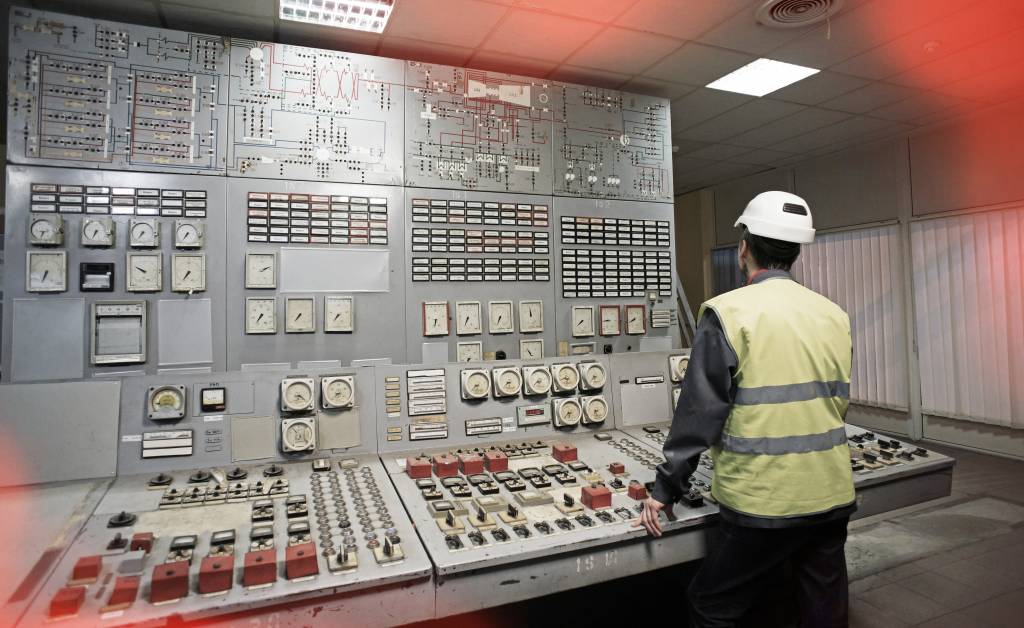
Die Vernetzung aller Gegenstände und Systeme sowie deren Ausstattung mit Intelligenz zur besseren Nutzung und Überwachung ist ein Grundgedanken der Smart Factory und wird von einem Großteil der Unternehmen bereits intensiv genutzt. Die nächsten Schritte zur weiteren Optimierung sind auch schon in der Realisierungsphase: Laut der Kapersky Lab-Studie ‚The State of Industrial Cybersecurity 2018‘ arbeiten heute 15 Prozent der Industrieunternehmen mit Scada-Steuerungssystemen, die an Cloud-Lösungen angeschlossen sind. Mit 5G sowie dem Industrial Internet of Things (IIoT) wird dieser Prozess noch einmal beschleunigt. Zunehmend ist auch der Einsatz mobiler Endgeräte in der Produktion auf dem Vormarsch. Im Regelfall werden diese heute lediglich für die Überwachung von Produktionsanlagen genutzt, doch zunehmend gestatten sie ebenso bedingte Eingriffsmöglichkeiten. So können Werks- oder Produktionsleiter nicht nur zu jeder Zeit von jedem Standort die Produktion überwachen, sondern sogar Einfluss auf Steuerungsparameter nehmen. Die Basis für diese Szenarien ist eine Vernetzung, sowohl intern als auch extern, teils bis hin zu den Herstellern von Maschinen oder Zulieferern.
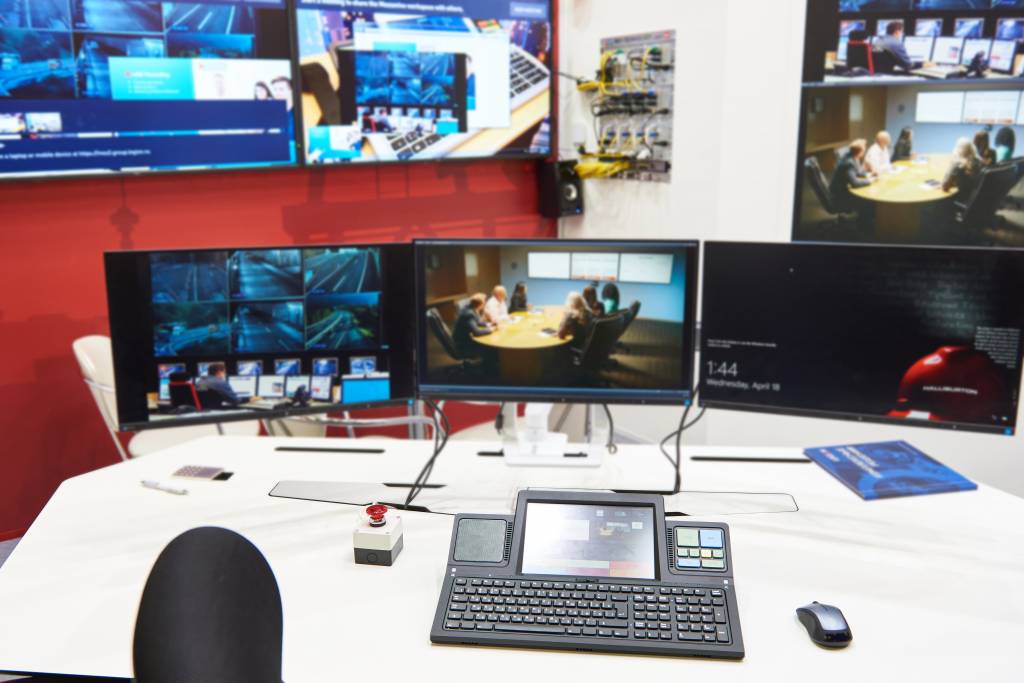
Offene Flanken
Die hochgradige Vernetzung bringt Vorteile für den Betriebsablauf und eröffnet die Möglichkeit zur Entwicklung neuer Fertigungs- und Geschäftsmodelle, wie etwa Predictive Maintenance, die erst auf Basis von Internettechnologien konzipiert werden konnten. Doch im Gegenzug entstehen dadurch neue Angriffspunkte. Die Bedrohung ergibt sich daraus, dass die eingesetzten Basistechnologien wie Websprachen, Kommunikationsprotokolle, Datenbanken oder Betriebssysteme der Internetwelt grundsätzlich als unsicher einzustufen sind und dies immer noch zu oft unterschätzt wird. Folglich finden diese Basistechnologien im Produktionsumfeld noch immer Verwendung und stoßen auf Produktionsnetze und -komponenten, die für solche Szenarien nie konzipiert waren. Mittlerweile haben sich Angreifer auch darauf spezialisiert, beständig und automatisiert nach Sicherheitslücken zu suchen, sobald Produktionsanlagen mit dem Internet – also in einem TCP/IP-Netz – verbunden sind. Aufgrund von unzureichenden Schutzmaßnahmen werden sie dabei häufig relativ schnell fündig. Dafür gibt es verschiedene Gründe: Der Datentransfer zwischen den Systemen der Produktion läuft häufig über offene Standards – zur Absicherung greifen hier jedoch die aus der IT bewährten Standardlösungen nur bedingt und sehr eingeschränkt. Zudem erfordert jede weitere Anbindung von Applikationen sowie Vernetzung von Geräten und Systemen neue Schnittstellen, die per se ein Risiko darstellen – denn hier werden ständig neue Schwachstellen entdeckt.
Getrennte Netze sicherer
Erhöht wird das Gefahrenpotential zusätzlich, wenn keine Trennung zwischen IT und OT besteht. Dann sind Angriffe wie der nachfolgend skizzierte möglich: Ein mit Administrationsrechten versehener Leitstand hatte uneingeschränkten Zugang zum Internet. Mit gravierenden Folgen. Innerhalb kürzester Zeit wurde er von einem seit langem bekannten Virus befallen, der in der IT mit einem Standard-Virenschutz keinerlei Schaden angerichtet hätte. Da in der OT jedoch kein entsprechendes Schutzprogramm einsetzbar war, verursachte der Schädling einen kompletten Produktionsstillstand – bei einem 24/7-Produktionszyklus. In diesem Fall dauerte die Zwangspause sieben Tage. Daraus resultierte ein täglicher Verlust von rund 200.000 Euro sowie Pönalen aufgrund vertraglich fixierter Lieferzusagen, die nicht eingehalten werden konnten. Im Allgemeinen werden Angriffe jedoch mittlerweile eher langfristig geplant und gezielt durchgeführt. Die Ausführung dieser systematischen Attacken erfolgt mit beständig aktualisierten Methoden; hierfür gibt es u.a. Standardwerkzeuge, die inzwischen auf speziellen Plattformen frei zugänglich im Internet zur Verfügung stehen. Weitere Einfallstore in die Produktionsumgebung werden durch schlecht programmierte Apps, die nur auf Funktionalität ausgerichtet sind, aber Sicherheitsaspekte wenig oder gar nicht berücksichtigen, sowie per se unsichere Endgeräte geschaffen. Da viele Apps heutzutage eine Maschinensteuerung ermöglichen, ergeben sich hier zahlreiche Eingriffsmöglichkeiten: diese reichen von einer Manipulation der Produktionsprozesse, die unter Umständen Einfluss auf die Produktions- und Produktqualität haben kann, bis hin zum Abschalten einer kompletten Produktionslinie.
Die richtigen Schritte einleiten
Sicherheit im Kontext des Digitalisierungsprozesses stringent einzuführen bedeutet, dass sich die zuständigen Mitarbeiter aus IT und Produktion an einen Tisch setzen, um ein gemeinsames Verständnis für die neuen Anforderungen zu entwickeln. Dieser Austausch ist von daher relevant, da traditionell die OT-Verantwortlichen vergleichsweise über geringere Kenntnisse bezüglich Schutzmaßnahmen gegen Cyberangriffe verfügen. Essentiell ist es auch, ein Bewusstsein für die Spezifika der beiden Bereiche zu schaffen. Unter anderem beispielsweise dazu, dass den kurzlebigen Innovationszyklen der IT – und letztendlich auch die der industriellen Steuerungssysteme – die Langlebigkeit der Anlagen entgegensteht. Denn diese extrem langen Lebenszyklen der Systeme im Produktionsumfeld bringen nicht zuletzt mit sich, dass sehr häufig ungewartete IT-Komponenten benutzt werden, für die es teils seit längerem keine Sicherheitspatche mehr gibt. Konkret müssen die, zur Erarbeitung eines ganzheitlichen Sicherheitskonzeptes relevanten, Einflussvariablen anhand einer Analyse ermittelt werden: Dazu gilt es erst einmal das unternehmenskritische Wissen zu identifizieren – also die Daten und Informationen, die für den Fortbestand des Unternehmens essentiell sind. Denn die Zuordnung des Schutzbedarfs erfolgt jeweils in Abhängigkeit zu den Schutzzielen – grundsätzlich wird dieser anhand der Beeinträchtigungen festgelegt, die durch eine Kompromittierung oder Behinderung im Geschäftsablauf des jeweiligen Schutzziels entstehen können. Im Produktionsumfeld muss eine Bestandsaufnahme der gesamten OT sowie des entsprechenden Datenverkehrs vorgenommen werden. Dazu sind der Stand der einzelnen Netzwerkkomponenten zu eruieren und die Kommunikationsprozesse auszuwerten. Zudem erfolgt mit der Untersuchung aller existierenden Verbindungen der OT zur Außenwelt die Bestandsaufnahme der eingesetzten Basistechnologien.