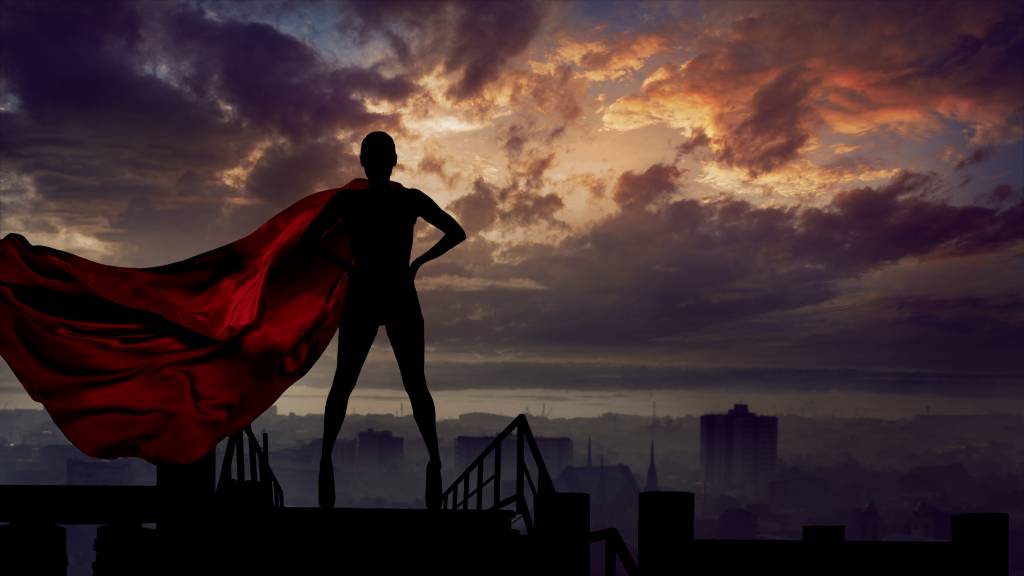
Bei den meisten Industrie 4.0-Szenarien geht es um vernetzte Systemkomponenten, digitale Prozessketten und die Verwaltung großer Datenmengen. Es ist daher zu erwarten, dass die Anzahl der Systemkomponenten und ihrer Funktionalitäten im industriellen Umfeld weiter steigt. Zusätzlich wird sich die Vernetzung von verteilten Komponenten erhöhen. Und schließlich sind es nicht nur die Industrieanlagen selbst, sondern auch deren Anbindungen an vor- oder nachgelagerte technische Systeme, die zu steigender Komplexität führen.
Anforderungen steigen mit
Diese höhere Komplexität wirkt sich auf das Systemverhalten aus, was deren Entwickler vor neue Aufgaben stellt. So sind effizientere Strategien für Instandhaltung, Inspektion und Wartung gefragt. Neue oder erweiterte Funktionalitäten für Software-, Daten- und Variantenmanagement sind notwendig. Sicherungs- und Schutzmaßnahmen gilt es zu prüfen und anzupassen. Ein Lösungsweg, all diese Aufgaben effektiv zu erledigen, verläuft in einem bislang wenig beachteten Gebiet – dem der Systemdiagnostik.
Digitale Systemdiagnostik
Um die Bedeutung der Systemdiagnostik für Industrie 4.0-Szenarien zu verstehen, hilft der Blick auf ihre Erfolgsgeschichte in der Fahrzeugindustrie. Seit der Jahrtausendwende steigt in der Automobilbranche die Anzahl der Funktionen an, und mit ihnen die Anzahl der beteiligten Teilkomponenten und deren Vernetzung untereinander. Dies führte zu zwei Entwicklungen:
- Zum einen gab es mehr potenzielle Fehler. Erst durch die steigende Funktionsvielfalt, dann durch ihre Vernetzung, die weitere Fehlerquellen birgt.
- Zum anderen setzen sich Fehler von Teilkomponenten in den Gesamtsystemen oft schleichend und unbemerkt über mehrere Funktionen fort. Über Fehlerspeichereinträge ist die eigentliche Ursache oft nicht mehr direkt zu identifizieren.
Im Ergebnis ist der Aufwand für Fehlersuche und -behebung deutlich gestiegen. Daher haben einige Automobilhersteller bereits 2005 für ihre Steuergeräte und deren Subsysteme Diagnoseobjekte, Diagnosekommunikation und Diagnosebeschreibungen standardisiert. Gleichzeitig wurden die Diagnosefunktionalitäten erweitert. Mit dieser Digitalisierung der Systemdiagnostik bekamen die Produzenten den steigenden Analyseaufwand in den Griff.
Technische Systemdiagnostik
Die Systemdiagnose sollte stets die Fehleranalyse bei technischen Systemen unterstützen. Ein technisches System lieferte im Fehlerfall einfache Codes oder Messwerte, die von einem Mechaniker mit einem externen System ausgewertet wurden. Daher rührt die Ansicht, die Systemdiagnostik sei nur Fehlersuche. Dabei hat sich die Systemdiagnostik in den letzten 20 Jahren gewandelt und deckt heute zahlreiche Aufgaben über den gesamten Produktentstehungsprozess ab. So definieren Fachleute den Begriff der Systemdiagnostik heute: „Systemdiagnostik ist die Lehre und Kunst, Zustände von Systemen strukturiert zu erfassen, einzustellen und zu beschreiben. Darunter werden alle Methoden, Algorithmen, Datenformate, Prozesse, Verfahren und Tools verstanden, deren Ziel die Entwicklung, Herstellung, Reparatur und Wartung einer elektronischen Komponente ist. Die Anwendung der Systemdiagnostik umfasst das Konzeptionieren, Spezifizieren, Entwickeln, Testen und Produzieren sowie das Funktionieren, das Updaten, das Reparieren und das Warten des Systems.“ Die technische Systemdiagnostik beinhaltet damit im Grunde alle Funktionalitäten, die ein technisches System nicht in seiner eigentlichen Funktion ausübt.