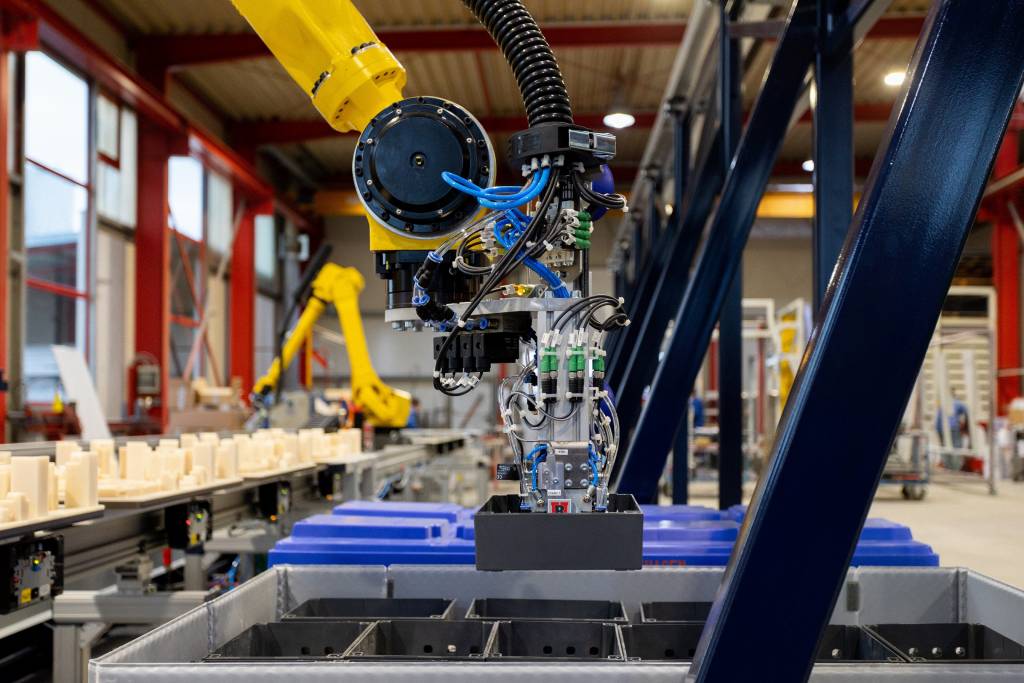
Als Sonderanlagenbauer sieht das Unternehmen Ulrich Rotte Anlagenbau und Fördertechnik seine große Stärke in maßgeschneiderten Lösungen für den Endkunden. Schwerpunktmäßig sind das vollautomatisierte Produktionsanlagen und Entwicklungen im Bereich Robotik. Eine umfangreiche Anlage zur Montage von Torsteuerungen entstand jetzt für den Tür- und Torspezialisten Hörmann. Auf dieser Anlage werden Steuerungen der aktuellen Generation, aber auch ältere Modelle und Ersatzteile montiert. Die Anlage ist auf eine Parallelfertigung ausgelegt und besteht aus manuellen sowie vollautomatischen Prozessen. Daniel Bürgermeister, Projektleiter bei Rotte, dazu: „Die Montagelinie ist in erster Linie für die Montage der aktuellen Torsteuerungen gedacht. Zudem legt Hörmann Wert auf einen nachhaltigen und kundenorientierten Produktsupport und will auch bei Produkten älterer Generationen lange lieferfähig bleiben.“ Deshalb ist die Anlage so ausgelegt, dass sowohl ältere Steuerungen als auch Neuentwicklungen montiert werden können.

Zwei Roboter auf einer Achse
Am Anfang der Montagelinie befindet sich die Kommissionierung. Von insgesamt 14 Stellplätzen entnehmen die Roboter die Teile aus bereitgestellten Großladungsträgern. Danach werden sie auf Werkstückträgern abgelegt. Das Handling der Mehrwegverpackung und die rücksendefähige Bereitstellung sind ebenfalls Teil der Arbeitsaufgabe. Die Ver- und Entsorgung der Kommissionierung kann wahlweise manuell oder automatisiert erfolgen. Die 14 Stellplätze bedeuten für die Roboter lange Laufwege. Deshalb hat man beide Fanuc-Roboter auf einer 13m langen Linearachse montiert. Die Roboter haben eine Traglast von 45kg und eine maximale Reichweite von 2.606mm. Prinzipiell ist die Aufgabenverteilung zwischen den beiden Robotern M-710iC/45M einfach: Roboter 1 fährt die Stellplätze 1 bis 7 an, Roboter 2 die Stellplätze 8 bis 14. Solange die Roboter nicht über ihre jeweilige Grenze hinausfahren, reicht eine Absicherung über Dual Check Safety (DCS). Eine andere Sicherheitsoption von Fanuc, der Interference Check, verhindert im dynamischen Betrieb eine Kollision der Roboter untereinander. Bürgermeister sieht beide Optionen als nützlich an: „Entweder wir sperren die Bereiche fest oder wir machen eine dynamische Abfrage. Technisch ist beides machbar.“ Geleitet werden die Roboter von einem 3D-Vision-System, das separat über der Anlage angebracht ist. Aufgrund der feststehenden Palettenplätze weiß der jeweilige Roboter zwar, wo das Gebinde steht, aber er kennt noch nicht die Lage der Teile, die er greifen und auf dem Werkstückträger ablegen soll. Im Projektverlauf wurden verschiedene Anlieferungsformen wie z.B. die Bereitstellung der Produkte in Trays oder Gitterboxen getestet. In enger Abstimmung mit dem Kunden wurde schließlich die Lösung mit den flexibel nutzbaren Kunststoffboxen realisiert. In diesen sind die Teile durch Zwischenlagen separiert in Ebenen angeordnet. Ein 3D-System liefert die fürs Greifen erforderlichen Positionsinformationen und ermittelt auch Informationen zum Füllstand des jeweiligen Ladungsträgers. Dazu wurde die Kamera unabhängig von den Robotern an einer eigenen Linearachse über den Palettenstellplätzen montiert. Der große Vorteil besteht darin, dass die Informationen unabhängig vom Roboter aufgenommen werden können. Eine Kamera am Handgelenk des Roboters hätte die Taktzeit des Roboters verlängert. Aus der Erfahrung mit anderen Vision-Systemen berichtet Bürgermeister: „Es ist deutlich einfacher, mit einem System zu arbeiten, bei dem sich CAD-Modelle hinterlegen lassen, statt Bildmerkmale zu definieren, die jedes Mal überprüft werden müssen. Als Nicht-Programmierer habe selbst ich das innerhalb weniger Minuten bedienen können. 2D-Systeme haben bei anderen Anforderungen ihre Stärken und ihre Berechtigung.“

Roboter am Prüfplatz
Die Werkstückträger mit allen für die Montage erforderlichen Teilen fahren das Produkt durch den kompletten Montageprozess. Nach Abschluss der Montage erfolgt am automatisierten Prüfplatz eine vollständige Abschlusskontrolle. Dort werden die Torsteuerungen optisch und elektronisch überprüft. Zwei Roboter des Typs LR Mate 200iD kontaktieren die Steuerung und simulieren unterschiedliche Bedienabläufe. Der Prüfplatz ist redundant aufgebaut, um Engpässe zu vermeiden. Auch wenn sich die beiden Roboter in der Zelle nahestehen, sind die Sicherheitszonen der beiden Roboter limitiert und haben keine Überschneidung. Dazu dient die integrierte Softwarelösung Dual Check Safety. Da keine platzraubende Sicherheitsausrüstung erforderlich ist, bleibt auch die für die Roboterzellen notwendige Fläche auf ein Mindestmaß begrenzt. Das Einrichten von Sicherheitszonen – das bestätigen die Programmierer bei Rotte – sei damit sehr einfach. Zudem lässt sich der abgesperrte Bereich am Monitor überprüfen und virtuell kontrollieren.
Die gesamte Kommissionierarbeit bei der Bereitstellung für die Montage übernehmen zwei 45kg-Roboter, die sich eine 13m lange Linearachse teilen. – Bild: Fanuc Deutschland GmbH Die zwei M-710iC-Roboter auf der Verfahrachse setzen alle zwölf zu handhabenden Produkte mit einem Universalgreifer auf entsprechende Ladungsträger. – Bild: Fanuc Deutschland GmbH
Ein Greifer für alles
Haben die Steuerungen die Prüfung bestanden, fährt der Werkstückträger zur sogenannten Einlagerung, die ebenfalls von Rotte entwickelt und realisiert wurde. In dieser Zelle wird die Steuerung komplettiert. Ein Roboter fügt den Deckel auf das Gehäuseunterteil, appliziert ein Typenschild und lässt dieses über eine Bilderkennung verifizieren. Passt alles, werden die Steuerungen sortenrein in Kleinladungsträger gelegt und über eine Förderanlage der Intralogistik übergeben. Da in dieser Zelle vom Roboter vor allem Reichweite gefragt ist, wurde ein Langarmroboter M-20iA/12L von Fanuc gewählt. Alle Anlagen sind mit Bediengeräten ausgestattet, auf denen die Anlagensteuerung visualisiert ist. Wenn nötig, lässt sich ein Roboter auch einzeln im Handmodus verfahren. Im Automatikbetrieb ist die Anlagensteuerung an die zentrale Produktionssteuerung angebunden. Übrigens arbeiten die beiden M-710iC-Roboter in der Kommissionierung mit einem einzigen Greifer für alle zwölf Produkte, Behälterdeckel und Zwischenlagen. Die maßgeschneiderten Robotergreifer entwickelt, konstruiert und baut Rotte je nach Kundenanforderung selbst, auch wenn Standardkomponenten der Einfachheit halber von einschlägigen Herstellern bezogen werden.