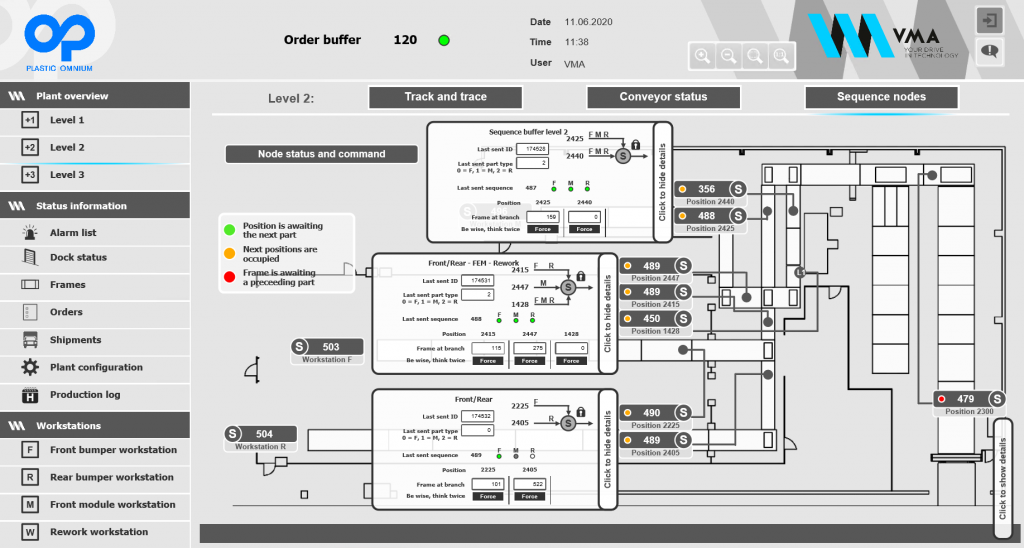
Die neueste E-Auto-Generation eines großen europäischen Automobilkonzerns braucht Stoßfänger. Um diese effizient produzieren zu können, musste der französische Automobilzulieferer Plastic Omnium eine bestehende Fließband-Installation erweitern, wodurch auch ein neues Scada-System nötig wurde. Die Funktionalität sollte sich so nah wie möglich an der bisherigen Lösung orientieren, sodass sich die Mitarbeiter möglichst wenig umgewöhnen müssen. Die bestehende SPS wurde aktualisiert, jedoch nicht ersetzt: „Das Risiko einer Produktionsverzögerung wäre für den Zulieferer einfach nicht tragbar gewesen“, betont Dirk Stradiot, Software Engineer bei VMA, einem Systemintegrator mit weltweit 850 Mitarbeitern.
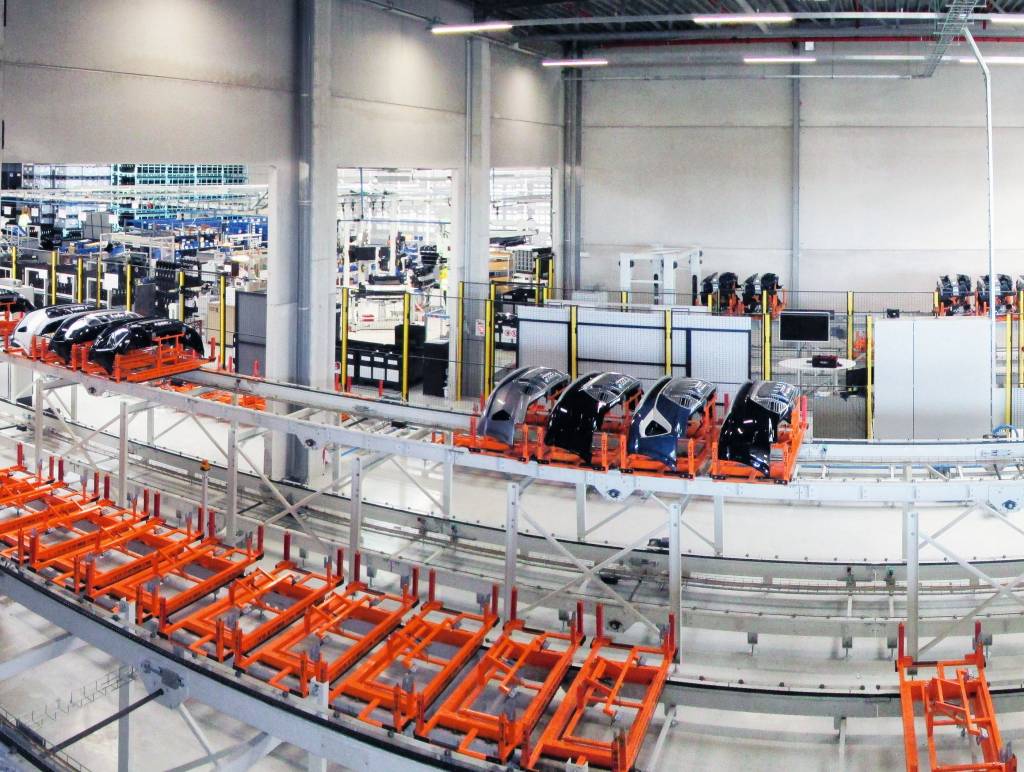
Offenheit macht flexibel
Der Zulieferer setzte bislang auf ein proprietäres Scada-System. „Das bestehende war für unsere Ingenieure eine Black Box“, schildert Stradiot die herausfordernde Situation. Das setzte entsprechend viel Flexibilität beim Einbinden der neuen Lösung voraus. Hinzu kam, dass zahlreiche kundenspezifische Logiken integriert und die Kommunikation mit Datenbanken, Barcode-Lesern und anderen Systemen sichergestellt werden musste. „Uns wurde schnell klar, dass wir mit einer 08/15-Lösung kaum zum Ziel kommen würden“, so der Ingenieur.
Deshalb kam Atvice Scada von Bachmann Visutec zum Einsatz. Mit OPC UA als weit verbreitete Schnittstelle bindet das System Prozessdaten von allen namhaften Steuerungsherstellern an. Darüber hinaus können Atvise-Scada-Anwendungen schnell und einfach mit Datenbanken und Webservices interagieren. Das Kommunikationsmodul ermöglicht eine zusätzliche Erweiterung der Schnittstellen und stellt eine Anbindung per Modbus, BacNet sowie den Zugriff auf Siemens- und Rockwell- Steuerungen ohne OPC-UA-Server sicher.
Einfache Visualisierung
Bei Plastic Omnium entfielen 90 Prozent der gesamten Entwicklungsaufwände in Atvise auf die Steuerlogik. Die restlichen 10 Prozent waren der klassischen Visualisierung zuzuschreiben, und Stradiot ist erfreut: „Dank der Offenheit von Atvise konnten wir für alle Produktionsschritte maßgeschneiderte und klar verständliche Bedienoberflächen basierend auf reiner Web-Technik erstellen. Auf die unterschiedlichen Displaygrößen skaliert Atvise automatisch und verlustfrei.“ Mit direkter API-Anbindung werden Bestellungen und Produktionsdetails bis hin zur aktuellen Position einzelner Stoßfänger in der Produktionsstraße in Echtzeit zwischen Hersteller und Zulieferer ausgetauscht. Eine Ablaufsteuerung berücksichtigt die unterschiedlichen Produktionszeiten der einzelnen Teile und sorgt für eine zuverlässige Just-in-Sequence-Anlieferung, zur richtigen Zeit in der korrekten Reihenfolge. „Diese Branche verzeiht keine Fehler oder Verzögerungen. Mit Atvise liefen Steuerlogik, Datenbankanbindung und Datenaustausch bislang völlig fehlerfrei und zuverlässig“, zeigt sich Dirk Stradiot zufrieden.
Inbetriebnahme in Rekordzeit
Die Installation beim Automobilzulieferer erstreckt sich über eine Fläche von rund 2.000m². „Das war kein kleines Projekt. Dass wir die komplette Anlage in weniger als zwei Monaten abbauen, mit Erweiterungen neu aufbauen und in Betrieb nehmen konnten, haben wir der einfachen Skalierbarkeit von Atvise zu verdanken“, ist der Software-Spezialist überzeugt. Besonders hilfreich für die Ingenieure bei der Inbetriebnahme sei das Online Engineering gewesen. Sie konnten sämtliche Änderungen direkt im laufenden Betrieb vornehmen, ohne das System im Anschluss stoppen oder neu starten zu müssen. „Das war ein echter Gewinn für uns.“