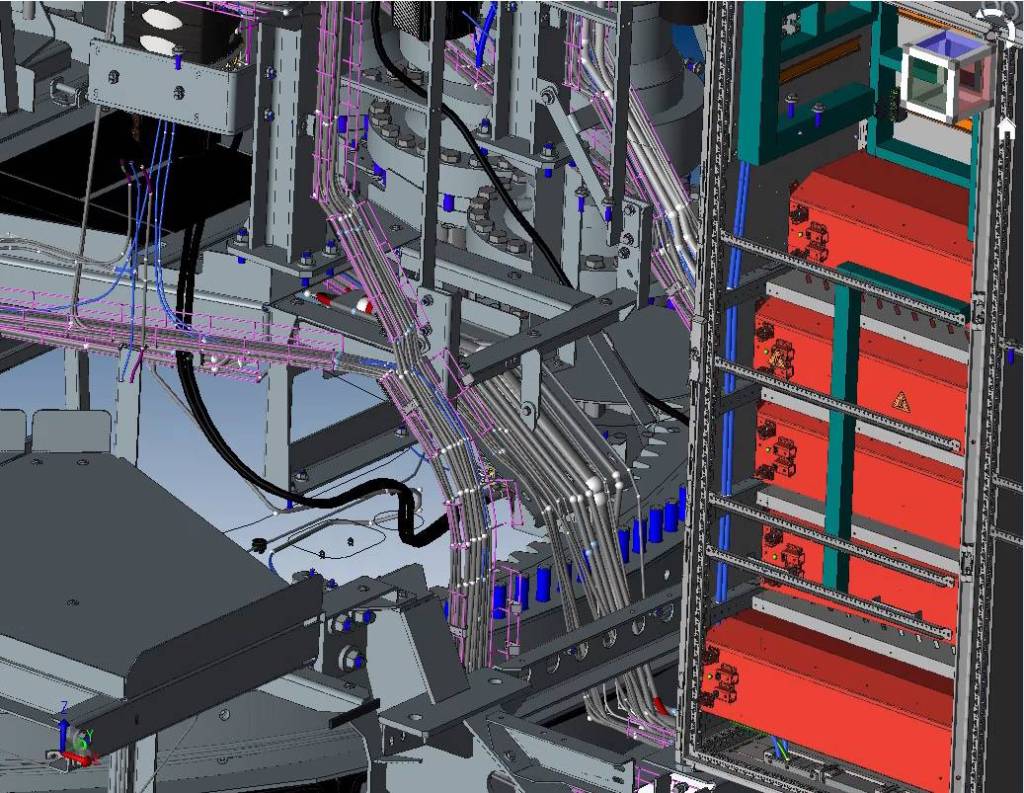
Funktionsorientierte Struktur
Mit der Einführung von Eplan hat Enercon zugleich auch eine funktionsorientierte Struktur im Elektro-Engineering etabliert – mit einer Einteilung in Module, beispielsweise Turm, Verstellsystem und Elektroverteilung. Diese Strukturierung ist folgerichtig, erleichtert das Arbeiten und stimmt auch mit dem neuen internationalen Kennzeichnungsstandard von Windkraftanlagen überein, dem Reference Designation System for Power Systems (RDS-PS). Praktischerweise unterstützt Eplan diesen Standard.
Bei allen Projekten und Investitionen, die mit der Konstruktion und der Fertigung zu tun haben, strebt Enercon eine weitgehend automatisierte und durchgängige Wertschöpfungskette an. Das gilt auch für die Überführung des digitalen Zwillings, der in der Elektrokonstruktion entsteht. Er soll auch in der realen Welt die Datenbasis sein, sprich in der Produktion. Andree Rülander: „Auch hier sind wir gleich mehrere Schritte vorangekommen, weil wir die Fertigung in Prozessschritte aufgeteilt haben, die einzelnen Eplan-Modulen entsprechen. Der digitale Zwilling dient uns hier als Datenbasis zur Ableitung von Fertigungsschritten, wie Verdrahtung, Kabelkonfektionierung und Schaltschrankmontage.“
Wie gut das in der Praxis funktioniert, lässt sich im Schaltschrankbau sehen: Bei den Schaltschränken für die neuen Baureihen E-175 EP5 und E-160 EP5 werden die Bohrungen in Eplan Pro Panel festgelegt und die Daten an Rittal übermittelt. Rittal liefert dann bereits vorgebohrte und vorgefräste Schrankelemente an Enercon. Ähnlich sind die Prozesse in der Kabelkonfektionierung. Hier arbeitet das Unternehmen mit dem Partner CadCabel zusammen.
Fazit: gut aufgestellt
Nach dem Launch und den Praxiserfahrungen der ersten Monate ziehen die Entscheider ein rundum positives Fazit. Andree Rülander: „Mit der neuen cloudbasierten Infrastruktur für das Elektro-Engineering haben wir einen großen Schritt nach vorn gemacht.“ Ein in allen Unternehmen drängender Engpass wird ebenfalls adressiert: „Die neue Infrastruktur ist auch ein Pluspunkt bei der Gewinnung von Fachkräften: Wir bieten Mitarbeitern eine moderne Konstruktionsumgebung und ein schickes Umfeld.“ Und nicht nur mit dem Ergebnis der cloudbasierten Elektrokonstruktion sind die Verantwortlichen zufrieden, sondern auch mit dem Consulting und dem Training durch Eplan: „Die Zusammenarbeit war und ist einfach gut – wie mit externen Kollegen.“
Im Zuge seiner Projekte hat Enercon auch die Schaltschrank-Frage neu gestellt und die wesentlichen Anbieter einem Benchmark unterzogen sowie Musterschränke getestet. Andree Rülander: „Das Ergebnis war eindeutig: Die Rittal Klein- und Großgehäuse bleiben unser Standard. Ein Grund dafür ist die sehr gute Abbildung in Eplan. Das wird für uns, mit zunehmender Automatisierung der Schaltschrank-Konfektionierung, künftig noch wichtiger werden.“ Zusätzlich nutzt Enercon in der Fertigung das Wire Terminal. Der Drahtkonfektionier-Vollautomat von Rittal Automation Systems ist zu einem wichtigen Baustein im Produktionsablauf und dort zu einem echten Effizienztreiber geworden – denn beim Schaltschrankausbau lassen sich bei der Verdrahtung die meisten Effizienzgewinne und Ersparnisse realisieren.
Wiederholte Entscheidung für Rittal
Im Zuge seiner Projekte hat Enercon auch die Schaltschrank-Frage neu gestellt und die wesentlichen Anbieter einem Benchmark unterzogen sowie Musterschränke getestet. Andree Rülander: „Das Ergebnis war eindeutig: Die Rittal Klein- und Großgehäuse bleiben unser Standard. Ein Grund dafür ist die sehr gute Abbildung in Eplan. Das wird für uns, mit zunehmender Automatisierung der Schaltschrank-Konfektionierung, künftig noch wichtiger werden.“ Zusätzlich nutzt Enercon in der Fertigung das Wire Terminal. Der Drahtkonfektionier-Vollautomat von Rittal Automation Systems ist zu einem wichtigen Baustein im Produktionsablauf und dort zu einem echten Effizienztreiber geworden – denn beim Schaltschrankausbau lassen sich bei der Verdrahtung die meisten Effizienzgewinne und Ersparnisse realisieren.