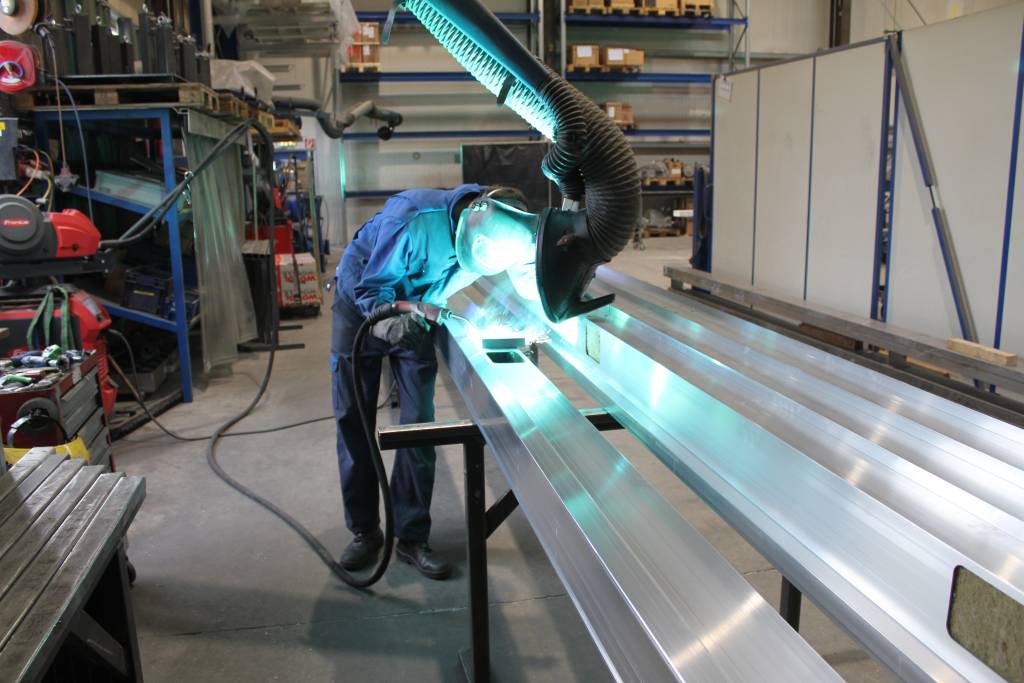
So groß wie ein Einfamilienhaus oder eine ganze Lagerhalle: Die Holztrocknungsanlagen von Mühlböck sind nichts für beengte Platzverhältnisse. Abhängig vom Anwendungszweck und den Gegebenheiten vor Ort werden diese individuell zugeschnitten und produziert. Entsprechend zeichnet sich Mühlböck durch seine hohe Fertigungstiefe aus: Alle Konstruktions- und Fertigungsschritte erfolgen inhouse. Von der Forschung und Entwicklung über die Produktion sämtlicher Anlagenkomponenten bis hin zur Programmierung der Steuerungssoftware. Rund 140 Mitarbeiter kümmern sich um Planung, Fertigung und Wartung der Anlagen am Stammwerk im oberösterreichischen Eberschwang sowie der Niederlassung in Hartberg in der Steiermark.

Konfigurator als Grundlage
Rein technisch schaffte in der Vergangenheit der Produktkonfigurator die Grundlage für individuelle Planung und Fertigung. Aus über 200 Parametern selektierten die Techniker darin die Eigenschaften der gewünschten Anlage. Daraufhin generierte der Konfigurator die zugeschnittenen Fertigungsdokumente wie Arbeitspläne und Stücklisten. „Für unser Tagesgeschäft war der Produktkonfigurator absolut unverzichtbar“, erklärt Mattäus Diermayr, IT-Administrator bei Mühlböck. „Das stellte uns jedoch vor eine gewaltige Herausforderung, als 2013 die Überlegung aufkam, eine neue ERP-Lösung zur Unterstützung unserer Geschäftsprozesse einzuführen.“ Erforderlich geworden war dies unter anderem dadurch, dass die bisher genutzte ERP-Lösung im Laufe der Zeit technisch veraltet war und den Anforderungen nicht länger gerecht wurde. So deckte die Altlösung hauptsächlich den Bereich Fertigung ab. Andere Prozessstufen, wie beispielsweise die Betriebsdatenerfassung, wurden hingegen nicht unterstützt und mussten durch Drittlösungen abgedeckt werden. In der Folge setzte sich die IT-Landschaft bei Mühlböck aus verschiedenen Inseln zusammen, deren Anzahl auch in Zukunft noch weiter zugenommen hätte. So bestand bei Mühlböck u.a. die Bestrebung, Monteure und Techniker durch eine Mobillösung unmittelbar an das zentrale System anzubinden. Doch auch dafür bot die Altlösung keine entsprechende Funktionalität.

Umstieg statt Upgrade
„Wir haben unsere Optionen analysiert und dabei hat sich gezeigt, dass eine Aktualisierung der Altlösung im Prinzip einer Neuinstallation gleichgekommen wäre“, erinnert sich Diermayr. „So setzte sich intern die Überlegung durch, stattdessen auf ein neues ERP-System umzusteigen.“ Über knapp fünf Jahre erstreckte sich die Suche nach einer Lösung, mit der eine Ablösung des Produktkonfigurators realisierbar wäre – ohne Erfolg. Ein erster Anlauf blieb erfolglos und das Team um Mattäus Diermayr musste schließlich von der vereinbarten Ausstiegsklausel Gebrauch machen und die Suche begann erneut. „Am Ende war die Asseco Solutions der einzige Hersteller, der sich überhaupt an die Ablösung herantraute“, fasst der IT-Administrator das Ende des Auswahlprozesses zusammen. Der ERP-Spezialist holte den Konfiguratorhersteller ABi ins Boot. Gemeinsam starteten die beiden Partner ihrerseits einen Anlauf zur Erstellung eines Prototyps. Der Kick-off zur Applus-Einführung erfolgte im September 2018. Das Go-Live fand am 1. Januar 2020 statt.

Regelwerk übernommen
Im Rahmen der Migration konnte das Regelwerk des alten Produktkonfigurators, in dem zahlreiche Mannjahre an Entwicklung und Weiterentwicklung steckten, von Asseco automatisiert übernommen werden. Und auch darüber hinaus profitiert Mühlböck von Verbesserungen und Optimierungen, die am Konfigurator vorgenommen wurden – und werden. Die Grundlage dafür bildet ein auf dem KVP-Ansatz (kontinuierlicher Verbesserungsprozesses) basierender Ablauf. „Unser internes KVP-Team dient dabei als Anlaufstelle für die Fertigung“, erklärt Mattäus Diermayr. Es übersetzt die Optimierungsvorschläge in konkrete Verbesserungen für den Produktkonfigurator. Denn dieser stellt die Weichen für den Fertigungsprozess. Er entscheidet über die Parameter, beispielsweise welche Blechformate für einen bestimmten Auftrag ausgewählt werden.