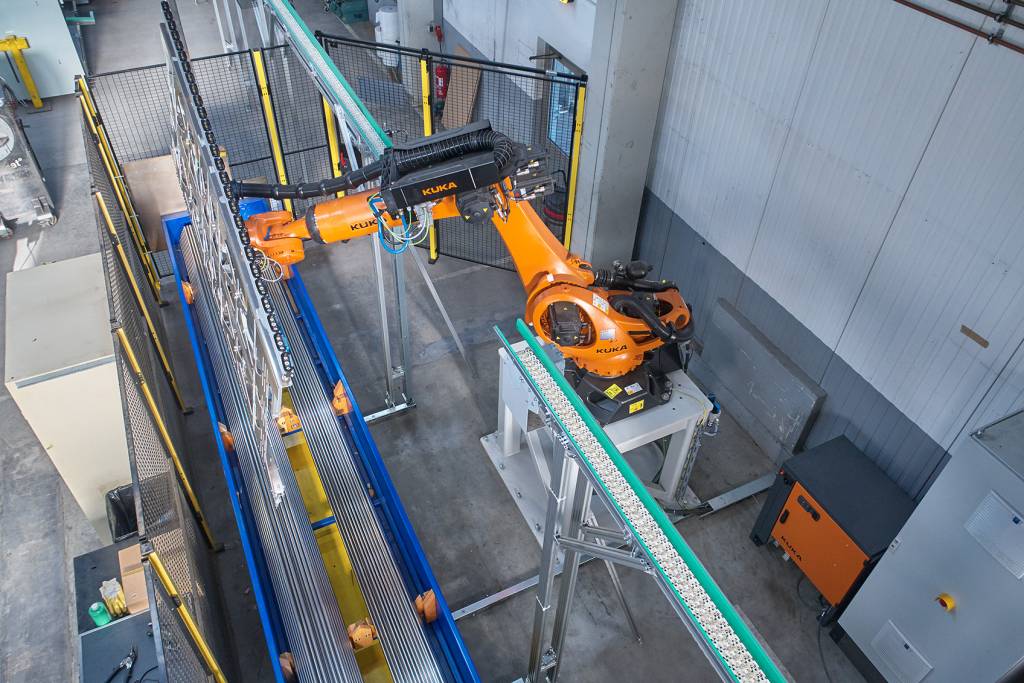
Das Unternehmen Sedus Stoll produziert seit 1871 hochwertige Büromöbel. Um die Automatisierung der Produktion voranzutreiben, hat Trafö Förderanlagen im Auftrag von Sedus Stoll eine Roboterzelle mit individuell angepasster Software konzipiert. Der Kuka-Roboter, ein KR Quantec vom Typ KR270 R2700 ultra, dient darin als Bindeglied: Er versorgt den Rohrlaser, der bisher manuell beladen wurde, vollautomatisch mit Material aus dem Lager. „Die Roboterzelle, die wir im Jahr 2018 implementiert haben, bringt eine erhebliche Arbeitserleichterung mit sich und beschleunigt den Produktionsablauf“, erklärt Ulrich Neckermann, Vertriebsleitung DACH bei Trafö. „Jetzt kann die Laseranlage mannlos im Mehrschichtbetrieb gefahren werden.“
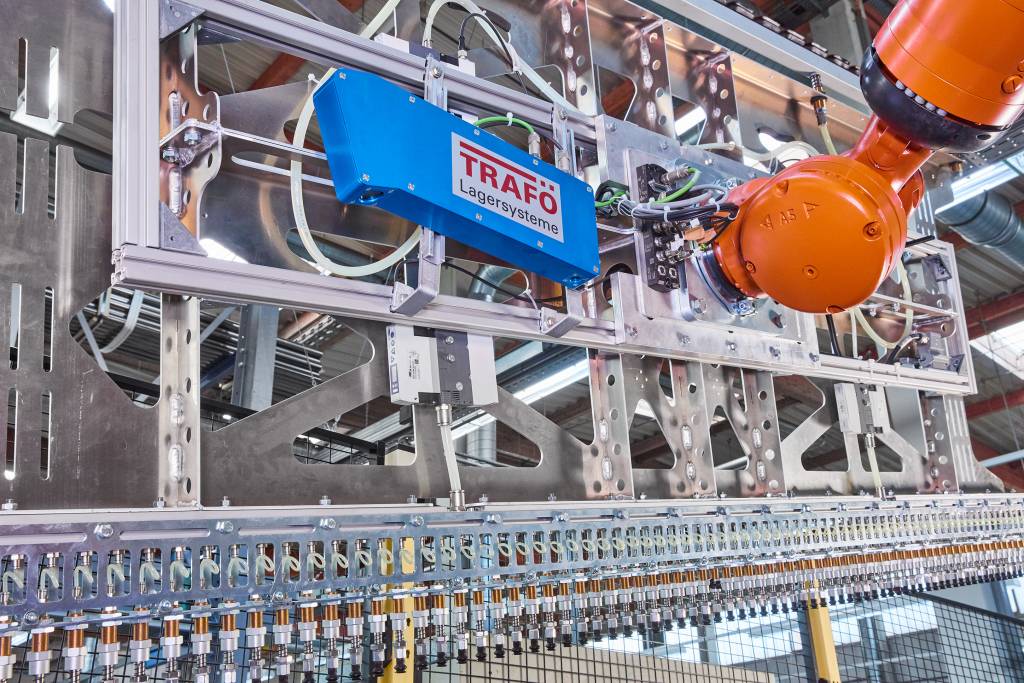
Vollautomatische Beladeeinheit
„Das Besondere an der Roboterlösung ist, dass der Laser direkt mit Einzelrohren bestückt wird“, so Neckermann. „Der Transport ganzer Bunde und die manuelle Beladung entfallen.“ Um einen reibungslosen Ablauf zu gewährleisten, hat Trafö für den Tube-Picking-Rohrlaser eine spezielle Software entwickelt. Diese ermöglicht, dass alle an der Anlage beteiligten Komponenten miteinander kommunizieren. Digitale Produktionspläne geben vor, welche Rohrtypen zu welcher Zeit am Laser benötigt werden. Das geforderte Material wird per Tablet aus dem Langgutlager geordert. Auch das Lager wurde technisch auf den neuesten Stand gebracht, indem es mit einem Retrofit ausgestattet wurde: Die Steuerung, Elektrik und Software wurden komplett erneuert. Außerdem führt nun eine neue Förderstrecke vom Langgutlager zum Roboter und vom Roboter hin zur Ablagestelle am Rohrlaser. Das Lagersystem liefert die bestellten Rohre über die Förderanlage in Systemkassetten an die Roboterzelle. In diesen oben offenen Kassetten sind meist verschiedene Rohrtypen eingelagert. Der Rohrlaser verarbeitet Rohre mit einer Länge von bis zu 6.800mm und einem Gewicht von bis zu 100kg. Neben Rundrohren mit einem Durchmesser von 16 bis 90mm können auch Quadrat- und Rechteckrohre mit Maßen zwischen 30×30 und 100x100mm bearbeitet werden. Auch der Kuka-Roboter ist auf das Handling solcher Rohre ausgelegt. Um die in der Systemkassette lagernden Rohre voneinander zu unterscheiden, ist der Roboter mit einem intelligenten 3D-Erkennungssystem ausgestattet.

Konstante Materialbelieferung des Rohrlasers
Im Detail läuft das Tube-Picking wie folgt ab: Der Roboter erhält aus dem Produktionsplan die Information, welches Rohr als nächstes im Rohrlaser bearbeitet werden soll. Anhand der übermittelten Daten scannt er mithilfe des integrierten 3D-Scanners den Inhalt der Systemkassette, um die Lage und Position der einzelnen Rohre zu erfassen. Sobald er das angeforderte Rohr aufgrund seiner Produkteigenschaften identifiziert hat, beginnt das Tube-Picking: Der Roboter ist mit zwei Vakuumgreifern ausgestattet – einer für runde und einer für eckige Rohre. Er wählt eigenständig das passende Werkzeug aus, greift in die Kassette und nimmt das betreffende Rohr heraus. Dabei passt er den Neigungswinkel des Greifers automatisch an die ermittelte Position und die Lage des Rohres an. Sollte die Aufnahme des Rohres nicht sofort gelingen, findet ein Nachgreifen statt. Diese Zusatzfunktion sorgt für einen zuverlässigen Ablauf, auch wenn die Rohre quer liegen oder verkantet sind. Wenn der Roboter das Rohr sicher erfasst hat, hebt er es an und legt es auf der Förderstrecke ab, die oberhalb der Roboterzelle angebracht ist und das Rohr zum Laser transportiert. Dort wird das Rohr mithilfe eines Senkförderers der Aufnahmevorrichtung des Rohrlasers zugeführt. Auf diesem Teil der Förderanlage können mehrere Rohre hintereinander abgelegt werden. Dieser Vorpuffer dient dazu, die durchgehende Versorgung des Lasers zu garantieren.
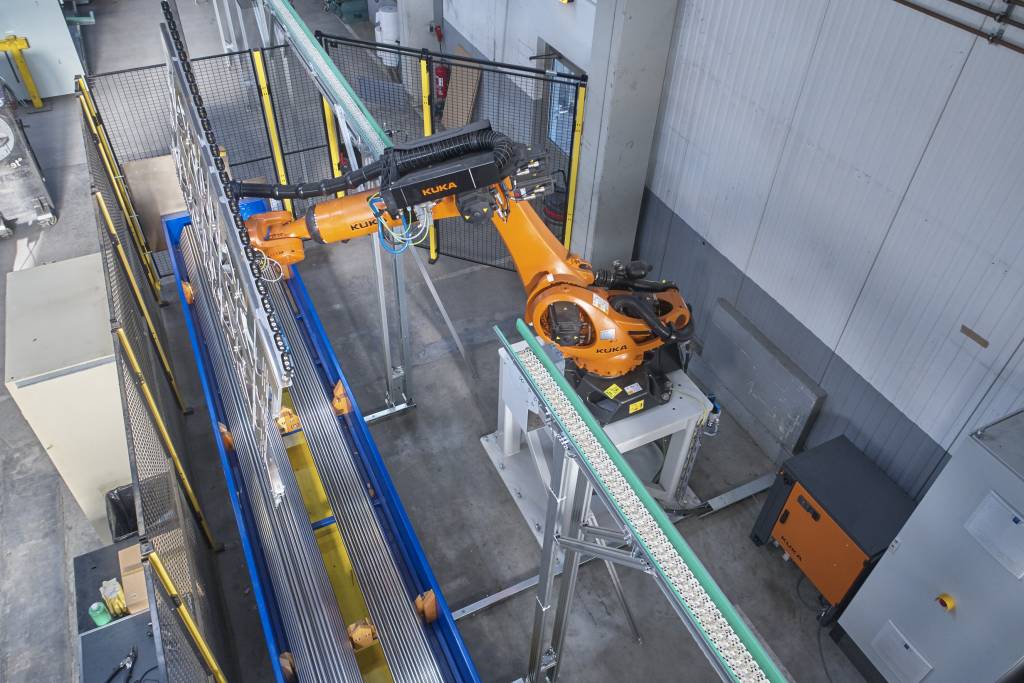
Hohe Wirtschaftlichkeit der Produktionsanlage
Die automatisierte Lösung ermöglicht es, die Wirtschaftlichkeit der Produktion zu steigern. Die Roboterzelle bietet verschiedene Vorteile: Zum einen entfallen manuelle Eingriffe in die Beladung des Rohrlasers. Der Roboter führt dem Laser die benötigten Teile präzise zu. Zum anderen kann durch die automatische Materialzuführung die maximale Auslastung des Lasers erreicht werden. „Durch die Roboterzelle kann die Laseranlage mehrschichtig im Takt von weniger als einer Minute bestückt werden“, hebt Neckermann hervor. Diese Effizienz sorgt für eine bestmögliche Ausnutzung des Rohrlasers. Die Vorteile machen sich insbesondere bemerkbar, wenn im Produktionsalltag häufige Materialwechsel stattfinden.