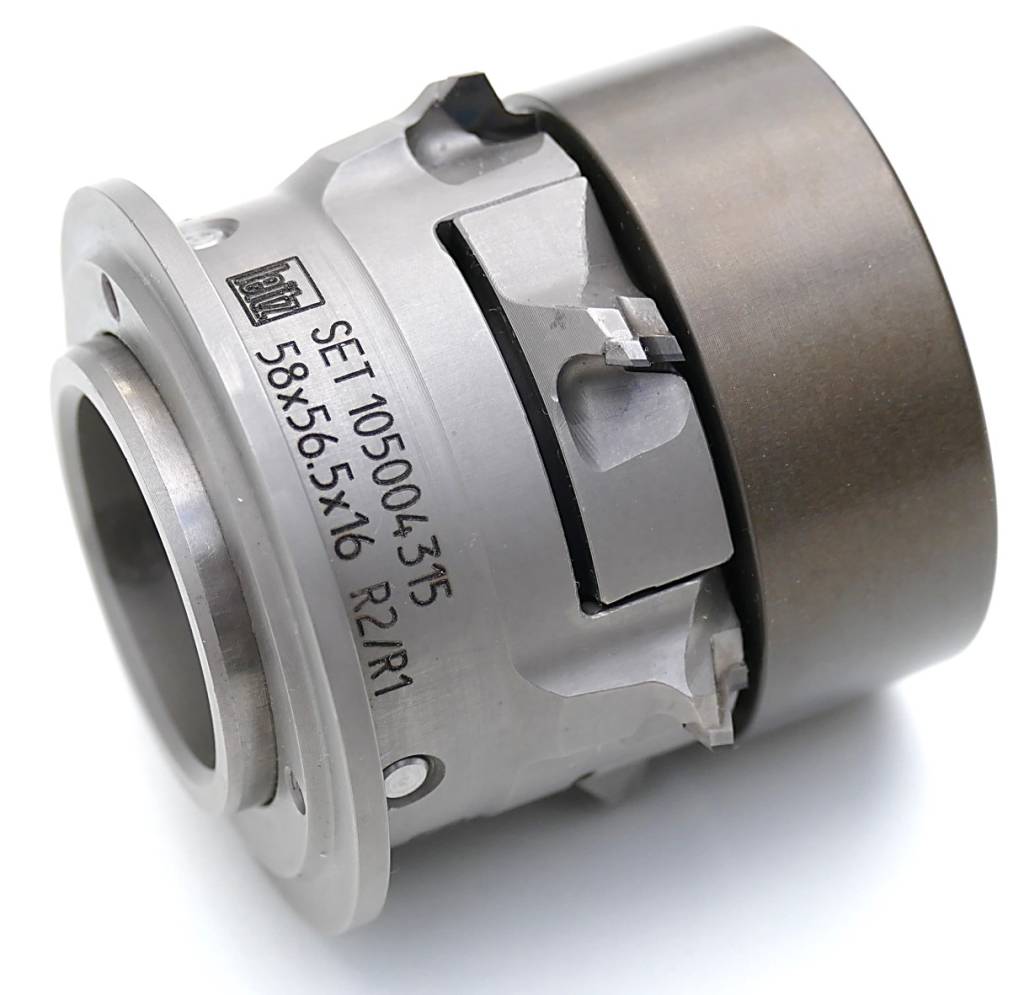
CNC-Formatbearbeitung mit Schaft- oder Fügefräsern
Ziel der Formatbearbeitung mit Fügefräsern sind beidseitig ausrissfreie Kanten. Dies lässt sich am besten mit diamantbestückten Werkzeugen erreichen, die über wechselseitige Achswinkel verfügen – also schräg eingebaute Schneiden. Jedoch darf dieser Achswinkel nur eine bestimmte Mindestgröße aufweisen, um den Schnittdruck zu reduzieren. Werkzeuge mit zu großen Achswinkeln erzeugen bei Spanplatten mit loser Mittelschicht raue und poröse, löchrige Oberflächen. Speziell bei der Laserbekantung kann dies zu Problemen bei der Kantenhaftung oder bei Wasserprüfungen führen. Ein weiteres Argument, das gegen die Verwendung solcher Werkzeuge spricht, sind die deutlich höheren Anschaffungs- und Instandhaltungskosten. Werkzeugsysteme mit hohem Achswinkel sind nämlich in der Regel mit überlangen Schneidelementen bestückt. Bei der Verwendung von Diamantschneiden entstehen also sowohl in der Anschaffung als auch beim Nachschärfen hohe Kosten.
Untersuchungen über viele Jahre hinweg haben gezeigt, dass die besten Bearbeitungsergebnisse hinsichtlich perfekter Kanten und ausrissfreier Mittellage am besten mit Werkzeugen gelingt, die einen Achswinkel von 50 Grad aufweisen. Nur so lässt sich beim Fügen ein perfektes Schnittergebnis erzeugen und die Prozesskosten steigen nicht unnötig. Wie etwa mit den EdgeExpert Fräswerkzeugen von Leitz.
Neben der Wahl des optimalen Werkzeugs, hat auch die Bearbeitungsstrategie einen wichtigen Einfluss auf die Bearbeitungsqualität beim Formatieren. Deshalb empfiehlt es sich auf entsprechende Anfahr- und Eckenstrategien im gesamten Fräsprozess zu achten. Anwender, die sich mit diesem Thema erstmalig auseinandersetzen, sind gut beraten, wenn ihnen dabei ein erfahrener Ansprechpartner mit tiefgreifendem Wissen rund um Material, Werkzeug und Bearbeitungsverfahren zur Seite steht.
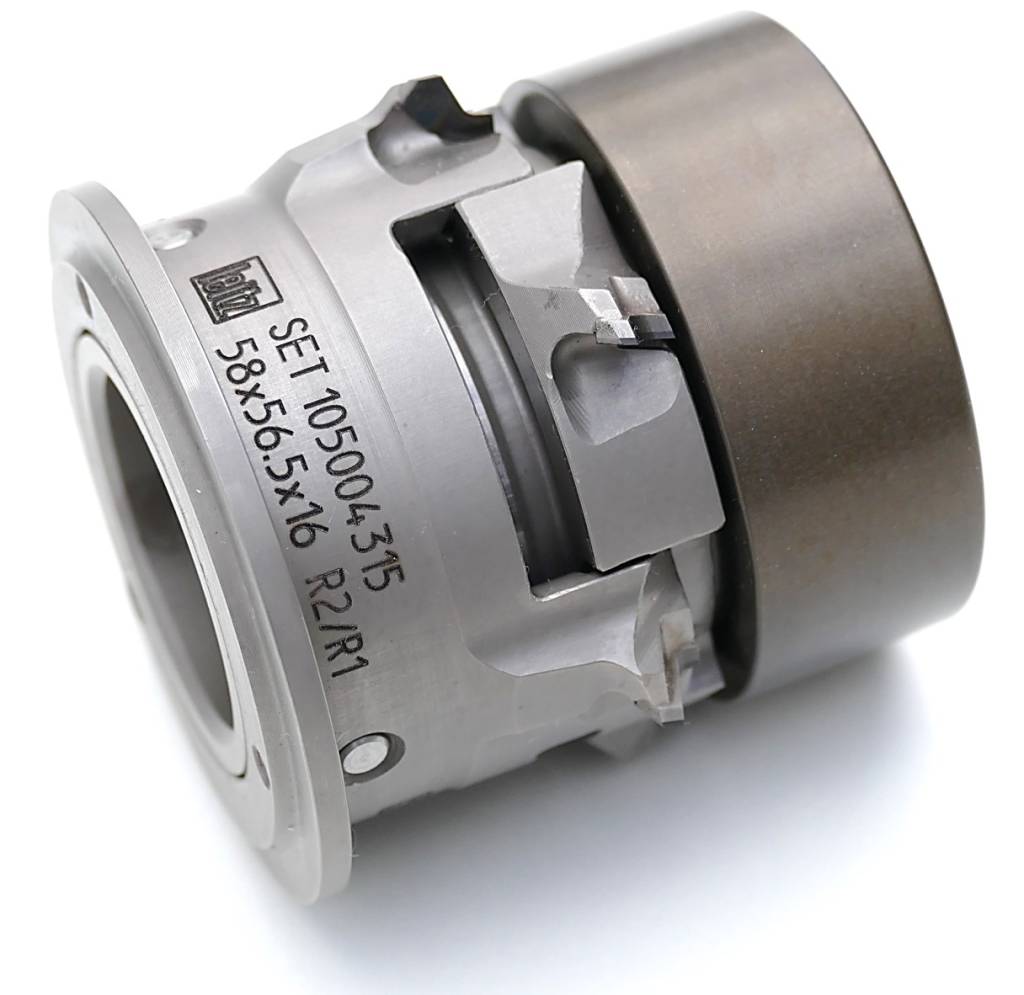
Der Gehrungsschnitt mit CNC-Maschinen
Das Gehrungssägen ist eine der anspruchsvollsten Bearbeitungen in der Möbel- und Innenausbau-Branche. Auf 5-Achs-Bearbeitungszentren oder mit speziellen CNC-Sägeaggregaten lassen sich schräge Sägeschnitte in allen gewünschten Winkeln sehr effizient herstellen. In der Praxis hat sich bewiesen, dass speziell für Gehrungsschnitte ausgelegte Kreissägeblätter ein absolutes Muss für diesen Anwendungsbereich sind. Der Hauptunterschied zu herkömmlichen Kreissägeblättern liegt in ihrer geringen Schnittbreite und der gleichzeitig hohen Planlaufqualität. Diese technischen Merkmale sind hier von großer Bedeutung, um Ausbrüche an der spitzen Seite der Gehrung zu vermeiden. Speziell bei sehr spitzen Gehrungen – wie beispielsweise 60 Grad – verschlechtert die kleinste Ungenauigkeit im Gesamtsystem das Bearbeitungsergebnis signifikant.
Ein weiterer wichtiger Punkt ist die Verwendung der richtigen Bearbeitungsstrategie. In diesem Fall empfiehlt es sich, in einer ersten Schnittbewegung die Platte an der innenliegenden Kante im Gleichlauf zwei Millimeter tief einzuritzen. Der Trennschnitt erfolgt anschließend im Gegenlauf. Somit erreichen CNC-Anwender den perfekten Schnitt. Ausrissfrei an beiden Kanten und in der Schnittfläche ohne Fehler.
Beispiele für derartige Kreissägeblätter, speziell für Gehrungsschnitte, sind das hartmetallbestückte Kreissägeblatt Katana und das diamantbestückte Kreissägeblatt WhisperCut von Leitz. Sowohl Katana als auch WhisperCut ermöglichen durch die geringe Schnittbreite und ihr besonders ruhiges Laufverhalten perfekte Schnittergebnisse in allen gängigen Materialien.
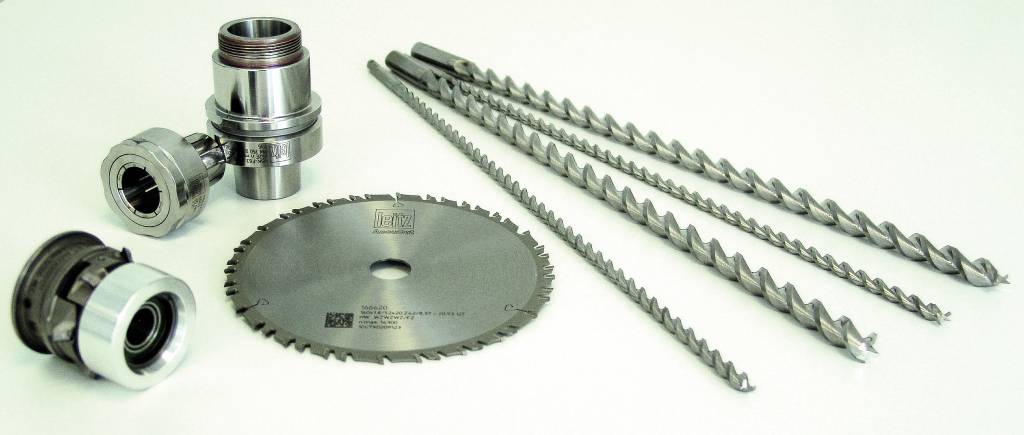
Das Nesting-Verfahren
Beim Nesting werden mit Hilfe von Schaftwerkzeugen verschachtelte Formen aus plattenförmigen Werkstoffen getrennt. Speziell bei filigranen Teilen und hohen Vorschubgeschwindigkeiten stehen CNC-Anwender regelmäßig vor der Herausforderung, dass die herausgefrästen Teile durch den schnelldrehenden Fräser beim Abtrennen verschoben und beschädigt werden. Das Vakuum des Bearbeitungstisches reicht nicht aus, um die entstehenden Kräfte zu kompensieren und die gefertigten Teile am Rutschen zu hindern. Abhilfe schafft hier die Verwendung kleiner Werkzeugdurchmesser. Zum einen werden dadurch die Schnittkräfte geringer, viel wichtiger sind jedoch die schmaleren Fräsnuten, die entstehen. Wird beispielsweise der Fräserdurchmesser von 16 auf 12 Millimeter reduziert, entspricht dies der Reduzierung des Zerspanungsvolumens um 44 Prozent. Je weniger Material beim Nesting also abgefräst wird und je schmaler die entstehenden Fräsnuten sind, desto weniger schwächt dies die Vakuumleistung am Bearbeitungstisch und die Werkstücke werden sicher an Ort und Stelle gehalten.