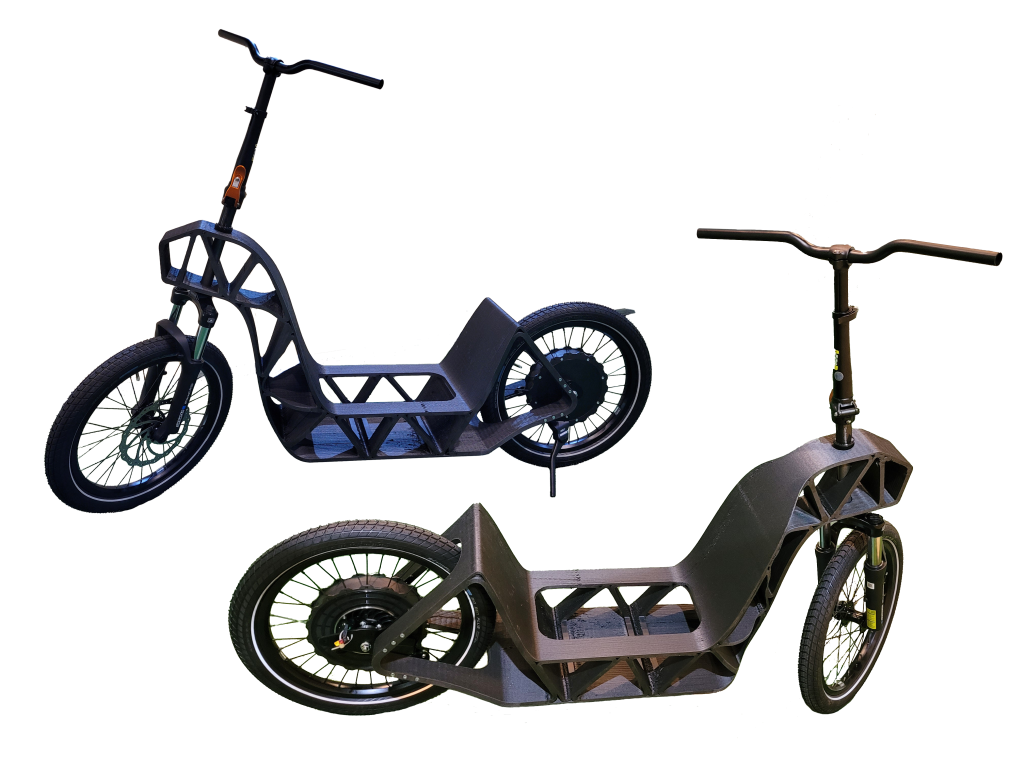
Batterieelektrische Fahrzeuge können einen Beitrag zur CO2-Reduktion im Verkehrssektor leisten. Das Mehrgewicht der Hochvoltspeicher geht jedoch auf Kosten der erlaubten Zuladung – außer es gelingt, an anderer Stelle Leichtbaulösungen zu finden. Das Fraunhofer IWU und Mosolf Special Vehicles haben einen Vorschlag, wie gleichzeitig Gewicht reduziert und dennoch der Bauraum optimal ausgenutzt werden könnte: durch ein 3D-gedrucktes Heckregal. Am Beispiel des Mercedes Vito lassen sich so im Vergleich zur bisherigen Nachrüstlösung einschließlich der Beschläge 26,5kg einsparen.
Nutzlast bleibt erhalten
Dabei bleibt die Nutzlast des Regalsystems vollständig erhalten. Auch im neuen Regal darf die untere Schublade mit bis zu 100kg beladen werden. Belastbarkeit und flexibler Einsatz des Systems sind wichtige Anforderungen, da die Ausrüstung für die Beamten zunehmend schwerer wird. Ballistische (kugelsichere) Schutzschilde beispielsweise bringen einiges Gewicht auf die Waage. Dennoch muss die Nutzung im Verkehrsdienst, Streifendienst oder bei Großveranstaltungen als Mannschafttransport flexibel möglich sein. Das neu entwickelte Regal schmiegt sich vollständig an die Fahrzeughaut, erfordert keine zusätzlichen Versteifungen oder Befestigungen und nutzt so den Bauraum im Heckbereich bestmöglich aus. In den oberen Fächern finden sogar mehr Gegenstände Platz als bisher, dank einer um 8 Prozent vergrößerten Ablagefläche. Selbstverständlich ist das Regal auch genauso sicher wie die Standardausführung.
Rahmen für E-Roller
Lastenroller mit elektrischem Antrieb werden künftig eine Rolle für den emissionsfreien Kurzstreckentransport spielen. Eingespartes Fahrzeuggewicht kommt dabei direkt der Nutzlast zugute. Doch die Sicherheit darf unter einer Gewichtsoptimierung nicht leiden. Ganz ähnlich wie beim Heckregal aus dem SEAM-Drucker ersetzt im Projekt DynaLight eine robuste Kunststoffkonstruktion die bisherige konventionelle Lösung, wobei der bisherige Rahmen des Innvelo Cargo-Scooters der Chemnitzer Forschungseinrichtung ICM aus Stahl bestand. Der neue Kunststoffrahmen spart rund 10 Prozent Gewicht und Kosten. Der neue Rahmen ist genauso praktisch wie der alte: Lieferdienste können auf dem Gepäckträger eine Getränkekiste oder eine Thermobox transportieren, einschließlich Fahrerin oder Fahrer schafft der Roller etwa 200kg Nutzlast. Partner im Projekt DynaLight sind neben dem Fraunhofer IWU das Institut Chemnitzer Maschinen- und Anlagenbau, ICM Chemnitz und Sauer Creations.
Fertigung großvolumiger Bauteiler
Für die Herstellung des Regals und der Rahmenkonstruktion des Rollers kam die SEAM-Technologie zum Einsatz. SEAM steht für Screw Extrusion Additive Manufacturing. Der Druckprozess erfolgt, indem über eine modifizierte Extrusionsschnecke Kunststoffgranulat in den Extruder eingezogen und plastifiziert wird. Dabei kann ein Materialaustrag von bis zu 10kg pro Stunde erreicht werden. Die entstehende Kunststoffschmelze wird anschließend schichtweise auf der Bauplattform abgelegt. Durch den kontinuierlichen Ablageprozess ist die Fertigung großvolumiger, belastbarer Bauteile möglich. SEAM trägt zudem zur Kreislaufwirtschaft bei, da für den Druck etwa auch aus Thermoplast-Rezyklaten gewonnenes Granulat geeignet ist, Kunststoff aus dem vorigen Produkt also nicht ‚abgewertet‘ werden muss. So können aus Kunststoffflaschen nicht nur Parkbänke entstehen, sondern auch hochbelastbare Regale und tragende Rahmen für E-Roller.