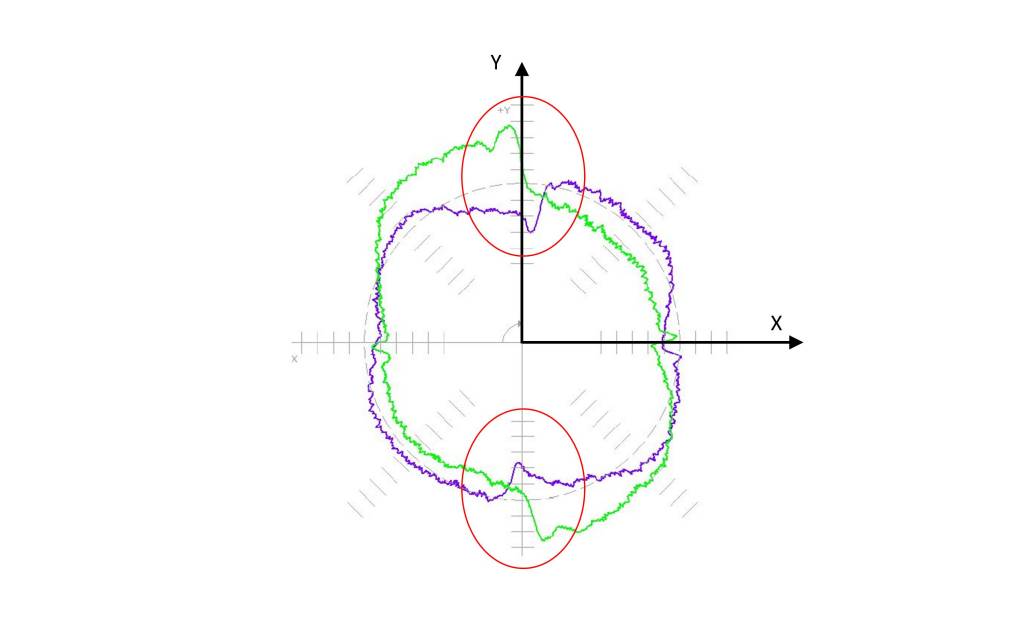
Die Positionier- und Bahngenauigkeit von Industrierobotern ist bei Bearbeitungsaufgaben von entscheidender Bedeutung für die Qualität der gefertigten Erzeugnisse. Übertragungsfehler, die sich aufgrund der hysteresebehafteten Getriebecharakteristik ergeben, wirken sich jedoch negativ auf die Robotergenauigkeit aus. Um neue Anwendungsbereiche von Industrierobotern zu erschließen, muss deren dynamische Bahngenauigkeit gesteigert werden. Einer der Hauptgründe für die auftretenden Bahnfehler ist die Hysterese der verwendeten Getriebe. Eine Methode zur Überprüfung und Beurteilung der Genauigkeit von Maschinen stellt der Kreisformtest dar. Das Ergebnis eines solchen Kreisformtests in der X-Y-Ebene eines Kuka KR 500-3 MT, der am Institut für Steuerungstechnik der Werkzeugmaschinen und Fertigungseinrichtungen der Universität Stuttgart (ISW) gemessen wurde, zeigt die Abbildung. Es ist jeweils der Positionsfehler für beide Drehrichtungen dargestellt und diejenigen Stellen hervorgehoben, an denen eine besonders hohe Abweichung von der vorgegebenen, idealen Kreisbahn (gestrichelte Linie) auftritt. Diese sogenannten Quadrantenfehler können mit der Richtungsumkehr der ersten Achse und damit mit dem Hystereseverhalten des Getriebes korreliert werden.

Modellbasierte Kompensation
In dem von der Deutschen Forschungsgemeinschaft (DFG) geförderten Projekt HyComp wird eine neuartige, modellbasierte Methode zur Kompensation der Hysterese entwickelt. Diese Methode basiert auf dem Konzept eines Koppelkraftbeobachters in Kombination mit einem mehrdimensionalen Hysteresemodell. Dazu wird die Koppelkraft zwischen An- und Abtriebsseite des Getriebes mit der über dem Getriebe auftretenden Winkeldifferenz eindeutig in Beziehung gesetzt werden. Wobei für die modellbasierte Kompensation des Hystereseverhaltens wiederum ein Modell des Hystereseverhaltens aufgestellt und identifiziert wird. Die Methode zeichnet sich insbesondere durch die Betrachtung der Hysterese als mehrdimensionalen Zusammenhang aus. Das Verfahren soll dazu beitragen, die Wissenslücke zwischen einer komplexen, modellbasierten Kompensation des Hystereseverhaltens und einer einfachen, konstanten Korrekturwertaufschaltung zu schließen. Dies geschieht unter Berücksichtigung der Randbedingungen der industriellen Praxis (erzielbare Abtastzeit, verfügbare Messgrößen, Robustheit gegenüber Modellunsicherheiten, etc.).
Experimenteller Nachweis und Ausblick
Zur Beurteilung des Kompensationsverfahrens ist eine praktische Umsetzung zwingend erforderlich. Hierzu wurde der in Abbildung 2 dargestellte Versuchsstand aufgebaut, der die besondere Charakteristik aufweist, dass das Getriebe abtriebsseitig nicht lediglich durch eine Trägheit mit Leistungsbremse belastet wird, sondern über einen abtriebsseitigen Lastmotor aktiv ein dynamisches Belastungsmoment aufgebracht werden kann. Somit können die Einflussgrößen auf das Hystereseverhalten unter reproduzierbaren Bedingungen untersucht werden. Dies erlaubt eine weitgehend isolierte Untersuchung der einzelnen Einflussparameter, wie z.B. Drehzahl, Temperatur und statische bzw. dynamische Belastung. Zudem lassen sich auch gezielt realitätsnahe Belastungssituationen herbeiführen, wie sie während des Betriebs von Industrierobotern auftreten. Diese Belastungssituationen können einerseits Bearbeitungsaufgaben mit hohen rückwirkenden Prozesskräften (Fräsbearbeitung) und andererseits Bearbeitungsaufgaben mit niedrigen bzw. keinen rückwirkenden Prozesskräften (Wasserstrahlschneiden/Laserbearbeitung) sein. Zukünftig soll das entwickelte Verfahren darüber hinaus auf einen Industrieroboter übertragen und anhand eines industriellen Anwendungsfalls, wie z.B. der Fräsbearbeitung, validiert werden.