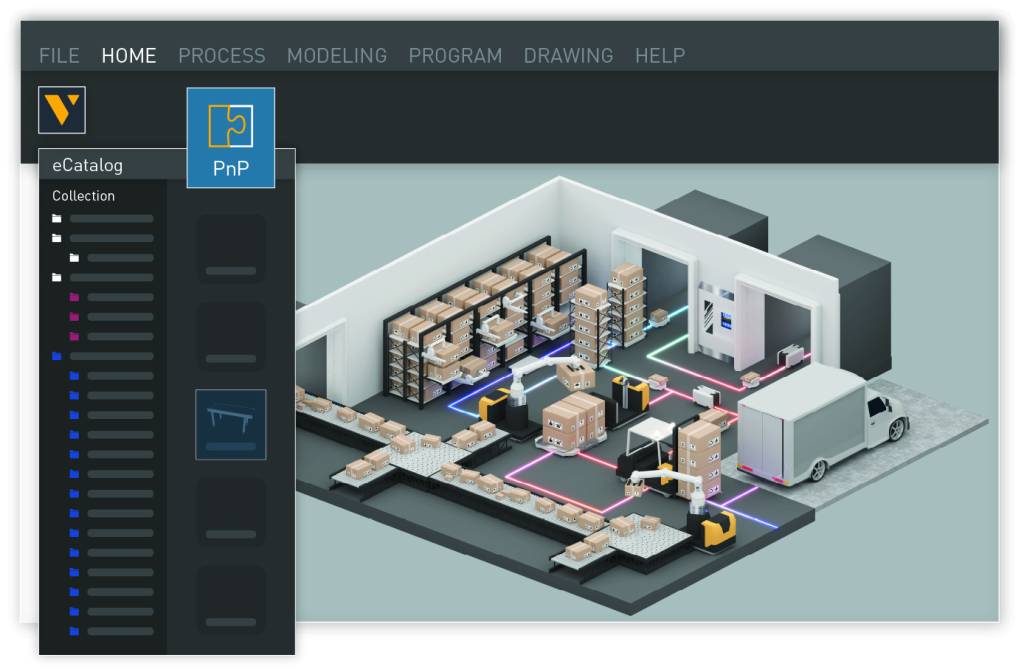
Mit der virtuellen Inbetriebnahme lassen sich Produktionslayouts in einer virtuellen 3D-Simulation einrichten, testen und validieren. Die Basis dafür ist eine Fabriksimulationssoftware. Ein Großteil der Inbetriebnahme kann so bereits vor oder parallel zum Bau der Anlage stattfinden. Zur statischen Darstellung der Maschinen ist eine 3D-CAD-Software nötig. Kinematik und ein Steuerungssystem für die Abläufe und das Timing sorgen dafür, dass die virtuellen Maschinen die Bewegungen und Prozesse der realen Anlage möglichst genau nachbilden. Die Methode verspricht einige der folgenden Effekte:
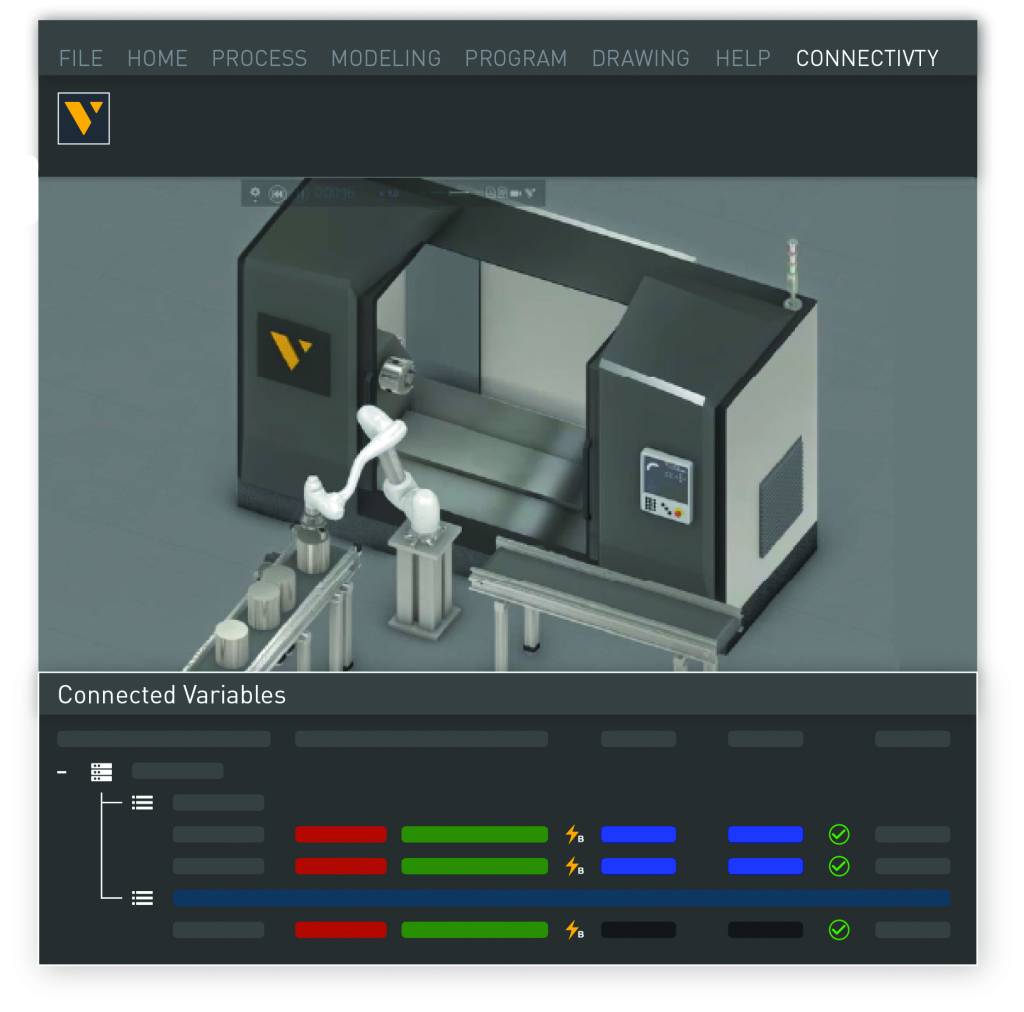
Warum auf VIBN setzen?
Früherkennung – Probleme wie die Fehlplatzierung von Robotern in einer Produktionslinie lassen sich früh erkennen und korrigieren.
Verkürzte Vorlaufzeit – Die Inbetriebnahme kann 25 Prozent der Projektlaufzeit betragen. Wird ein Teil davon früher durchgeführt, werden Projekte schneller fertig. Werden Probleme früh erkannt und behoben, können Hersteller den Termin der Fertigstellung zudem genauer vorhersagen.
Kosteneinsparungen – Probleme lassen sich in der Planungsphase meistens kostengünstiger aus der Welt schaffen als später. Das schont die Budgetierung, da weniger Mittel für ‚Unvorhergesehenes‘ gebraucht werden.
Innovationen – Oft erkennt das Team nach dem Bau der Maschinen Verbesserungsmöglichkeiten an der Konstruktion, etwa kürzere Zykluszeiten durch andere Greifabläufe. Doch nachträgliche Änderungen sind teuer und dauern. Bei der VIBN können Ideen einfacher berücksichtigt werden.
Ausbildung – Meist soll eine Anlage schnellstmöglich in Betrieb gehen. Schulungen zu Nutzung und Wartung sind einzurechnen. Bei der VIBN kann diese zunächst am digitalen Modell stattfinden. Eine Schulung an der physischen Maschine ist weiter empfehlenswert, doch sie geht schneller, wenn das Team die Abläufe bereits kennt.
Sicherheit – Bei der physischen Inbetriebnahme müssen Schutzvorrichtungen etwa von Robotern oft geöffnet werden, um Zugang zu gewähren. Virtuelle Prüfungen von Bewegungspfaden, Abläufen, Zeitplanung und Ausnahmebehandlungen verringern daraus entstehenden Risiken.
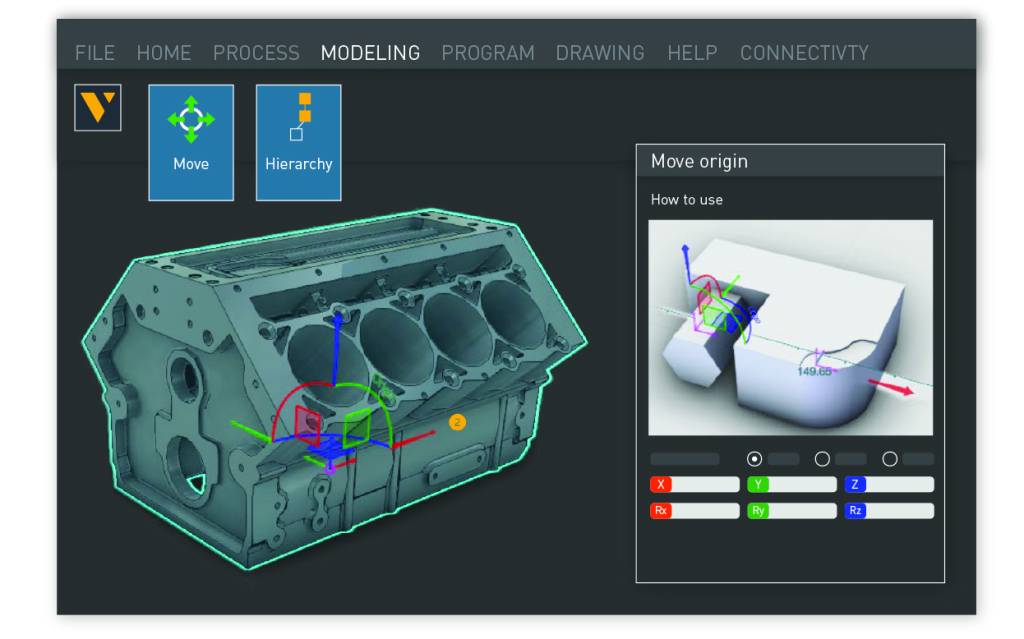
In zehn Schritten zur VIBN
Grundlage für die VIBN können Fabrikplanungsanwendungen wie Visual Components darstellen, die 3D-Simulation der Fertigung bieten. Der Ablauf einer Inbetriebnahme lässt sich grob in zehn Schritte strukturieren:
Verständnis schaffen – Das beteiligte Team ist mit der Relevanz eines genauen Modells vertraut und stellt die nötigen Informationen bereit. Denn bei Unstimmigkeiten wird die VIBN keine akkuraten Informationen liefern und die Schlussfolgerungen werden eventuell nicht ausreichend auf die reale Welt übertragbar sein.
System analysieren – Verantwortliche verschaffen sich ein Bild über die Ziele und Funktionen des Produktionssystems sowie über alle technischen Unterlagen, Spezifikationen und Anforderungen an die Maschinen und Steuerungssysteme.
Modell erstellen – Die Planer erstellen ein 3D-Modell des Produktionssystems. Bei Visual Components erfolgt das mit einer Kombination aus CAD-Daten und Modellen aus dem e-Catalog des Systems. Letzterer enthält über 3.000 Komponenten. Anschließend erfolgt die Integration u.a. kinematischer und elektrischer Daten, um eine möglichst genaue digitale Darstellung der geplanten Anlage zu erhalten.
Steuerlogik integrieren – Die SPS und die Robotersteuerung werden mit dem digitalen Modell verbunden. Dadurch können Steuerungssequenzen, Reaktionen und das gesamte Systemverhalten getestet werden. Visual Components bietet für diesen Schritt Konnektivität zu gängigen Robotermarken und SPS-Systemen wie Kuka, ABB, Fanuc und Siemens.
Simulieren und testen – Das Modell durchläuft verschiedene Betriebsszenarien, um die Leistung zu testen und es mit realen Daten zu validieren. Damit das System mit unvorhergesehenen Problemen umgehen kann, sollten auch Ausnahme- und Fehlersituationen geprüft werden.
Optimieren – Die Ergebnisse der Simulationsläufe sind die Basis, um Leistungsschwächen in der Steuerungslogik zu identifizieren und zu beheben. Anschließend werden die Tests solange wiederholt, bis dass das virtuelle Modell bestmöglich funktioniert.
Sicherheit und Konformität prüfen – Weitere Test stellen sicher, dass die Steuerungslogik und das Systemdesign funktionieren und die relevanten Industrienormen sowie Sicherheitsvorschriften eingehalten werden. Ein besonderes Augenmerk sollte dabei auf der Sicherheit der Industrieroboter liegen. Diese Kontrollen und Tests sind in Sektoren mit strengen Sicherheits- und Konformitätsanforderungen sehr wichtig.
Physisch In Betrieb nehmen – Die VIBN kann die physische Inbetriebnahme zwar deutlich verkürzen, aber nicht ersetzen. Die getestete und verifizierte Steuerungslogik muss in diesem Schritt vom Modell auf das reale System übertragen und das System bei der Inbetriebnahme genauestens überwacht werden, um sicherzustellen, dass es wie geplant funktioniert.
Kontinuierlich verbessern – Nachdem das physische System in Betrieb ist, werden Betriebsdaten gesammelt und mit den Prognosen aus der virtuellen Inbetriebnahme verglichen, um Bereiche mit Verbesserungsbedarf zu identifizieren. Die daraus gewonnenen Erkenntnisse helfen, das Modell und die Steuerungslogik weiterzuentwickeln.
Dokumentieren – Die VIBN ist kein einmaliger Prozess. Sie wird bei nötigen Änderungen oder Optimierungsbedarf am physischen System erneut durchgeführt. Um die Fehlersuche bei Upgrades oder bei der Skalierung zu unterstützen, wird jeder Schritt des virtuellen Inbetriebnahmeprozesses dokumentiert, angefangen beim ersten Entwurf bis hin zur endgültigen Implementierung.
Faktor im digitalen Wandel
Mit einer VIBN können Hersteller Zeit, Kosten und Ressourcen einsparen. Sie kann damit zum wichtigen Faktor im digitalen Wandel der Fertigungsindustrie werden und ist gleichzeitig ein Baustein auf dem Weg zur Industrie 4.0. Und nichtzuletzt stellt sie für Produzenten einen greifbaren Wettbewerbsvorteil dar.