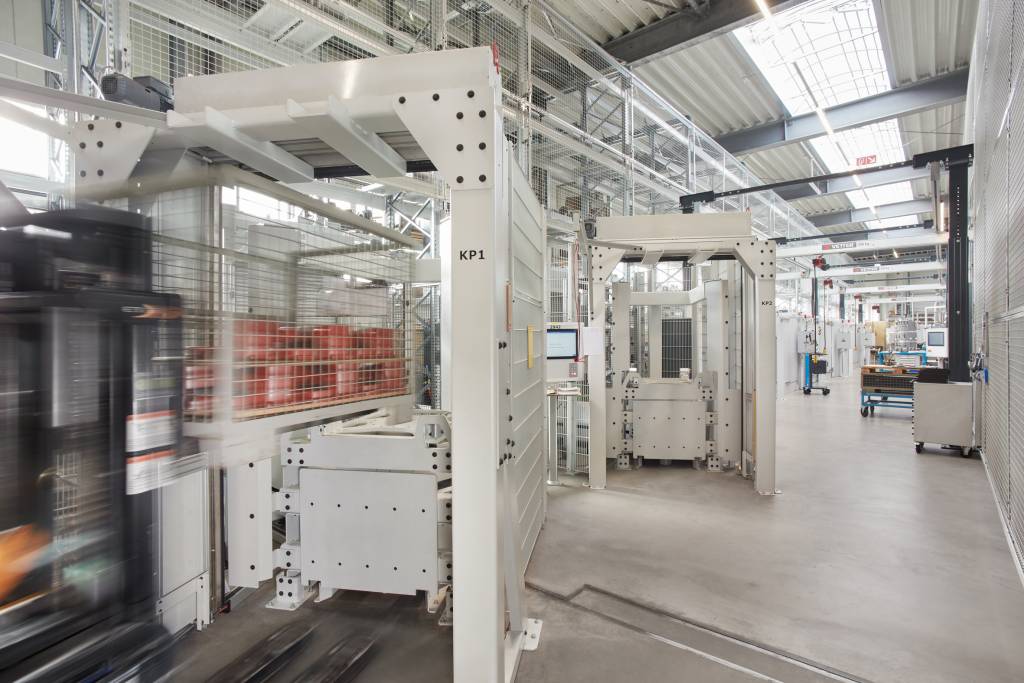
Zum Angebot der Firma Kordel Antriebstechnik gehören Getriebe für Flurförderzeuge, Getriebe für Landmaschinen sowie Getriebe für Baumaschinen. Das Unternehmen ist einer von wenigen Getriebelieferanten, die eine hohe Fertigungstiefe haben, um vom Rohling bis zum fertigen Getriebeteil jeden Arbeitsgang abzudecken. Insgesamt fertigt das Unternehmen etwa 325.000 Getriebe im Jahr. Die Grundüberlegung lautete, das tägliche Rüsten, das an Stand-Alone-Maschinen erforderlich ist, durch automatisierte Abläufe zu ersetzen.
Modernisierung mit automatisierten Anlagen
Vor vier Jahren begannen die Planungen, die Fertigung in Dülmen ebenso wie am zweiten Produktionsstandort in Jawor, Polen, mit automatisierten Anlagen zu modernisieren. Für neue Bearbeitungszentren, auf denen Getriebeteile aus Guss und Aluminium gebohrt und gefräst werden, entstand eine automatisierte Materialversorgung vom Lager zur Maschine und wieder zurück. Zwei Anlagen mit je zwei Strängen des PHS 1500 PRO bedeuteten den bisher größten Einzelauftrag für die Palettenhandhabungssysteme bei Liebherr. In der Projektierung wurden zunächst alle Abläufe betrachtet und anschließend für jeden einzelnen Schritt entschieden, ob er künftig automatisiert oder händisch ausgeführt werden soll. Während die Reduzierung der Rüstzeiten, die zuvor etwa ein Drittel der Maschinenzeit beanspruchten, das Hauptargument für die Automatisierung in Dülmen war, bestimmte in Jawor der Fachkräftemangel die Entscheidung.
Mit zwei Strängen zur individuellen Lösung
Da Kordel mit ca. 25.000 Eigenfertigungsteilen eine große Teilevielfalt anbietet, muss die Materialversorgung hierauf abgestimmt sein. Die Abläufe sind bestimmt durch die Losgrößen von typischerweise fünf bis 30 Teilen pro Auftrag. Entsprechend ist die Materialbeschaffung ein sensibler Punkt; das Shuttle, das die Rohteile zur Maschine bringt, darf nicht zum Engpass werden. „Das Bearbeitungszentrum ist die teuerste Komponente, sie muss immer laufen und darf nie auf die angeschlossenen Systeme warten,“ fasst Johannes Kordel, einer der Geschäftsführer und bei Kordel für die technische Leitung zuständig, die wichtigste Vorgabe zusammen. Schnell war klar, dass das bei der geforderten Taktfrequenz mit einem einzigen System nicht zu machen war. Deshalb besteht die Anlage jetzt aus zwei Strängen, einem Materiallagersystem und einem Fertigungssystem mit je einem Regalbediengerät. Die zwei Systeme kommunizieren permanent über die gemeinsame Leitsteuerung miteinander. Als die Idee für die Architektur mit zwei Strängen stand, erfolgte die Berechnung, wie viele Maschinen über ein solches System zu bedienen wären. Im Ergebnis sind die PHS heute für bis zu sechs Maschinen ausgelegt. An beiden Standorten stehen aktuell bereits je fünf baugleiche Bearbeitungszentren. Die Stränge sind parallel angeordnet, sodass die Wege zwischen beiden Seiten möglichst kurz gehalten sind.
Reibungslose Abläufe
Um eine hohe Frequenz und kurze Taktzeiten zu halten, müssen die Abläufe an allen Übergabepunkten reibungslos sein. Auf der Materialseite gibt es zwei Be- und Entladestationen für Gabelstapler und acht für die händische Entnahme. Fährt ein bearbeitetes Gehäuse aus der Maschine über Regalbediengerät 1 in eine Rüststation des Fertigungssystems, wird aus dem Materiallagersystem je eine Gitterbox für die Fertigteile, als auch eine Gitterbox mit Rohteilen über Regalbediengerät 2 ausgeschleust. Es ist erforderlich, dass alle benötigten Werkzeuge hinterlegt und bevorratet sind. Wenige, sehr spezielle Messmittel sind nicht an allen Bearbeitungsstationen vorgesehen, die Mehrzahl der Werkstücke soll allerdings an allen Stationen zu bearbeiten sein. Neben den sechs Rüstplätzen auf der Maschinenseite, von denen je zwei nebeneinander liegen und von insgesamt drei Mitarbeitern bedient werden, gibt es einen separaten Platz für kompliziertere Artikel, neue Vorrichtungen oder Problemfälle, damit die Mitarbeiter an den Doppelstationen ungestört weiter arbeiten können. Die Maschine arbeitet den Auftrag ab und bringt die Vorrichtung wieder zurück. Jedes Bauteil hat ein eigenes Hebezeug, das rechtzeitig bereitgestellt werden muss.