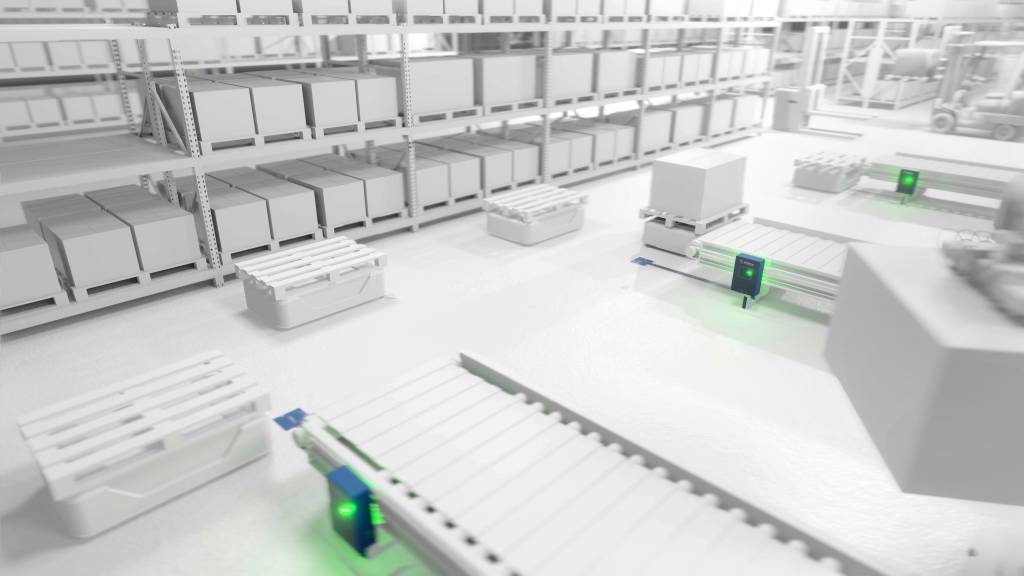
Die Bedeutung von automatisierten Transportsystemen für industrielle Prozesse steigt. Diese Aussage teilen 80 Prozent der Befragten einer Studie zur Transformation der Energieversorgung von Flurförderzeugen (FFZ) und Automated Guided Vehicles (AGV) in der Logistik. Die Studie wirft einen Blick auf die eingesetzten Fahrzeuge in der Logistik, Produktion und Montage sowie deren Energieversorgung. Sie wurde von der Logistik- und Organisationsberatung Prolog-Team in Zusammenarbeit mit der Hochschule für Wirtschaft und Gesellschaft Ludwigshafen sowie Wiferion durchgeführt. 50 überwiegend große und mittelständische Unternehmen aus der Industrie, dem Handel und dem Dienstleistungssektor gaben Auskunft zu den eingesetzten Elektrofahrzeugen, Batterien und Ladeprozessen.
Lithium-Ionen-Batterie ist etabliert
Ob fahrerloses Transportsystem (FTS) oder autonomer mobiler Roboter (AMR) – der Automatisierungsgrad der intralogistischen Prozesse ist bereits auf einem beachtlichen Niveau. So sind zwar bei den elektrisch angetriebenen Fahrzeugen derzeit noch überwiegend Gabelstapler (87,5 Prozent) und Handhubwagen (85,5 Prozent) im Einsatz, aber auch bereits FTS und AGV mit 29,2 Prozent und AMR mit 12,5 Prozent. Die eingesetzten Fahrzeuge werden zu 50 Prozent mit Lithium-Ionen-Batterien betrieben und zu 43,8 Prozent mit Blei-Säure-Batterien. Der relativ hohe Anteil an Blei-Säure-Batterien liegt dabei möglicherweise in noch bestehenden Kontrakten begründet. Denn die Vorteile der leistungsstarken Lithium-Ionen-Batterie liegen auf der Hand: längere Lebensdauer, ein niedriger Wartungsaufwand, geringes Gewicht und reduzierte Betriebskosten sowie die Möglichkeit zur Zwischenladung. Daher ist auch nachzuvollziehen, dass über die Hälfte der Befragten künftig eine Umrüstung oder Neuanschaffung mit Lithium-Ionen-Batterien plant.
Nicht nur die Investitionskosten betrachten
Doch nicht alle Unternehmen setzen sich mit der Energieversorgung ihrer eingesetzten Systeme auseinander. Die Studie führte zu dem überraschenden Ergebnis, dass ein Drittel der Befragten keine Angaben zu den verwendeten Batterien machen konnte. Hier besteht scheinbar ein großer Aufklärungsbedarf. Um die Total Cost of Ownership (TCO) ihrer FTS und AMR im Blick zu behalten, sollten Unternehmen nicht allein die Technologie und deren Investition in den Vordergrund stellen. Es gilt, eine umfassende Bewertung der Wirtschaftlichkeit durch die Ermittlung der gesamten Kosten vorzunehmen. Demnach muss der gesamte Aufwand betrachtet werden, verursacht durch Auswahl, Beschaffung, Kauf, Installation, Betrieb, Nutzung und Wartung, Schulung und Reparatur, Entsorgung und Rückgabe. Vor diesem Hintergrund überzeugt die Lithium-Ionen-Batterie aufgrund ihrer zahlreichen Vorteile. Trotz anfänglich höherer Investitionskosten erzielen Unternehmen durch den Einsatz der zukunftsorientierten Technologie einen deutlich höheren Return on Investment (ROI).
Ladeprozesse sind häufig ineffizient
Die Studie zeigt: FTS und FFZ werden meist erst nach Schichtende geladen, manchmal auch in den Pausen oder sogar erst dann, wenn die Energie aufgebraucht ist. Das Problem: Ist keine Energie für nachgelagerte Arbeiten vorhanden, müssen ungeplante Ladepausen eingelegt werden. Das führt zu Unterbrechungen im Workflow und ist nicht effizient. Auch ein Laden nach Schichtende kann zu Problemen führen, wenn beispielsweise in Mehrschichtbetrieben nicht ausreichend geladene Fahrzeuge für die nächste Schicht zur Verfügung stehen. Dabei arbeiten die meisten Unternehmen in der Logistik in mehr als zwei Schichten. Es lohnt sich also, einen Blick auf den Ladeprozess zu werfen. Denn fehlerhafte Ladevorgänge, Stromausfall und Spannungsspitzen beim Laden können die Versorgungssicherheit erheblich gefährden und zu Produktionsausfällen führen. Im Arbeitsalltag wird häufig vergessen, das Fahrzeug anzuschließen und zu laden. So dauern die Ladeprozesse bei einem Drittel der Befragten mindestens 60 Minuten. Ein weiteres Drittel der Befragten kann keine Angaben zur Dauer des Ladevorgangs machen und hat sich scheinbar noch nie intensiver mit dem Ladevorgang beschäftigt. Dabei sind Lithium-Ionen-Batterien für häufiges Zwischenladen ausgelegt und besitzen die Fähigkeit, in kurzer Zeit hohe Ströme aufzunehmen. Doch dieses Potenzial kann mit der herkömmlichen Ladetechnik nicht ausgeschöpft werden. So verpasst ein Großteil der Unternehmen die Gelegenheit, die eigene Produktivität durch die Optimierung der Ladevorgänge zu steigern. Dabei gilt: Je höher dabei die Anzahl der eingesetzten Fahrzeuge ist, desto mehr Beachtung sollte der Ladeprozess bekommen.