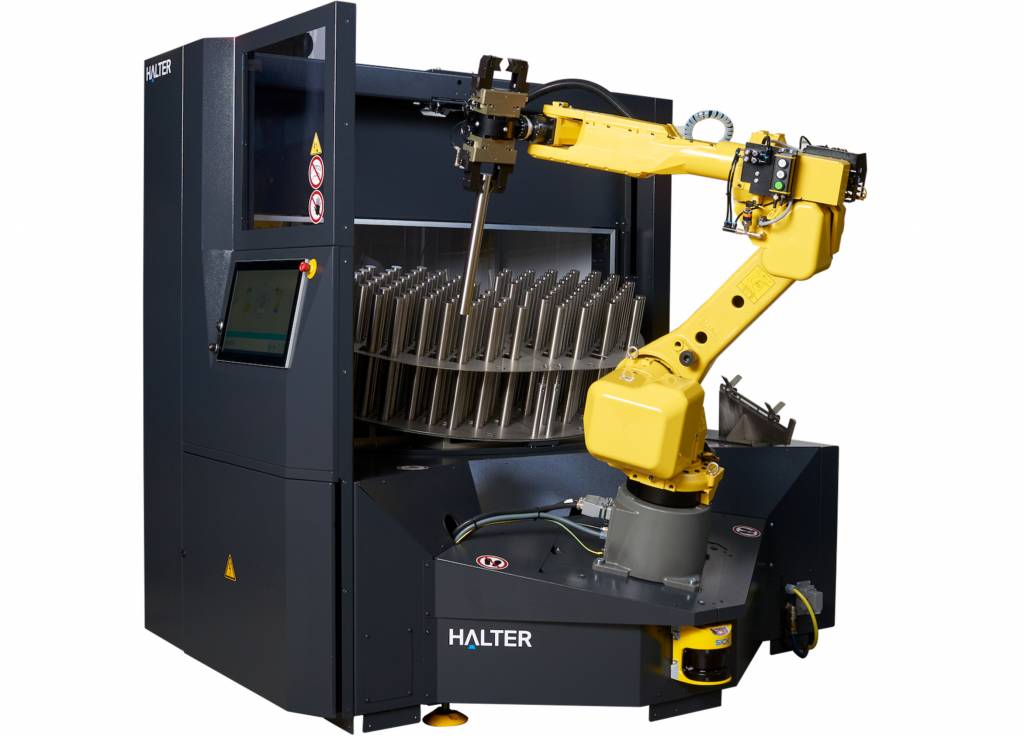
Heinz Knöpfle ist als Lohnfertiger auf die Bereiche Drehen, Dreh-Fräsen und Fräsen spezialisiert. Der Betrieb fertigt unter anderem präzise und anspruchsvolle Dreh- und Frästeile vom Einzelteil bis hin zu Klein- und Großserien für unterschiedliche Branchen wie Maschinenbau, Medizintechnik, Luftfahrt oder Lebensmittelindustrie. Vor rund 16 Jahren erwarb das Unternehmen die erste Maschine von Mazak, die ein Jahr darauf mit einem Stangenlader automatisiert wurde. Dem Maschinenhersteller ist der Geschäftsführer Christian Knöpfle, der mit seinen Geschwistern Susanne und Andreas 2009 die Firma in der zweiten Generation übernahm, bis heute treu geblieben – und ebenso dem Automatisieren. Gemessen an der Beschäftigtenanzahl (fünf Mitarbeiter) verfügt die Firma über einen beachtlichen Maschinenpark: Auf einer Produktionsfläche von rund 1.500m2 befinden sich insgesamt 22 Anlagen von Mazak, alle automatisiert z.B. mit Paletten- und Shuttlesystemen oder Stangenladern. Der Einstieg speziell in die robotergestützte Automatisierung begann 2018, als Knöpfle über einen Salesmanager von Mazak auf Halter CNC Automation aufmerksam wurde. Wenig später wurde das erste Dreh-/Fräszentrum, eine Mazak Integrex i-200ST, mit einem Halter Universal Premium gekoppelt.

Kompakte Roboterzelle
Die Lösungen von Halter CNC Automation sind kompakte, besonders vielseitig einsetzbare Roboterzellen in verschiedenen Ausführungen für CNC-Drehmaschinen und -Fräsmaschinen, die für das automatisierte Be- und Entladen von rotationssymetrischen und rechteckigen Werkstücken sowie auch langen Wellen entwickelt wurden. Hierzu stehen verschiedene Werkstückaufnahmen, darunter z.B. beim Halter Universal Premium sogenannte Rasterplatten, als Teilepuffer mit unterschiedlicher Kapazität zur Verfügung. Während der Roboter auf der Vorderseite ein CNC-Dreh-/Fräszentrum belädt oder Fertigteile entnimmt, kann ein Mitarbeiter auf der Rückseite das System mit neuen Rohteilen bestücken – ohne Unterbrechung der laufenden Produktion. Die Roboterzelle ist rasch installiert und lässt sich als mobile Lösung bei Bedarf überdies von einer Maschine zu einer anderen umpositionieren.
Vier weitere Lösungen
Die Vorzüge der ersten Roboterzelle überzeugten offensichtlich, denn allein in den letzten beiden Jahren investierte das Unternehmen in vier weitere Lösungen von Halter CNC Automation: zwei zusätzliche Halter Universal Premium für ein CNC-Dreh-Fräszentrum sowie ein Dreiachs-Bearbeitungszentrum, einen Halter Big für ein CNC-Dreh-/Fräszentrum vom Typ Mazak i-300 und einen Halter Turnstacker Compact 12 für eine Mazak Quickturn Nexus 250-II MSY. Beim Halter Big handelt es sich um ein Beladesystem, das eigens für schwere Werkstücke und somit lange Wellen bis 800mm ausgelegt ist. Die gleichsam kompakte und robuste Lösung integriert einen Roboter mit einer Tragfähigkeit von bis zu 70kg. Der Halter Turnstacker Compact verfügt hingegen über insgesamt zwölf Stapelstationen für einen hohen Werkstück- und Fertigteilepuffer mit einem maximalen Fassungsvermögen von bis zu 385 Teilen.
Nach Auffassung von Knöpfle habe ihn die durchgängige Automatisierung dazu gezwungen, noch sorgfältiger über die damit zusammenhängenden Prozesse nachzudenken. So muss unter anderem auf die Temperaturen in der Maschine im Sinne einer konstant hohen Genauigkeit bei der Werkstückbearbeitung, den Werkzeugverschleiß und die Werkzeugverfügbarkeit, eine ausreichende Kühlmittelzufuhr und nicht zuletzt auf einen hocheffizienten Abtransport der Späne geachtet werden, um nur einige Faktoren für eine hohe Prozesssicherheit zu nennen. Bekommen Fertigungsverantwortliche solche und weitere Herausforderungen zuverlässig in den Griff, führt das letztendlich zu einer gleichbleibend hohen und somit stabilen Fertigungsqualität mit spürbar steigender Produktivität.
Unbemannte Schichten
Bei Heinz Knöpfle wird rund um die Uhr im Drei-Schicht-Betrieb gefertigt, mit bemannter Tagschicht und unbemannten Spät- sowie Nachtschichten. Auch an den Wochenenden laufen die Maschinen, weitestgehend unbemannt. So ließen sich die Spindelzeiten bei einigen mit Roboterzellen gekoppelten Maschinen um das Dreifache steigern. Und mit einer automatisierten Maschine werden gar bis zu 6.000 Spindelstunden im Jahr erzielt. Analog hierzu verdoppelte sich innerhalb von nur zwei Jahren durch gleichsam konsequente wie weitsichtige Automation der Umsatz des Unternehmens.