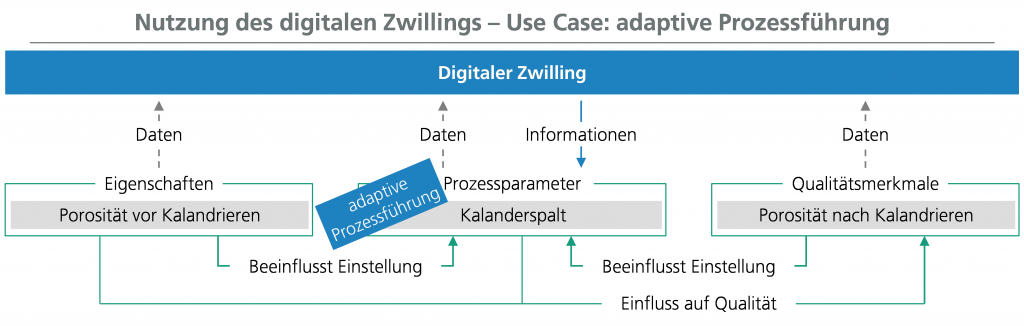
Die Nachfrage nach Batteriezellen boomt, doch ihre Fertigung ist komplex. Sie lässt sich unterteilen in die Fertigung der Elektroden, die Assemblierung – während der die Elektroden in eine Hülle eingesetzt, die Zellen geschlossen und mit Elektrolyt befüllt werden – und die Formierung – die erste Aufladung der Zellen, womit die Bildung wichtiger Eigenschaften verbunden ist. Hierbei erweist sich die Zellqualität als zentrale Herausforderung. Digitalisierung und Vernetzung der Produktion bergen großes Potenzial, um hier die Qualität zu verbessern. Die Erfassung und Verarbeitung von Produktionsdaten ist dabei ebenso wichtig wie die Aggregation von unterschiedlichen Datentypen. Möglich wäre das so: Mit einem geeigneten Traceability-System ließe sich die Batteriezelle prozessübergreifend betrachten. Im System zeichnet sich so der digitale Schatten jeder Batteriezelle ab, der anhand der aggregierten Daten die Ableitung des digitalen Zwillings ermöglicht. Um aus diesem Zwilling Nutzen zu ziehen, werden Modelle basierend auf Algorithmen erstellt, die Rückschlüsse auf die Batteriezelle zulassen.
Von der Raumkapsel zur Batteriezelle
Die NASA schuf bereits für ihre Apollo-Mission das Konzept, ein Produkt eigens für Simulationen nachzubilden. Damals blieb ein Nachbau der Raumkapsel im Space Center in Texas. Seit der Erwähnung des Begriffs Digital Twin in einer Veröffentlichung der NASA wird die Idee in Wissenschaft und Industrie zunehmend thematisiert. Kernelemente eines digitalen Zwillings bilden dabei: die physische Welt, die virtuelle Welt, der Datenfluss von der physischen in die virtuelle Welt, der Informationsfluss in umgekehrter Reihenfolge sowie virtuelle Teilräume. Noch immer wird diskutiert, wie diese Abbilder am besten zu erstellen sind.
Traceability-System verbindet
Die Auseinandersetzung mit dem physikalischen Gegenstück und die Ableitung eines Zielbildes für den digitalen Zwilling ist wichtig. Damit sollen Daten nicht wahllos aufgenommen, kein Ressourcen verschwendet und keine nutzlosen Informationen generiert werden. Das Datenmanagement umfasst sowohl den Soll-Zwilling – die Charakterisierung des zu fertigenden Produkts – als auch Datenaufnahme, -transfer und -vorverarbeitung für jeden Prozess. Isoliert betrachtet lassen die Daten der einzelnen Prozesse kaum Rückschlüsse auf die Qualität des Endprodukts zu. Erst durch die Aggregation der Daten mithilfe einer für die Zellfertigung spezialisierten Traceability-Lösung können interprozessuale Abhängigkeiten IT-seitig erfasst werden. Folglich erweist sich das Traceability-System als digitaler Faden, der die Produktionsprozesse miteinander verbindet. Die Überführung der Daten in den digitalen Zwilling erlaubt Analysen und Simulationen, die die qualitätsoptimierende Steuerung des Produktionsprozesses in Echtzeit erlaubt.
In der Forschungsfertigung
Das wichtigste Ziel, den digitalen Zwilling im Rahmen der Forschungsfertigung einzuführen, waren Qualitätsverbesserungen. Dazu wurden im Projekt allein für die Elektrodenfertigung 118 qualitätskritische Parameter identifiziert – von der Partikelgröße der Eingangsmaterialien bis zum Gewicht der Elektroden am Ende ihrer Fertigung. Die Anforderungen an die Sensorik zur Erfassung vieler dieser Größen wurde ebenfalls abgeleitet. Die ermittelten Daten sind schließlich nach dem Vorbild des Aachener Internet of Production zu verarbeiten, zu transferieren und zu speichern. Der Fokus bei der Entwicklung des digitalen Zwillings galt der Entwicklung eines Traceability-Systems, das die zellgenaue Zuordnung der erfassten Daten von der Elektrodenfertigung bis zur Formierung sicherstellt und somit die Analyse und Informationsgenerierung prozessübergreifend für jede Zelle ermöglicht. Hierfür ist eine Codierung der Elektroden mittels Laser oder Tintenstrahl geplant, wodurch jeder Zelle eine eindeutige ID zugewiesen werden soll. Schließlich wurden auf Basis des generierten Wissens Anwendungsfälle für den digitalen Zwilling abgeleitet und den Stufen der Datenanalyse – deskriptiv, diagnostisch, prädiktiv, präskriptiv – zugeordnet. Die adaptive Prozesssteuerung im Rahmen der prädiktiven Analytik ist hierfür am Beispiel des Kalanderspaltes – des Abstandes der zwei Kalanderwalzen, zwischen denen die Elektroden verdichtet werden – dargestellt.