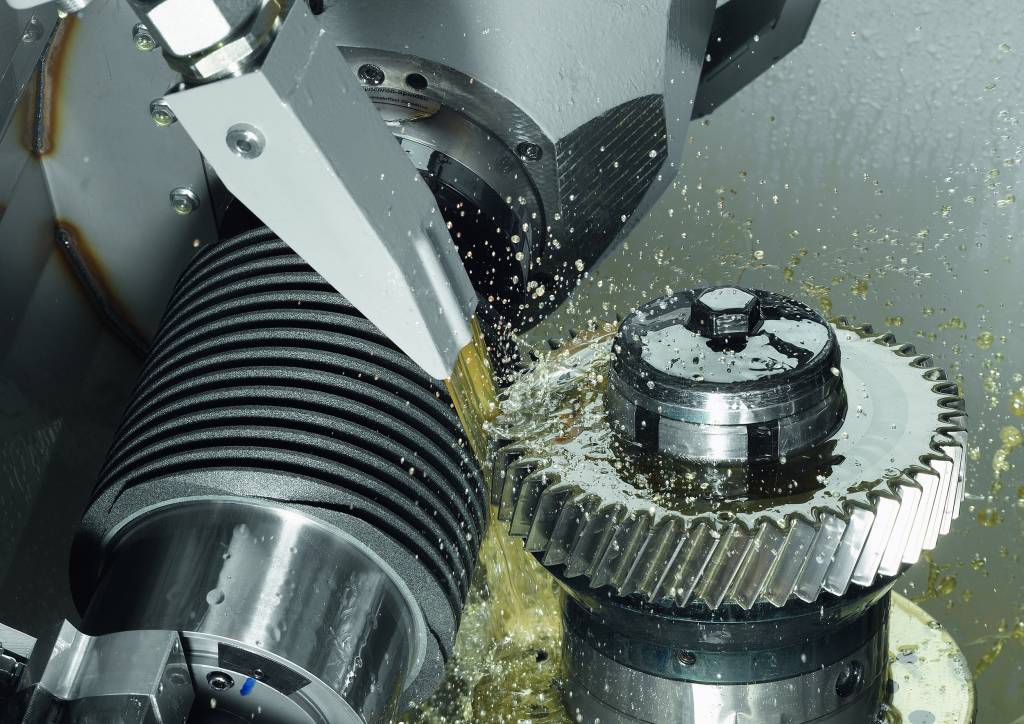
Die E-Mobilität verändert den gesamten Antriebsstrang im Auto und damit einhergehend auch die Anforderungen an die Getriebebauteile. Eines der wichtigsten Themen dabei ist die Reduzierung der Geräuschentwicklung des Antriebsstranges im Fahrbetrieb. Um Bauraum einzusparen, werden viele Teile des Getriebes in Leicht- bzw. Kompaktbauweise hergestellt. Gleichzeitig müssen Getriebebauteile immer robuster und langlebiger werden, um der hohen Beanspruchung aufgrund der höheren Motordrehzahlen standzuhalten.
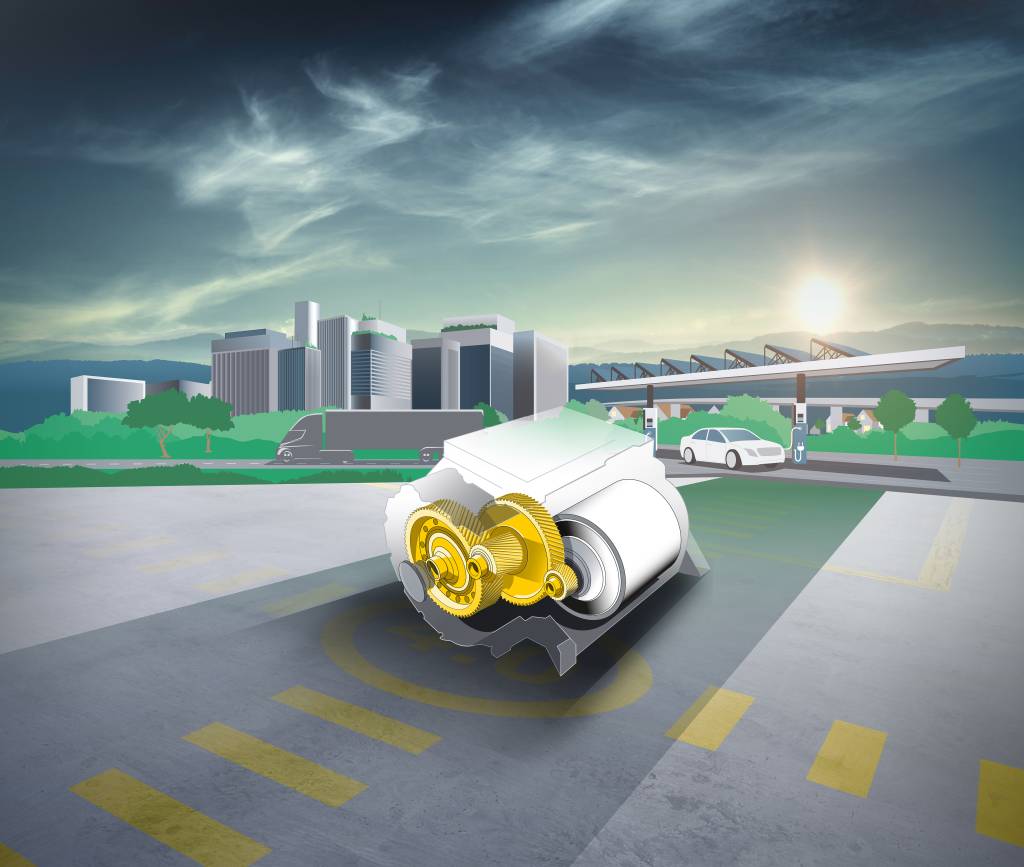
Hohe Kompetenz
Daraus ergeben sich hohe Qualitätsansprüche an die Zahnflankenoberflächen, die wiederum steigende Anforderungen an den Verzahnungsprozess mit sich bringen. Liebherr-Verzahntechnik hat sich mit dem Thema intensiv beschäftigt sowie verschiedene Technologielösungen für E-Getriebe weiterentwickelt und optimiert. „Wir wissen um die Herausforderungen, denen sich Hersteller und Zulieferer stellen müssen, was Qualität und Prozessstabilität angeht“, erläutert Dr. Andreas Mehr, verantwortlich für die Technologieanwendungen Verzahnungsschleifen und -stoßen. „Wir bringen unser Knowhow sowohl in der Prozesstiefe als auch in der Breite der Technologien mit ein. Damit können wir den Kunden als Partner umfassend beraten und begleiten, um für ihn und seine Anwendung die optimale Lösung zu finden.“
Auf der Verfahrensseite bietet z.B. das Wälzschleifen mit abrichtfreien CBN-Schleifschnecken eine hohe Prozesssicherheit. Im Rahmen der Hartfeinbearbeitung können die Zahnräder feingeschliffen und poliert werden, was den Oberflächenrauheitswert weiter senkt. Werkzeuge mit kleinem Außendurchmesser bearbeiten kollisionskritische Verzahnungen mit begrenztem Werkzeugauslauf.
Hinsichtlich der Zahnflankentopologie stehen Methoden für Flankenlinienmodifikationen zur Verfügung. Beispielsweise sorgt das topologisch abweichungsfreie Schleifen mit gezielter Endrücknahme (GER) für Traglastoptimierung. Um die Geräuschentwicklung zu verringern, lässt sich eine gezielte Welligkeit auf die Zahnflanke aufbringen (Noise Excitation Optimization). Oder es kann der diagonale Anteil beim Schlichten erhöht werden, um die Schleifriefenstruktur stochastisch zu verteilen (Silent Shift Grinding).
Je mehr topologische Modifikationen erforderlich sind, desto eher lohnt es sich, über das Werkzeugmaterial nachzudenken: Hier können CBN-Werkzeuge eine wirtschaftliche Alternative sein. Für viele Applikationen ist das Schleifen mit Korund-Schnecken eine gute Lösung, die beim Schleifen bei hohen topologischen Anforderungen aufgrund des Abrichtaufwands allerdings an ihre Grenzen kommt. Abrichtfreie CBN-Schleifschnecken aus der Liebherr-Eigenproduktion bieten eine Reihe von Vorteilen: hohe Prozessstabilität aufgrund der langen Werkzeugstandzeiten, die Vermeidung von Fehlerquellen beim Abrichten, das einfache Werkzeughandling sowie deutlich reduzierte Mess- und Prüfaufwände. Bei einer Topologie mit GER-Modifikation beispielsweise schneidet das CBN-Schleifen hinsichtlich der Stückkosten gegenüber dem Korund-Schleifen deutlich besser ab. Auch feinste Oberflächen mit einem Rz-Rauheitswert von unter drei Mikrometern lassen sich damit erzielen.
Spanntechnik und exklusives Maschinenkonzept
Die Herausforderung in der Herstellung von Getriebeteilen für E-Bikes liegt häufig in den filigranen Abmessungen und kleinen Modulen. Für die Fertigung dieser Bauteile in hoher Qualität müssen Schleifprozess und Spanntechnik schnell und hochpräzise sein. Spezielle Spannlösungen sorgen dafür, dass auch kleine und kollisionskritische Bauteile wie zum Beispiel Antriebswellen mit Modul 0,6mm in einer Verzahnungsqualität von DIN 1-4 problemlos bearbeitet werden können.
Für optimalen Rundlauf und hohe Reproduzierbarkeit sorgt das exklusive Liebherr-Maschinenkonzept mit einer Ein-Tisch-Lösung – für die kontrollierte und kontinuierliche Fertigung von Teilen mit Qualitätsanforderungen im Mikrometerbereich ein entscheidender Vorteil. Speziell bei kleineren und mittleren Stückzahlen, wie sie häufig in der Fertigung für die E-Mobilität vorkommen, ist dieses Konzept auch besonders wirtschaftlich, denn die kurzen Rüstzeiten gestatten einen schnellen Produktionsstart.
Kundennahe Unterstützung
„Wir verstehen uns nicht nur als Produktanbieter, sondern als Partner und Lösungsanbieter“, betont Dr. Andreas Mehr. „Wir nehmen den Kunden mit auf die Reise, indem wir ihm Entscheidungshilfen bieten und plausible Alternativen aufzeigen, damit er am Ende die für ihn optimale Entscheidung treffen kann.“ So waren beispielsweise im Getriebe eines Kunden trotz Einhaltung der geforderten Spezifikationen Geräusche aufgetreten. Liebherr nahm sich des Themas an. Es stellte sich heraus, dass die Ursache in weiteren Parametern außerhalb des Schleifprozesses lag und das Getriebe anders ausgelegt werden musste. Auf Basis dieser Ergebnisse konnte der Kunde seine Prozesse entsprechend optimieren. „Der enge Zeitrahmen konnte eingehalten werden, weil bei Liebherr die komplette Technologie und das Knowhow gebündelt vorhanden waren“, erinnert sich Dr. Andreas Mehr. „Oft gibt es kein ‚Richtig oder Falsch‘: Vielmehr hängt die Wahl des optimalen Verfahrens von den spezifischen Anforderungen und Parametern ab. An der Stelle wollen wir unsere Kunden unterstützen, in dem wir ehrlich das Für und Wider für das ein oder andere Verfahren abwägen.“