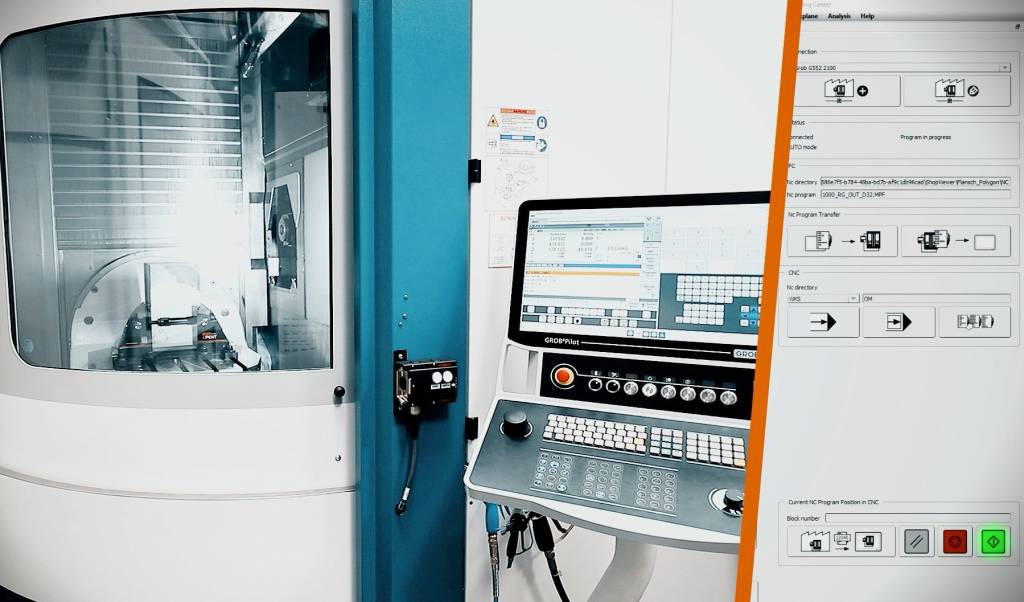
Grundlage einer Digitalisierung ist zunächst die Datenweitergabe im Unternehmen – ohne Medienbrüche. Und es geht noch weiter: Es gilt ein Bewusstsein dafür zu entwickeln, wie sehr Produkte oder Bauteile heute durch Datenströme bestimmt werden. Sie sind nicht mehr nur von ihren CAD-Daten definiert, sondern durch die Summe aller in der Fertigungsprozesskette entstehenden Informationen, wie CAM-Daten, NC-Codes, Fertigungsparameter, Daten über benötigte Werkzeuge und Bearbeitungszeiten. Hier gilt es einen wertvollen Informations-Pool zu verwalten, inklusive Beteiligung des CAM-Systems. Dieses ist über Schnittstellen mit allen Systemen zu vernetzen, die mit fertigungsrelevanten Daten umgehen. Wer eigene Produkte herstellt, nutzt eventuell eine Product-Lifecycle-Management-Software als datenführendes System. Auftragsfertiger setzen dagegen häufig auf ein Manufacturing-Execution-System.
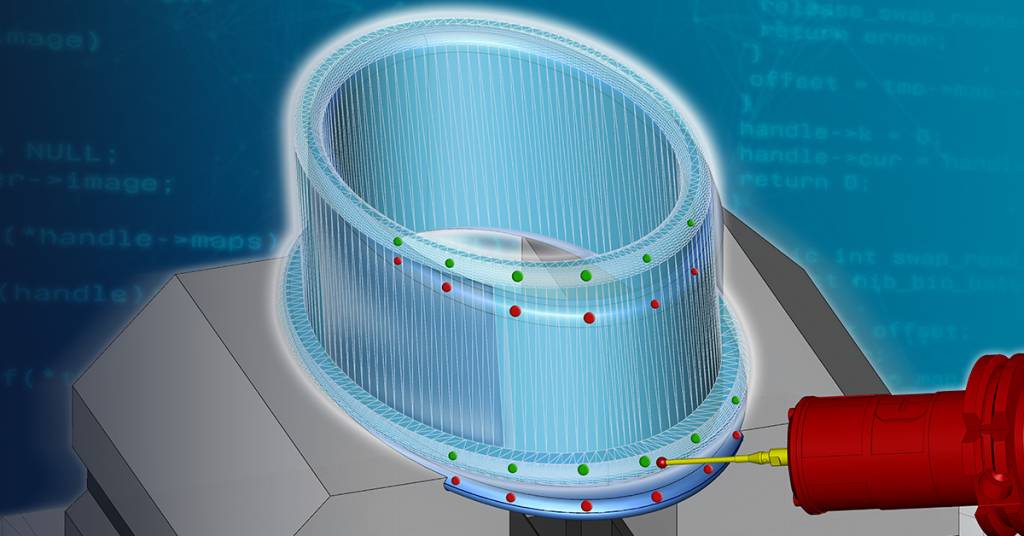
Nachhaltigkeit mit CAM
CAM wird heute mehr und mehr zum zentralen Baustein einer nachhaltigen und ressourcenschonenden Produktion. Hier entstehen die NC-Codes, die eine effiziente werkzeug- und maschinenschonende Bearbeitung zulassen und Ausschuss verhindern. In Zukunft werden weitere Optimierungsoptionen entstehen, wie ein Forschungsprojekt des Instituts für Fertigungstechnik und Werkzeugmaschinen der Leibniz Universität Hannover in enger Kooperation mit Open Mind Technologies zeigt. Dabei geht es um die Energieeinsparung durch Kühlmitteldrucksteuerung. Aber schon heute erzielen vernetzte CAM-Systeme signifikante Optimierungen. Ein einfaches Beispiel ist die Werkzeugverwaltung: Sie umfasst auch die Parametererfassung, die Dokumentation von Standzeiten und Schnittwerten sowie Simulationen, die auf individuellen 3D-Werkzeugdaten basieren.
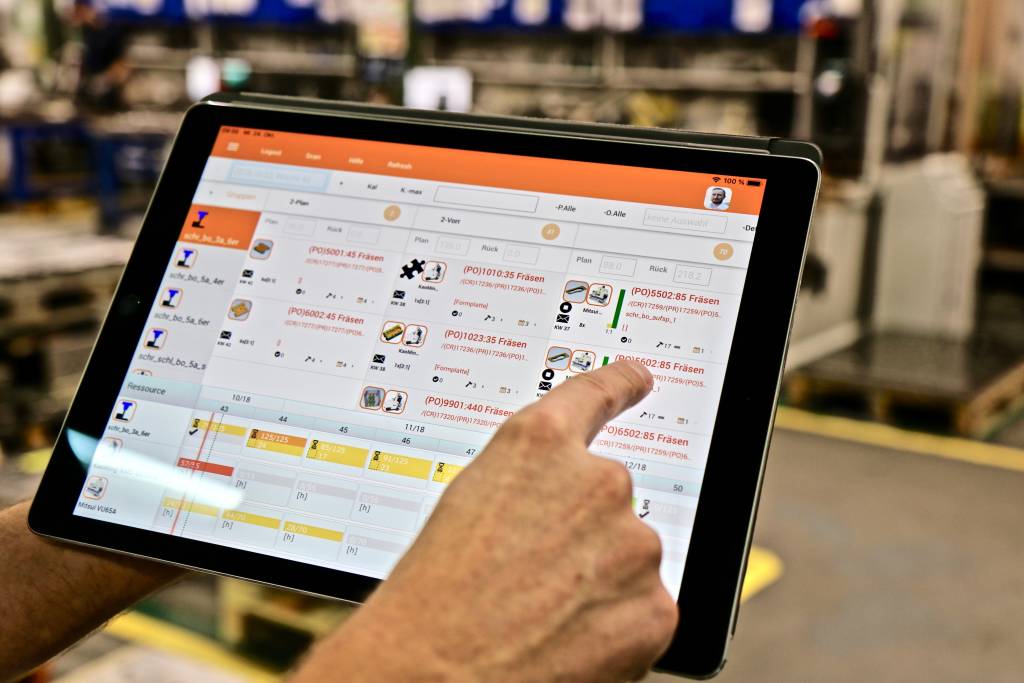
Die virtuelle Maschine
NC-Codes über das Netzwerk direkt an die Maschinensteuerungen zu übertragen, ist aktuell ein verbreiteter Standard. Der logische nächste Entwicklungsschritt ist die bidirektionale Kommunikation zwischen CAM und Steuerung. Ganz neue Optimierungsmöglichkeiten eröffnen sich, wenn die Bearbeitungssimulation mit echtem NC-Code und einem digitalen Zwilling der Maschine arbeiten kann. Dann ist z.B. eine generische CAM-Programmierung möglich. Ein bestens angepasster NC-Code wird erst dann generiert, wenn feststeht, welche Maschine für die Produktion zum Einsatz kommt. Die Limitation einer Rotationsachse zu erkennen und Re-Winds automatisch einzufügen, bedeutet dann keinen zusätzlichen Programmieraufwand mehr.
Digital Twin und 3D-Druck
Vielfältige Potenziale bei der Ressourcenschonung eröffnet heute die additive Fertigung. Wer kleine Losgrößen, Einzelstücke oder Prototypen produziert, kann unter Umständen Werkzeugkosten einsparen. Hohes Spanvolumen lässt sich gerade bei filigranen Bauelementen mit 3D-Druck vermeiden. Aber ganz gleich, welches additive Verfahren Unternehmen einsetzen: Eine zerspanende Nachbearbeitung ist praktisch immer erforderlich. Und dafür muss das Rohteil manuell ausgerichtet werden – ein zeitaufwendiger und fehleranfälliger Prozessschritt, der beispielsweise auch bei durch Schweißen reparierten oder gegossenen Werkstücken auftritt. Viele Produzenten scheuen diesen zusätzlichen Aufwand bei der Nachbearbeitung – er kann die Entscheidung für additive Fertigung negativ beeinflussen.