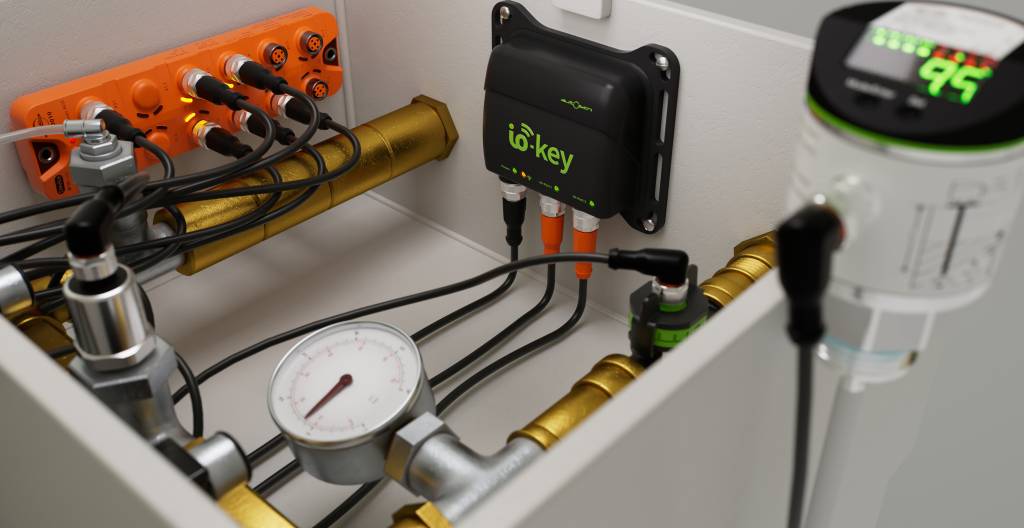
Bei Drehen, Bohren, Fräsen und anderen Zerspanungstechniken kommen große Mengen Kühlschmierstoffe zum Einsatz, um die Reibung und die Temperatur zu verringern sowie die Korrosion zu verhindern. Meist werden dazu wasserlösliche Konzentrate verwendet, die vor Ort mit Wasser gemischt und der Maschine zugeführt werden. Das Wasser kommt dabei aus der Leitung und das Konzentrat wird über Dosiergeräte in die Tanks gemischt. Diese Tank sind permanent zu überwachen und bei Bedarf aufzufüllen. Der damit verbundene Aufwand ist hoch: So betreiben Kunden von Oilgate 1 standortübergreifend Parks von vielen Hundert Maschinen, von denen die Mehrzahl wasserlösliche Schmierstoffe benötigt. Da liegen Themen wie Remote Monitoring und Automatisierung auf der Hand, doch nicht alles, was technisch möglich ist, hat sich bislang als sinnvoll erwiesen. Daher setzt Michael Kutscher, Geschäftsführer von Oilgate 1 nach rund drei Jahren Pionierarbeit mit den am Markt verfügbaren Möglichkeiten heute bewusst auf konsequentes Downsizing sowie auf eine gemeinsam mit dem Sensorik- und IoT-Anbieter Autosen entwickelte Lösung: „Sie ist einfach, aber effektiv. Sie kommt ohne komplizierten Messverfahren oder wartungsintensive Technik aus, die kaum operativen Mehrwert bieten, aber hohe Kosten und viel Aufwand mit sich bringen.“
Keep it simple
Stattdessen kommt der IO-Key zum Einsatz, eine Lösung für die Übertragung von Sensordaten in die Cloud. Da man diese auch unabhängig von der Unternehmens-IT und den Maschinensteuerungen betreiben kann, geht die Installation schnell und unkompliziert vonstatten. Sensoren erfassen die Füllstände in den Konzentrat- sowie Emulsionstanks, welche dann über den IO-Key in die Cloud übertragen und in einem Dashboard visualisiert werden. Analog zur Messtechnik hat Oilgate 1 auch die Prozesse hinterfragt und – wo es möglich war – verschlankt.
So erfolgt das Nachfüllen der Emulsion automatisch bei Unterschreiten des Min-Wertes, jedoch nicht bis zu einem – ebenfalls über einen Sensor-überwachten Max-Wert – sondern schlicht über einen festgelegten Zeitraum, der nach Faktoren wie Wasserdruck, Durchfluss, Behältergröße etc. für jeden Tank definiert wird. Das Auffüllen des Konzentrats erfolgt – nach Alarmmeldung aus der Cloud – weiterhin manuell.
Aktuell befindet sich das Projekt noch in der Pilotphase, wobei noch einige technische Details zu klären sind, darunter die Synchronisation von mehreren Maschinen, die vom selben Wasserzulauf bedient werden. Aber Kutscher ist optimistisch: „Das System ist so einfach, dass ich sicher sagen kann, dass es funktioniert.“
Stillstände und Schlimmeres verhindern
Füllstände überwachen und die Wassertanks automatisiert befüllen, das kann die Technik dank IO-Key zuverlässiger und effizienter erledigen als der Mensch. Das Auffüllen der Konzentratbehälter aber überlässt Kutscher seinen eigenen Mitarbeitern. Die Schmierstoff-Profis sind ohnehin vor Ort und kennen „ihre“ Maschinen aus dem Eff-Eff – aber eben auch die Tücken der Schmierung. Die ist komplizierter, als man annehmen könnte. Wer etwa die Emulsion direkt an der Maschine nur mit großen Zeitabständen nachfüllt, der spielt mit nicht nur mit der Qualität des Kühlschmierstoffs, sondern auch mit der Lebensdauer der Emulsion, seiner Maschinen und dem Wohlbefinden der Mitarbeiter. Korrosion an der Maschine sowie an den Werkstücken kann zu massiven Kosten und Maschinenausfällen führen, während eine Verkeimung gesundheitliche Probleme verursacht. Ein falsches Mischungsverhältnis kann überdies die Funktion des Kühlschmierstoffs einschränken, was Schäden an Werkzeugen und -stücken nach sich ziehen kann. Besser ist das bedarfsgerechte Nachfüllen mehrmals am Tag, angeleitet durch die Informationen aus dem IO-Key.
Ein effektives Schmierstoffmanagement gelingt also am besten im Zusammenspiel von moderner Technologie und kundigen Händen, gehört aber definitiv nicht zum Kerngeschäft eines metallverarbeitenden Betriebs. Das Unternehmen Oilgate 1 kann mit IO-Key hingegen einen noch individuelleren Service anbieten und Licht in so manche Black-Box bringen. So lässt sich beispielsweise der Wasser- und Konzentratverbrauch für einzelne Maschinen dokumentieren und vergleichen, um Kostentreiber zu identifizieren. Auch dies ohne weitere, unnötig komplizierte Technik.