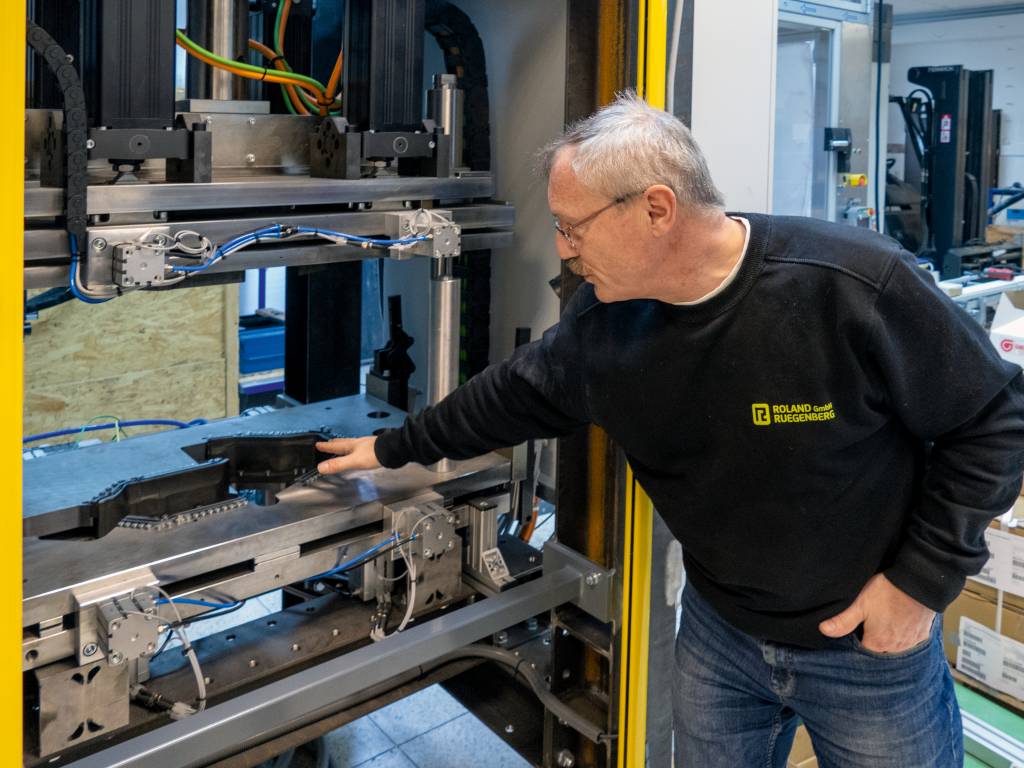
Durch die Realisierung zahlreicher Bördel- und Falzanlagen hat Ruegenberg viel Knowhow auf diesem Gebiet gesammelt. Die Anlagen verbinden zwei Blechelemente schnell und zuverlässig – ohne zu schweißen. Daneben bietet das Unternehmen auch Lösungen für einen ebenen Bord sowie für einen besonders kleinen und enganliegenden Falz. Die Bearbeitungszeiten liegen unter 30 Sekunden pro Teil in vollautomatisierten Anlagen. Ende 2018 erhielt Ruegenberg den Auftrag eines Automobilzulieferers für mehrere automatische Falzanlagen. Besondere Herausforderungen hierbei waren die Produktvielfalt, die Rüstzeit, enge Platzvorgaben und ein anspruchsvoller Terminplan. Eine wichtige Hürde stellte die Technologie zur Ummantelung und Isolation von abgasführenden Komponenten dar. Sie wurde parallel zum Auftrag entwickelt und getestet. Anstelle herkömmlicher Hydraulik kam moderne Servoantriebs- und Steuerungstechnik zur Anwendung.
Große Verfahrgeschwindigkeiten und Dynamik, hohe Anforderungen an Kraft bzw. Leistung und bei unterschiedlichen Kräften synchron im Verbund fahrend – so lautete einige der Herausforderungen. Darüber hinaus sollten die verbauten Motoren möglichst leicht und individuell konfigurierbar sein. Aufgrund der verlässlichen bereits bestehenden Partnerschaft und positiven Erfahrungen in vorangegangenen Projekten entschied sich Ruegenberg bei der Antriebstechnik für SEW-Eurodrive.
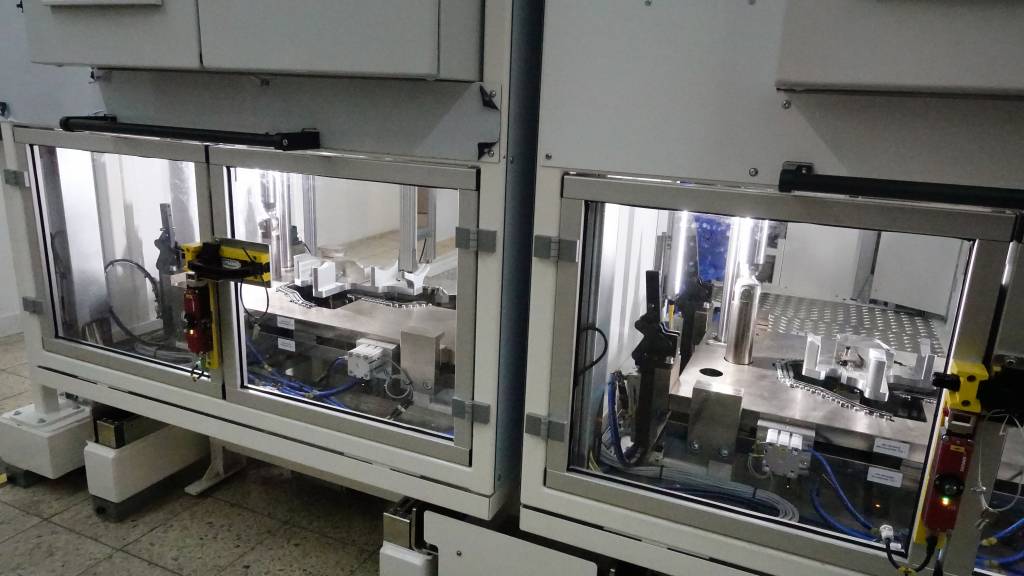
Hydraulisches Testwerkzeug
Zunächst mussten verschiedene Tests durchgeführt werden. „Dazu verwendeten wir ein hydraulisch angetriebenes Probewerkzeug“, erläutert Matthias Scheffler, CAD-Konstrukteur bei Ruegenberg. Allerdings sei ein Hydraulikzylinder langsam und nicht punktgenau zu steuern. „Bei der Vorserie hatten wir bereits einen Vierer-Achsverbund mit Elektrozylindern für die Arbeitshübe und Zwischenpositionen eingesetzt. Der Zweier-Achsverbund für die Schließbewegung wurde aber zunächst mit Hydraulikzylindern realisiert“, ergänzt Elektrik-Abteilungsleiter Matthias Kürzer. „Nach den Tests entschlossen wir uns, den Hydraulikhub ebenfalls mit Elektrozylindern auszuführen.“ Diese Umsetzung wurde parallel zum Auftrag entwickelt. Für die Blechteile war ein spezieller Beschnitt erforderlich sowie sehr geringe Toleranzen.
An der Beladestation werden durch einen Werker Hitzeschilde und Bauteil zusammengesetzt. Mittels eines Drehtellers wird das Bauteil in die Maschine geschwenkt. Ein Roboter übernimmt das weitere Bauteil-Handling. Über die Codierung der Werkzeuge ist sichergestellt, dass er stets das richtige Werkzeug bedient. Nach dem Bördel- bzw. Crimpvorgang bringt der Roboter das Bauteil zur Laserstation, wo ein Datamatrix-Code sowie Klarschrift aufgebracht werden. Im Anschluss wird auch ein Etikett gedruckt und automatisch aufgeklebt. Erst wenn sicher ist, dass die Bauteile korrekt markiert wurden, wird das Bauteil für die weitere Bearbeitung ausgegeben.
Doppelt gefalzt hält besser
Die bisherige Umsetzung basierte auf einem einfachen Falz im Verbund mit einer Punktschweißung. Die Festigkeit dieser Verbindung liegt allerdings unter der des neuentwickelten Crimpverfahrens. „Die größten Herausforderungen beim Doppelfalzen sind Faltenlagen in den Hitzeschildblechen. Dazu kommt die Unsicherheit bei den dabei zu erwartenden Prozesskräften“, erklärt Scheffler. „Die genaue Dosierbarkeit der Einzelkräfte ist daher äußerst wichtig, damit zum einen jeder Einzelvorgang gesamtumfänglich korrekt ausgeführt wird und zum anderen die schmalen Stempel und Matrizen des Werkzeugs nicht beschädigt werden.“ Daher wurde der Crimp zunächst mit einer Handvorrichtung erzeugt und dabei den erforderlichen Kraftaufwand gemessen. Eine Anforderung an die Anlage war, dass auf ihr unterschiedliche Bauteile gefertigt werden, die drei verschiedene Werkzeuge erfordern. Wenn in Zukunft neue Bauteile hinzukommen, wird nur ein neues Werkzeug benötigt. Die modular aufgebaute Anlage kann bleiben wie sie ist, lediglich ein neues Rezept mit den Verfahrwegen und Kraftgrenzen der Motoren wird aufgespielt.
Die Besonderheit der neuen Lösung zeigt sich darin, dass auch in Radien und Kurven die Falzkante geschlossen ist. Das ermöglicht, das Bauteil mit einem rundum geschlossenen Falz ohne Unterbrechung zu versehen. Durch das zweifache Falzen und anschließendes Aufstellen der Falzkante wird eine höhere Festigkeit erzielt. Die innenliegende Isolierung ist vor eindringenden Flüssigkeiten wie Wasser oder Öl geschützt. Die thermischen Eigenschaften werden verbessert. Der Doppelfalz ist weniger anfällig gegenüber Vibrationen als eine punktgeschweißte Verbindung und weist somit eine längere Lebensdauer auf. Durch den Crimpprozess entstehen keine offenen oder scharfen Kanten. Daher stellt dieser Falz kein Sicherheitsrisiko für die Werker in der Endmontage dar.
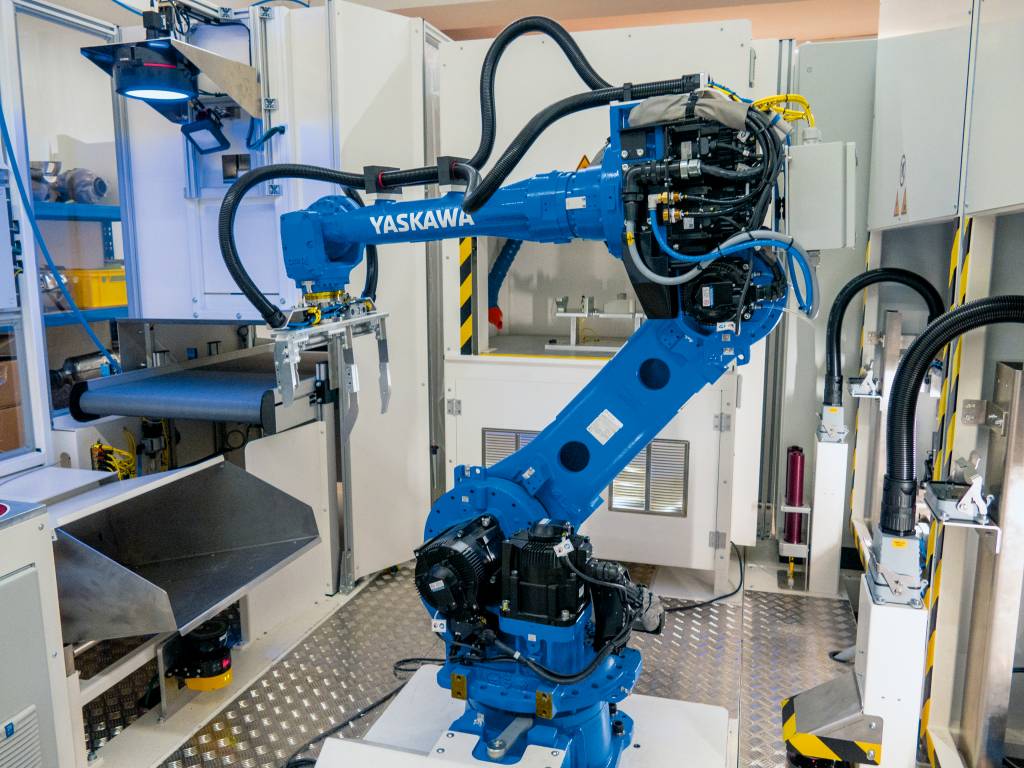
Bestückung der Maschine
„Gegenwärtig verarbeiten wir drei verschiedene Bauteiltypen“, so Kürzer. Dafür gibt es drei unterschiedliche, binär codierte Werkzeuge. Dazu wird das Rezept in die Steuerung geladen. Jede Anlage hat zwei Werkzeugstellplätze, so dass Rüstzeiten minimiert werden. Weil die Steuerung Werkzeuge, Stellplatz und Bauteile eindeutig identifiziert, entscheidet der Roboter automatisch die Zuordnung des Bauteils. Kürzer fährt fort: „Es gibt ein enges Zusammenspiel zwischen dem Beschnitt der Hitzeschilder und der Werkzeugkontur.“ Um einen sauberen Falz zu erzielen, wird in der Entwicklungsphase manchmal Material der Schale weggenommen oder hinzufügt. Gelegentlich wird in der Erprobungsphase die Werkzeugkontur angepasst, um einen perfektes Falzergebnis zu erzielen. Ist der Falz fertig erprobt, bedarf es keiner weiteren Nachjustierungen an den Hitzeschildern oder der Werkzeugkontur.