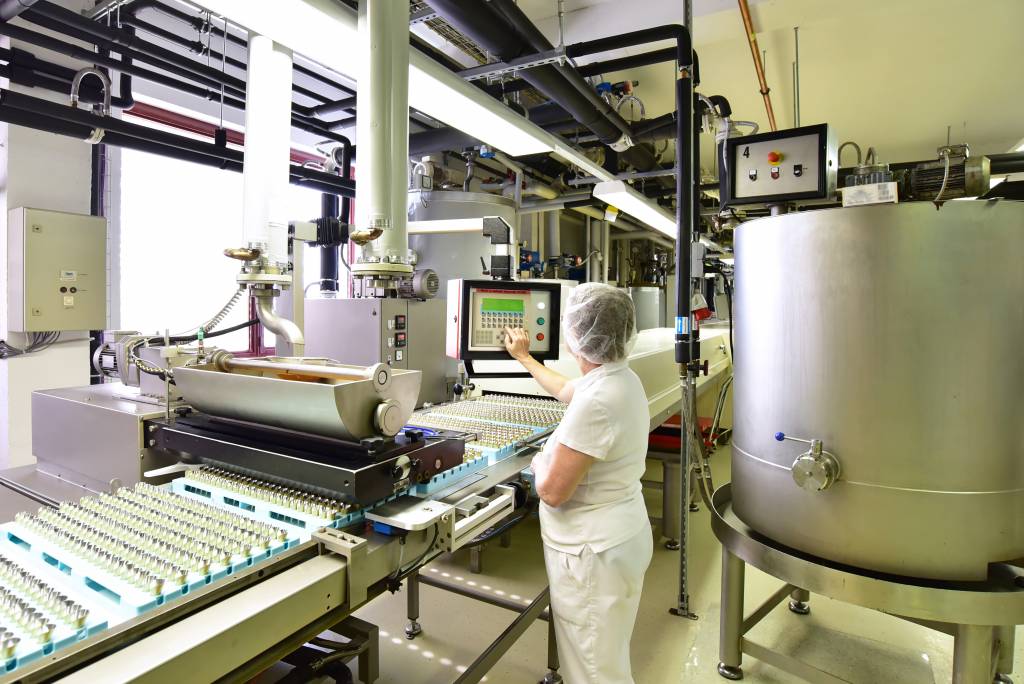
In puncto IT-Vernetzung wird der Brownfield-Bereich häufig vernachlässigt oder nur ungern angerührt. Gründe hierfür sind die Komplexität und schwierigen Rahmenbedingungen, die es zu beachten gilt. Gerade aber in der Lebensmittelindustrie kann sich ein Anlagenretrofit lohnen. Stellen doch Maschinen und Anlagen Investitionsgüter dar, die sich durch Zuverlässigkeit und Langlebigkeit auszeichnen. Beispiele sind Molkerei-Abfüllanlagen oder Verpackungslinien inklusive Waagen, die über Jahrzehnte genutzt werden. Steuerungstechnisch entsprechen sie damit aber meist nicht den aktuellen Standards. Die Ertüchtigung dieser Anlagen für die Integration in übergeordnete Produktionsnetzwerke und Anbindung an ERP- und MES-Programme stellt zwar durchaus eine Herausforderung dar, ist jedoch mittlerweile meist mit vertretbaren Kosten und Aufwand realisierbar. Zumal die Vorteile eines höheren Automatisierungsgrads den Aufwand schnell aufwiegen können: Kurze Produktionszyklen und häufige Produktwechsel beispielsweise bei Lohnverpackern in der Lebensmittelbranche erfordern häufige Konfigurationswechsel der einzelnen Maschinen in den Verpackungslinien. Die einzelne Umrüstung, teils mit manueller Parametereingabe, ist zeitaufwändig und fehlerträchtig. Moderne Steuerungssysteme können viele anfallenden Arbeiten deutlich beschleunigen.
Schlankes Retrofit
Bei der Anbindung von Produktionsanlagen an übergeordnete Anlagen sind mehrere Disziplinen beteiligt: Im ersten Schritt muss spezifisches Prozess- und Anlagenwissen, welches unter Umständen nur bei wenigen Personen im Unternehmen vorhanden oder schlecht dokumentiert ist, mit Knowhow über zukunftsfähige Integrationsszenarien kombiniert werden. Einige Integrations- und Schnittstellen-Lösungen auf dem Markt ermöglichen es, Anlagen sogar ohne viel IT- und Schnittstellenwissen anzubinden. Über vorgefertigte Adapter und Schnittstellen sowie grafische Regeleditoren lassen sich Integrationsszenarien mit Fokus auf den Prozess modellieren. Häufig soll die Anbindung der bestehenden Anlagen vor allem möglichst schnell und kostengünstig erfolgen. Stillstände und oder Hardwareaufrüstungen sollen vermieden werden.
Die Klassiker Rüstzeiten und Qualität
Teil der Vision einer Industrie 4.0 sind Plug&Play-Installationen von Industrieanlagen, wie Menschen sie bei USB-Sticks oder Druckern gewohnt sind. Aktuelle Ansätze setzen etwa auf maschinenspezifische Kommunikationsadapter, die auf der einen Seite die proprietären Schnittstellen von Maschinen und Anlagen unterstützen und auf der anderen Seite Kommunikationsstandards wie OPC UA, Datenbanken oder XML mitbringen. Auf einer Datenbank-gestützten Zwischenebene lassen sich produktionsnahe und maschinenspezifische Daten speichern, sofern erforderlich und diese Daten nicht in übergeordneten ERP-Systemen oder MES bleiben sollen. Über solche bidirektionalen Schnittstellen lassen sich die vielfältigen Informationen aus den Maschinen und Anlagen auslesen und für Auswertungen oder Verbesserungen nutzen. Zum anderen können Maschinen- und Anlagenparameter aus übergeordneten Systemen heruntergeladen und Rückgabewerte zurückgeladen werden. Das hilft Anwenderunternehmen, etwa Rüstzeiten zu reduzieren oder die Qualität zu verbessern, weil weniger handschriftliche Datenübergaben anfallen. Auch die automatisierte Einführung neuer Produkte, gerade bei einer variantenreichen Produktion, aus dem ERP-System in die Produktionsanlagen wird meist deutlich einfacher.
Systeme kommunizieren
Sind mehrere komplexe Anwendungen wie Planungslösungen und ME-Systeme beteiligt, die mit unterschiedlichen Kommunikationsstandards arbeiten, kann ein Broker (Vermittler)-Ansatz auf der Zwischenebene Daten etwa unter OPC UA vereinheitlichen. Dabei übersetzt der Broker nicht nur, sondern sorgt auch für den Ablauf der Workflows, um Daten und Funktonsaufrufe zu transportieren.