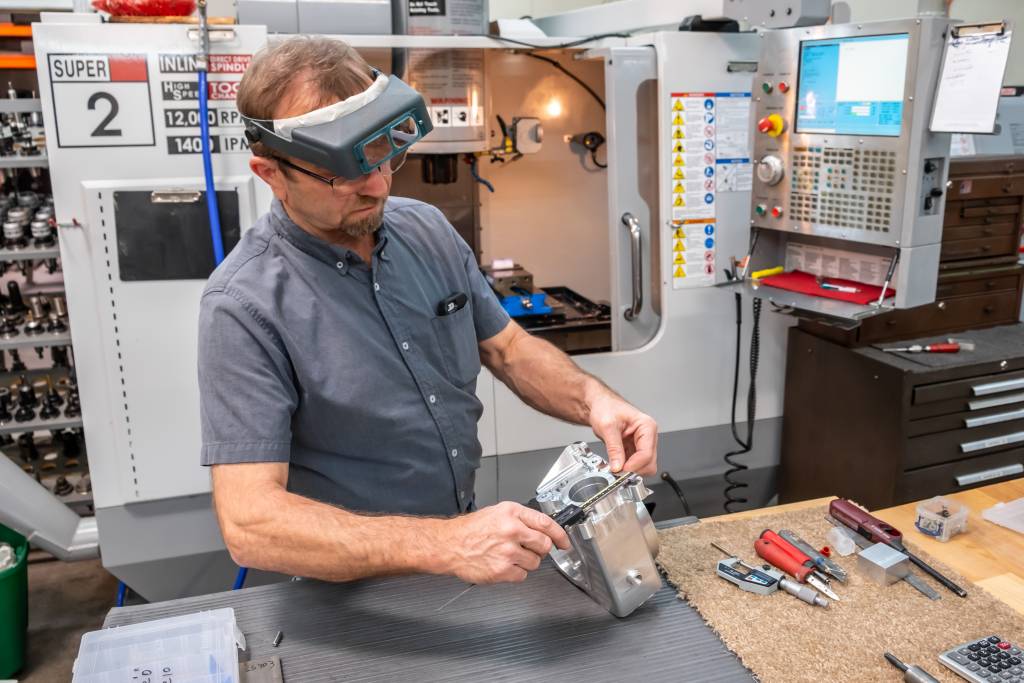
Als Hersteller von komplexen Präzisionsteilen hat sich die Martin Höhn GmbH auf dem internationalen Markt etabliert. Die Kernkompetenz des Familienunternehmens mit 170 Mitarbeitern liegt in der Bearbeitung von Edelstählen, Titan, Hasteloy und hochfesten Vergütungsstählen sowie Aluminiumlegierungen, Gussarten und Kunststoffen. Obwohl die Gelenklagertechnik viel Handarbeit verlangt, ist es Höhn gelungen, in der Fertigung einen hohen Automatisierungsgrad zu erreichen. Außerdem verfügt das Industrieunternehmen über eine große Fertigungstiefe für die Zerspanungsbearbeitungen und für die Montage. Dafür hat Höhn hohe Investitionen in robotergestütztes Handling getätigt, etwa bei den Montageautomaten.

20 Jahre Zusammenarbeit
Bereits seit 1989 arbeitet Höhn mit dem MES-Anbieter GBO Datacomp zusammen. Damals wurde eine Lösung zur Betriebsdatenerfassung (BDE) eingeführt, die kurz darauf um eine Personalzeiterfassung (PZE) ergänzt wurde. Im Jahr 2015 hat Höhn die BDE-Lösung aktualisiert und in diesem Zuge die BisoftMES Lösung zur Maschinendatenerfassung (MDE) integriert. „Wir mussten in der Produktion mehr Transparenz schaffen, um im globalen Wettbewerb bestehen zu können“, sagt Geschäftsführer Reiner Höhn. Das MDE-Modul ermöglicht es, Informationen über Maschinen, Personal und Fertigungsaufträge in die MES-Plattform zu integrieren. Durch die Daten wird erkennbar, an welcher Maschine welcher Auftrag mit welchen Leistungszahlen produziert wurde. Auf diese Weise können auch die Ursachen für Maschinenstillstände identifiziert werden. Parallel dazu werden die Prozesse dokumentiert.

Kommunikation mit dem ERP-System
Höhn arbeitet nach dem TOC-Konzept (Theory of Constraints) und hat dafür Engpassmaschinen definiert, die im Produktionsprozess nach Möglichkeit nicht stillstehen dürfen. Sämtliche Produktionsaufträge laufen über Nacht in ein separates System ein, das daraufhin die Fertigungsreihenfolge festlegt. Dabei berücksichtigt das System sowohl die Priorisierung der Engpassmaschinen als auch andere Parameter wie Außer-Haus-Zeiten, etwa für die ausgelagerte Oberflächenbehandlung. Die Reihenfolge liegt jedem Werker als digitale Liste an der Maschine vor, damit er erkennen kann, welcher Auftrag priorisiert ist und wann welche Materialien oder Teile zur Verfügung stehen. Was nun fehlte, war eine Art Drehkreuz, um die Daten zwischen BDE/MDE und dem ERP-System von ProAlpha in beide Richtungen übertragen zu können. Hier kam das MDE-Modul von GBO Datacomb ins Spiel. „Bis wir die erste Maschine angebunden hatten, vergingen gerade einmal vier Monate“, sagt Höhn. Der Austausch erfolgt über eine entsprechende Schnittstelle.
Alle Informationen verfügbar
Durch die Anbindung des Maschinenparks an das ME-System findet ein Informationstransfer zwischen BDE/MDE und Fertigungsplanung statt. Höhn erhält zum einen Informationen darüber, wann welche Aufträge auf welchen Maschinen ausgeführt werden können. Zum anderen erhalten die Werker einen aktuellen Überblick. Alle Informationen liegen jederzeit für die jeweilige Maschine vor. Zudem können die Werker einsehen, welche Aufträge gerade auf anderen Maschinen laufen. „Uns war auch wichtig, dass das System einfach zu bedienen ist“, schildert Höhn. Kommt es zu einem Stillstand, kann der Werker am Terminal per Klick den Grund für den Stillstand eingeben. Zusätzlich wurden in der Fertigung Dashboards installiert, auf denen signalisiert wird, wenn eine Maschine stillsteht. Diese Informationen werden auch auf die Monitore in der Arbeitsvorbereitung übertragen. „Selbst ich kann in meinem Büro die aktuellen Fertigungsdaten abrufen“, fügt Höhn hinzu.