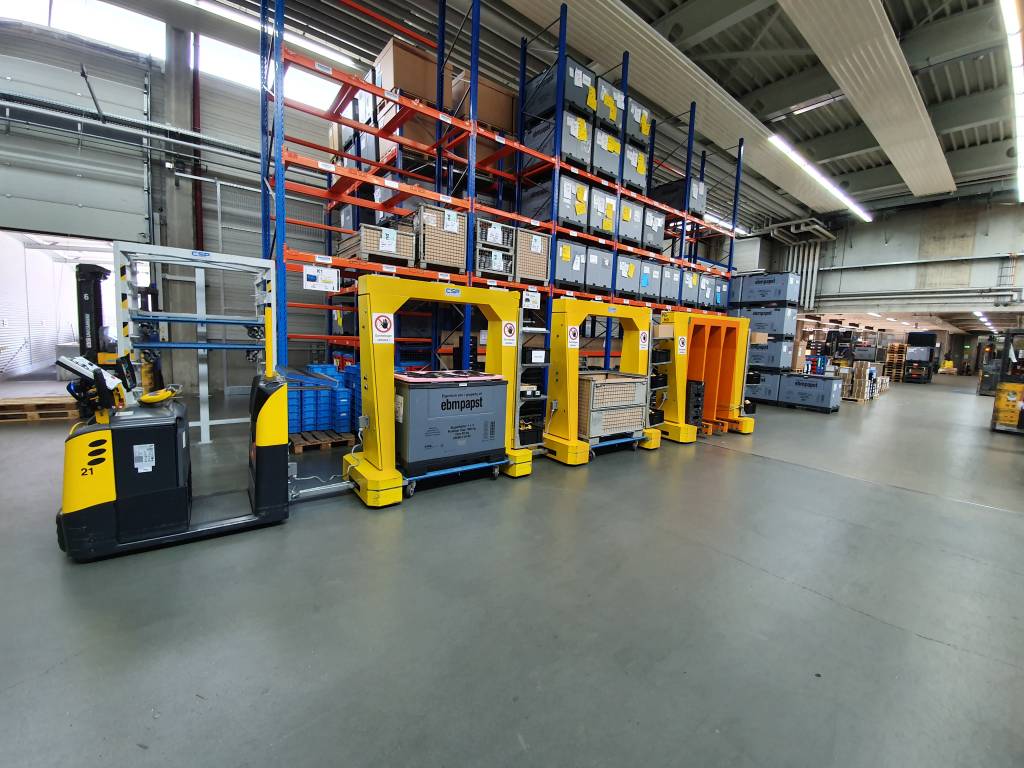
Ventilatoren und Motoren von EBM-Papst sind fast überall auf der Welt zu finden: in Backöfen und Dunstabzugshauben, in Pkws, Bussen und Traktoren, in Klima- und Lüftungsanlagen von Gebäuden und Rechenzentren, in Kühlhäusern oder in der Medizin- und Heiztechnik. Das Unternehmen beschäftigt weltweit knapp 15.000 Mitarbeiter und unterhält 29 Produktionsstandorte.
„Wir haben sehr viele verschiedene Transportboxen und rund 20 verschiedene Ladungsträger, weil unsere Produkte so unterschiedlich sind“, erklärt Ottmar Rupp. Er ist bei EBM-Papst zuständig für Projekte und Routenzüge. „Unser kleinster Ventilator misst etwa 5cm im Durchmesser, der größte rund 1,8m. Das ist eine echte Herausforderung für die Verpackung und den Transport innerhalb der Produktionsstätten.“
Als Ottmar Rupp vor Jahren begann nach Lösungen zu suchen, wie sich die Intralogistik in den Werken von EBM-Papst elegant verschlanken lassen könnte, war genau das einer der Knackpunkte – die Unterschiedlichkeit der Produkte und damit der Transportmittel.
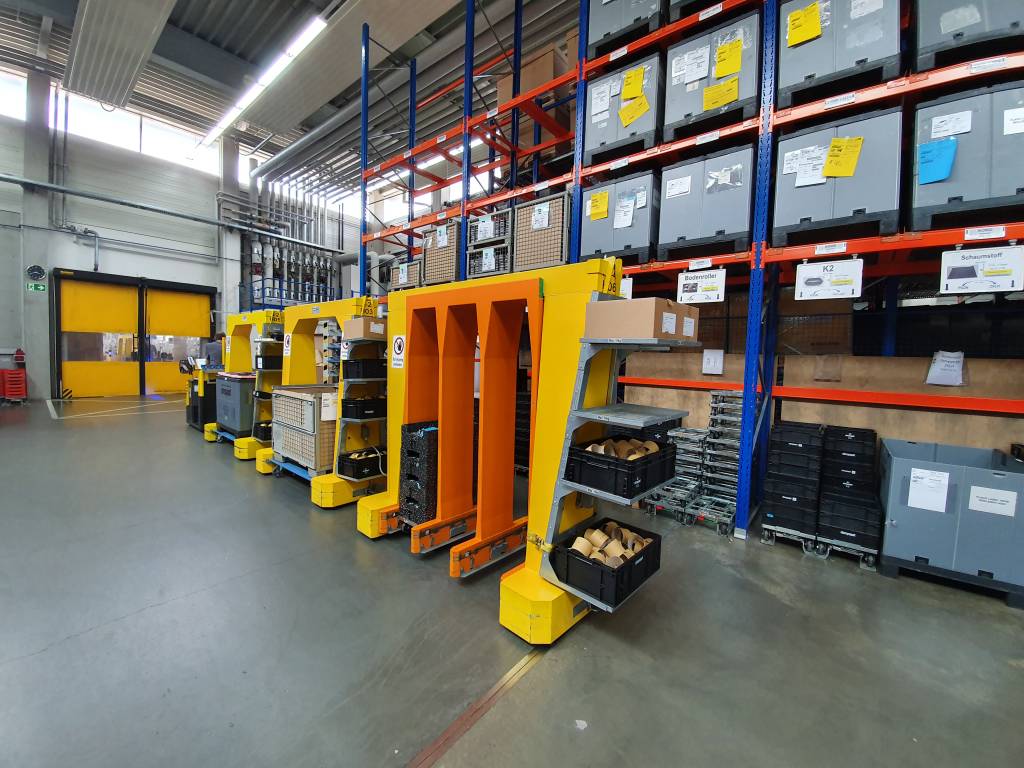
Das Ziel: gabelfreier Transport und zyklische Materialversorgung
„Unser Ziel war es vor allem, künftig ohne Stapler auszukommen.“ Das würde das Verkehrsaufkommen und die Geräuschkulisse in den Produktionsstätten senken, die Sicherheit und Flexibilität erhöhen und Kosten einsparen, so der Logistiker. „Gabelstapler bringen das Material in der Regel auf Europaletten an die Fertigungslinien. Diese Paletten stehen dann meist viele Stunden im Weg, bis sie abgearbeitet sind. Das kostet Platz, ist unpraktisch und provoziert Unfälle.“ Hinzu kommt: Ein Stapler fährt nach dem Abliefern seiner Ladung fast immer leer wieder zurück ins Lager.
Zudem ist in den letzten Jahren die Varianz in den Produkten immer weiter gestiegen, was zwangsläufig zu kleineren Losgrößen in der Produktion führte. Parallel dazu wurde die Materialsteuerung vom jahrelang praktizierten Push auf Pull umgestellt. Die Endmontageeinrichtungen ‚ziehen‘ das auftragsbezogen vorkommissionierte Material aus den Groß- und Supermärkten, das sie für die Abarbeitung der Kundenaufträge benötigen.
Die Herausforderung, die sich daraus für die Materialversorgung stellte, war alle Verbrauchsstellen in der Produktion kurzzyklisch zuverlässig – ‚öfter mit kleineren Mengen‘ zu versorgen. Gleichzeitig sollten das Leergut und die Fertigpackstücke herausgefahren werden.
Routenzüge, so die Überlegung, sind dafür das geeignete Transportmittel. Allerdings: Das Unterfangen erwies sich als ausgesprochen schwierig, so Ottmar Rupp. „Für uns kamen nur Routenzüge in Frage, die problemlos unsere sehr unterschiedlichen Ladungsträger aufnehmen konnten. Es macht schließlich keinen Sinn, mit verschiedenen Routenzugsystemen zu arbeiten. Aber wir haben rund acht Jahre lang den Markt analysiert und Routenzüge getestet.“
Bevorzugter Ausrüster
Bis der Logistiker auf einer Messe mit CSP in Kontakt kam. Das metallverarbeitende Unternehmen mit Sitz in Pfronstetten auf der Schwäbischen Alb ist seit Jahren bevorzugter Ausrüster vieler produzierender Unternehmen, unter anderem in der Automotive-Branche. Das Team um die Geschäftsführer Katrin und Harald Späth ist in der Branche vor allem bekannt für zuverlässig arbeitende, robuste Sondermaschinen und Anlagen für die innerbetriebliche Logistik.
Die ersten Gespräche zwischen Ottmar Rupp und den Verantwortlichen bei CSP verliefen vielversprechend. CSP hat uns zum Beispiel gleich zu Beginn einen ihrer Routenzüge mehrere Wochen lang zum Testen überlassen. Das hat uns in unserer Entscheidungsfindung sehr weitergeholfen.“
Also schickte EBM-Papst Muster von allen seinen Bodenrollern nach Pfronstetten. Und die Entwickler bei CSP lieferten einen Routenzug, der jeden geforderten Ladungsträger aufnehmen konnte. „Natürlich gab und gibt es immer Dinge, die noch zu verbessern und zu korrigieren sind“, so Ottmar Rupp, „aber unterm Strich hat die Lösung von CSP gepasst.“
Routenzüge ersetzen Stapler
Heute sind bereits fünf Produktionsstandorte von EBM-Papst weitgehend staplerfrei. Den Transport der Bauteile vom Lager an die Fertigungslinie übernehmen Routenzüge von CSP mit bis zu fünf Hängern. „Die fahren mit den Bauteilen an die Fertigung und entweder mit Endprodukten in Kartons oder mit Leergut zurück ins Lager. Damit haben wir kaum noch Leerfahrten.“