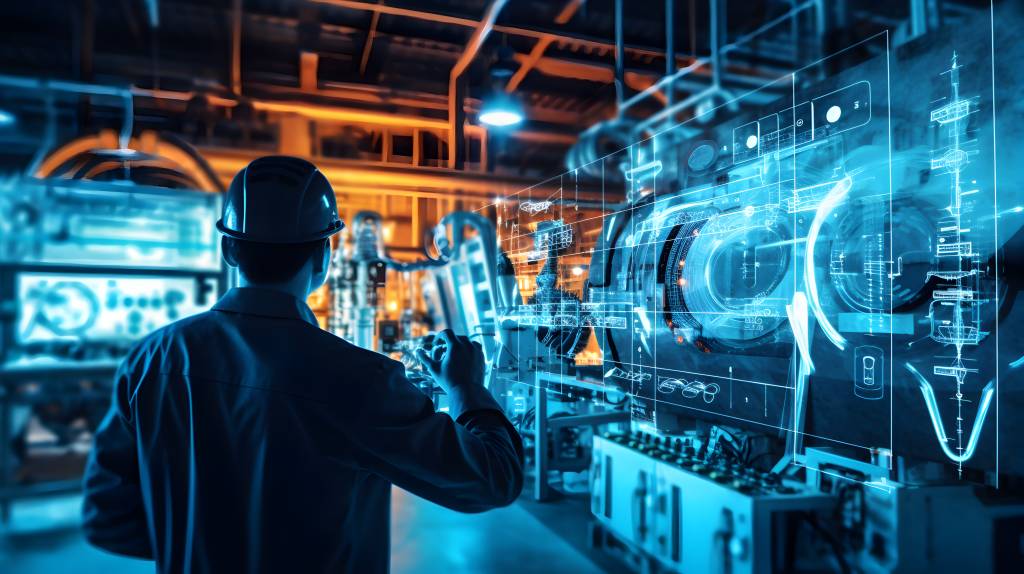
Betriebsstörungen und unerkannte Mängel am Equipment sind nicht nur mit ungeplanten Ausfallzeiten und Gefahren für die Mitarbeitenden verbunden, sondern auch mit Kosten. Mit Predictive Maintenance erkennt und behebt das Team frühzeitig Maschinenstörungen, bevor ernsthafte Probleme auftreten. Das erhöht die Planbarkeit der Betriebsabläufe und Wartungsintervalle, steigert die Effizienz der Produktion und beeinflusst eine ganze Reihe weiterer KPIs. Praxisbeispiele zeigen, wie sich die Umstellung auf Predictive-Maintenance-Modelle konkret auswirkt, und wie die Implementierung am besten gelingt.
Effizienz, Kostenreduktion und Sicherheit
Der größte Mehrwert von Predictive-Maintenance-Modellen liegt in der Reduzierung ungeplanter Ausfallzeiten. Untersuchungen beziffern die durchschnittlichen Kosten für einen ungeplanten Maschinenstillstand auf 562.000 US-Dollar pro Jahr. Wenn der Maschinenausfall sich auf den Gesamtproduktionsprozess auswirkt, steigen diese Kosten sogar auf 2,3 Millionen US-Dollar pro Jahr. Durch vorausschauende Wartungsstrategien können Unternehmen Ausfallzeiten- und -kosten erheblich senken und die Effizienz ihrer Produktion insgesamt steigern.
Nicht nur bei den Produktionsabläufen steigt mit Predictive Maintenance die Effizienz. Auch für die Maintenance-Teams selbst ist effektiveres und effizienteres Arbeiten möglich, was gerade in Zeiten des Fachkräftemangels ein wesentlicher Faktor ist. Predictive-Maintenance-Systeme können eine Vielzahl von Maschinen gleichzeitig überwachen und ermöglichen es Wartungsfachkräften somit, ihre Aufmerksamkeit gezielt auf Anlagen mit Handlungsbedarf zu lenken. Sie können sich bereits ein Bild vom Zustand der jeweiligen Maschinen machen, bevor sie ihren Schreibtisch verlassen. Das ist besonders von Bedeutung bei großen Industrieanlagen, bei denen Wartungsteams bis zu 30 Minuten benötigen, um überhaupt zur fraglichen Maschine zu gelangen oder aufwendige Sicherheitsprozeduren durchlaufen werden müssen. Dadurch gehen Unternehmen mehrere Herausforderungen simultan an und entlasten die Mitarbeiter.
Ursachen beheben
Ein weiterer wesentlicher Nutzen von Predictive Maintenance besteht in der datenbasierten Evaluierung des Maschinenzustands. Der entscheidende Vorteil der Datenanalyse liegt darin, dass sie nicht nur akute Symptome, sondern auch strukturelle Probleme wie grundsätzliche Fehlausrichtungen oder Unwuchten an Maschinen offenlegt. Mit diesem Wissen können Wartungsteams gezielt die Ursache eines oder mehrerer Probleme beseitigen, anstatt kontinuierlich einzelne Reparaturen bei entstandenen Schäden durchzuführen oder beschädigte Komponenten auszutauschen. Darüber hinaus ermöglicht diese Wartungsstrategie eine faktenbasierte Beurteilung von durchgeführten Wartungsarbeiten. Somit kann sichergestellt werden, dass die Arbeiten erfolgreich waren und alle vorhandenen Probleme effektiv beseitigt wurden. Das ist insbesondere dann entscheidend, wenn mehrere Fehlerursachen parallel bestehen.
Beispiel Überwachung von Kühltürmen
Insgesamt steigt dadurch die Maschinenleistung und -zuverlässigkeit, und das langfristig. Durch die kontinuierliche und vernetzte Überwachung zeigen sich Probleme frühzeitig, wie das Beispiel eines Chemieunternehmens bei der Überwachung industrieller Kühltürme bestätigt. Das Maintenance-Team erkannte durch die präzise Analyse von Vibrationsdaten ein Problem in der grundsätzlichen Gesamtanlagenkonstruktion. Durch die Korrektur und erforderliche Maßnahmen konnte die mittlere Betriebsdauer zwischen Ausfällen deutlich erhöht werden. Das Resultat: geringere, wiederkehrende Reparaturkosten, höhere Maschinenverfügbarkeit und letztendlich messbar mehr Produktion.