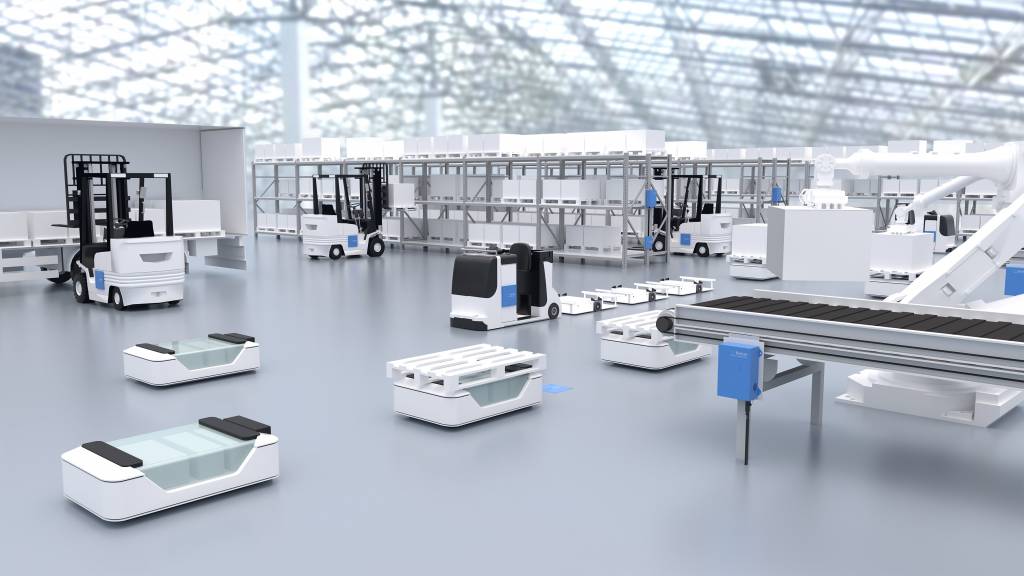
Die Lithium-Ionen-Technologie hat sich vor allem im Bereich der fahrerlosen Transportsysteme und mobilen Roboter längst durchgesetzt. Für die Aufladung der leistungsstarken Batterien stehen verschiedene Systeme und Konzepte zur Verfügung, die sich hinsichtlich Wirtschaftlichkeit, Wartungsaufwand, Flexibilität sowie Arbeitsschutz unterscheiden. Dabei ist die Sicherheit für Mitarbeiter sowie der verschleißfreie Betrieb im optimalen Arbeitspunkt unbedingt zu gewährleisten, um das volle Potential auszuschöpfen.
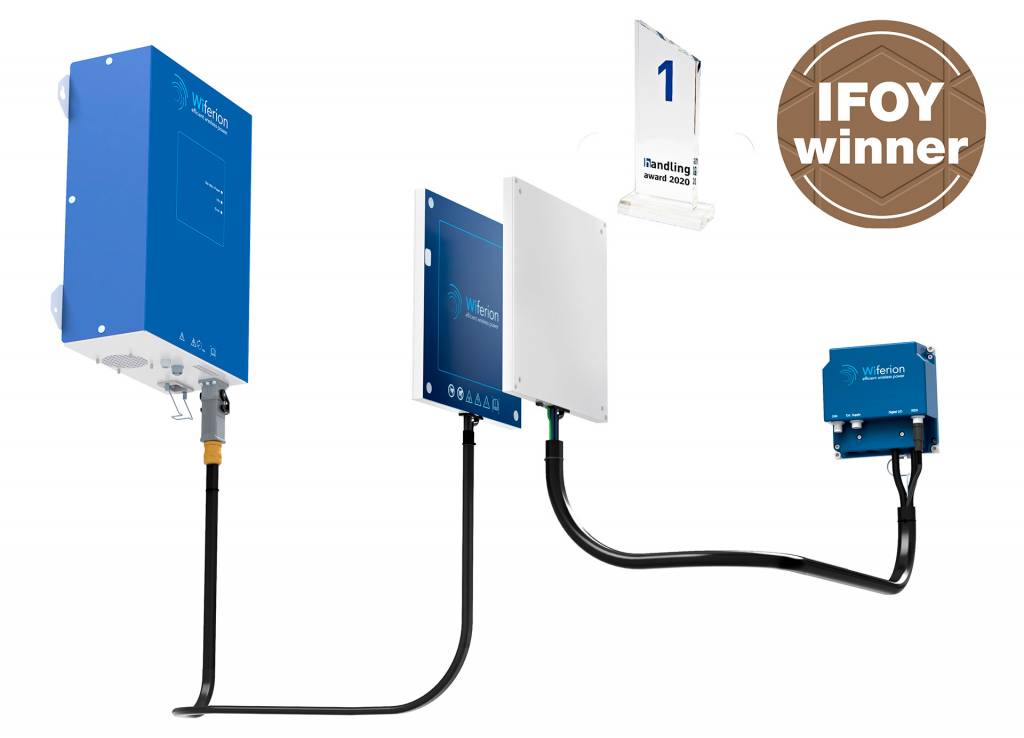
Ladekabel und offene Kontakte – nicht ohne Stolpergefahr und Sicherheitsrisiko
Bei Flurförderzeugen (FFZ) erfolgt die Aufladung der Batterie häufig über kabelgebundene Steckverbindungen. Mitarbeiter schließen die Fahrzeuge in längeren Pausen oder nach Schichtende an das Ladegerät an. Dabei stellen die Kabel ein Sicherheitsrisiko dar, da Mitarbeiter darüber stolpern und stürzen können. Bei unsachgemäßem Gebrauch entstehen Gewaltschäden und weitere Sicherheitsprobleme wie abgebrochene Pins und abgerissene Kabelenden. Aus Gründen des Arbeitsschutzes befinden sich die Ladepunkte häufig nicht in unmittelbarer Nähe der Produktionsbereiche, sondern weiter entfernt in extra dafür eingerichteten Ladezonen, manchmal sogar außerhalb der Produktionshalle. Zum Laden müssen die Fahrzeuge in diese Zonen fahren und fehlen dann im Produktionsprozess.
Auch über Schleifverbindungen lassen sich Batterien aufladen. Gerade bei FTS oder automatisierten FTF kommt diese Lösung zum Einsatz. Bei dieser Lösung führen die Schaltrelais immer wieder zu Problemen, beispielsweise bei einer nicht korrekten Ansteuerung oder einem Verkleben der Kontakte. Funktioniert das System nicht korrekt, kann es nach der Beendigung des Ladeprozesses zu Funkenbildung kommen. Wie der Kontaktvorgang aufgebaut wird, ist entscheidet darüber, ob Oxidschichten vor dem Laden entfernt werden und Einbrandstellen vermieden werden können. In Produktionslinien sind auf dem Boden montierte Ladekontakte zudem hinderlich und eine Stolpergefahr für die Mitarbeiter.
Induktive Leitlinien – permanent aktiv
Bei diesem System bewegen sich die Fahrzeuge auf vorgegebenen Fahrwegen mit integrierten Stromleitern. Bei der Installation ist eine genaue Analyse der Infrastruktur vor Ort notwendig, um etwaige Wechselwirkungen mit Bodenarmierungen durch die Magnetfelder um die Leitung auszuschließen. Ansonsten entstehen beträchtliche Verluste in der Armierung und der Boden erwärmt sich. Eine Kommunikation zwischen Leitung und Fahrzeugkomponenten ist systembedingt nicht möglich, wodurch die Leitungsströme zu jedem Zeitpunkt aufrechterhalten werden müssen und die Effizienz limitieren.
Auch ein kompletter Batterietausch birgt Gefahren
Beim Batteriewechsel werden die mehrere hundert Kilo schwere Batterien aus den Fahrzeugen entnommen und einem speziellen Batterieraum geladen. Ein Prozess mit hohen Verletzungsrisiken. Bei Blei-Säure-Batterien sind zusätzliche Vorkehrungen zum Schutz vor der Säure notwendig. Beim Wechsel selbst können leicht Quetschwunden entstehen. Die Entstehung von Knallgas und Schwefelsäure ist ein zusätzliches Sicherheitsrisiko während des Ladeprozesses. Auch beim Nachfüllen von Wasser und Säure können sich die Mitarbeiter verletzen.