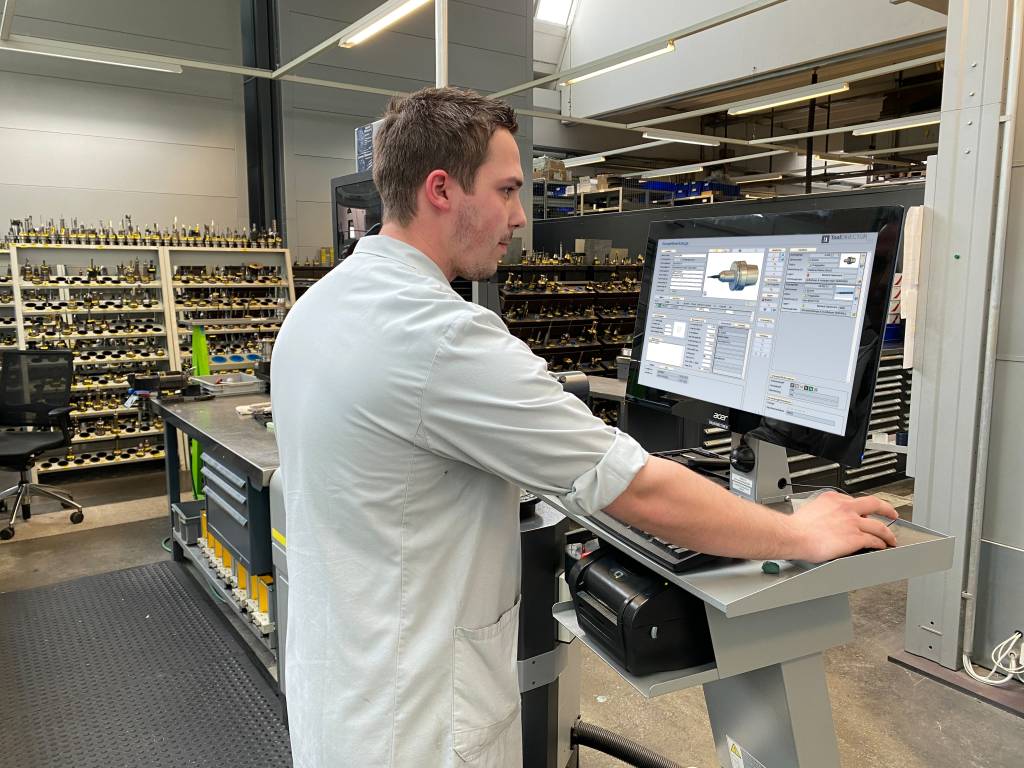
In einem Digitalisierungsprojekt hat der Softwareanbieter Coscom der Wild-Gruppe geholfen, Fehlerursachen in der Auftragsbearbeitung im Sinne von Poka Yoke früh zu erkennen und zu beheben. Der Auftragsentwickler und -fertiger konnte so die Auftragsabwicklung seiner anspruchsvollen optomechatronischen Produkte um bis zu 30 Prozent beschleunigen. Wild entwickelt und fertigt im Kundenauftrag Produkte für die Branchen Medizintechnik, optische Technologien und Industrietechnik, was stabile Prozesse über den gesamten Auftragslebenszyklus erfordert. bei Wild entsteht ein breites Spektrum an medizintechnischen Geräten in Medical & Life Sciences, Labortechnik, InVitro Diagnostik & Analytik, Lasertechnik für medizinische und industrielle Anwendungen sowie optischer Messtechnik und Halbleitertechnikequipment. Die Kunden der fertigers können aus einer Vielzahl an Oberflächen- und Montagetechniken bis zu Reinheitsanforderungen der ISO-Klasse 5 wählen. Neben der Produktqualität, die auch über Normen und Zertifizierungen abgesichert wird, achtet Wild besonders auf die Fertigungseffizienz und -transparenz sowie Prozesssicherheit. Gerade in der Fertigung spielt dabei Software von Coscom Computer aus Ebersberg bei München eine zentrale Rolle.
Präzision als Konstante
Um den Bedarf an Bauteilen mit Toleranzen im µm-Bereich zu bedienen, betreibt die Unternehmensgruppe u.a. eine Hochpräzisionsdrehmaschine. Insgesamt bewältigt Wild die Aufgaben an rund 40 CNC-Maschinen, inklusive temperaturkompensierender Fertigungsmessmaschinen und eines klimatisierten Messraums mit zwei automatisierten 3D-Koordinaten-Messmaschinen. Für den Informationsaustausch sorgt ein Digitalisierungs- und Vernetzungskonzept auf Basis von Coscom-Anwendungen. „Wir müssen den Mitarbeiter, der an der Maschine steht, mit allen Informationen versorgen, die er für seine Arbeit braucht“, sagt Mario Pföstl von Wild.
Drei CAM-Systeme im Zugriff
Bis vor kurzem war der Aufwand an Mehrfachdatenpflege von Fertigungsinformationen hoch, zumal am Stammwerk in Völkermarkt, Kärnten, die beachtliche Anzahl von 150 Aufträgen täglich bearbeitet werden müssen. Da der Auftragsfertiger nicht mehr bereit war, verschiedene Parallelwelten in der Shopfloor-IT hinzunehmen, wurde ein Digitalsierungsprojekt angestoßen. „Zentrales Ziel war, dass die richtige Information zum richtigen Zeitpunkt an der richtigen Stelle abrufbar ist“, sagt der Produktionsleiter am dortigen Standort, Christian Tazoll. Bei Wild muss ein komplexes Wechselspiel bewältigt werden. Zunächst wird die Rohmaterial-Bestellung für einen neuen Auftrag auf den Weg gebracht. Ist es im Haus verfügbar, kommt gemäß Fertigungsbeauftragung über das ERP-System Proalpha die mechanische Bearbeitung mit bis zu 20 Prozessschritten: grobes Honen, Fräsen, feines Honen, zwischendurch Oberflächenveredelung, Drehen usw. „Die Werker müssen an den einzelnen Stationen sehr genau wissen, was zu tun ist: Das CNC-Programm mit den richtigen Parametern verwenden usw. Dabei dürfen keine Fehler auftreten“, betont Tazoll. Manche Bauteile bahnen sich drei Monate lang ihren Weg durch die Fertigungshallen. Zwischenzeitlich kann es zu einer Änderung kommen, die aber nur eine bestimmte Charge an Teilen betrifft. Die Produktion muss daher auch mit verschiedenen Revisionsständen absolut nachvollziehbar arbeiten können. Kurzum: „Es führt kein Weg an einer umfassenden Digitalisierung und Coscom als zentrales System vorbei. Das gilt insbesondere deswegen, weil wir Prozesssicherheit im Rahmen von Zertifizierungen gewährleisten müssen“, sagt Christian Tazoll.
IT wächst zusammen
Für das Shopfloor-Management fließen alle Datenströme auf der Plattform von Coscom zusammen und werden von dort aus verteilt. Es besteht aus dem Fertigungsdatenmanagement FactoryDirector VM und der Werkzeugdatenverwaltung ToolDirector VM. Die Kunden- und Lieferantenstammdaten werden vom ERP-System über FactoryDirector zur Verfügung gestellt. Die CAD/CAM-Prozesskette besteht aus dem 2D/3D-CAD-System SolidWorks und den CAM-Systemen TopSolid V6, TopSolid V7 sowie ProfiCAM VM. Das Prüfmittelmanagement verwendet eine Software von AHP, die Werkzeugvoreinstellung erfolgt über die beiden Zoller-Messgeräte, automatisierte Storage- und Data Retrieval-Systeme von Kardex sind ebenfalls im Einsatz. Als DNC-System ist InfoPoint VM von Coscom für die auftragsbezogene Fertigungsdatenvisualisierung an den CNC-Maschinen eingerichtet. Insgesamt sind 33 Info-Terminals installiert, die per Ethernet ins Produktionsnetzwerk angebunden sind. Außerdem ist das Lasermarkier-System TruMark Station an das digitale Fertigungsmanagement eingebunden. Es sind drei unterschiedliche CAM-Systeme im Einsatz: TopSolid CAM V6 für die Fräsbearbeitung, TopSolid CAM V7 ebenfalls für die Fräsbearbeitung und ProfiCAM VM von Coscom für die Programmierung der Drehmaschinen. Die CAM-Version 6 von TopSolid ist mit der Version 7 und seiner integrierten Datenbank inkompatibel. Es mussten demnach in der Vergangenheit zwei Systeme parallel betrieben werden. Das führte zur ursprünglichen Anfrage aus der CAM-Programmierung bei Wild an den Key Account Manager Christian Snetivy von Coscom: Man wollte alle drei Tools über eine Benutzeroberfläche aufrufen können. „Es musste eine Lösung entwickelt werden, um das neue CAM-System von Missler prozessfähig zu machen“, erinnert sich Christian Snetivy. Unter der Regie von Coscom ist schließlich mit TCI-Technologie und einer Kooperation mit dem Missler-Vertriebspartner Evolving Technologies aus Wien ein integriertes System entstanden: Drei CAM-Anwendungen, die auf Knopfdruck mit den relevanten Daten versorgt werden. Die Werkzeugbereitstellung und -beschaffung, das Messmittel- und das CAM-Programmmanagement erfolgt zentral.