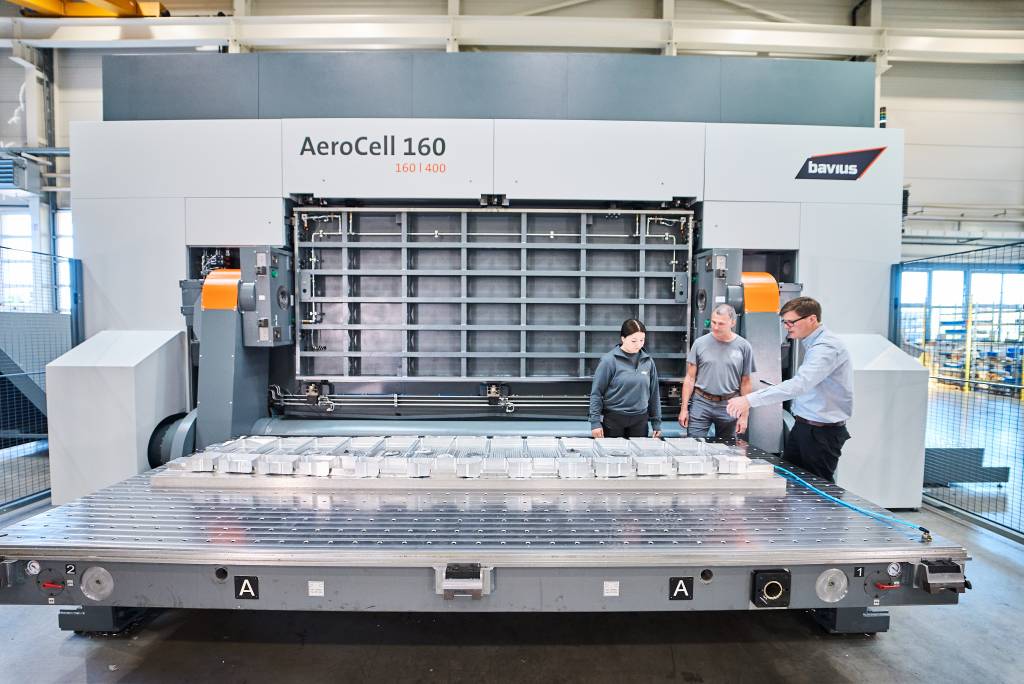
Die Anforderungen an die Sicherheit der Flugzeugfertigung sind enorm, um das Risiko von Defekten an den Teilen soweit wie möglich auszuschließen. Dies ist auch der Grund für die hohen Zerspanungsanteile der in Flugzeugen verbauten Strukturteile. Da es sich vielfach um große Bauteile handelt, sind die Fräszeiten vergleichsweise lang. Deshalb wurde die aktuelle Bavius-Maschine AeroCell 160 für möglichst hohe Produktivität ausgelegt. Sie eignet sich insbesondere für Anwender, die Bauteile mit Abmessungen bis zu 4.000x1.600mm und maximal 800mm Höhe bearbeiten wollen.

Außerordentliche Zerspanungsleistungen
„Um bei der Zerspanung Höchstleistungen bieten zu können, haben wir die Technologie unserer Gabel-Fräsköpfe selbst entwickelt“, erläutert Werner Zell von der Abteilung Mechanische Konstruktion. In der AeroCell 160 arbeitet im Bavius Fräskopf bmh3 die grundlegend optimierte und leistungsgesteigerte neue Hochleistungsspindel der Firma Fischer (bis zu 30.000 Umdrehungen pro Minute, Leistung: maximal 140kW). Sie gestattet im S6-Betrieb Zerspanungsraten bis zu 20,6 und im S1-Betrieb bis zu 16,7 Liter Späne pro Minute.
Hohe Zerspanungsleistungen setzen eine entsprechende Dynamik der Maschine voraus: So erreichen die drei Hauptachsen Verfahrgeschwindigkeiten bis zu 70m/min und Beschleunigungen bis 7m/s2. Noch entscheidender sind allerdings der hohe ‚Ruck‘ der Antriebstechnik und die Fähigkeit des Maschinenkonzepts, diesen umzusetzen. Der Ruck sorgt dafür, dass das Fräswerkzeug bei Richtungsänderungen in kürzester Zeit wieder auf volle Bahngeschwindigkeit kommt. Dies ist insbesondere dann bedeutsam, wenn das Bauteil viele Taschen aufweist. Darüber hinaus sorgte der Hersteller bei der Maschine für möglichst kurze Nebenzeiten, etwa durch einen schnellen Werkzeugwechsler, der Span-zu-Span-Zeiten von nur zehn Sekunden erlaubt. Eine zusätzliche Variante ist ein Tausch der Werkzeugaufnahme der Spindel von HSK-A63/80 gegen HSK-A100. Das Werkzeugmagazin ist zudem von 103 auf 240 Plätze erweiterbar.

Raus mit der Wärme
„Bei derartig hohen Zerspanungsleistungen muss die Abfuhr der in der Maschine entwickelten Wärme mit besonderer Effizienz erfolgen“, ergänzt Bavius-Vertriebsleiter Amit Paranjape. Das beginnt bereits mit der Orientierung der Werkstücke, die horizontal statt vertikal bearbeitet werden. So verbleiben die Späne samt der darin enthaltenen Wärme nicht in den Taschen des Werkstücks, sondern fallen der Schwerkraft folgend nach unten. Dabei hilft zudem ein scharfer Kühlschmierstoff (KSS)-Strahl, der restliche Späne mit bis zu 80bar aus den Vertiefungen spült.
Des Weiteren verfügt die gesamte Anlage über ein ausgefeiltes Temperaturmanagement. Dies beginnt bei der Spindel, die über eigene Kühlkanäle sowie über Temperatursensoren in den Wicklungen des Antriebs verfügt. Diese Temperaturmessung ist zugleich Voraussetzung für eine hohe Positioniergenauigkeit von 0,02mm, u.a. durch Kompensation der Spindellängung über die CNC-Steuerung. Auch die beiden Rundachsen des Gabelkopfs, die Z-Achse, die sonstigen Hauptkomponenten und das Maschinenbett werden gekühlt. Da der größte Teil der in der Maschine entstehenden Wärme über die Späne im KSS landet, wird dieser nach der Rückgewinnung und Filterung intensiv gekühlt. In Kombination mit einer nach thermischen Gesichtspunkten optimierten Maschinenkonstruktion sind dies ideale Voraussetzungen für eine ausgezeichnete Bearbeitungsqualität.
Besonderes Augenmerk galt bei der Konstruktion auch dem Abluftmanagement. Der im Inneren der Anlage entstehende KSS-Nebel wird mit hoher Leistung abgesaugt und mehrstufig gefiltert. Die Filterung ist so effizient, dass die Abluft anschließend in die Maschinenhalle zurückgeführt werden kann.
Rascher Werkstückwechsel
„Bei großen Werkstücken kann das Aufspannen und Einmessen oft viel Zeit in Anspruch nehmen“, weiß Werner Zell. Deshalb habe man wie auch bei den bewährten Horizontal-Bearbeitungszentren AeroCell 200 mit deren einzigartigem Paletten-Wechselsystem viel getan, um diese Aufgaben in die Nebenzeit verlegen zu können. Die Teile werden vor der Maschine auf einer separaten Palette aufgespannt.