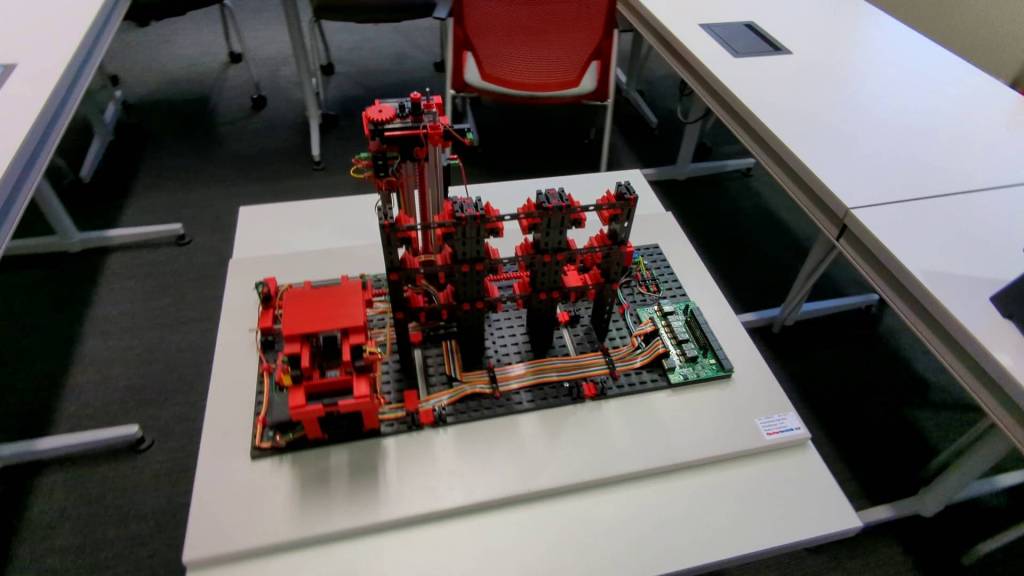
Ein digitales Abbild einer Industrieanlage entsteht meist in ihrer Planungsphase. Die Modelle können danach etwa für eine virtuelle Inbetriebnahme genutzt werden. Dabei werden das Steuerungssystem, bzw. die Abläufe mit einer Computersimulation getestet und optimiert, noch bevor die Anlage physisch vorhanden ist. Entwickler können dadurch potenzielle Probleme frühzeitig identifizieren, Abläufe anpassen und Fehler minimieren. Das verwendete Anlagenmodell während der virtuellen Inbetriebnahme umfasst alle relevanten Komponenten, Maschinen, Steuerungssysteme und Prozesse.
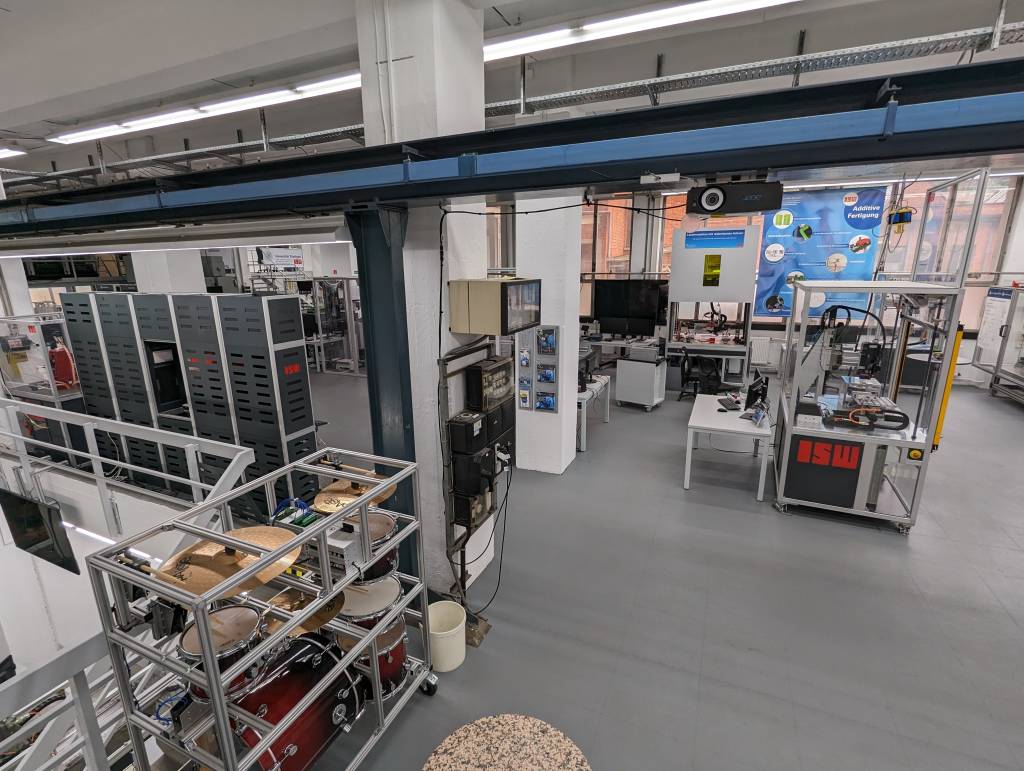
Und nach der Inbetriebnahme?
Aber auch nach der Inbetriebnahme soll das aufwändig entwickelte Modell weiterverwendet werden. Der Digitale Zwilling bildet eine fortlaufende digitale Repräsentation der physischen Industrieanlage über ihren gesamten Lebenszyklus hinweg. Er bildet die reale Anlage betriebsbegleitend ab, indem er kontinuierlich Daten aus Sensoren und anderen Quellen sammelt. Diese Daten werden dann genutzt, um den Zustand, die Leistung und die Effizienz der Anlage zu überwachen. Ein Problem des Digitalen Zwillings ist jedoch eine zunehmende konstruktive Abweichung zu der physischen Anlage. So müssen nachträgliche Umbauten an oder Umpositionierungen von Maschinen auch am Digitalen Zwilling modelliert werden. Dies erfordert zusätzlichen Personalaufwand. Werden die digitalen Modelle von externen Dienstleistern entwickelt, müssen diese erneut beauftragt werden.
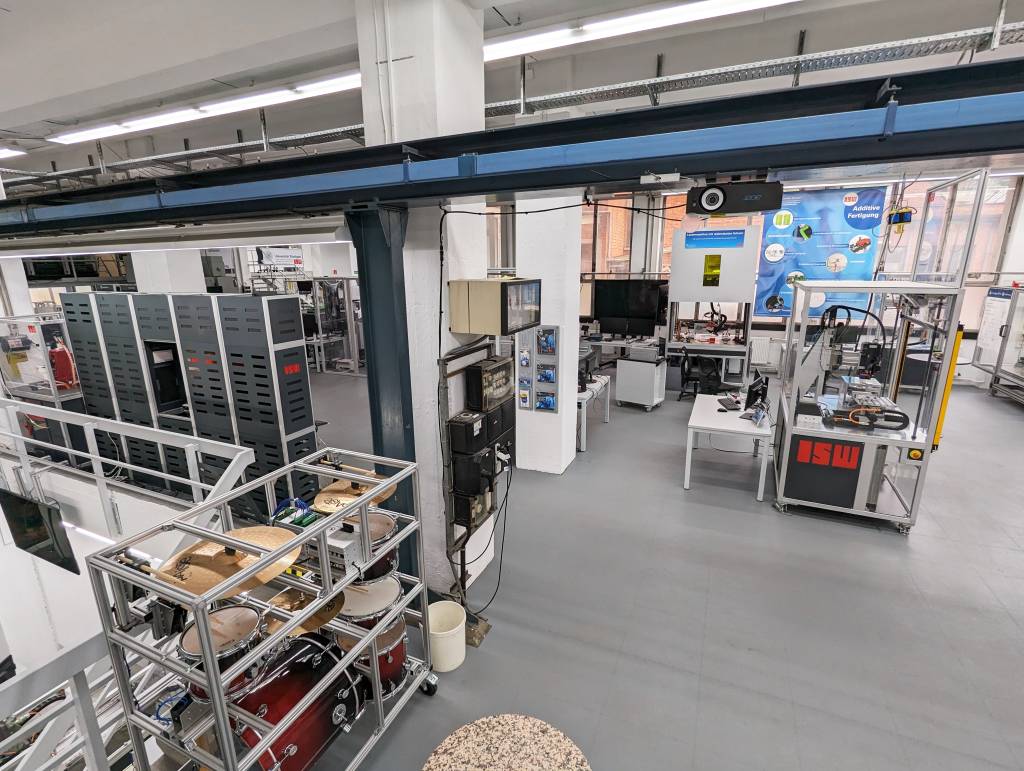
Den Zwilling anpassen
Welche Möglichkeiten gibt es also, konstruktive Anpassungen an der realen Anlage schnell und ohne großes Fachwissen in den Digitalen Zwilling zu überführen? Eine Möglichkeit ist die Rekonstruktion des Shopfloors mit Hilfe von Laserscannern oder Lidar-Sensorik. Nachteile dieser Verfahren sind jedoch die hohen Kosten für die Anschaffung der Hardware oder die Beauftragung eines Dienstleisters. Letzteres ist insbesondere dann unwirtschaftlich, wenn Veränderungen innerhalb der Anlage zum Tagesgeschäft gehören. Als neue und kostengünstigere Alternative bietet sich das Verfahren der Neural Radiance Fields (NeRF) an. Dabei wird zur Digitalisierung von Objekten eine Anzahl an Kamerabildern aus verschiedenen Blickwinkeln verwendet. Das Ergebnis wird mittels Deep Learning optimiert, wodurch Unsicherheiten kompensiert werden sollen, die durch unvollständige Eingangsdaten – beispielsweise zeigen die verwendeten Einzelbilder das Objekt nicht aus allen Blickwinkeln – entstehen. Die Erzeugung des digitalen Modells lässt sich in drei Phasen aufteilen: Zunächst werden die Einzelbilder eines Videos der Maschine aus mehreren Blickwinkeln verwendet (1), um diese digital zu rekonstruieren (2). Schließlich werden die Oberflächen der Rekonstruktion algorithmisch identifiziert wodurch ein dreidimensionaler Körper entsteht, der die Maschine nachbildet (3).
Wo liegen die Grenzen?
Durch das NeRF-Verfahren können konstruktive Änderungen an der Anlage erfasst werden. Das Ergebnis unterliegt derzeit jedoch noch einigen Beschränkungen: Ist das digitalisierte Objekt in der Realität beispielsweise in Bewegung, muss dieses Verhalten auch auf den Digitalen Zwilling übertragen werden. Mittels NeRF lässt sich nur eine rein visuelle Darstellung digitalisieren. Soll der Ablauf der veränderten Anlage also erneut durch eine virtuelle Inbetriebnahme getestet werden und integrieren sich die angepassten Anlagenbestandteile nicht rein statisch, muss manuell nachgearbeitet werden. Hierzu forscht das Institut für Steuerungstechnik der Universität Stuttgart an den Möglichkeiten und Grenzen, einfaches Verhalten, wie Bewegungen oder Rotationen, von Anlagenkomponenten aufzuzeichnen und in den Digitalen Zwilling zu integrieren. Unternehmen, für die diese Forschung einen konkreten Anwendungsfall darstellt, können mit dem ISW in Kontakt treten. n ist Wissenschaftlicher Mitarbeiter für Virtuelle Methoden in der Produktionstechnik am Institut für Steuerungstechnik der Werkzeugmaschinen und Fertigungseinrichtungen (ISW) der Universität Stuttgart.