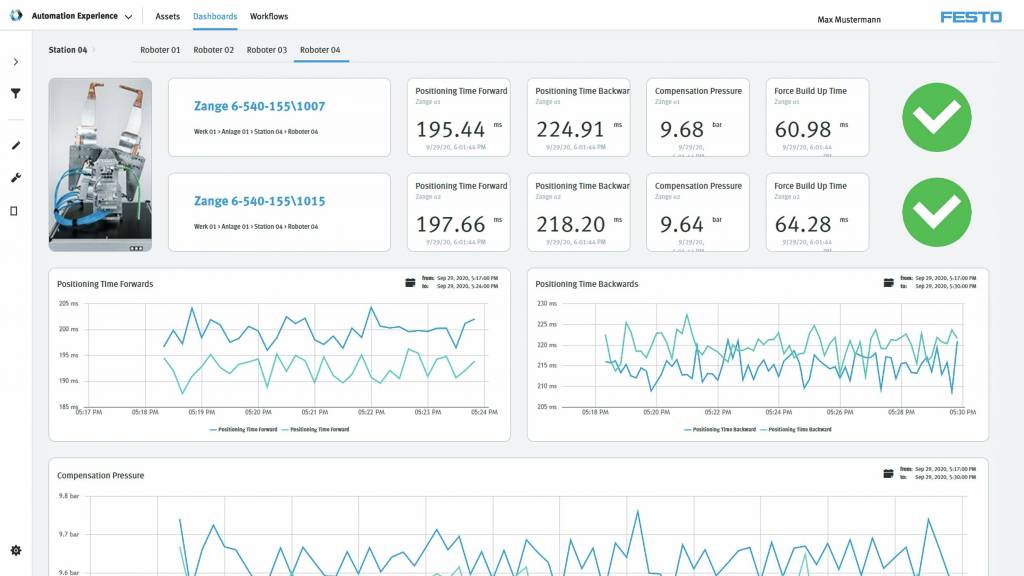
In zahlreichen Anwendungen der Automobil- und Zulieferindustrie, der Metallverarbeitung oder auch in der Lebensmittelindustrie realisiert Festo Projekte, bei denen vorausschauende Wartung – zukünftig mit künstlicher Intelligenz – dafür sorgen soll, Prozessabweichungen rechtzeitig zu erkennen, die Instandhaltung zu verbessern und Energie zu sparen.
Mehrwertlösungen generieren
Aus den Erfahrungen ergeben sich Potentiale, solche Lösungen fürs Standardgeschäft zu multiplizieren. Die Herausforderung dabei: mit den Daten aus den Geräten, den Daten aus dem Applikationsumfeld und dem Wissen über die Prozesse echte Mehrwerte für den Endkunden zu liefern.
Die Vorteile liegen auf der Hand: Automobilhersteller können Zangenreparaturen in produktionsfreie Zeiten verlagern und damit die Verfügbarkeit ihrer Anlagen erhöhen. Der Status der Zange lässt sich im Leitsystem abbilden. Automatisierte Reparaturaufträge und sogar ‚Lebensläufe‘ von Zangen sind damit leicht zu generieren. Filterfunktionen ermöglichen Vergleiche. Das frühzeitige Erkennen von Undichtigkeiten führt zu Energieeinsparungen, denn gerade Energie- und Instandhaltungskosten spielen im Karosseriebau eine große Rolle.
Predictive Maintenance
Beim Widerstandspunktschweißen in mechatronischen Systemprodukten werden heute schon viele Daten verarbeitet und zu Diagnosen vorverdichtet, die für die Instandhaltung nutzbar sind. Jedoch reicht es nicht aus, Daten nur bereitzustellen und anzuzeigen. Gegenüber klassischen Condition-Monitoring-Ansätzen sollen sich in Zukunft mit Predictive Maintenance auf Basis von künstlicher Intelligenz erweiterte Möglichkeiten ergeben: Daten werden aus den Geräten mit Prozessdaten zusammengeführt und mit Analytics-Modellen sowie cloudbasierten Lösungen ausgewertet.
Festo hat die vorhandenen Anlagen-PCs der Roboterzelle um eine Software erweitert, die die Diagnosedaten der Schweißzange einsammelt und an einen Cloud-Eingangspunkt sendet. In der Cloud wird eine Instandhaltungsapplikation betrieben, die neben der Darstellung der Daten im Browser (Instandhaltungs-Dashboards) auch die Bewertung der Daten hinsichtlich voraussichtlicher Lebensdauer vornimmt.
Herausforderung Datentransport
„Die Herausforderung dabei war, die Daten von der Schweißzange aus der Produktion überhaupt in die Cloud zu transportieren. Themen wie Netzwerkauslastung, Prozessorlasten und Datensicherheit waren zu diesem Zeitpunkt für beide Parteien Neuland“, erklärt Dr. Jan Bredau, Leiter der Abteilung Anwendungssoftware für Systemlösungen bei Festo.