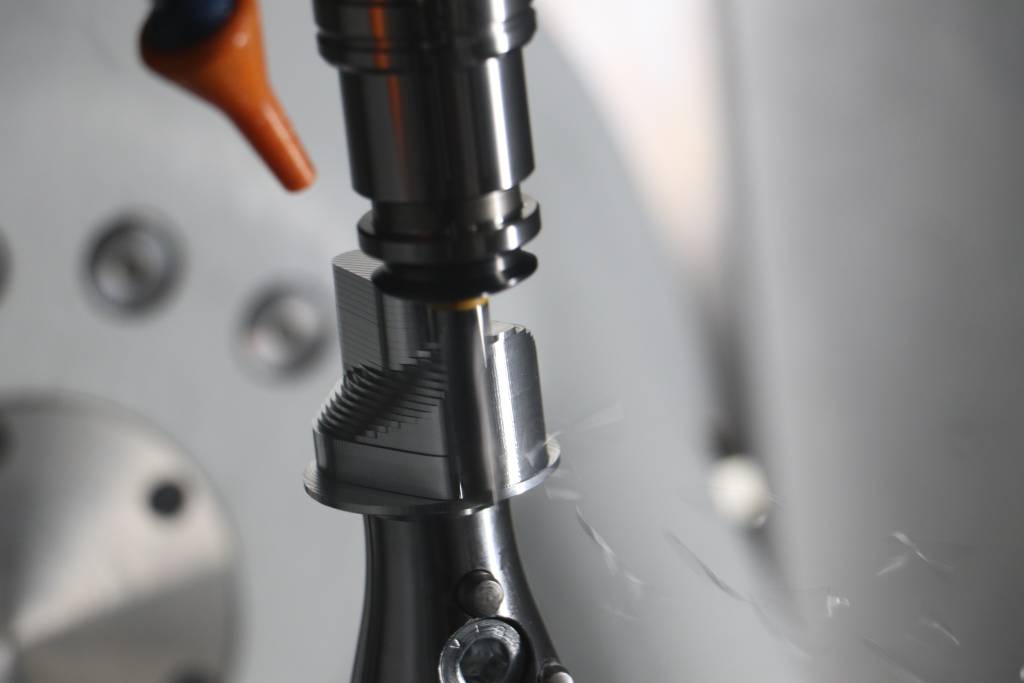
Gelebte Präzision
Hohe Qualität und Flexibilität ist für Siegfried Innerbichler in jeglicher Hinsicht wichtig. Nur so kann der Gründer und Geschäftsführer den Anforderungen seiner Kunden gerecht werden. Diese stammen durchwegs aus anspruchsvollen Branchen wie Werkzeugbau, Analyse- und Medizintechnik, Präzisionsoptik und Automobilindustrie. 1998 gegründet, stieg die Nachfrage nach Mikrobearbeitung stetig an. „In meiner Technikerlaufbahn erinnere ich mich schon seit über 30 Jahren an Maschinen von Kern“, berichtet der Firmenchef. „Im Jahr 2016 konnte ich mir mit der Kern Micro einen lang ersehnten Traum erfüllen. Mit der Micro HD, die wir jetzt im Verbund mit der Micro betreiben, setzte ich diesem dann in 2020 noch die Krone auf. Wir leben jetzt Präzision – und Kern macht das möglich.“
Bei den Aufträgen sind meistens zuverlässige Wiederholgenauigkeiten von unter 10µm gefragt. Aktuell gilt es u.a. gehärtete Formeinsätze für Dichtungen in Serien von bis zu 400 Stück herzustellen. Hier sind eine Präzision von 2µm und eine polierte Oberfläche vorgeschrieben. Für Prokurist Jochen Fill stellt dies mit den Kern-Maschinen kein Problem dar: „Die Kundenvorgaben erreichen wir hundertprozentig zuverlässig und mit der Micro HD um mehr als 30 Prozent schneller als das früher möglich war.“ Dabei überzeugt nicht nur die zuverlässige Wiederholgenauigkeit. Auch die durchgängig erreichte Oberflächengüte in Polierqualität mit Ra-Werten im niedrigen Nanometerbereich hilft dabei, Zeit zu sparen. Das schafft zusätzliche Kapazitäten, denn früher mussten immer wieder Mitarbeiter fürs Polieren der Bauteile abgestellt werden.
Messen eigentlich überflüssig
Um maximale Produktivität zu gewährleisten, läuft das fünfachsige Präzisionsfräszentrum bei Bedarf rund um die Uhr, zwei Schichten davon mannlos. Möglich ist dies dank eines Erowa-Werkstückladesystems, das die automatisierte Be- und Entladung für beide Maschinen übernimmt. Die fertigen Bauteile entnimmt Jochen Fill dann am nächsten Tag und gibt sie weiter in die Messabteilung. „Diese könnten wir eigentlich auflösen“, schmunzelt Innerbichler, „denn die Kern HD macht keine Fehler und ist genauer als unsere Messmaschine. Aber so lange unsere Kunden das Messprotokoll anfordern, machen wir das natürlich. Ein nachgewiesener Ausschuss von null Prozent ist ja auch ganz schön.“
Möglich ist diese zuverlässige Präzision aufgrund der ausgewogenen Grundkonstruktion der Kern Maschinen mit ausschließlich hochwertigen Komponenten. Sie sind schwingungsentkoppelt oder -gedämpft und werden durch ein ausgeklügeltes Kühlmanagement thermisch stabil gehalten. Bei der Micro HD sind dem Projektteam weitere Entwicklungssprünge gelungen, die vor allem auf drei Innovationen basieren: der Mikrospalt-Hydrostatik, linearen Direktantrieben und dem Temperaturmanagement. Insbesondere die Mikrospalt-Hydrostatik gibt es nirgendwo sonst im Werkzeugmaschinenbau. In Kombination mit Linearmotoren ist sie extrem dynamisch und benötigt etwa 80 Prozent weniger Energie als herkömmliche hydrostatische Systeme. Gleichzeitig verbessern sich durch den geringen Spalt Steifigkeit und Dämpfungseigenschaften der Maschine. Das sorgt für hohe Oberflächengüten und Genauigkeit am Werkstück. Zudem sind die Linearmotoren aktiv temperiert und in das hydrostatische System integriert – das minimiert den Wärmeeintrag. Des Weiteren werden die Kühlflüssigkeiten genau geregelt. Im Ergebnis heißt das: Die Temperaturschwankungen im Maschinenraum bleiben bei lediglich +/- 0,05 Kelvin.
Anspruchsvolle Werkstoffe
Dabei spielt es keine Rolle, welche Werkstoffe zu fräsen sind, betont der Chef des Tiroler Betriebs: „Wir bearbeiten fast ausschließlich anspruchsvolle Materialien wie Titan, Werkzeugstähle, pulvermetallurgische Stähle und seit Kurzem auch technische Keramik wie Siliziumcarbid oder Aluminiumoxide.“ Die Vorteile dieser Werkstoffe sind vielfältig: extrem hart, hochsteif, chemie- und wärmebeständig sowie temperaturleitfähig. Nachteilig ist hingegen die hohe Sprödigkeit von Keramik; das schließt einige Anwendungen aus und macht die mechanische Endbearbeitung teuer. Eine Lösung für letzteres Problem scheint jedoch in Sichtweite, wie Kern-Spezialist Peter Schöps verrät: „Unsere Kern Anwendungstechniker haben einen duktilen Schnittmodus entwickelt. Dadurch fließt jetzt beim Fräsen von Keramik ein Span und bricht nicht mehr. Das vervielfacht die Abtragraten prozessstabil, wie unsere umfangreichen Tests beweisen.“ Siegfried Innerbichler freut sich schon auf den Schnittmodus: „Wir sind – wie alle Kunden von Kern – ein Teil der Kern-Familie und partizipieren an allen Innovationen. Es hat in der Vergangenheit schon mehrfach Weiterentwicklungen gegeben, die Kern zusammen mit Werkzeugherstellern auf den Weg gebracht hat und mit denen wir unsere Produktivität steigern konnten. Das war beispielsweise bei einem neuen Werkzeug so, mit dem sich bleifreies Kupfer sehr gut bearbeiten lässt… und der neue Keramik-Schnittmodus wird sicher auch perfekt funktionieren.“