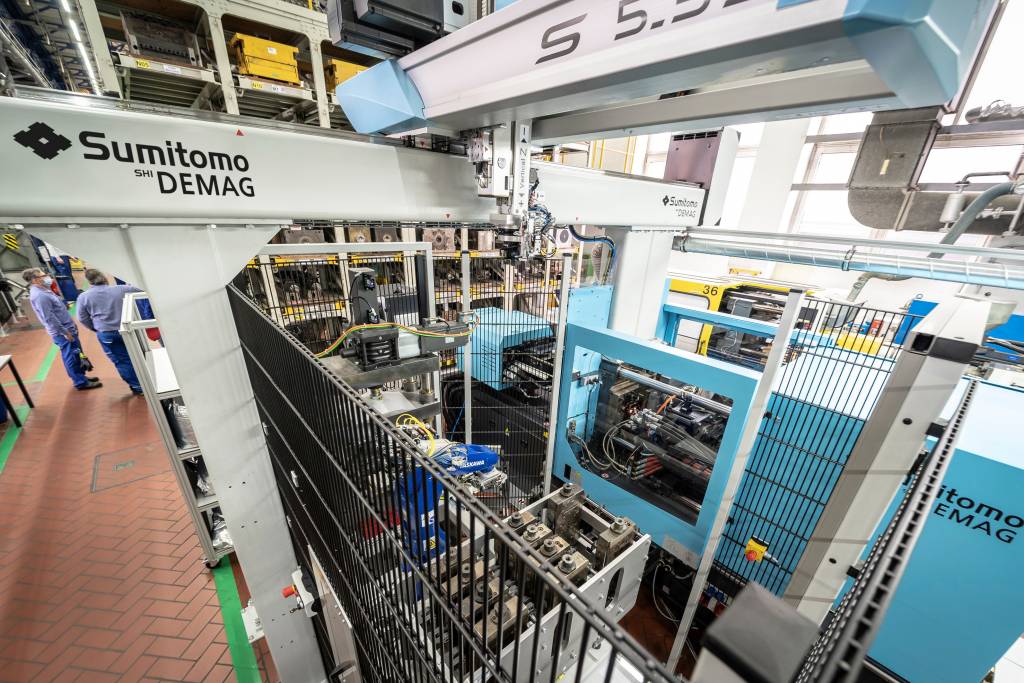
Im Mittelpunkt der Zelle steht eine hochpräzise, vollelektrische Intelect Spritzgießmaschine von Sumitomo Demag mit 1.000kN Schließkraft. Neben den wichtigsten Entscheidungskriterien wie kompakter Bauweise, Energieeffizienz und Wiederholgenauigkeit schätzt das 30-köpfige Team im Technikum die verbesserte Komfort- und Sicherheitsausstattung, darunter der niedrige Geräuschpegel aber auch fortschrittliche, voll digitalisierte Lösungen für den automatischen Werkzeugwechsel und die Robotersteuerung. Der Linearroboter SDR 5-35S erfüllt dabei zwei Aufgaben. Zum einen sorgt er für die vollautomatische Platzierung von zwölf unterschiedlichen Wechseleinsätzen aus einem Magazin in die Spritzgießmaschine. Zum anderen entnimmt derselbe Roboter mit seinem multifunktionalen Greifer den Prüfkörper aus dem Werkzeug und gibt ihn an einen kleinen Yaskawa GP8 Sechsachs-Gelenkarmroboter weiter, der die Teile auf einer spindelangetriebenen Stanze ablegt, die den Anguss abtrennt. Das vorhandene Werkzeugeinsatz-Konzept und die weitere Sonderfunktionen enthaltende Spritzeinheit wurden in die neue Fertigungszelle integriert. Erweiterungen erfuhr die Zelle durch die Einbindung der Temperiergeräte-Steuerung und die Anbindung an das neu eingeführte Manufacturing Execution System.

Werkzeugwechsel: immer ein heißes Eisen
Viele der Prüfkörper, die im BASF Technikum verarbeitet werden, sind glasfaserverstärkte, oft auch mit Flammschutz ausgerüstete Hochtemperatur-Thermoplaste. Infolgedessen erreichen die Schmelzetemperaturen bis zu 400°C und die Werkzeugtemperaturen bis zu 180°C. Das Werkzeugmagazin kann über den Roboter mit zwölf Wechseleinsätzen bestückt werden. Aufgrund der Integration von Temperiergeräten in die Maschinensteuerung erfolgen die Wechsel der Einsätze in die Spritzgießmaschine auch bei hohen Werkzeugtemperaturen automatisiert. Um eine sichere Werkzeugentnahme durch den Roboter zu garantieren, wird die Temperatur auf 80°C gesenkt und der Druck im Einsatz herabgesetzt. Das MES von BASF benachrichtigt die Zelle, wann das Ende der aktuellen Versuchseinstellung ansteht und übergibt den Befehl zum nächsten Werkzeugwechsel an die Fertigungszelle. Unmittelbar im Anschluss an die Herstellung des letzten Probekörpers wird der Wechseleinsatz von dem integrierten Temperiergerät geregelt abgekühlt. Als nächstes wird der Einsatzwechsel über Ausgangs- und Eingangssignale mit der Zellensteuerung synchronisiert und der neue Werkzeugdatensatz über die Roboterschnittstelle umfangtragen. Nach dem Einsatzwechsel heizen die Temperiergeräte wieder auf. Der automatische Betrieb läuft an und sobald die Werkzeugtemperatur erreicht ist, wird die Produktion einer neuen Versuchseinstellung gestartet.
Stanzen mit Präzision
Der multifunktionale Greifer stellt sicher, dass alle Probekörpergeometrien mit höchster Präzision auf dem Stanztisch abgelegt werden. Dies ist nicht unproblematisch, da viele der Materialien einen hohen Glasfaseranteil haben, was Verzug bei den Probekörpern verursachen kann. Werden die Prüfkörper nicht hinreichend gut fixiert, kann es passieren, dass sie schief gestanzt werden und damit nicht den spezifizierten Qualitätsstandards entsprechen.
Digitale Integration
Das BASF-Team fährt jeden Tag eine Vielzahl unterschiedlicher Versuchseinstellungen auf der Fertigungszelle. Dies bedeutet, dass das MES der Zelle jeweils verschiedene Material- und Prozessparameter, Prüfteilgeometrien und Temperaturen vorgibt. Jeder einzelne Spritzgusszyklus wird anschließend digital erfasst und dokumentiert. Das System zeichnet aus, dass jeder einzelne Zyklus und eine Vielzahl von Daten aufgenommen werden. Diese Daten repräsentieren den kompletten Bearbeitungsablauf und liefern Rückschlüsse, wie sich das Material unter bestimmten Bedingungen verhält und wie es später verarbeitet werden kann.