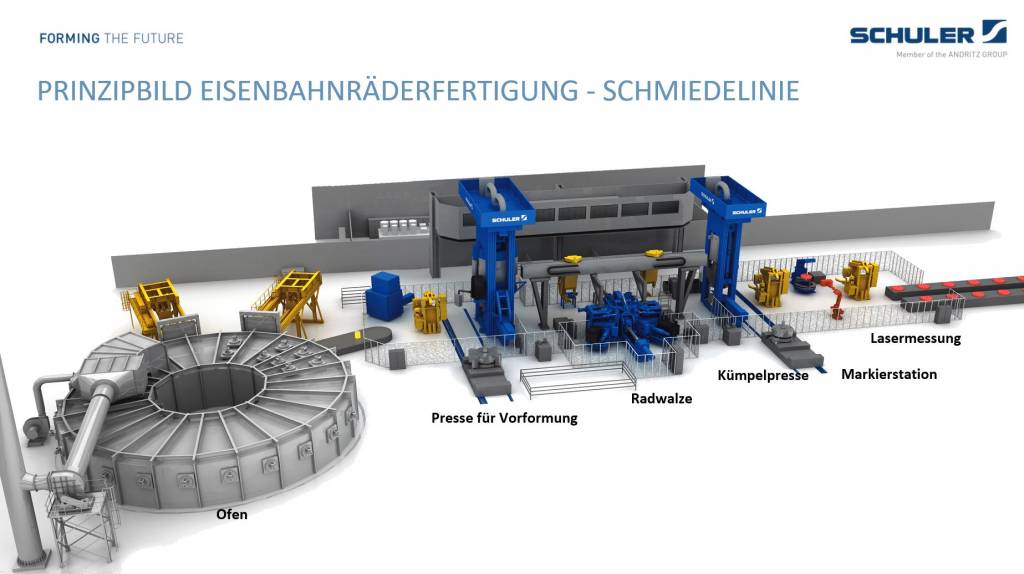
Wer wirtschaftlicher arbeiten will, muss Abläufe eindeutig identifizieren, steuern, dokumentieren und jederzeit reorganisieren können – auch in der Metallverarbeitung. Das trifft auch auf die Fertigung von Eisenbahnrädern in einer Fabrik im kasachischen Ekibastuz zu. Für den gesamten Fertigungsprozess sind Anlagen und Maschinen unterschiedlicher Hersteller im Einsatz, die miteinander interagieren müssen. Zugleich muss für jedes Rad, das das Werk verlässt, der vollständige Fertigungsprozess dokumentiert werden.

Tracking & Tracing
Die komplette Schmiedelinie lieferte die Schuler Pressen GmbH aus dem baden-württembergischen Waghäusel. Das Unternehmen ist zudem für die Koordination und das Zusammenspiel des Track & Trace-Prozesses der einzelnen Anlagenteile zuständig. Dafür musste der Pressenhersteller eine Lösung finden, mit der die Anlageneffizienz im Blick behalten werden kann und gleichzeitig die Qualität jedes Rades dokumentiert wird. Dabei kam die Karlsruher ZOZ & Partner GmbH ins Spiel – ein Unternehmen, mit dem Schuler bereits in der Vergangenheit zusammen gearbeitet hatte. Die Aufgabe bestand nun darin, ein Produktions-Informations-System (PIS) für die gesamte Anlage aufzusetzen.

Räder verfolgen
„Die größte Herausforderung war in diesem Fall die Teileverfolgung. Für einen Großteil der Zeit sind das Material und später die Räder so heiß, dass man sie nicht mit einer Kennzeichnung versehen kann. Trotzdem ist es wichtig, die Geschichte eines jeden Rades zu kennen“, sagt Klaus Gille, Geschäftsführer von ZOZ & Partner. Würde ein Rad von Anfang bis Ende die Produktion durchlaufen, wäre das kein Problem, jedoch ist der Prozess nicht linear: In der Stahlschmelze erhält jede Schmelze eine individuelle Heat ID. Danach werden Stangen geformt und daraus je nach Endgewicht automatisiert Stücke in passender Länge abgesägt. Diese werden dann – circa 340 Stück gemeinsam – bis zum Kern auf 1.200 bis 1.300°C erhitzt, was etwas sechs bis sieben Stunden dauert. Danach muss die dabei entstandene Verzunderung entfernt werden. In zwei Pressstufen erhalten die Räder nun ihre Rohform, werden per Roboter an die Radwalze übergeben, dort in ihre finale Grundform gebracht und anschließend in der Kümpelpresse gelocht. Im Anschluss werden die Räder per Laservermessung geprüft. Räder, die nicht den Vorgaben entsprechen, werden ausgeschleust. Das muss im Produktions-Informations-System dokumentiert werden, um eindeutig zuordnen zu können, welche Eigenschaften jedes Rad hat. Für manuelle Eingriffe muss auch der Mitarbeiter geschult sein – das Ausschleusen muss vermerkt werden.
Räder markieren
Nach dem Vermessen wird jedes Rad mit einer eindeutigen ID markiert. Dann werden die Laufflächen gehärtet. Dieser Prozess hängt von der Stahlmischung des jeweiligen Rades ab, die im System der Heat ID entnommen werden kann. Nach dem Härten werden die Räder nachbehandelt und final geprüft. Täglich verlassen dabei mehrere hundert Räder die Produktion. „Der herausforderndste Teil des Projektes ist aus meiner Sicht die Punkte auszumachen, wo es zu Problemen mit der Nachverfolgbarkeit kommen kann. Also da, wo manuell in den Prozess eingegriffen wird, oder wenn beispielsweise mehrere Elemente gleichzeitig in eine Station hineinlaufen, dort rotiert werden und danach schlimmstenfalls in versetzter Reihenfolge den Prozess wieder verlassen. Dann ist die Nachverfolgbarkeit unmarkierter Räder nicht trivial“, sagt Gille. Das Karlsruher Unternehmen hat dazu eine Lösung entwickelt, die an den Übergabepunkten der Produktion nicht nur die greifbaren Räder, sondern auch alle Informationen dazu virtuell übergibt. Dadurch verlässt jedes Rad mit seinem individuellen Radpass inklusive Produktionsdaten die Fabrik.