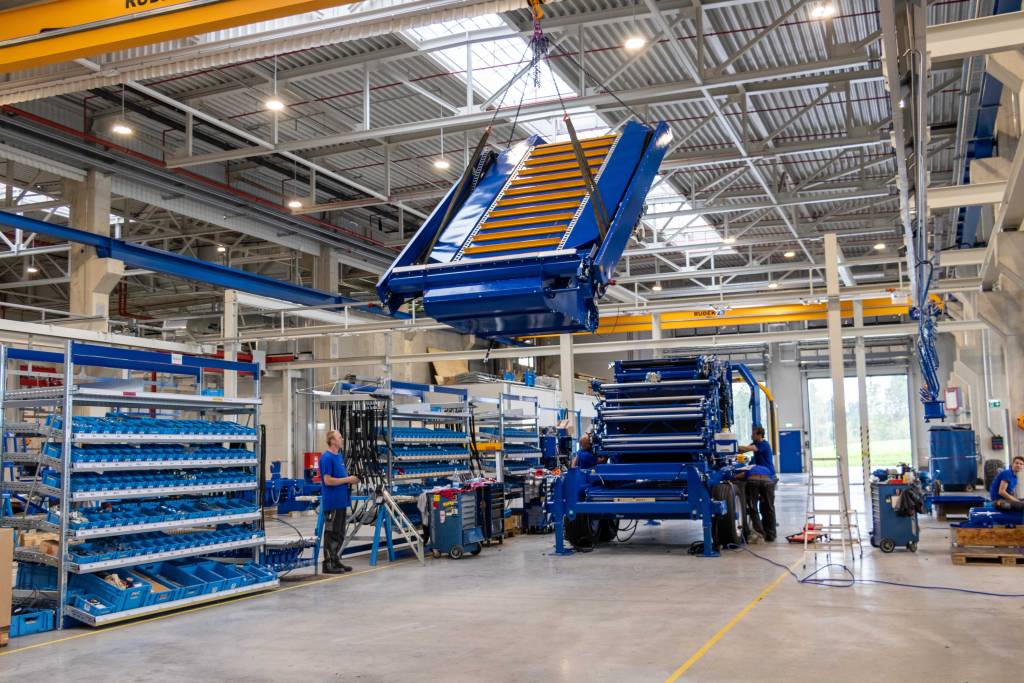
Das Produktprogramm des österreichischen Landtechnikspezialisten Göweil umfasst unter anderem Ballenwickel- und Presstechnik. Die Maschinen sind jedoch mittlerweile auch im industriellen Umfeld im Einsatz. Lange wurden die Produkte ausschließlich am Hauptstandort in Kirchschlag in Oberösterreich produziert. Um den neuen Marktanforderungen und der hohen Nachfrage auch in Zukunft nachkommen zu können, investierte das Unternehmen in den Bau eines neuen Produktionsstandortes. Auf mehr als 15.000m² werden nun auch in Rainbach landtechnische Produkte lackiert, montiert und versandt. Eng verbunden mit dem Projekt war der Wunsch nach Digitalisierung am neuen Standort. „Wir setzen in Lackiererei und Montage auf ein Perlenkettensystem. Das heißt, die geplanten Abläufe erfolgen in einer festgelegten Auftragsreihenfolge, in die nur schwer oder gar nicht eingegriffen werden kann. Die Herausforderung besteht darin, die Transportelemente für die zu lackierenden Teile – die sogenannten Träger – so mit Komponenten zu bestücken, dass die dafür festgelegten Formeln und Lackiervorgänge zusammenpassen und anschließend auch die richtigen Montageplätze damit beliefert werden können. Alleine durch dieses Grundsetting sind in der MES-Vorauswahl einige Anbieter ausgeschieden“, sagt Markus Jungwirth, verantwortlicher Techniker für die Ablaufoptimierung bei Göweil. Ziel sei gewesen, die lackierten Teile so wenig wie möglich ‚anzugreifen‘ und ohne große Umwege immer an den richtigen Orten und Arbeitsplätzen zu haben.
Integrative Systeme als Schlüssel
Bereits vor Baubeginn waren bei Göweil ein ERP- und ein Lagerverwaltungssystem (LVS) im Einsatz. Die für die Fertigung angedachte MES-Software (Manufacturing Execution System) sollte nahtlos an die bestehenden Strukturen anknüpfen und eine Einheit mit ihnen bilden. Mit Cronetwork MES wurde schlussendlich ein System gefunden, das die bestehenden und künftigen Prozesse abbildet und unterstützt. Markus Jungwirth erklärt: „Das LVS wird heute von der Fertigungsfeinplanung angetriggert und damit die notwendigen Kommissionierungsschritte ausgelöst. Die zu lackierenden Teile machen sich auf den Weg, werden auf Trägern verplant und gehen schlussendlich durch die Lackieranlage.“ Das bedeutet im Detail, dass auf Basis der Plandaten in der Feinplanung dem LVS mitgeteilt wird, wo und zu welchem Zeitpunkt die benötigten Komponenten in der Produktion bereitgestellt werden müssen. Es erfolgt eine Verfügbarkeitsprüfung via LVS, das die aktualisierten Daten an das MES retourniert. Sind alle Komponenten verfügbar, gibt der Planer den Auftrag frei. Es folgen die Verplanung und Beauftragung der Transporte durch das LVS, der Start des Lackiervorgangs und schlussendlich die Lieferung an die Montage-Arbeitsplätze. Die MES-Software ist durch laufende, automatische Abgleiche stets über die Auftragsstatus, Abstellplätze, etc. informiert und übernimmt so die führende Rolle im digitalen Shopfloor-Prozess.
Komplexe Aufgaben bewältigen
Auch in der Montage setzt Göweil auf die Feinplanung mit Cronetwork. Die Produkte bestehen größtenteils aus sehr vielen Baugruppen. Diese werden über das MES ‚just-in-time‘ von mehreren Arbeitsplätzen der Endmontagelinie zugeführt. Das bedeutet, dass diese nebeneinanderliegenden Arbeitsplätze so verplant werden müssen, dass die Endmontagelinie optimal mit den nötigen Baugruppen versorgt wird. Diese komplexe Aufgabe kann der Landmaschinenhersteller nun bewältigen.
Mitarbeiter im Fokus
Die Erfassung der dabei gewonnen Daten, etwa zu Mengen und Zeiten, erfolgt mittels BDE-Funktion der MES-Software. Hier rücken die Mitarbeiter am Shopfloor in den Fokus. „Unsere Mitarbeiter werden über die Terminals am Arbeitsplatz informiert, wann welche Montageabschnitte begonnen, bzw. fertiggestellt werden müssen und wann die benötigten Teile zur Verfügung stehen. Zudem können sie weitere produktrelevanten Informationen, wie zum Beispiel Zeichnungen, abrufen“, so Jungwirth: „Die Kollegen nutzen die Cronetwork Terminals außerdem gerne für einen Blick in die nahe Zukunft. So sind sie besser auf die kommenden Aufträge vorbereitet. Ein von uns unterschätzter Effekt sind die vielen Optimierungsideen, die von unseren Mitarbeitern auf Basis dieser neuen Informationen kommen und unsere Abläufe ständig verbessern.“ Ein wichtiger Faktor sei zudem die enge Zusammenarbeit und das Mitspracherecht der Kollegen bei der Gestaltung der Terminals, so Jungwirth.