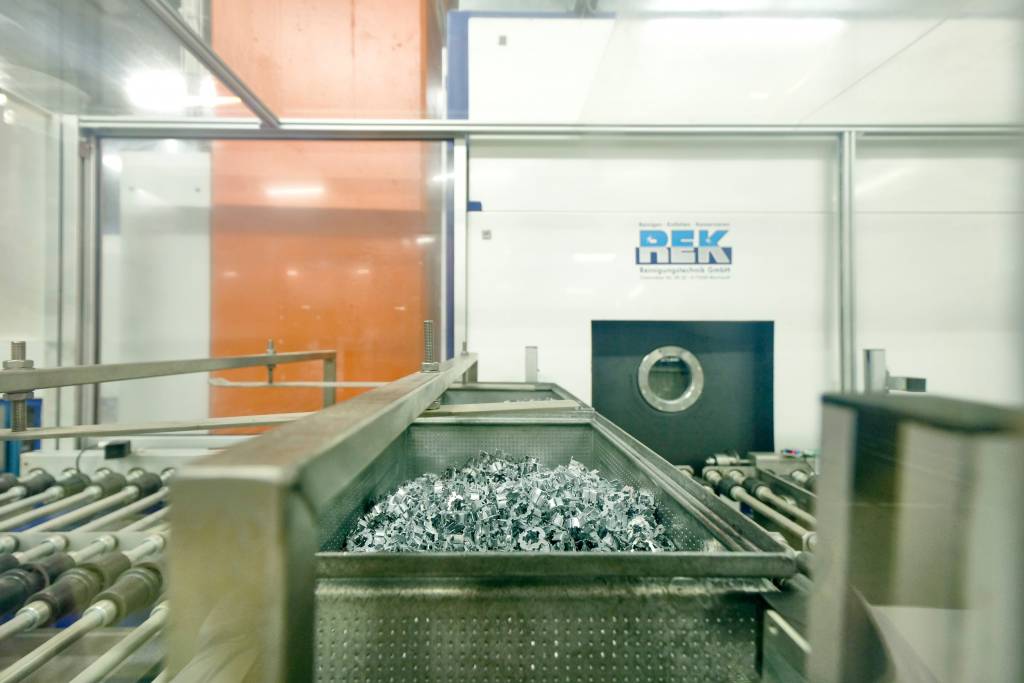
Johnson Electric International gehört zur Johnson Electric Group mit weltweit 36.000 Beschäftigten in über 23 Ländern. Der Schweizer Standort in Murten ist laut der Unternehmensgruppe eines ihrer Innovations- und Produktentwicklungszentren und beschäftigt 400 Mitarbeiter. 75 Prozent der dort gefertigten Bauteile gehen in die weltweite Automobilindustrie, darunter auch die in drei Montagelinien produzierten Schrittmotoren. 36 Millionen Stück verlassen jedes Jahr das Werk.
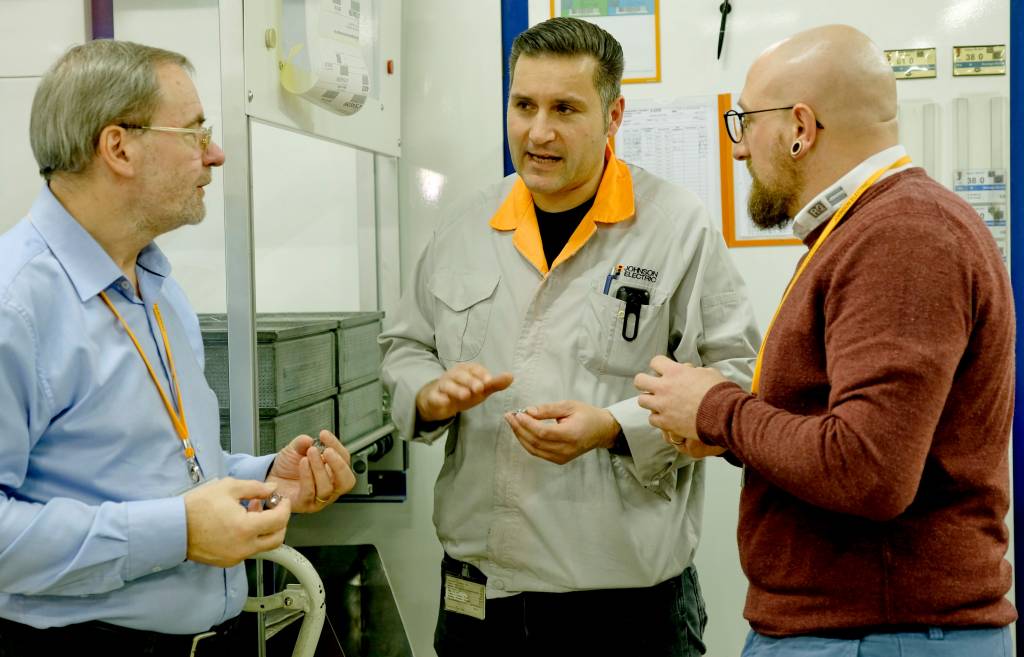
450.000 Teile pro Tag entfetten
„Jeden Tag laufen bei uns 450.000 Einzelteile für die Schrittmotoren durch die Produktion. Immer zwei Einzelteile ergeben einen Motor“, erklärt José Landeira, Metal Part Manager bei Johnson Electric International. Später im Auto verbaut, steuern sie beispielsweise die Klappen der Heizung und Klimaanlage. Bevor die beiden Einzelteile jedoch zu einem Schrittmotor zusammengesetzt werden, gilt es diese perfekt zu reinigen. Die Entfettung der Statoren übernehmen in Murten zwei Anlagen des Anbieters REK Reinigungstechnik. Beim Lösemittel vertraut Johnson Electric auf den modifizierten Alkohol RG Cleaner 63 der Firma Richard Geiss. Er befreit die Bauteile nicht nur effizient von polaren Stoffen wie Salzen, Staub oder Metallabrieb, sondern löst auch unpolare Stoffe wie Fette und Öle.
„Die Ausreißkräfte unserer Schrittmotoren wurden aber mit der Zeit immer schwächer – und wir konnten uns nicht erklären warum. Schließlich haben wir die Einzelteile ja wie gewohnt in unseren Anlagen entfettet“, so Landeira. Die Schrittmotoren müssen Ausreißkräfte von 80Nm halten, um die strengen Anforderungen der internationalen Automobilindustrie zu erfüllen. Johnson Electric fährt die beiden REK-Dampfentfettungsanlagen im Dreischichtbetrieb, fünf Tage die Woche. „Zum Wochenbeginn waren die Messungen immer in Ordnung“, erklärt Landeira, „aber zum Ende der Woche hin wurden sie immer schlechter.“
Erster Gedanke: Es könnte am Öleintrag liegen, denn am Wochenende stehen die beiden Entfettungsanlagen still und das Lösemittel wird destilliert. Das hätte die besseren Prüfergebnisse am Wochenanfang erklärt. „Die Analysen in unserem Firmenlabor aber haben gezeigt, dass die beiden Lösemittelproben, die wir am Anfang und am Ende der Woche aus der Anlage entnommen hatten, keine großen Unterschiede aufwiesen. Im Gegenteil: Das Medium war sauber“, betont Manuel Huihui, Außendienstmitarbeiter im internationalen Vertrieb von Richard Geiss, der den Kunden auch vor Ort betreute.
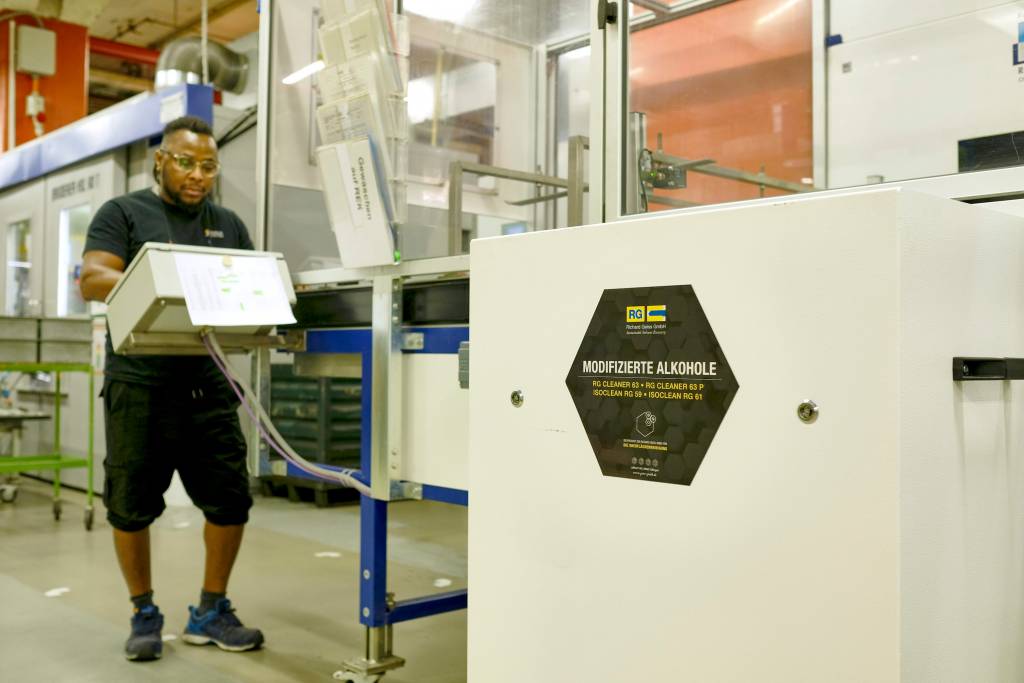
Entfettungsproblem: Analyse deckt Ursachen auf
Zur Ursachenforschung untersuchten die Lösemittelspezialisten von Richard Geiss alle verschiedenen Prozessschritte. „Das ging weit über normale Serviceanalysen hinaus“, weiß José Landeira zu schätzen. Die umfassenden Analysen fanden im unternehmenseigenen Labor in Offingen statt. Neben dem Lösemittel wurde auch die gesamte Anlagentechnik überprüft. Das Ergebnis: Die Anlagen neigten unter den eingestellten Parametern zum Schäumen – und dieses Schäumen verschmutzte die Teile nach dem Reinigen wieder.
Zur Lösung des Entfettungsproblems wurden in Rücksprache mit einem auf die Anlagen spezialisierten Servicetechniker der Druckunterschied in den Anlagen verringert und weitere Parameter optimiert. Darüber hinaus nutzt Johnson Electric in den beiden Dampfentfettungsanlagen jetzt den Entschäumer Geiss Distil: Der ‚Schaumbrecher‘ verhindert die Schaumbildung in organischen Lösemitteln. „Diese Umstellung hat geholfen“, verdeutlicht Landeira. „Wir können jetzt wieder problemlos die strengen Anforderungen der Automobilindustrie erfüllen.“
50 Prozent weniger Lösemittel
Johnson Electric fährt in Murten jetzt nicht nur einen stabilen, sondern sogar einen optimierten Entfettungsprozess. Dank der Anlagennachjustierung und des Entschäumers Geiss Distil wird die Hälfte an Lösemittel im Vergleich zu vorher gespart. „Wo wir früher alle drei Monate fast 700 Liter Lösemittel austauschen mussten, kommen wir mit dem Lösemittel jetzt sechs bis acht Monate aus“, so Ladeira.