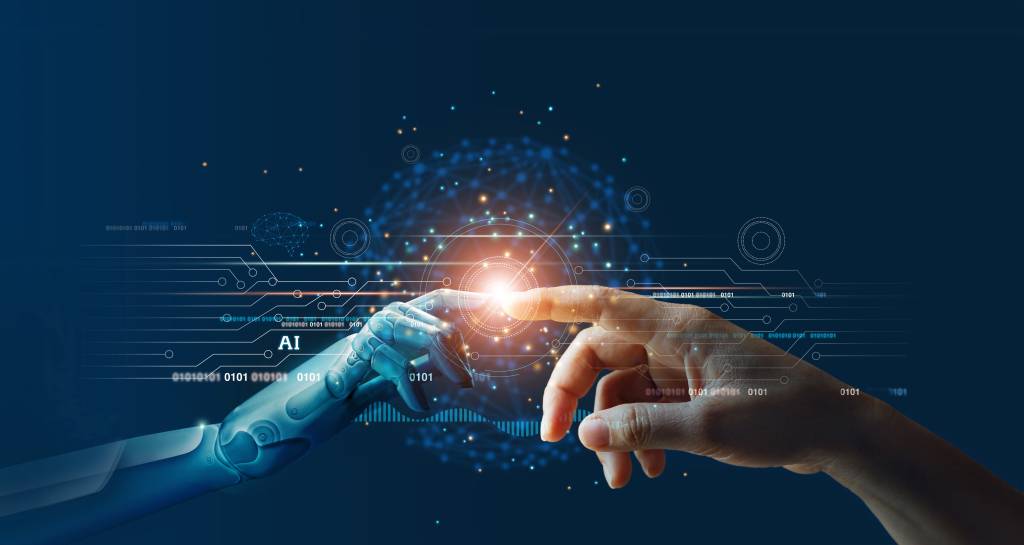
Neben einer besseren Konnektivität von Geräten auf Anlagenebene ermöglichen es digitale Tools, Daten an andere Systeme weiterzuleiten und Maschinen aus der Ferne, tiefergehender, über größere Entfernungen und längere Zeiträume zu überwachen, als es in der Vergangenheit möglich war. Ein Beispiel: Die meisten Unternehmen haben Rückverfolgbarkeit in der Fertigung traditionell über papierbasierte Chargenprotokollierungen realisiert. Rückverfolgbarkeit auf Produktebene ist ohne digitale Unterstützung kaum vorstellbar Predictive Maintenance, also vorausschauende Wartung, wäre theoretisch zwar möglich, allerdings nur, wenn Geräte periodisch überwacht würden. Die Digitalisierung bietet Firmen zweifelsohne hilfreiche Funktionen, die sich Daten zunutze machen, die in den meisten Produktionslinien zwar bereits vorhanden sind, allerdings in unterschiedlichen Systemen vorliegen und konventionell nicht miteinander in Verbindung gesetzt werden konnten. Im einfachen Sinn ist digitalisierte Produktion die Integration von bestehenden Systemen und Maschinen, um so Informationen zu gewinnen, die bei der Behebung von Problemen helfen. Zugleich lassen sich über die Datenvisualisierung deutlich bessere Einblicke in die Produktivität und Effizienz der gesamten Wertschöpfung gewinnen.
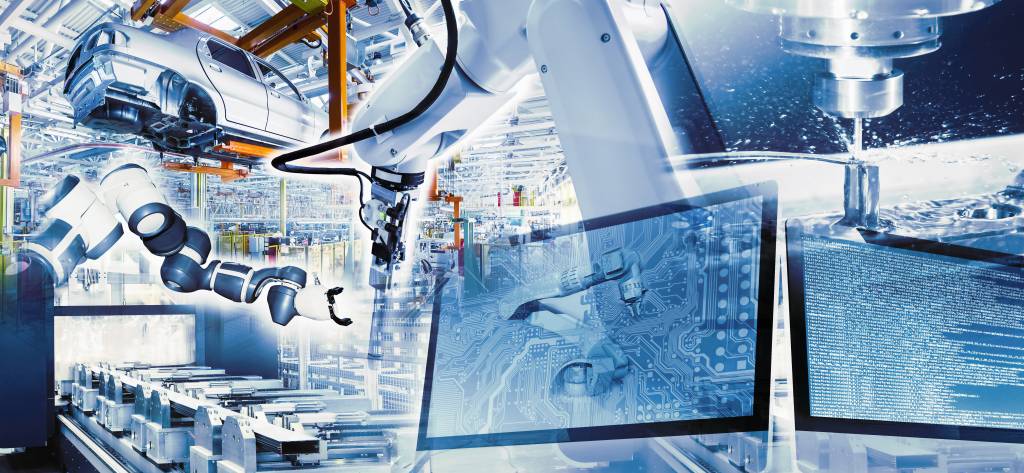
Barrieren überwinden
Das größte Hindernis bei der Einführung digitaler Technologien besteht häufig darin, dass die Betriebstechnik (OT) oft vorrangig auf Maschinenoptimierung ausgerichtet war und daher Architekturen und Netzwerke verwendet wurden, die zuerst der Maschinenleistung dienen. Um die IT- und OT-Welt miteinander zu verschmelzen, muss die Integrationsfähigkeit der OT-Ebene weiterentwickelt werden. Neuere Maschinensteuerungslösungen bingen solche IT-Funktionalität bereits meistens mit. Die Sysmac-Steuerung von Omron verfügt etwa über eine SQL-Datenbankanbindung und ist außerdem mit OPC-UA- sowie MQTT-Option erhältlich. Dies vereinfacht die Weitergabe der Betriebsinformationen von der Maschinenebene an die IT-Umgebung und umgekehrt deutlich. Inzwischen gibt es auch Middleware-Lösungen, die als Gateway Alt-Geräte mit der IT-Welt verbinden.
Tipps für das Datenhandling
On-Premise-Server können eine gute Lösung darstellen, wenn es um schnelle Datenzugriffe geht. Die Krux: Ist eine Verbindung der OT-Umgebung mit anderen Anwendungen geplant, müssen Fragen der IT-Sicherheit berücksichtigt werden. Sollten die Daten nur auf dem On-Premise-IT-Server analysiert und gespeichert werden, dürfte die werksweite Firewall nebst Sicherheitsinfrastruktur ausreichen. Da aber jeder Verbindungspunkt ein potenzielles Sicherheitsrisiko darstellen kann, sollten weitere Vorsichtsmaßnahmen erwogen werden. Omron verwendet daher vertrauenswürdige Zertifikate (Trusted Certificates) für OT-Geräte, die so IT-Server eindeutig identifiziert werden.
In der Cloud skalieren
On-Premise-Servern können nicht unendlich viele Daten speichern. Muss eine Anwendung große Datenmengen verarbeiten, ist die Verwendung eines Cloud-basierten Servers oft die bessere Lösung, auch wenn das noch strengere Sicherheitsvorkehrungen erfordert. Die Cloud bietet skalierbare Datenspeicherung, die quasi unbegrenzt ist und keine Änderungen der Architektur erfordert, wenn sich der Speicherbedarf ändert. Der Nachteil von Cloud-basierten Servern: Sie ermöglichen keine Echtzeit-Verbindung im Sinne eines diskreten Produktionsumfeldes. Es wird daher immer eine gewisse Latenzzeit geben, wenn es um die Verarbeitung und Reaktion auf Informationen geht. Als Datenspeicherplattform eignen sich verschiedene Lösungen für unterschiedliche Anwendungsszenarien. Aufgaben wie die Produktionsvisualisierung sind beispielsweise gut bei On-Premise-Servern aufgehoben, da geringere Mengen an Daten gespeichert werden müssen und weniger Datenverarbeitung erforderlich ist. Für Predictive Maintenance sind wiederum große Datenmengen und eine hohe Rechenleistung erforderlich. Daher bietet sich hier die Cloud an, um diese Informationen zu verarbeiten und aussagekräftige Ergebnisse zu erhalten. Rückverfolgbarkeit in der Fertigung eignet sich ebenfalls für die Cloud, da hier große Mengen an Datensätzen gespeichert werden müssen. Und auch Projekte zur Verbesserung der Produktqualität finden in der Cloud einen guten Platz, da ein Echtzeit-Zugriff nicht zwingend erforderlich ist.